- お役立ち記事
- Reviewing safety stock: Key points for cost reduction and risk management by the purchasing department
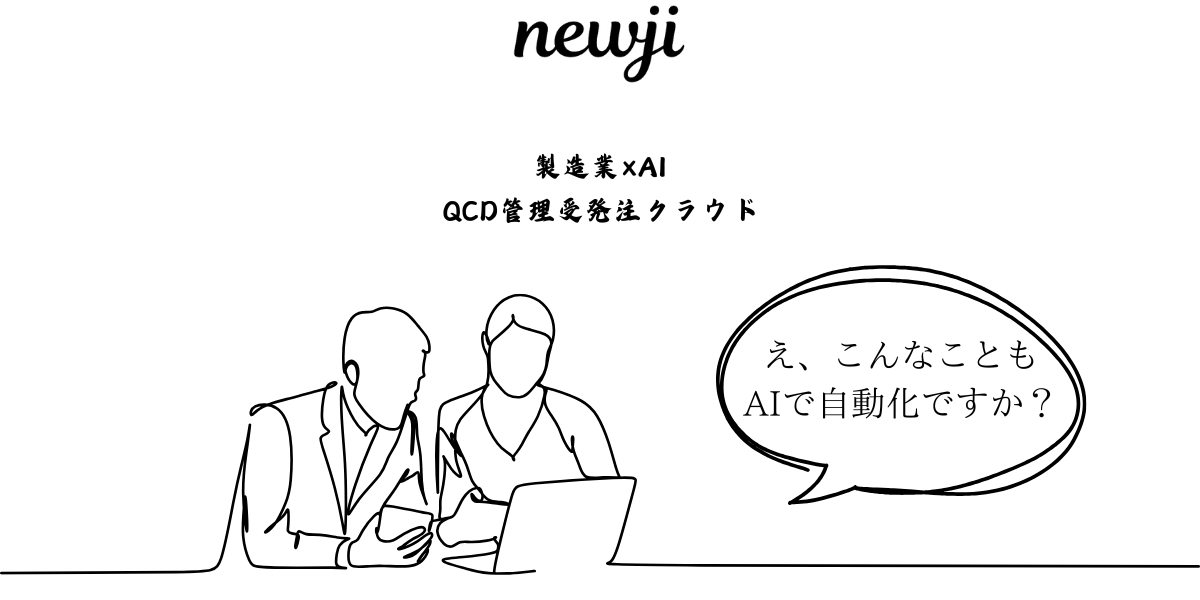
Reviewing safety stock: Key points for cost reduction and risk management by the purchasing department
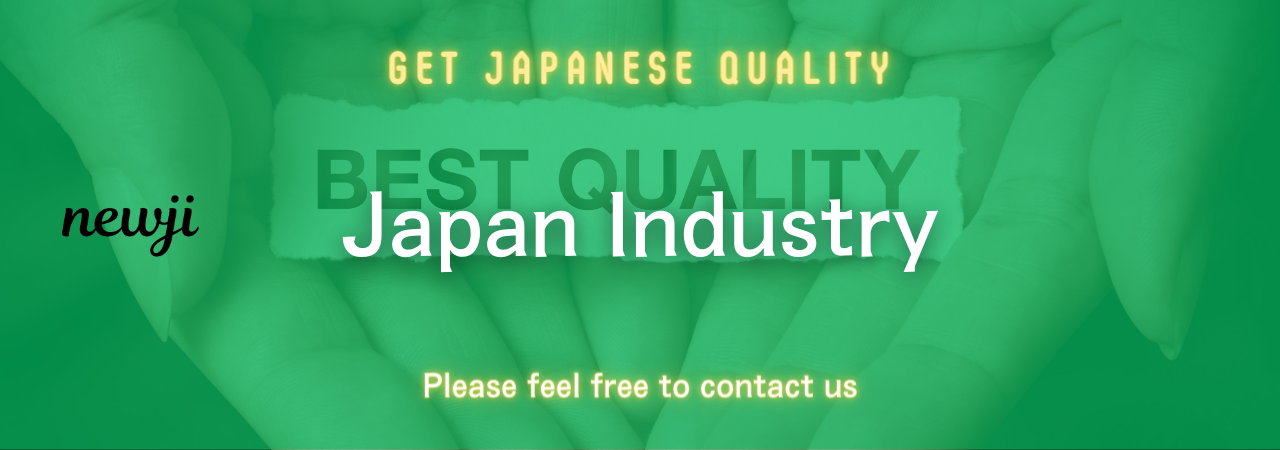
目次
Understanding Safety Stock
Safety stock serves as a critical component in inventory management, aimed at preventing stockouts caused by fluctuations in demand or supply chain disruptions.
For purchasing departments, maintaining an optimal level of safety stock is crucial for balancing cost efficiency and risk management.
But how do businesses find this optimal level?
The Role of Safety Stock in Inventory Management
Safety stock acts as a buffer to absorb irregularities in supply chain operations and unforeseen spikes in customer demand.
The key is to keep just enough to ensure that operations remain smooth without tying up too much capital in surplus inventory.
Exceeding necessary levels can lead to increased holding costs, while insufficient stock may result in lost sales and compromised customer satisfaction.
Key Points for Evaluating Safety Stock
Analyze Historical Data
Start by analyzing historical sales and demand data.
Understanding past patterns helps in predicting future trends.
Seasonal fluctuations, special promotions, and market expansions should be accounted for to get a complete picture.
This data lays the groundwork for calculating the minimum safety stock required to cushion your inventory against unexpected changes.
Consider Lead Time Variability
Lead time variability is another major factor in gauging safety stock needs.
Longer lead times increase the chances of stockout risks, as do frequent fluctuations in supplier lead times.
By assessing your suppliers’ reliability and consistency, you can better predict and prepare for potential disruptions.
Calculate Optimal Safety Stock Levels
Once you’ve determined the demand and lead time variability, the next step is to calculate the optimal safety stock.
The safety stock formula takes into account the standard deviation of demand and lead time, as well as the desired service level.
Regular reevaluation is necessary, as market conditions, supplier relationships, and other factors evolve over time.
Strategies for Cost Reduction
Negotiate Better Supplier Terms
One practical approach is renegotiating terms with suppliers for more favorable lead times or pricing.
Improved terms can directly reduce the safety stock requirements and associated carrying costs.
Consider working with multiple suppliers to minimize risk and provide leverage in negotiations.
Implement Just-in-Time Inventory
By moving to a Just-in-Time (JIT) inventory system, companies can reduce the need for safety stock.
JIT focuses on receiving goods as close as possible to when they are needed, thereby minimizing storage costs.
However, this requires a highly reliable supply chain and robust forecasting methods.
Invest in Technology for Better Forecasting
Adopting modern inventory management software can enhance your forecasting accuracy.
These tools often utilize algorithms and machine learning to predict demand much more accurately than traditional methods.
With precise forecasting, companies can significantly lower their safety stock without increasing the risk of stockouts.
Balancing Cost and Risk
Evaluate Risk Tolerance
A company’s approach towards safety stock should align with its overall risk tolerance.
Industries with minimal tolerance for stockouts, such as pharmaceuticals or automotive, might prioritize risk reduction over cost.
On the other hand, retail businesses may lean towards cost savings, especially for non-essential goods.
Monitor and Adjust Continuously
The purchasing department should continuously monitor safety stock levels and assess if they align with current business goals and market conditions.
Regular reviews ensure that the company adapts swiftly to changes, maintaining that delicate balance between cost and risk.
Conclusion
Understanding and managing safety stock is a delicate but essential process for purchasing departments.
By leveraging data, reevaluating supplier relationships, adopting JIT practices, and investing in technology, organizations can effectively lower costs while minimizing risk.
Such strategic efforts not only enhance operational efficiency but also promote sustained business growth in an ever-changing market environment.
資料ダウンロード
QCD調達購買管理クラウド「newji」は、調達購買部門で必要なQCD管理全てを備えた、現場特化型兼クラウド型の今世紀最高の購買管理システムとなります。
ユーザー登録
調達購買業務の効率化だけでなく、システムを導入することで、コスト削減や製品・資材のステータス可視化のほか、属人化していた購買情報の共有化による内部不正防止や統制にも役立ちます。
NEWJI DX
製造業に特化したデジタルトランスフォーメーション(DX)の実現を目指す請負開発型のコンサルティングサービスです。AI、iPaaS、および先端の技術を駆使して、製造プロセスの効率化、業務効率化、チームワーク強化、コスト削減、品質向上を実現します。このサービスは、製造業の課題を深く理解し、それに対する最適なデジタルソリューションを提供することで、企業が持続的な成長とイノベーションを達成できるようサポートします。
オンライン講座
製造業、主に購買・調達部門にお勤めの方々に向けた情報を配信しております。
新任の方やベテランの方、管理職を対象とした幅広いコンテンツをご用意しております。
お問い合わせ
コストダウンが利益に直結する術だと理解していても、なかなか前に進めることができない状況。そんな時は、newjiのコストダウン自動化機能で大きく利益貢献しよう!
(Β版非公開)