- お役立ち記事
- Reviving Japan: How Degraded Restoration Techniques are Revolutionizing Manufacturing
月間76,176名の
製造業ご担当者様が閲覧しています*
*2025年3月31日現在のGoogle Analyticsのデータより
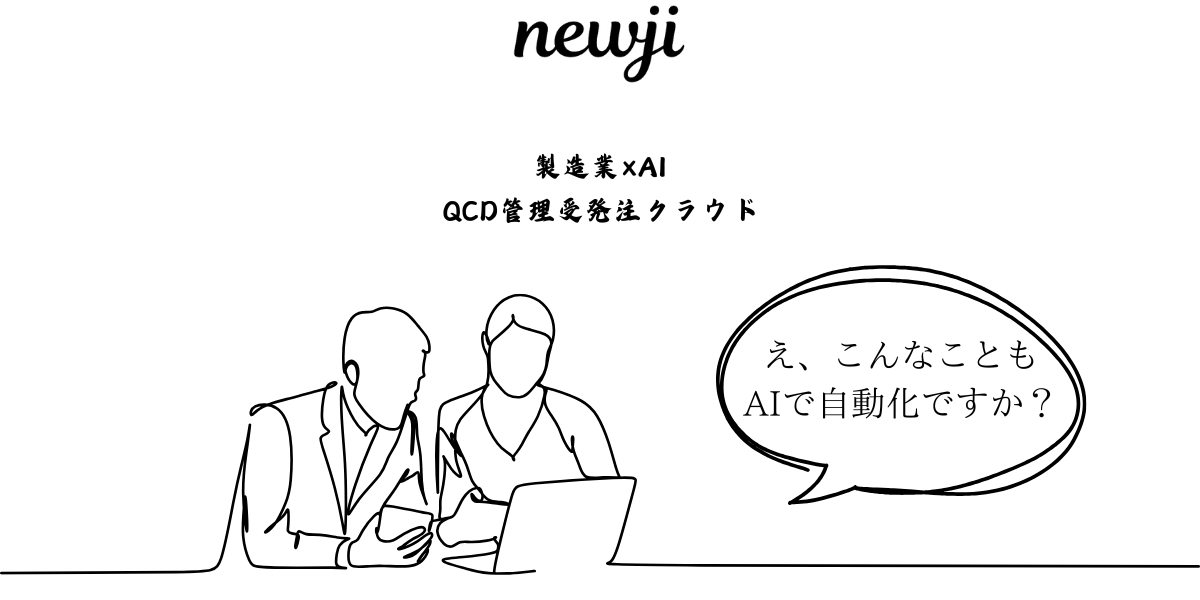
Reviving Japan: How Degraded Restoration Techniques are Revolutionizing Manufacturing
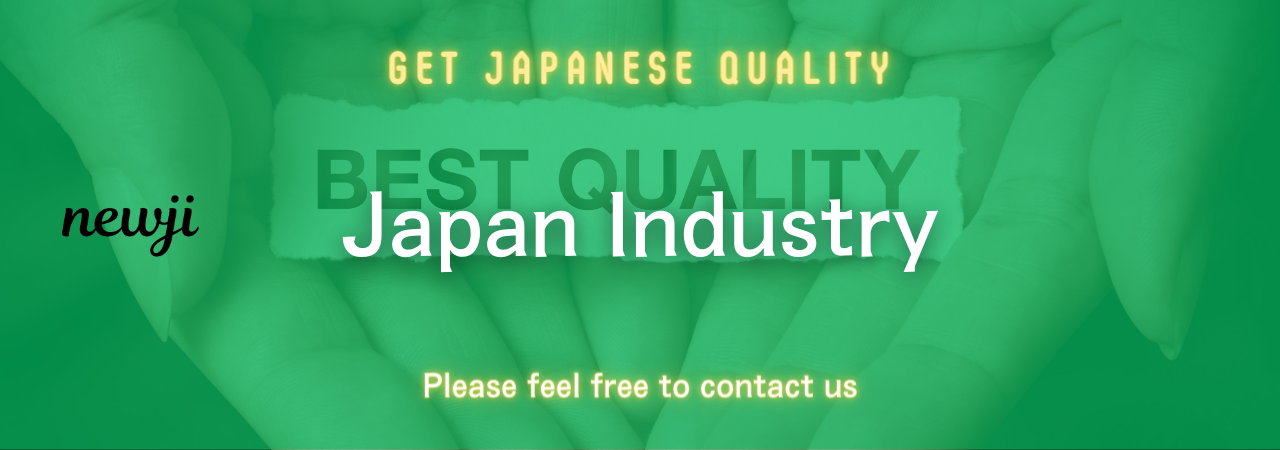
目次
Introduction to Degraded Restoration Techniques
In recent years, the manufacturing landscape has witnessed a remarkable transformation driven by the revival of traditional Japanese restoration techniques. These methodologies, once considered degraded or outdated, are now being reimagined and integrated into modern manufacturing processes. This resurgence not only preserves the rich heritage of Japanese craftsmanship but also introduces innovative practices that enhance efficiency, quality, and sustainability in manufacturing operations worldwide.
Degraded restoration techniques refer to traditional methods that have fallen out of mainstream use due to advancements in technology and shifts in manufacturing paradigms. However, their inherent value, characterized by meticulous attention to detail, resourcefulness, and sustainability, offers a unique edge in today’s competitive market. By revisiting and revitalizing these techniques, manufacturers can leverage a blend of historical wisdom and contemporary innovation to address current industry challenges.
The Renaissance of Japanese Manufacturing
Japan has long been recognized for its exceptional manufacturing prowess, often attributed to principles such as Kaizen (continuous improvement) and Just-In-Time (JIT) production. The current renaissance in Japanese manufacturing stems from a renewed focus on integrating traditional restoration techniques with modern manufacturing technologies. This fusion is creating a new paradigm that emphasizes quality, efficiency, and resilience.
Traditional Japanese manufacturing techniques, such as Kintsugi (the art of repairing broken pottery with gold) and Shibori (a method of dyeing cloth), exemplify the meticulous craftsmanship and innovative problem-solving approaches that characterize Japanese industry. By adapting these techniques to modern manufacturing contexts, Japanese companies are setting new standards for product quality and operational excellence.
Procurement and Purchasing Strategies in Japanese Manufacturing
Effective procurement and purchasing strategies are crucial for the successful integration of degraded restoration techniques into manufacturing processes. Japanese manufacturers employ several strategies to ensure the acquisition of high-quality materials and services that align with their restoration-focused approach.
Supplier Relationship Management
Building strong, long-term relationships with suppliers is a cornerstone of Japanese procurement strategies. Manufacturers prioritize collaboration and trust, fostering partnerships that enable mutual growth and innovation. This approach ensures a consistent supply of quality materials essential for restoration techniques.
Localized Sourcing
Japanese manufacturers often prefer sourcing materials locally to maintain quality control and reduce lead times. Local sourcing supports the preservation of traditional materials and techniques, ensuring that restoration methods remain authentic and effective.
Cost Management
Balancing cost and quality is a key aspect of Japanese procurement strategies. By working closely with suppliers, manufacturers negotiate favorable terms without compromising on material quality. This balance is crucial for maintaining the integrity of restoration techniques while ensuring economic viability.
Advantages of Japanese Restoration Techniques
Integrating traditional Japanese restoration techniques into manufacturing offers numerous advantages that contribute to overall business success.
Enhanced Quality and Durability
Traditional restoration techniques emphasize precision and attention to detail, resulting in products of superior quality and longevity. This focus on durability reduces the need for frequent replacements, leading to cost savings and increased customer satisfaction.
Sustainability and Resource Efficiency
Many restoration techniques embody sustainable practices, such as the efficient use of materials and energy. By adopting these methods, manufacturers can minimize waste, lower environmental impact, and achieve greater resource efficiency.
Innovation through Tradition
Reviving traditional techniques fosters innovation by providing a unique foundation upon which modern technologies can be built. This blend of old and new encourages creative problem-solving and the development of novel manufacturing solutions.
Competitive Differentiation
Manufacturers that incorporate restoration techniques can differentiate their products in the marketplace. The unique qualities imparted by these methods can serve as a distinctive selling point, attracting customers seeking authenticity and craftsmanship.
Disadvantages and Challenges
While the integration of degraded restoration techniques offers significant benefits, it also presents certain challenges that manufacturers must navigate.
Initial Implementation Costs
Adopting traditional restoration techniques may require substantial initial investment in training, equipment, and materials. These upfront costs can be a barrier, particularly for smaller manufacturers or those transitioning from entirely modern processes.
Skill Shortages
The specialized nature of restoration techniques necessitates a skilled workforce. Finding and retaining employees proficient in traditional methods can be challenging, leading to potential delays and increased labor costs.
Scalability Issues
Traditional restoration methods are often labor-intensive and may not easily scale to meet large production volumes. Manufacturers must find a balance between maintaining quality and achieving the desired scale, which can be difficult to manage.
Integration with Modern Technologies
Blending traditional techniques with modern manufacturing technologies requires careful planning and coordination. Ensuring compatibility and seamless integration can be complex, potentially leading to disruptions in production processes.
Supplier Negotiation Techniques with Japanese Suppliers
Effective negotiation with Japanese suppliers is essential for successful procurement of materials and services aligned with restoration techniques. Japanese suppliers value mutual respect, long-term relationships, and clear communication, which are integral to the negotiation process.
Understanding Cultural Nuances
Japanese business culture places significant emphasis on etiquette, humility, and consensus-building. Recognizing and respecting these cultural aspects can facilitate smoother negotiations and foster stronger supplier relationships.
Emphasizing Long-Term Partnerships
Rather than focusing solely on immediate gains, Japanese suppliers value long-term collaborations. Demonstrating a commitment to ongoing partnerships can enhance trust and reliability, leading to more favorable negotiation outcomes.
Clear Communication of Requirements
Clearly articulating material specifications, quality standards, and delivery expectations is crucial. Detailed communication helps ensure that suppliers fully understand and can meet the manufacturing requirements associated with restoration techniques.
Offering Fair and Transparent Terms
Fairness and transparency in negotiating terms, including pricing, payment schedules, and delivery timelines, are vital. Transparent negotiations build trust and reduce the likelihood of misunderstandings or conflicts.
Market Conditions Influencing Restoration Techniques
Several market conditions are driving the adoption of degraded restoration techniques in manufacturing. Understanding these factors is essential for manufacturers seeking to integrate traditional methods into their operations.
Consumer Demand for Quality and Authenticity
Modern consumers increasingly value products that offer quality, authenticity, and craftsmanship. Restoration techniques align well with these preferences, enabling manufacturers to meet and exceed customer expectations.
Environmental Sustainability Trends
Growing awareness of environmental issues has heightened demand for sustainable manufacturing practices. Restoration techniques, with their emphasis on resource efficiency and waste reduction, resonate with sustainability-focused consumers and businesses.
Technological Advancements
Advancements in technology have made it easier to integrate traditional restoration methods with modern manufacturing processes. Innovations in materials, automation, and digital tools enable the efficient application of restoration techniques on a larger scale.
Globalization and Supply Chain Dynamics
Global supply chain dynamics, including the need for localized production and resilient sourcing strategies, have spurred interest in traditional techniques that can be adapted to diverse manufacturing environments. Restoration methods offer flexibility and resilience in the face of global disruptions.
Best Practices for Integrating Restoration Techniques into Manufacturing
Successful integration of degraded restoration techniques into manufacturing requires a strategic approach that addresses various operational aspects. Adopting best practices ensures that the benefits of restoration methods are fully realized while mitigating potential challenges.
Comprehensive Training Programs
Investing in training programs to equip employees with the necessary skills in restoration techniques is essential. Comprehensive training ensures that staff can effectively apply traditional methods within modern manufacturing contexts.
Collaborative Supplier Partnerships
Establishing collaborative partnerships with suppliers enhances the quality and consistency of materials used in restoration techniques. Working closely with suppliers fosters innovation and ensures the reliable supply of high-quality materials.
Incremental Implementation
Implementing restoration techniques gradually allows manufacturers to manage risks and address challenges as they arise. An incremental approach facilitates continuous improvement and adaptation without disrupting overall production.
Leveraging Technology for Integration
Utilizing modern technologies, such as automation, data analytics, and digital tools, can streamline the integration of restoration techniques. Technology can enhance precision, reduce labor costs, and improve overall efficiency in manufacturing processes.
Quality Assurance and Continuous Improvement
Maintaining rigorous quality assurance practices ensures that restoration techniques meet high standards. Continuous improvement initiatives, inspired by principles like Kaizen, help refine and optimize restoration methods over time.
Case Studies: Successful Implementations
Examining real-world examples of manufacturers successfully integrating degraded restoration techniques provides valuable insights and inspiration for others seeking to adopt similar approaches.
Case Study 1: Automotive Component Manufacturing
A leading automotive component manufacturer in Japan revitalized its production line by integrating traditional restoration techniques to enhance the durability and precision of its components. By collaborating with local artisans and investing in specialized training, the company achieved a significant reduction in defect rates and improved overall product quality. The adoption of restoration methods also enabled the company to market its components as high-quality, long-lasting products, differentiating itself in a competitive market.
Case Study 2: Electronics Assembly
A prominent electronics manufacturer incorporated restoration techniques to refine its assembly processes, focusing on meticulous quality control and resource efficiency. By adopting traditional craftsmanship principles, the company minimized waste and enhanced the reliability of its electronic products. The integration of restoration methods led to increased customer satisfaction and a stronger reputation for quality in the electronics industry.
Case Study 3: Textile Manufacturing
A Japanese textile manufacturer embraced Shibori dyeing techniques to create unique, high-quality fabrics. By combining traditional dyeing methods with modern machinery, the company was able to scale production while maintaining the intricate patterns and superior quality associated with Shibori. This approach attracted a niche market of customers seeking authentic, handcrafted textiles, boosting the company’s market presence and profitability.
Future Outlook: The Role of Restoration Techniques in Manufacturing
The future of manufacturing is poised to increasingly incorporate traditional restoration techniques, driven by the ongoing pursuit of quality, sustainability, and innovation. As manufacturers continue to navigate evolving market demands and technological advancements, the integration of restoration methods will likely play a pivotal role in shaping industry standards and practices.
Emphasis on Sustainable Manufacturing
Sustainability will remain a central focus in manufacturing, with restoration techniques offering effective solutions for reducing waste and conserving resources. Manufacturers that prioritize sustainable practices will gain a competitive advantage and align with global environmental objectives.
Technological Synergy
The continued synergy between traditional restoration methods and cutting-edge technologies will unlock new possibilities for manufacturing innovation. Technologies such as artificial intelligence, robotics, and the Internet of Things (IoT) will enhance the application and scalability of restoration techniques, driving efficiency and precision.
Global Adoption and Adaptation
As global manufacturers recognize the value of restoration techniques, there will be a broader adoption and adaptation across various industries. This global diffusion will foster cross-cultural collaboration and the exchange of best practices, further enriching manufacturing processes.
Educational and Institutional Support
Educational institutions and industry bodies will play a crucial role in sustaining the knowledge and practice of restoration techniques. By incorporating these methods into curricula and providing industry support, the longevity and evolution of restoration-focused manufacturing practices will be ensured.
Conclusion
The revival of degraded restoration techniques in Japanese manufacturing represents a harmonious blend of tradition and innovation. By integrating these time-honored methods with modern manufacturing practices, Japanese companies are not only preserving their cultural heritage but also driving advancements in quality, sustainability, and efficiency. For manufacturers worldwide, embracing restoration techniques offers a pathway to differentiate products, enhance operational resilience, and meet the evolving demands of the global market. As the manufacturing industry continues to evolve, the lessons learned from Japan’s restoration-focused approach will undoubtedly influence and inspire future developments in the field.
資料ダウンロード
QCD管理受発注クラウド「newji」は、受発注部門で必要なQCD管理全てを備えた、現場特化型兼クラウド型の今世紀最高の受発注管理システムとなります。
ユーザー登録
受発注業務の効率化だけでなく、システムを導入することで、コスト削減や製品・資材のステータス可視化のほか、属人化していた受発注情報の共有化による内部不正防止や統制にも役立ちます。
NEWJI DX
製造業に特化したデジタルトランスフォーメーション(DX)の実現を目指す請負開発型のコンサルティングサービスです。AI、iPaaS、および先端の技術を駆使して、製造プロセスの効率化、業務効率化、チームワーク強化、コスト削減、品質向上を実現します。このサービスは、製造業の課題を深く理解し、それに対する最適なデジタルソリューションを提供することで、企業が持続的な成長とイノベーションを達成できるようサポートします。
製造業ニュース解説
製造業、主に購買・調達部門にお勤めの方々に向けた情報を配信しております。
新任の方やベテランの方、管理職を対象とした幅広いコンテンツをご用意しております。
お問い合わせ
コストダウンが利益に直結する術だと理解していても、なかなか前に進めることができない状況。そんな時は、newjiのコストダウン自動化機能で大きく利益貢献しよう!
(β版非公開)