- お役立ち記事
- Revitalizing Japanese Manufacturing: The Role of PROFINET in Smart Factory Automation
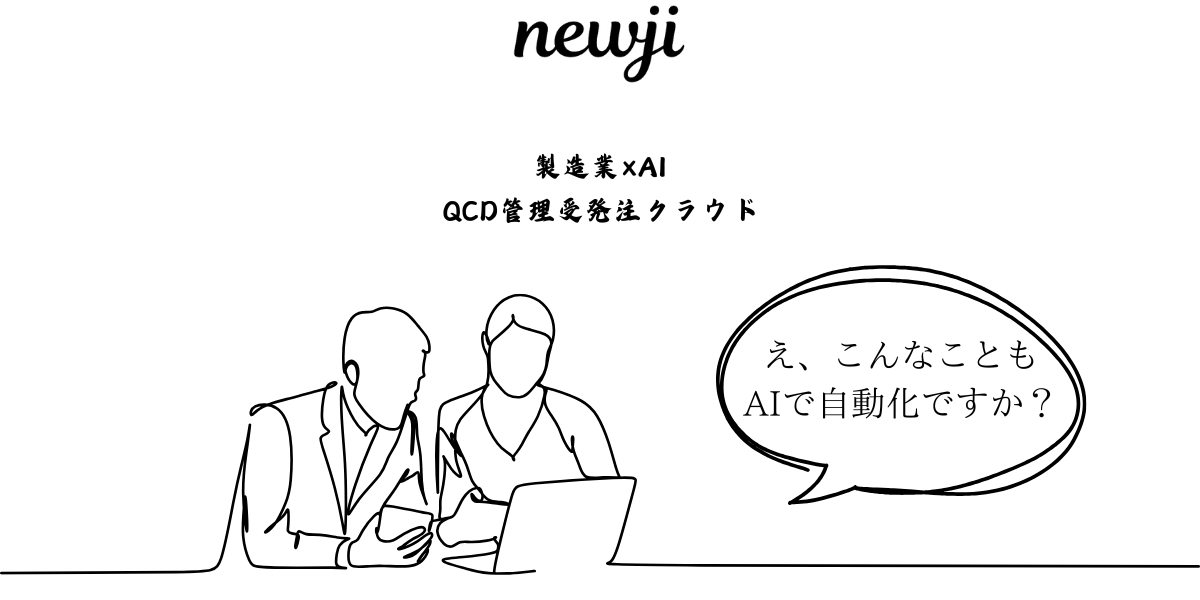
Revitalizing Japanese Manufacturing: The Role of PROFINET in Smart Factory Automation
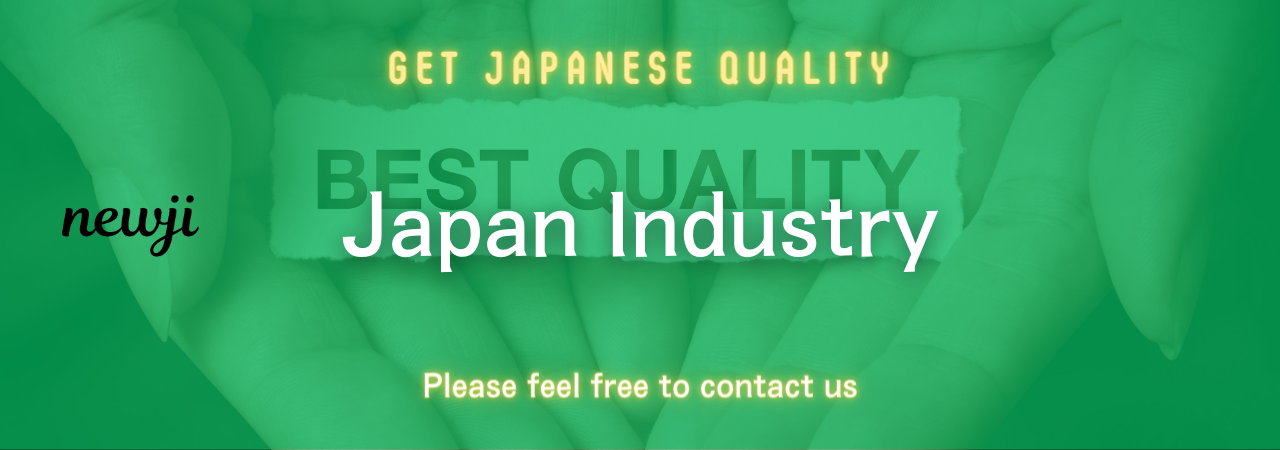
In the evolving landscape of global manufacturing, the necessity for enhanced operational efficiency and seamless connectivity among devices has never been more pressing.
Japan, recognized globally for its manufacturing prowess, is keenly embracing technological advancements to uphold its competitive edge. One pivotal technology facilitating this shift is PROFINET, a standard for industrial networking based on Ethernet.
Here’s a comprehensive look into the role of PROFINET in smart factory automation and how it is revitalizing Japanese manufacturing.
目次
Overview of PROFINET Technology
PROFINET, or Process Field Net, is an industry technical standard for data communication over Industrial Ethernet.
It significantly extends the capabilities of traditional fieldbuses by offering faster communication, increased flexibility, and enhanced functionalities intended for industrial automation.
Its implementation spans a broad spectrum, including real-time data acquisition, control applications, and device integration across the factory floor.
Why PROFINET?
One of the distinguishing features of PROFINET is its real-time, deterministic communication.
This allows for synchronized operations of machines and devices, crucial for applications where timing precision is paramount.
Moreover, PROFINET’s scalability ensures that it can be used in small applications or scale up to manage entire production lines.
Advantages of Using PROFINET in Japanese Manufacturing
Integrating PROFINET in Japanese manufacturing setups yields multiple benefits, ensuring these facilities remain at the forefront of global competition.
Improved Operational Efficiency
PROFINET’s real-time (RT) and isochronous real-time (IRT) communication capabilities ensure minimal delays and increased coordination among production units.
This seamless communication elevates operational efficiency by reducing downtime and enabling faster manufacturing cycles.
High Flexibility and Scalability
PROFINET adapts to various industrial needs, from simple to complex applications.
Its flexibility ensures it can handle different network topologies and complex production systems, making it particularly beneficial for advanced Japanese manufacturing settings.
Enhanced Data Integration
In the era of Industry 4.0, the integration of data from various sources is crucial for informed decision-making.
PROFINET allows effortless integration and interoperability with other systems, facilitating comprehensive data analysis and process optimization.
Future-Proofing Manufacturing Infrastructure
With its robust data handling and communication protocols, PROFINET is future-proof, ensuring that facilities can incorporate emerging technologies without substantial infrastructural overhauls.
This is vital for maintaining Japan’s position in the rapidly evolving global market.
Practical Applications and Case Studies
Let’s delve into some specific applications and case studies showcasing the transformative impact of PROFINET in smart factory automation in Japan.
Case Study 1: Toyota’s Smart Assembly Lines
Toyota, a benchmark for global automotive manufacturing, has implemented PROFINET to streamline its assembly lines.
By integrating PROFINET, Toyota ensures real-time communication between robotic arms, sensors, and control systems.
This synchronization has drastically reduced production times and increased overall assembly line efficiency, maintaining Toyota’s high standards of quality and performance.
Case Study 2: Mitsubishi Electric’s Automation Systems
Mitsubishi Electric, another industry giant, leverages PROFINET for its advanced automation systems.
Through PROFINET’s high-speed data transfer capabilities, Mitsubishi Electric manages complex processes with unprecedented accuracy and reliability.
This has significantly enhanced the speed and efficiency of their production lines, demonstrating PROFINET’s potential in sophisticated manufacturing environments.
Case Study 3: Panasonic’s Modular Production Units
Panasonic uses PROFINET to facilitate the modularity of its production units.
This allows for quick reconfiguration and adaptation to different production requirements, ensuring maximum flexibility and resource utilization.
The integration of PROFINET has thus enabled Panasonic to quickly respond to market changes and maintain high levels of productivity.
Challenges and Disadvantages of Implementing PROFINET
While PROFINET offers numerous advantages, the transition to this technology comes with its own set of challenges.
High Initial Investment
Implementing PROFINET requires significant upfront investment in both hardware and training.
For small to medium-sized enterprises, this could be a substantial financial burden, making it difficult to justify the initial costs without guaranteed returns.
Complexity of Integration
Integrating PROFINET into existing systems can be complex.
It necessitates thorough planning and a detailed understanding of both current and future requirements.
Inadequate integration can lead to inefficiencies and disruptions, negating the potential benefits of the technology.
Need for Skilled Workforce
The success of PROFINET depends heavily on a technically skilled workforce capable of managing and maintaining the system.
This requires comprehensive training and, in some cases, hiring new talent with specialized skills—another potential challenge for companies.
Supplier Negotiation Techniques for PROFINET Implementation
Effective procurement and purchasing strategies can play a crucial role in the successful implementation of PROFINET.
Conduct Thorough Market Research
Before entering negotiations, conduct detailed market research to understand the offerings and pricing structures of various suppliers.
This equips you with the information needed to make informed decisions and leverage better deals.
Focus on Long-Term Collaboration
When negotiating with suppliers, prioritize long-term collaboration over short-term gains.
A strong, ongoing relationship with your supplier can lead to preferential pricing, better support, and access to future technological advancements.
Emphasize Total Cost of Ownership (TCO)
Rather than focusing solely on the upfront costs, consider the total cost of ownership, including maintenance, training, and potential downtime.
This holistic view ensures that you are making a cost-effective decision in the long run.
Current Market Conditions for PROFINET
Understanding the current market conditions can help in formulating effective procurement strategies for PROFINET.
Growing Demand for Industrial Automation
The global trend towards industrial automation is driving demand for advanced networking solutions like PROFINET.
This increased demand is pushing innovation and creating a competitive market landscape.
Technological Advancements
Technological advancements in industrial Ethernet solutions are continuously improving the capabilities and applications of PROFINET.
Staying updated with these advancements ensures that your factory gains a competitive edge.
Market Competition and Supplier Diversity
The presence of numerous suppliers in the PROFINET market encourages competitive pricing and innovation.
This diversity allows manufacturers to choose suppliers that best fit their specific needs and budget.
Best Practices for Implementing PROFINET
Successful implementation of PROFINET requires adherence to certain best practices.
Comprehensive Planning
Detailed planning is critical for the smooth integration of PROFINET.
Outline clear objectives, timelines, resources, and potential challenges to mitigate risks and ensure successful implementation.
Employee Training and Development
Invest in robust training programs to equip your workforce with the skills required to manage and maintain PROFINET systems effectively.
Continuous learning and development are key to leveraging the full potential of this technology.
Continuous Monitoring and Optimization
Regular monitoring and optimization of the PROFINET network ensure sustained performance and reliability.
Implementing feedback loops and performance metrics can help in identifying areas for improvement and ensuring long-term efficiency.
The Future of Japanese Manufacturing with PROFINET
The integration of PROFINET is a testament to Japan’s commitment to maintaining its leadership in global manufacturing.
Embracing Industry 4.0
PROFINET’s capabilities align seamlessly with the principles of Industry 4.0, enabling smart, connected, and highly efficient manufacturing environments.
This positions Japanese manufacturers to take full advantage of the digital transformation.
Sustaining Competitive Advantage
By adopting PROFINET, Japanese manufacturers can sustain and even enhance their competitive advantage in the global market.
The technology’s benefits in terms of efficiency, flexibility, and scalability ensure that Japan remains a hub of manufacturing excellence.
Driving Innovation
The continuous innovation driven by PROFINET will propel Japanese manufacturing towards new heights of technological advancement.
This not only benefits individual companies but also contributes to the overall growth of the manufacturing industry in Japan.
As we conclude, it’s evident that PROFINET holds immense potential in revitalizing Japanese manufacturing.
Its integration promises enhanced operational efficiency, flexibility, and future-readiness, essential for thriving in the competitive global market.
By addressing the associated challenges through strategic planning, training, and negotiation, companies can fully harness the benefits of this transformative technology.
In doing so, they not only safeguard their own futures but also contribute to the sustained leadership of Japanese manufacturing on the world stage.
資料ダウンロード
QCD調達購買管理クラウド「newji」は、調達購買部門で必要なQCD管理全てを備えた、現場特化型兼クラウド型の今世紀最高の購買管理システムとなります。
ユーザー登録
調達購買業務の効率化だけでなく、システムを導入することで、コスト削減や製品・資材のステータス可視化のほか、属人化していた購買情報の共有化による内部不正防止や統制にも役立ちます。
NEWJI DX
製造業に特化したデジタルトランスフォーメーション(DX)の実現を目指す請負開発型のコンサルティングサービスです。AI、iPaaS、および先端の技術を駆使して、製造プロセスの効率化、業務効率化、チームワーク強化、コスト削減、品質向上を実現します。このサービスは、製造業の課題を深く理解し、それに対する最適なデジタルソリューションを提供することで、企業が持続的な成長とイノベーションを達成できるようサポートします。
オンライン講座
製造業、主に購買・調達部門にお勤めの方々に向けた情報を配信しております。
新任の方やベテランの方、管理職を対象とした幅広いコンテンツをご用意しております。
お問い合わせ
コストダウンが利益に直結する術だと理解していても、なかなか前に進めることができない状況。そんな時は、newjiのコストダウン自動化機能で大きく利益貢献しよう!
(Β版非公開)