- お役立ち記事
- Revolutionizing Efficiency: A Management Review of Japanese Manufacturing Strategies
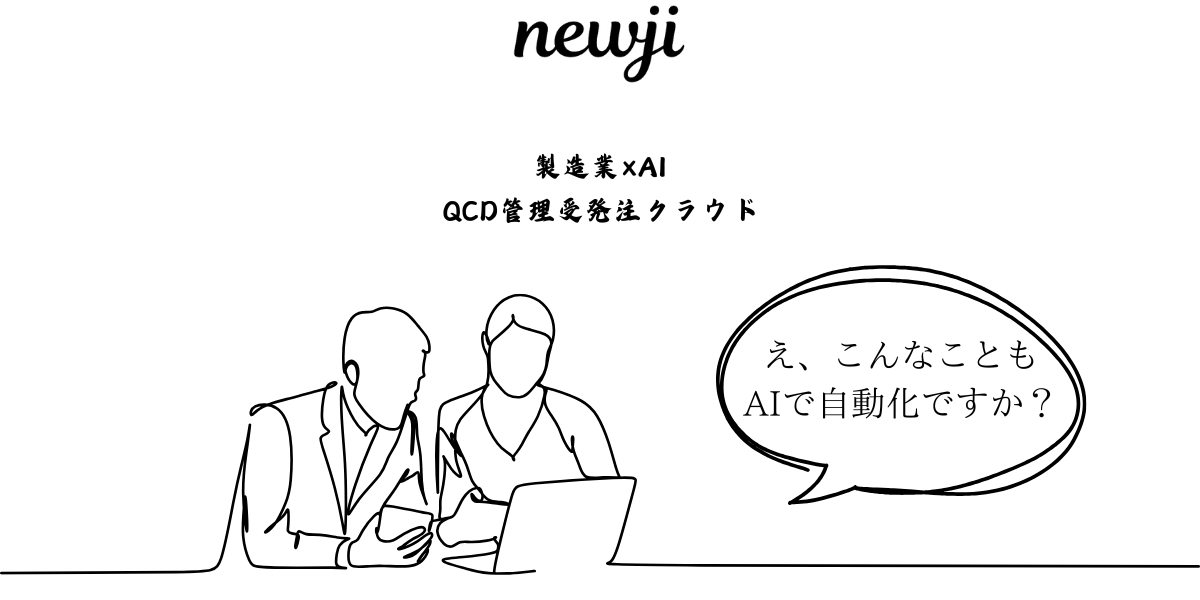
Revolutionizing Efficiency: A Management Review of Japanese Manufacturing Strategies
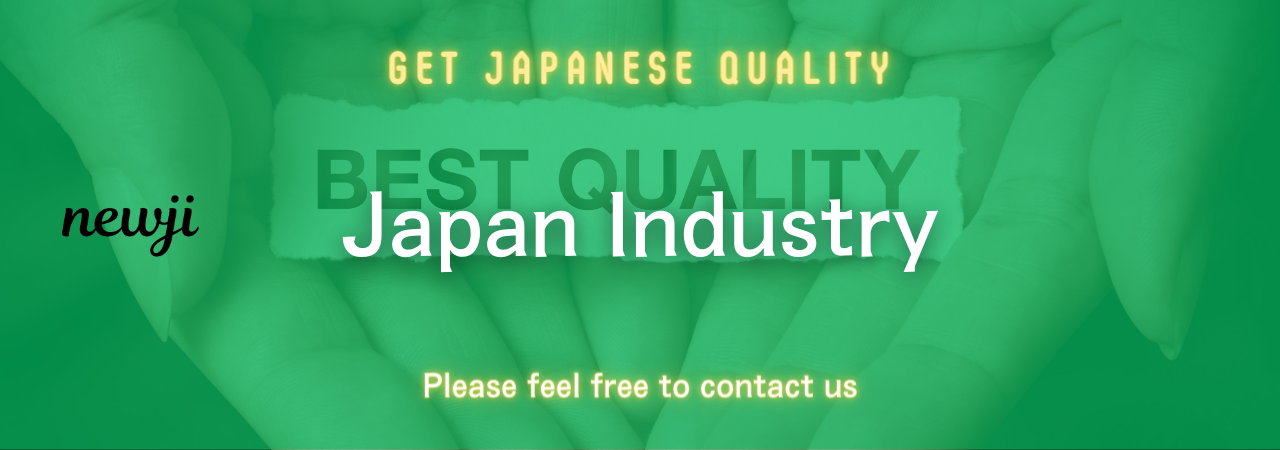
目次
Introduction to Japanese Manufacturing Efficiency
Japanese manufacturing has long been heralded for its exceptional efficiency and innovative strategies.
This reputation stems from decades of refined processes and a deep-rooted cultural emphasis on quality and continuous improvement.
Companies worldwide seek to emulate these practices to enhance their own operations.
In this review, we explore the key strategies that have revolutionized efficiency in Japanese manufacturing, focusing on procurement and purchasing, supplier relationships, and overall production management.
Core Principles of Japanese Manufacturing
Kaizen: Continuous Improvement
The philosophy of Kaizen is central to Japanese manufacturing.
It emphasizes ongoing, incremental improvements in all aspects of production.
Employees at all levels are encouraged to suggest changes that can enhance efficiency and quality.
This collective approach ensures that small adjustments lead to significant long-term gains.
Just-In-Time (JIT) Production
Just-In-Time is a strategy that aims to reduce inventory costs by receiving goods only as they are needed in the production process.
This minimizes waste and ensures a smoother workflow.
JIT requires precise coordination with suppliers to align deliveries with production schedules.
The success of JIT hinges on reliable supplier relationships and accurate demand forecasting.
Lean Manufacturing
Lean Manufacturing focuses on maximizing value while minimizing waste.
It involves streamlining processes, eliminating non-essential activities, and optimizing resource use.
By adopting lean principles, Japanese manufacturers can produce high-quality products more efficiently and cost-effectively.
Procurement and Purchasing Strategies
Strategic Supplier Partnerships
Japanese companies often form close partnerships with their suppliers.
These relationships are built on trust, mutual respect, and shared goals.
Long-term collaborations encourage suppliers to invest in quality improvements and innovation.
In return, manufacturers provide consistent business and support, creating a win-win scenario.
Supplier Integration
Supplier integration involves aligning the operations and processes of suppliers with those of the manufacturer.
This can include sharing technological advancements, production forecasts, and quality standards.
Integrated suppliers can respond more rapidly to changes in demand, reducing lead times and enhancing overall efficiency.
Quality Control in Procurement
Quality is paramount in Japanese manufacturing.
Procurement processes are designed to ensure that only the highest-quality materials are sourced.
Stringent quality checks and audits are conducted regularly to maintain standards.
This focus on quality in purchasing directly influences the final product’s excellence.
Advantages of Japanese Manufacturing Strategies
High-Quality Products
The emphasis on quality at every stage of production results in superior products.
Customers receive reliable and well-crafted goods, fostering brand loyalty and market competitiveness.
Reduced Waste and Costs
Techniques like Just-In-Time and Lean Manufacturing significantly reduce waste.
This not only lowers production costs but also contributes to environmental sustainability.
Enhanced Flexibility
Japanese manufacturing strategies allow for greater flexibility in production.
Companies can quickly adapt to market changes and customer demands without disrupting the overall workflow.
Strong Supplier Relationships
Close partnerships with suppliers ensure a stable supply chain and foster innovation.
Reliable suppliers can adapt to the manufacturer’s needs, enhancing the overall efficiency of operations.
Disadvantages and Challenges
High Dependence on Suppliers
While strong supplier relationships are a strength, they also create dependence.
If a supplier fails to deliver or encounters issues, it can disrupt the entire production process.
Implementation Costs
Adopting strategies like Lean Manufacturing and JIT requires significant investment in training and technology.
Small and medium-sized enterprises may find these initial costs challenging to manage.
Cultural Barriers
Transferring Japanese manufacturing practices to other cultural contexts can be difficult.
Different business practices and workplace cultures may hinder the effective implementation of these strategies.
Risk of Over-Standardization
While standardization enhances efficiency, excessive standardization can stifle creativity and innovation.
Balancing efficiency with the need for innovation is crucial to maintaining a competitive edge.
Supplier Negotiation Techniques
Building Trust and Relationships
Effective negotiations are built on trust and long-term relationships.
Japanese manufacturers prioritize relationship-building over short-term gains.
This approach fosters cooperation and mutual respect, leading to more favorable negotiation outcomes.
Win-Win Negotiations
Japanese negotiation practices aim for win-win outcomes, where both parties benefit.
This contrasts with adversarial negotiation tactics and promotes sustainable partnerships.
Transparent Communication
Clear and honest communication is essential in negotiations.
Both parties share their expectations and constraints openly, reducing misunderstandings and conflicts.
Flexibility and Compromise
Flexibility in negotiations allows for creative solutions and compromises.
By understanding and accommodating each other’s needs, manufacturers and suppliers can reach mutually beneficial agreements.
Market Conditions and Adaptation
Globalization and Market Dynamics
Japanese manufacturers operate in a highly globalized market.
Adapting to diverse market conditions and consumer preferences is essential for maintaining competitiveness.
Technological Advancements
Staying abreast of technological advancements is crucial.
Japanese companies invest heavily in research and development to incorporate the latest technologies into their manufacturing processes.
Economic Fluctuations
Economic changes can impact production costs and demand.
Japanese manufacturers employ flexible strategies to mitigate the effects of economic volatility.
Environmental Considerations
Sustainability is increasingly important in global markets.
Japanese manufacturing strategies incorporate eco-friendly practices to meet environmental standards and consumer expectations.
Best Practices in Japanese Manufacturing
Continuous Training and Development
Investing in employee training ensures that the workforce is skilled and adaptable.
Continuous development programs keep employees updated on the latest manufacturing techniques and technologies.
Emphasis on Innovation
Innovation drives efficiency and competitiveness.
Japanese manufacturers encourage creative thinking and invest in new technologies to stay ahead in the market.
Robust Quality Management Systems
Implementing comprehensive quality management systems ensures consistency and excellence.
Regular audits and quality checks maintain high standards across all production stages.
Efficient Resource Management
Managing resources effectively reduces costs and enhances productivity.
Japanese companies optimize the use of materials, labor, and machinery to achieve maximum efficiency.
Case Studies of Successful Japanese Manufacturers
Toyota: Pioneer of Lean Manufacturing
Toyota’s implementation of Lean Manufacturing principles revolutionized the automotive industry.
Their focus on eliminating waste, continuous improvement, and supplier integration set new standards for efficiency and quality.
Honda: Innovation and Flexibility
Honda’s emphasis on innovation and flexibility has allowed it to adapt to changing market conditions.
Their robust R&D and responsive production systems ensure they remain competitive in the global market.
Panasonic: Diversification and Quality Control
Panasonic’s diversification into various electronics markets demonstrates the effectiveness of their quality control and procurement strategies.
Their ability to maintain high standards across diverse product lines underscores the strength of their manufacturing philosophies.
Implementing Japanese Strategies in Western Companies
Cultural Adaptation
Adopting Japanese manufacturing strategies requires cultural adaptation.
Western companies must align these practices with their own organizational cultures to ensure successful implementation.
Training and Education
Providing comprehensive training ensures that employees understand and can effectively apply Japanese methodologies.
Educational programs and workshops can facilitate the transition to new manufacturing practices.
Gradual Integration
Implementing changes gradually allows companies to adjust and refine processes without overwhelming the workforce.
Phased integration helps in identifying and addressing challenges early in the transition.
Leadership Commitment
Strong leadership is essential for driving the adoption of new strategies.
Leaders must demonstrate commitment to continuous improvement and support their teams throughout the implementation process.
Future Trends in Japanese Manufacturing
Automation and Industry 4.0
The integration of automation and Industry 4.0 technologies will further enhance efficiency in Japanese manufacturing.
Smart factories with interconnected systems enable real-time data analysis and decision-making, optimizing production processes.
Sustainability Initiatives
Sustainability will continue to be a major focus.
Japanese manufacturers are investing in green technologies and sustainable practices to meet global environmental standards and consumer demands.
Global Expansion
Expanding into new international markets presents opportunities and challenges.
Japanese companies are adapting their strategies to cater to diverse markets while maintaining their core manufacturing principles.
Advanced Robotics and AI
The use of advanced robotics and artificial intelligence will revolutionize manufacturing operations.
These technologies enhance precision, reduce labor costs, and increase production speeds, contributing to overall efficiency.
Conclusion
Japanese manufacturing strategies offer valuable lessons in efficiency, quality, and continuous improvement.
By adopting principles such as Kaizen, Lean Manufacturing, and strategic supplier partnerships, companies can enhance their own operations.
While challenges exist in implementing these strategies, the potential benefits make them a worthwhile investment.
As the manufacturing landscape evolves, the innovative and efficient approaches developed in Japan will continue to influence and inspire global industries.
資料ダウンロード
QCD調達購買管理クラウド「newji」は、調達購買部門で必要なQCD管理全てを備えた、現場特化型兼クラウド型の今世紀最高の購買管理システムとなります。
ユーザー登録
調達購買業務の効率化だけでなく、システムを導入することで、コスト削減や製品・資材のステータス可視化のほか、属人化していた購買情報の共有化による内部不正防止や統制にも役立ちます。
NEWJI DX
製造業に特化したデジタルトランスフォーメーション(DX)の実現を目指す請負開発型のコンサルティングサービスです。AI、iPaaS、および先端の技術を駆使して、製造プロセスの効率化、業務効率化、チームワーク強化、コスト削減、品質向上を実現します。このサービスは、製造業の課題を深く理解し、それに対する最適なデジタルソリューションを提供することで、企業が持続的な成長とイノベーションを達成できるようサポートします。
オンライン講座
製造業、主に購買・調達部門にお勤めの方々に向けた情報を配信しております。
新任の方やベテランの方、管理職を対象とした幅広いコンテンツをご用意しております。
お問い合わせ
コストダウンが利益に直結する術だと理解していても、なかなか前に進めることができない状況。そんな時は、newjiのコストダウン自動化機能で大きく利益貢献しよう!
(Β版非公開)