- お役立ち記事
- Review demand forecasting and supplier selection criteria to reduce inventory risk
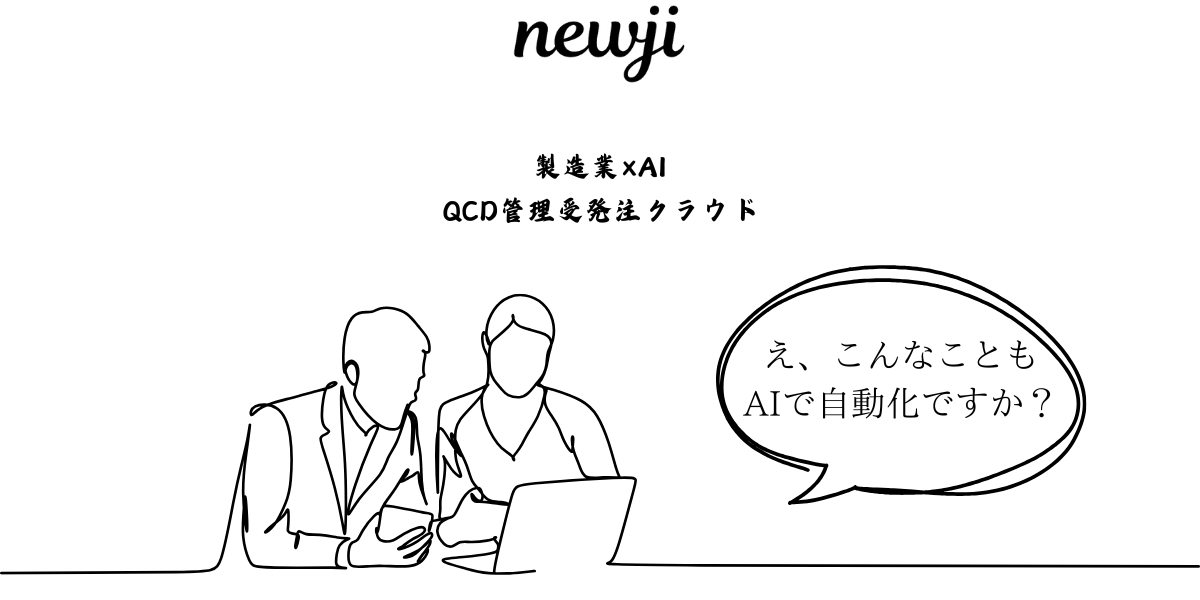
Review demand forecasting and supplier selection criteria to reduce inventory risk
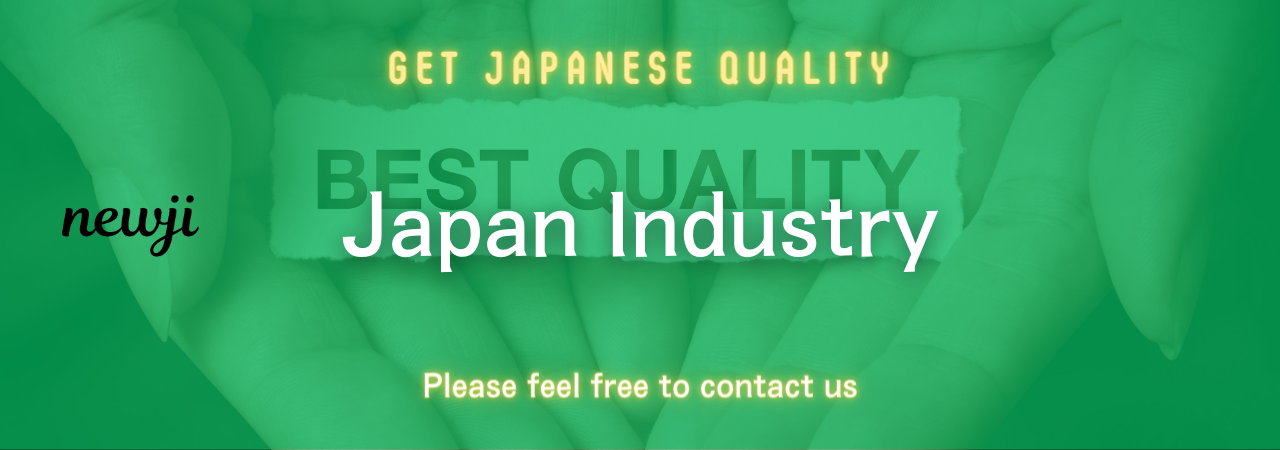
目次
Understanding Demand Forecasting
Demand forecasting is a crucial aspect of inventory management that helps businesses predict future customer demand for their products.
Accurate demand forecasting allows companies to make informed decisions about inventory levels, production schedules, and supply chain management.
This process involves analyzing sales data, market trends, and customer behavior to estimate the amount of product that customers are likely to purchase in the future.
By understanding demand patterns, companies can better align their inventory with actual customer demand, reducing excess stock and minimizing the risk of stockouts.
Importance of Accurate Demand Forecasting
Accurate demand forecasting is essential for businesses to optimize their inventory management.
Without precise forecasts, companies may either overstock, resulting in increased carrying costs and potential obsolescence, or understock, leading to missed sales opportunities and dissatisfied customers.
Effective demand forecasting helps ensure that businesses have the right amount of inventory at the right time, minimizing both overstock and stockout risks.
This balance is vital for maintaining customer satisfaction and maximizing profitability.
Challenges in Demand Forecasting
Despite its importance, demand forecasting is not without its challenges.
Factors such as market volatility, changing consumer preferences, and unexpected events can significantly impact demand predictions.
Additionally, inaccurate data or improper analysis can lead to forecasting errors.
Companies must continuously review and update their demand forecasting models to adapt to these challenges and improve accuracy.
Implementing advanced statistical methods and leveraging technology like machine learning can enhance the forecasting process and lead to better outcomes.
Supplier Selection Criteria
Selecting the right suppliers is another critical component of effective inventory management.
A reliable and efficient supply chain can help reduce inventory risks and ensure timely product availability.
Certain criteria are necessary for choosing the best suppliers for your business needs.
Factors to Consider in Supplier Selection
When selecting suppliers, businesses should consider several key factors:
1. **Reliability:** Dependable suppliers consistently meet delivery schedules and quality standards.
2. **Cost:** While cost is important, it’s crucial to balance cost efficiency with quality and service levels.
3. **Quality:** High-quality products and materials contribute to customer satisfaction and brand reputation.
4. **Flexibility:** Suppliers that can adjust to changing demands or custom requirements add value to the supply chain.
5. **Capacity:** Ensure that the supplier can handle your volume needs without compromising on quality or timeliness.
6. **Reputation:** A supplier’s reputation within the industry can provide insights into their reliability and performance.
7. **Communication:** Open and transparent communication fosters a collaborative relationship and quick resolution of issues.
Benefits of Careful Supplier Selection
Choosing the right suppliers offers numerous benefits, including reduced costs, improved quality, and increased efficiency.
Reliable suppliers help optimize inventory levels by ensuring consistent supply and minimizing the risk of disruptions.
Additionally, a strong supplier relationship can enhance innovation and provide competitive advantages, as suppliers may offer insights into market trends or new technologies.
Reducing Inventory Risk
Reducing inventory risk involves implementing strategies that balance supply with demand, optimizing stock levels, and minimizing the chances of excess or insufficient inventory.
Strategies to Mitigate Inventory Risk
Here are a few strategies businesses can adopt to lower inventory risks:
1. **Implement Just-in-Time Inventory:** This strategy reduces holding costs by maintaining minimal inventory and restocking only as needed.
2. **Use Demand Planning Software:** Advanced software solutions can aid in accurate demand forecasting and inventory management.
3. **Regularly Review Inventory Levels:** Continuous monitoring allows businesses to adjust inventory based on changes in demand and supply.
4. **Enhance Supplier Collaboration:** Strong partnerships with suppliers can lead to better communication and flexibility, reducing the likelihood of stockouts.
5. **Diversify Suppliers:** Having multiple suppliers mitigates the risk of dependency on a single source, providing more security.
6. **Invest in Inventory Management Systems:** These systems provide accurate tracking, which is crucial for maintaining optimal stock levels.
Conclusion
Ultimately, the integration of accurate demand forecasting and strategic supplier selection is critical for reducing inventory risk.
Businesses that invest in both robust forecasting methods and carefully chosen supplier relationships are more likely to maintain balance between supply and demand, ensuring customer satisfaction and optimizing profits.
By continuously reviewing these processes and adapting to market changes, companies can effectively manage their inventory and mitigate associated risks.
資料ダウンロード
QCD調達購買管理クラウド「newji」は、調達購買部門で必要なQCD管理全てを備えた、現場特化型兼クラウド型の今世紀最高の購買管理システムとなります。
ユーザー登録
調達購買業務の効率化だけでなく、システムを導入することで、コスト削減や製品・資材のステータス可視化のほか、属人化していた購買情報の共有化による内部不正防止や統制にも役立ちます。
NEWJI DX
製造業に特化したデジタルトランスフォーメーション(DX)の実現を目指す請負開発型のコンサルティングサービスです。AI、iPaaS、および先端の技術を駆使して、製造プロセスの効率化、業務効率化、チームワーク強化、コスト削減、品質向上を実現します。このサービスは、製造業の課題を深く理解し、それに対する最適なデジタルソリューションを提供することで、企業が持続的な成長とイノベーションを達成できるようサポートします。
オンライン講座
製造業、主に購買・調達部門にお勤めの方々に向けた情報を配信しております。
新任の方やベテランの方、管理職を対象とした幅広いコンテンツをご用意しております。
お問い合わせ
コストダウンが利益に直結する術だと理解していても、なかなか前に進めることができない状況。そんな時は、newjiのコストダウン自動化機能で大きく利益貢献しよう!
(Β版非公開)