- お役立ち記事
- Revitalize Your Business: Cost Reduction Activities in Japanese Manufacturing for Unparalleled Efficiency
Revitalize Your Business: Cost Reduction Activities in Japanese Manufacturing for Unparalleled Efficiency
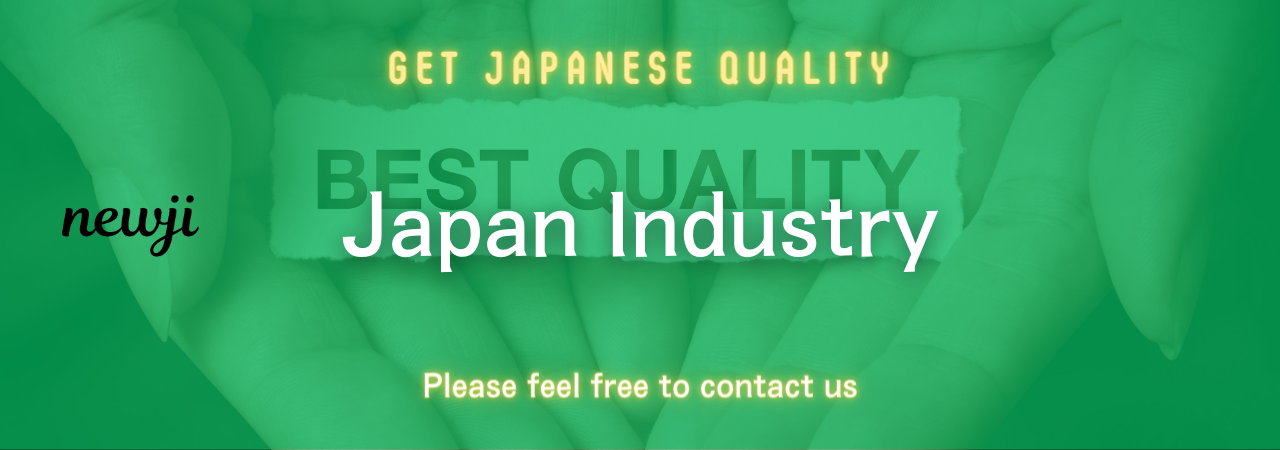
In today’s hyper-competitive global market, staying ahead requires relentless efforts in streamlining operations and optimizing costs. Japanese manufacturing stands as a testament to achieving unparalleled efficiency, blending time-tested practices with cutting-edge technology. Drawing from over two decades of experience in procurement, purchasing, and production management, this article unravels the cost reduction activities in Japanese manufacturing and how they can revitalize your business.
目次
Understanding the Japanese Manufacturing Ethos
To fully appreciate the benefits of integrating Japanese manufacturing practices, it’s essential to understand the ethos driving such efficiency. Japanese manufacturers center their practices around a principle known as “Kaizen” – meaning continuous improvement. This philosophy permeates every aspect of their operations, from procurement to production, and drives a culture where small, incremental changes accumulate into significant advancements over time.
The Role of Kaizen in Cost Reduction
Kaizen emphasizes employee involvement at all levels. Workers are encouraged to share insights and suggest improvements. By adopting Kaizen, manufacturers can eliminate waste, optimize processes, and ultimately reduce costs. It’s not a radical overhaul of the system but a meticulous polishing to enhance performance continually.
Cost Reduction Through Lean Manufacturing
Lean manufacturing is another cornerstone of Japanese industrial prowess. By focusing on value creation for the customer and eliminating waste, lean practices ensure that every step in the manufacturing process adds value.
Identifying and Eliminating Waste
Lean manufacturing identifies seven wastes, known as “Muda.” These include overproduction, waiting, transport, extra processing, inventory, motion, and defects. By addressing each of these areas systematically, companies can significantly cut costs. For instance, optimizing the supply chain to reduce waiting times and unnecessary transport can lead to immediate cost savings.
Just-In-Time (JIT) Production
Just-In-Time production is a hallmark of lean manufacturing. By producing goods as they are needed, manufacturers can minimize inventory costs and reduce waste. JIT requires precise coordination with suppliers and a robust logistics network, ensuring materials arrive exactly when needed without holding excess inventory. This practice not only cuts costs but also enhances production flexibility, allowing manufacturers to respond swiftly to market changes.
Procurement Strategies for Cost Reduction
Effective procurement strategies play a crucial role in Japanese manufacturing efficiency. From supplier selection to negotiation techniques, every aspect of procurement is geared towards minimizing costs and maximizing quality.
Building Strong Supplier Relationships
Japanese manufacturers prioritize long-term relationships with suppliers. By fostering strong partnerships, they can negotiate better terms, achieve consistent quality, and ensure a reliable supply chain. Trust and collaboration enable both parties to work towards mutual goals, such as cost reduction and process optimization.
Supplier Evaluation and Selection
Selecting the right supplier is paramount. Japanese procurement teams conduct thorough evaluations, considering factors such as quality, reliability, financial stability, and technological capability. A meticulous vetting process ensures that suppliers can meet strict standards and contribute to cost-effective manufacturing.
Negotiation Techniques
In negotiations, Japanese procurement professionals focus on creating win-win scenarios. They approach discussions with the aim of finding solutions that benefit both parties. By emphasizing fairness and transparency, they build strong, lasting relationships, which can lead to favorable terms and reduced costs.
Leveraging Advanced Technology for Efficiency
Advancements in technology have further cemented Japanese manufacturing’s reputation for efficiency. From automation to data analytics, integrating cutting-edge technology can yield significant cost savings.
Automation and Robotics
Automation plays a crucial role in reducing labor costs and increasing precision. Incorporating robotics into production lines can speed up processes, minimize errors, and enhance overall efficiency. Japan has been a pioneer in adopting automation, and manufacturers worldwide can learn valuable lessons from their implementation.
Data Analytics and Predictive Maintenance
Harnessing the power of data can lead to substantial cost reductions. By analyzing production data, manufacturers can identify inefficiencies, predict maintenance needs, and optimize operations. Predictive maintenance, in particular, helps avoid costly downtime by addressing equipment issues before they escalate. Utilizing data-driven insights enables informed decision-making and continuous improvement.
Quality Control for Cost Efficiency
Maintaining high quality while reducing costs may seem contradictory, but Japanese manufacturers have mastered this balance. Robust quality control processes ensure that products meet stringent standards, minimizing defects and rework.
Implementing Total Quality Management (TQM)
Total Quality Management (TQM) is a holistic approach to long-term success through customer satisfaction. TQM involves every employee, from top management to frontline workers, in a continuous effort to improve quality and reduce costs. By focusing on quality at every stage of production, manufacturers can prevent errors and enhance efficiency.
Quality Circles
Quality circles are small groups of employees who regularly meet to discuss and solve work-related problems. This collaborative approach harnesses the collective expertise of the workforce, leading to practical solutions and continuous improvements. Quality circles not only enhance product quality but also contribute to a culture of shared responsibility and teamwork.
Case Studies: Success Stories from Japanese Manufacturers
Examining real-world examples can provide valuable insights into effective cost reduction practices. Several Japanese companies have achieved remarkable success through their commitment to efficiency and quality.
Toyota’s Lean Manufacturing
Toyota’s production system is a benchmark for lean manufacturing. By eliminating waste and optimizing processes, Toyota has consistently delivered high-quality vehicles at competitive prices. Their focus on continuous improvement and respect for people has fostered a resilient and efficient manufacturing environment.
Canon’s Automation and Precision
Canon has integrated advanced automation to achieve precision and efficiency in its manufacturing processes. By leveraging robotics and data analytics, Canon has minimized defects and streamlined production. Their commitment to innovation has resulted in significant cost savings and enhanced product quality.
The Challenges and Considerations
While adopting Japanese manufacturing practices offers numerous benefits, it’s essential to consider potential challenges. Implementing these practices may require cultural and organizational adjustments, investment in technology, and a commitment to long-term improvement.
Cultural Alignment
Embracing practices like Kaizen and lean manufacturing may require a cultural shift within the organization. Companies need to foster a culture that values continuous improvement, employee involvement, and collaborative problem-solving.
Initial Investment
Transitioning to advanced technology and automation may require significant upfront investment. However, the long-term benefits in terms of cost reduction and efficiency often outweigh the initial costs.
Continuous Commitment
Japanese manufacturing principles are not one-time fixes but ongoing efforts. Companies must commit to continuous improvement and regularly assess their processes to ensure sustained efficiency and cost savings.
Best Practices for Implementing Japanese Manufacturing Techniques
To successfully integrate Japanese manufacturing principles, consider the following best practices:
Engage Employees at All Levels
Involve employees in identifying inefficiencies and suggesting improvements. Their firsthand experience can provide valuable insights into practical solutions.
Prioritize Supplier Collaboration
Build strong, collaborative relationships with suppliers. Work together to achieve mutual goals, such as cost reduction and process optimization.
Utilize Technology Wisely
Invest in advanced technology strategically. Focus on areas where automation and data analytics can yield the most significant benefits.
Regularly Review and Improve Processes
Continuously assess and refine processes. Implement feedback loops to ensure that improvements are sustained over time.
Commit to a Long-Term Vision
Embrace a mindset of continuous improvement. Understand that achieving unparalleled efficiency is an ongoing journey, not a destination.
Conclusion
Revitalizing your business through cost reduction activities inspired by Japanese manufacturing principles can lead to unparalleled efficiency and competitiveness. By adopting practices like Kaizen, lean manufacturing, and advanced technology, companies can minimize waste, optimize operations, and achieve long-term success.
Implementing these techniques requires a commitment to continuous improvement, collaboration, and innovation. With the right strategies and mindset, businesses can harness the power of Japanese manufacturing to drive cost efficiency and thrive in the global market. In an increasingly competitive landscape, the lessons from Japanese manufacturing are more relevant than ever, offering a blueprint for sustainable success.
資料ダウンロード
QCD調達購買管理クラウド「newji」は、調達購買部門で必要なQCD管理全てを備えた、現場特化型兼クラウド型の今世紀最高の購買管理システムとなります。
ユーザー登録
調達購買業務の効率化だけでなく、システムを導入することで、コスト削減や製品・資材のステータス可視化のほか、属人化していた購買情報の共有化による内部不正防止や統制にも役立ちます。
NEWJI DX
製造業に特化したデジタルトランスフォーメーション(DX)の実現を目指す請負開発型のコンサルティングサービスです。AI、iPaaS、および先端の技術を駆使して、製造プロセスの効率化、業務効率化、チームワーク強化、コスト削減、品質向上を実現します。このサービスは、製造業の課題を深く理解し、それに対する最適なデジタルソリューションを提供することで、企業が持続的な成長とイノベーションを達成できるようサポートします。
オンライン講座
製造業、主に購買・調達部門にお勤めの方々に向けた情報を配信しております。
新任の方やベテランの方、管理職を対象とした幅広いコンテンツをご用意しております。
お問い合わせ
コストダウンが利益に直結する術だと理解していても、なかなか前に進めることができない状況。そんな時は、newjiのコストダウン自動化機能で大きく利益貢献しよう!
(Β版非公開)