- お役立ち記事
- Revisiting Machining Processes Through Learning from Contemporary Parts Manufacturing Techniques and Cases
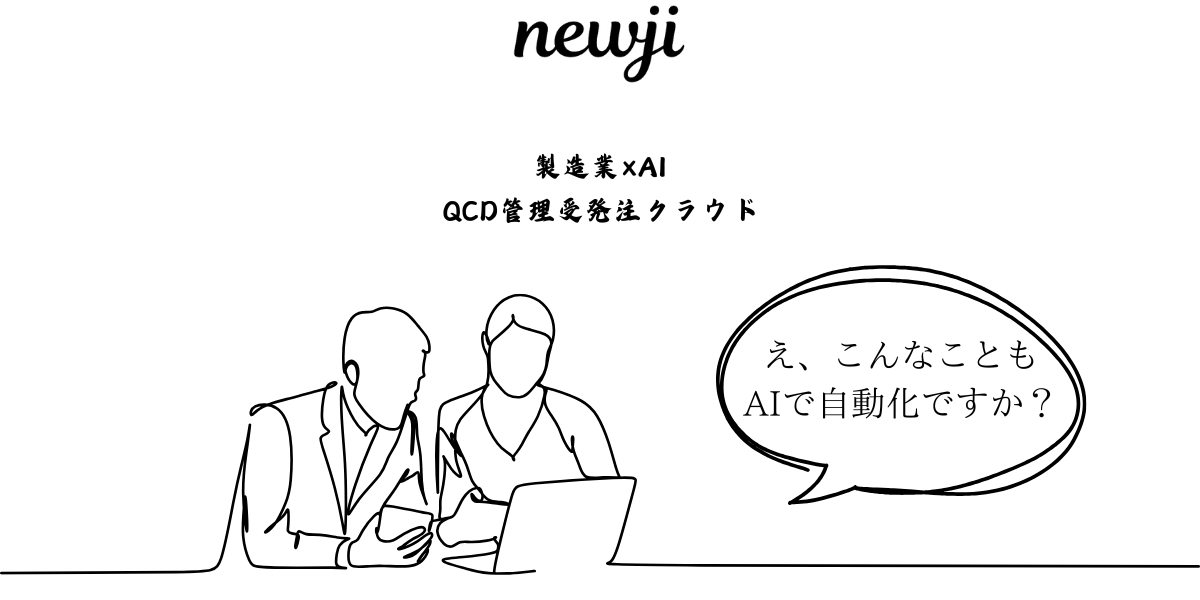
Revisiting Machining Processes Through Learning from Contemporary Parts Manufacturing Techniques and Cases
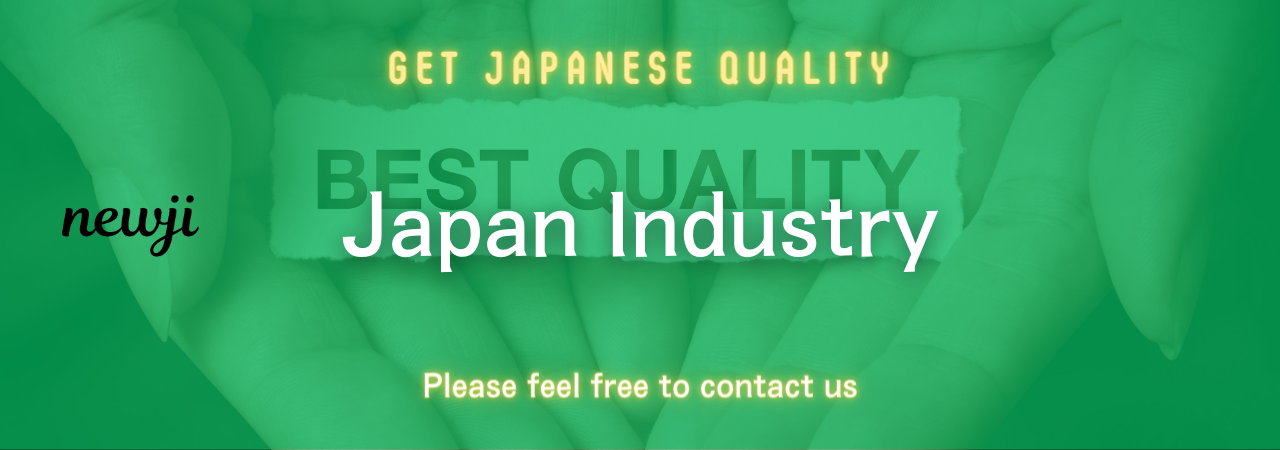
In today’s fast-paced manufacturing world, machining processes are crucial to creating high-quality parts and products. Understanding contemporary parts manufacturing techniques can significantly enhance the efficiency and precision of these processes. This article delves into modern machining methods and real-life cases to shed light on how they evolve and redefine manufacturing.
目次
Introduction to Machining Processes
Machining is a manufacturing process in which material is removed from a workpiece to shape it into the desired form. The primary methods of machining include cutting, drilling, grinding, milling, and turning. These processes are fundamental to industries ranging from automotive to aerospace, ensuring precision and accuracy in the production of complex parts.
Advancements in Machining Technology
Over the years, machining technology has evolved, introducing several advancements that enhance both speed and precision. Automation and computer numerical control (CNC) machining are two significant developments that have transformed machining processes.
Automation in Machining
Automation in machining involves using robotic systems to perform tasks traditionally undertaken by humans. These robots can handle repetitive tasks with high precision, reduce human error, and increase production speed. Automated machining processes include robotic milling, robotic welding, and automated assembly lines.
Computer Numerical Control (CNC) Machining
CNC machining refers to the use of computers to control machining tools. CNC machines follow programmed instructions to precisely shape parts. This technology allows for highly accurate and repeatable operations, making it ideal for producing components with tight tolerances. CNC machining has revolutionized industries by enhancing product quality and reducing production time.
Contemporary Parts Manufacturing Techniques
Modern parts manufacturing techniques leverage advanced technologies to meet the demands of today’s market. These techniques focus on efficiency, precision, and cost-effectiveness.
Additive Manufacturing
Additive manufacturing, commonly known as 3D printing, involves creating a part layer by layer from digital blueprints. This method allows for complex geometries that would be challenging or impossible to achieve with traditional machining. Additive manufacturing has found applications in prototyping, medical implants, and even aerospace components.
High-Speed Machining (HSM)
High-speed machining (HSM) is a technique that involves operating machining tools at higher speeds than conventional methods. This increases material removal rates and reduces cycle times, making it a cost-effective solution for manufacturing large volumes of parts. HSM is particularly advantageous in industries where time and efficiency are critical factors.
Micro-Machining
Micro-machining is the process of making very small and precise parts often used in medical devices, electronics, and aerospace applications. Techniques in micro-machining include micro-milling, micro-drilling, and micro-turning. This method requires specialized equipment and considerable expertise to achieve the desired results.
Case Studies in Contemporary Machining
Examining real-life cases helps us understand the practical applications and benefits of contemporary machining techniques. Here are two case studies showcasing how modern machining processes have been employed successfully.
Case Study 1: Aerospace Component Manufacturing
An aerospace company needed to manufacture turbine blades with intricate geometries and tight tolerances. Traditional machining methods were found inadequate due to the complexity of the parts. The company turned to additive manufacturing to produce the blades layer by layer from a titanium alloy.
The results were impressive. The additive manufacturing process not only produced the turbine blades with the required precision but also reduced material waste. Additionally, the manufacturing time was significantly shortened, allowing the company to meet its production deadlines and reduce costs.
Case Study 2: Medical Device Production
A medical device manufacturer required micro-sized components for a new line of minimally invasive surgical instruments. The parts needed to be extremely precise and consistent. The company employed micro-machining techniques to produce these tiny components.
Using micro-milling and micro-drilling, the manufacturer was able to achieve the high level of precision necessary for the medical devices. The process was automated using CNC machines, ensuring consistency and reliability in production. As a result, the company successfully developed its new product line, meeting all regulatory standards and market demands.
The Future of Machining Processes
The future of machining processes looks promising, with ongoing advancements in technology continuing to shape the industry. Researchers are exploring the use of artificial intelligence (AI) and machine learning to further improve machining efficiency and precision.
Artificial Intelligence in Machining
Artificial intelligence can enhance machining processes by optimizing tool paths, predicting machine failures, and improving quality control. AI algorithms can analyze data from previous machining operations to identify patterns and recommend process improvements. This level of automation can lead to significant cost savings and higher-quality products.
Hybrid Machining Processes
Hybrid machining processes combine multiple techniques, such as additive and subtractive manufacturing, in a single operation. This allows manufacturers to leverage the benefits of both methods, creating parts with complex geometries more efficiently. Hybrid machining is expected to become more prevalent as technology advances and industries demand higher precision and flexibility.
Conclusion
Revisiting machining processes through the lens of contemporary parts manufacturing techniques reveals a dynamic industry that continues to evolve. Advancements in automation, CNC machining, additive manufacturing, high-speed machining, and micro-machining are transforming the way parts are produced. Real-life case studies demonstrate the practical benefits and successes of these modern methods.
As technology continues to advance, the future holds even greater potential for precision, efficiency, and innovation in machining processes. Understanding and embracing these contemporary techniques will be essential for manufacturers aiming to stay competitive in an ever-changing market.
資料ダウンロード
QCD調達購買管理クラウド「newji」は、調達購買部門で必要なQCD管理全てを備えた、現場特化型兼クラウド型の今世紀最高の購買管理システムとなります。
ユーザー登録
調達購買業務の効率化だけでなく、システムを導入することで、コスト削減や製品・資材のステータス可視化のほか、属人化していた購買情報の共有化による内部不正防止や統制にも役立ちます。
NEWJI DX
製造業に特化したデジタルトランスフォーメーション(DX)の実現を目指す請負開発型のコンサルティングサービスです。AI、iPaaS、および先端の技術を駆使して、製造プロセスの効率化、業務効率化、チームワーク強化、コスト削減、品質向上を実現します。このサービスは、製造業の課題を深く理解し、それに対する最適なデジタルソリューションを提供することで、企業が持続的な成長とイノベーションを達成できるようサポートします。
オンライン講座
製造業、主に購買・調達部門にお勤めの方々に向けた情報を配信しております。
新任の方やベテランの方、管理職を対象とした幅広いコンテンツをご用意しております。
お問い合わせ
コストダウンが利益に直結する術だと理解していても、なかなか前に進めることができない状況。そんな時は、newjiのコストダウン自動化機能で大きく利益貢献しよう!
(Β版非公開)