- お役立ち記事
- Revolutionizing Efficiency: How Palletizing Robots Are Transforming Japanese Manufacturing
月間77,185名の
製造業ご担当者様が閲覧しています*
*2025年2月28日現在のGoogle Analyticsのデータより
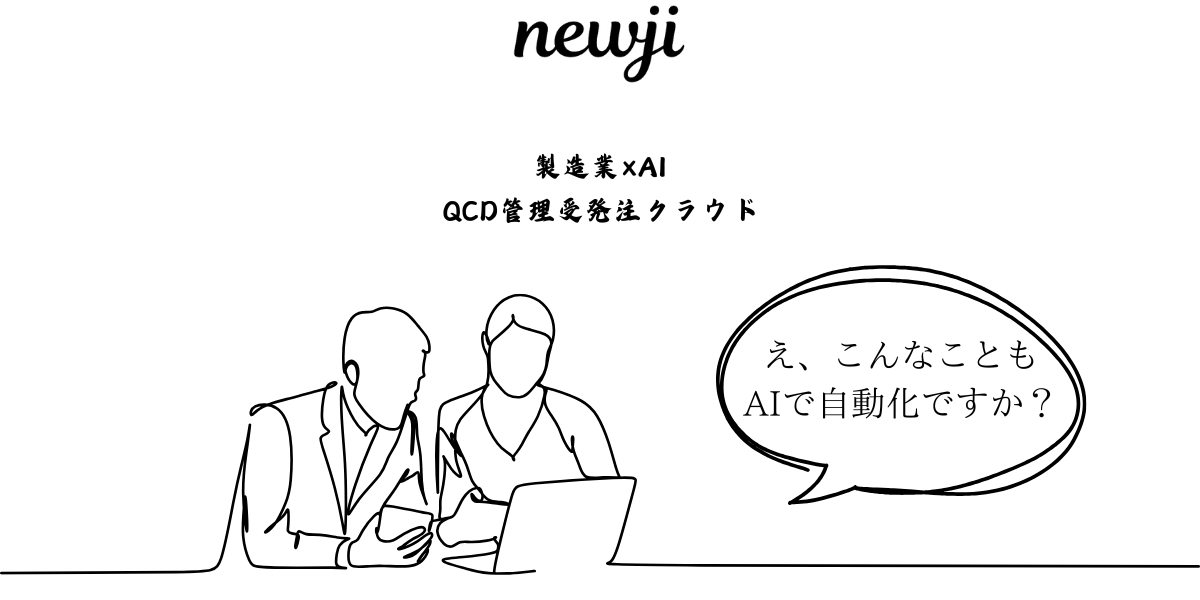
Revolutionizing Efficiency: How Palletizing Robots Are Transforming Japanese Manufacturing
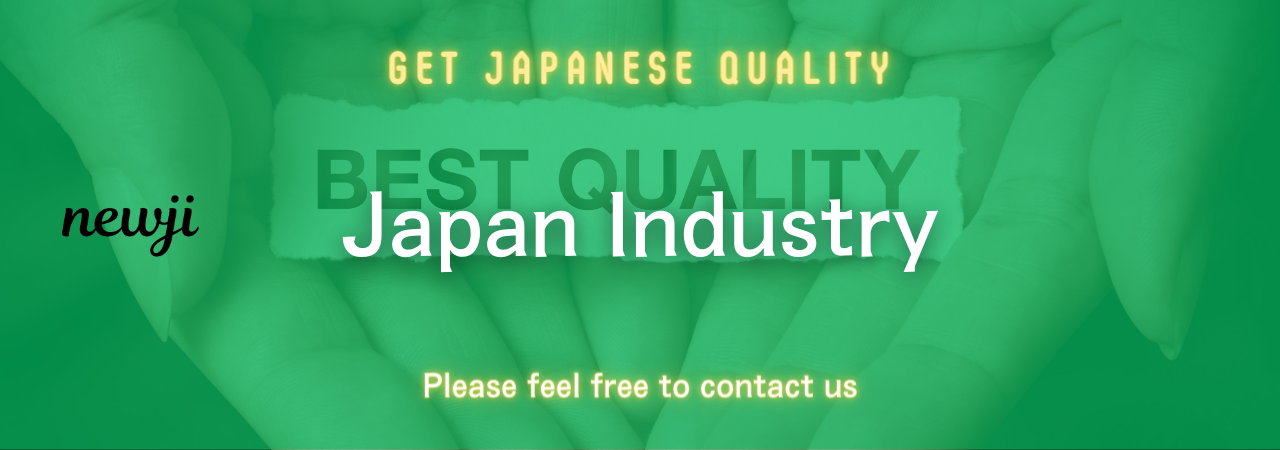
目次
The Role of Palletizing Robots in Modern Manufacturing
Palletizing robots have become a cornerstone of modern manufacturing operations.
These automated systems are designed to handle the stacking and arrangement of products onto pallets.
In Japanese manufacturing, the integration of palletizing robots is pivotal for enhancing production efficiency and maintaining high-quality standards.
The precision and speed offered by these robots surpass traditional manual methods.
This shift towards automation aligns with Japan’s reputation for technological advancement and efficiency.
Palletizing robots not only streamline the workflow but also contribute to the overall productivity of manufacturing facilities.
By adopting these robots, companies can achieve a higher output with consistent quality, meeting the demands of a competitive global market.
Moreover, the flexibility of palletizing robots allows for easy adjustments to different product sizes and packaging configurations.
This adaptability is essential in industries where product variations are frequent.
Japanese manufacturers leverage palletizing robots to maintain their edge in innovation and operational excellence.
The strategic implementation of these robots signifies a commitment to embracing cutting-edge technology for sustainable growth.
Advantages of Palletizing Robots in Japanese Manufacturing
Increased Efficiency
Palletizing robots significantly boost the efficiency of manufacturing processes.
They operate at high speeds, reducing the time required to stack products compared to manual labor.
This increased throughput allows factories to meet higher production targets without compromising quality.
Moreover, robots can work continuously without breaks, ensuring consistent output and minimizing downtime.
The automation of palletizing tasks frees up human workers to focus on more complex and value-added activities.
As a result, overall operational efficiency is enhanced, contributing to the competitiveness of Japanese manufacturing firms in the global market.
Improved Safety
Implementing palletizing robots enhances workplace safety by reducing the risk of injuries associated with manual pallet stacking.
Workers are no longer required to perform physically demanding and repetitive tasks that can lead to musculoskeletal disorders.
Robots handle heavy loads and operate in environments that may be hazardous to humans.
This shift not only protects workers but also decreases the likelihood of workplace accidents, leading to a safer and more compliant manufacturing environment.
Enhanced safety measures contribute to higher employee satisfaction and lower absenteeism rates, further increasing productivity.
Consistent Quality
Palletizing robots ensure consistent and precise stacking of products.
Their ability to maintain uniform placement reduces the variability associated with manual handling.
This consistency is crucial for preserving the integrity of products during transportation and storage.
High-quality palletizing minimizes the risk of product damage, returns, and customer dissatisfaction.
By maintaining stringent quality standards, Japanese manufacturers reinforce their reputation for reliability and excellence in the marketplace.
Cost Savings
While the initial investment in palletizing robots can be substantial, the long-term cost savings are significant.
Automation reduces the need for a large workforce dedicated to palletizing tasks, lowering labor costs.
Additionally, robots operate more efficiently, decreasing energy consumption and operational expenses.
The reduction in product damage and waste also contributes to cost savings.
Over time, the return on investment is realized through enhanced productivity, lower operational costs, and improved product quality.
Disadvantages and Challenges
High Initial Investment
The adoption of palletizing robots requires a considerable upfront investment.
The cost of purchasing, installing, and integrating these advanced systems can be a barrier for some manufacturers.
Additionally, companies may need to invest in training and support to ensure effective utilization of the robots.
Balancing the initial expenditure with the long-term benefits is a critical consideration for businesses evaluating this technology.
Technical Complexity
Palletizing robots are sophisticated systems that require specialized knowledge for operation and maintenance.
Manufacturers must ensure that their workforce is adequately trained to handle the technical aspects of these robots.
The complexity of programming and troubleshooting can pose challenges, especially for companies transitioning from manual methods.
Effective management of the technical intricacies is essential to maximize the benefits of automation.
Maintenance Requirements
Regular maintenance is essential to keep palletizing robots functioning optimally.
This includes routine inspections, software updates, and repairs as needed.
The reliance on high-precision machinery means that any downtime can disrupt manufacturing operations.
Establishing a comprehensive maintenance schedule and having access to skilled technicians are vital for minimizing disruptions and ensuring the longevity of the robotic systems.
Supplier Negotiation Techniques for Palletizing Robots
Building Strong Relationships
Establishing a robust relationship with suppliers is crucial in negotiating favorable terms for palletizing robots.
Japanese suppliers value trust and long-term partnerships, which can lead to better pricing and support.
Regular communication and mutual understanding foster a collaborative environment, making negotiations more effective.
Building strong relationships also encourages suppliers to prioritize your company’s needs and provide tailored solutions.
Understanding Supplier Capabilities
A thorough understanding of a supplier’s capabilities and limitations is essential for effective negotiation.
Assessing the technological expertise, production capacity, and service quality of potential suppliers helps in determining their suitability.
This knowledge enables companies to negotiate terms that align with their specific requirements and ensure that the supplier can meet their expectations.
Additionally, understanding the supplier’s strengths can highlight areas where collaboration can lead to mutual benefits.
Negotiating Terms and Pricing
Negotiating favorable terms and pricing requires a strategic approach.
Companies should leverage their purchasing power and demonstrate a clear understanding of the market to secure competitive prices.
Negotiations can include discussions on payment terms, delivery schedules, and warranty provisions.
Flexible terms that accommodate both parties’ needs contribute to a more successful and enduring partnership.
Additionally, negotiating value-added services, such as training and maintenance support, can enhance the overall value of the agreement.
Market Conditions for Palletizing Robots in Japan
Current Market Trends
The market for palletizing robots in Japan is experiencing significant growth, driven by the increasing demand for automation in manufacturing.
Technological advancements are leading to more sophisticated and versatile robotic systems.
There is a trend towards integrating artificial intelligence and machine learning to enhance the capabilities of palletizing robots.
This evolution enables robots to adapt to various tasks and improve their performance over time.
Moreover, the focus on sustainability is prompting manufacturers to adopt energy-efficient robotic solutions.
Technological Advancements
Japanese manufacturers are at the forefront of technological innovation in palletizing robotics.
Advancements in robotics technology have resulted in more precise, reliable, and user-friendly systems.
Improvements in sensor technology, motion control, and machine vision have enhanced the accuracy and efficiency of palletizing robots.
These technological strides enable robots to handle a wider range of products and adapt to changing production needs.
Continuous research and development in Japan contribute to the ongoing refinement and sophistication of palletizing robotics.
Competitive Landscape
The competitive landscape for palletizing robots in Japan is robust, with numerous established and emerging players.
Japanese suppliers are known for their high-quality products and commitment to excellence.
This reputation drives competition, as companies strive to differentiate themselves through innovation and superior service.
Furthermore, the presence of global competitors intensifies the market dynamics, pushing Japanese manufacturers to maintain their edge through continuous improvement and strategic partnerships.
Best Practices for Implementing Palletizing Robots
Assessing Production Needs
Before implementing palletizing robots, it is essential to conduct a thorough assessment of production needs.
This involves analyzing current workflows, identifying bottlenecks, and determining the specific requirements for automation.
Understanding the volume, variety, and complexity of products to be palletized helps in selecting the appropriate robotic system.
A comprehensive needs assessment ensures that the chosen solution aligns with the company’s operational objectives and maximizes the return on investment.
Selecting the Right Supplier
Choosing the right supplier is critical for the successful implementation of palletizing robots.
Factors to consider include the supplier’s experience, product quality, technological capabilities, and support services.
Evaluating the supplier’s track record and customer testimonials can provide insights into their reliability and performance.
Additionally, assessing the level of customization and flexibility offered by the supplier ensures that the robotic system can be tailored to meet specific production needs.
Ensuring Seamless Integration
Seamless integration of palletizing robots into existing manufacturing processes is vital for minimizing disruptions.
This involves aligning the robotic system with the company’s workflow, technology infrastructure, and operational protocols.
Collaborating closely with the supplier during the integration phase ensures that potential challenges are addressed proactively.
Proper planning and coordination facilitate a smooth transition to automated palletizing, enhancing overall efficiency without compromising ongoing production.
Training and Support
Comprehensive training and ongoing support are essential for maximizing the effectiveness of palletizing robots.
Employees should receive adequate training on operating, maintaining, and troubleshooting the robotic systems.
This knowledge empowers the workforce to manage the technology independently and respond to potential issues promptly.
Additionally, establishing a support structure with the supplier ensures access to technical assistance and updates as needed.
Investing in training and support enhances the longevity and performance of the palletizing robots, contributing to sustained operational success.
Procurement and Purchasing Strategies for Palletizing Robots
Evaluating Total Cost of Ownership
When procuring palletizing robots, it’s important to consider the total cost of ownership (TCO), which includes not only the initial purchase price but also ongoing expenses such as maintenance, training, and energy consumption.
Evaluating the TCO provides a comprehensive understanding of the financial commitment required and helps in making informed purchasing decisions.
Considering factors like the robot’s lifespan, reliability, and efficiency can influence the overall cost-effectiveness of the investment.
A thorough TCO analysis ensures that the chosen robotic system delivers value over the long term.
Sourcing from Japanese Suppliers
Sourcing palletizing robots from Japanese suppliers offers numerous advantages, including access to advanced technology, high-quality products, and reliable support.
Japanese manufacturers are renowned for their precision engineering and commitment to quality, ensuring that the robotic systems meet stringent standards.
Additionally, partnering with Japanese suppliers can provide insights into best practices and innovative solutions tailored to specific industry needs.
Leveraging the expertise and craftsmanship of Japanese manufacturers enhances the effectiveness and performance of palletizing robots in the procurement and purchasing process.
Leveraging Japanese Manufacturing Expertise
Japanese manufacturing expertise plays a crucial role in the successful implementation of palletizing robots.
The deep technical knowledge and experience of Japanese suppliers contribute to the design and functionality of advanced robotic systems.
Collaborating with these experts enables companies to benefit from customized solutions and innovative features that enhance production efficiency.
Furthermore, Japanese manufacturers often prioritize continuous improvement and quality control, ensuring that the palletizing robots remain at the forefront of technological advancement.
Leveraging this expertise drives operational excellence and fosters a culture of innovation within the manufacturing enterprise.
Case Studies of Successful Palletizing Robot Implementation
Several Japanese manufacturing companies have successfully integrated palletizing robots into their operations, demonstrating significant improvements in efficiency and quality.
One such example is Toyota, which implemented palletizing robots in its automotive assembly lines.
The robots streamlined the packing and stacking of automotive parts, reducing manual labor and increasing production speed.
This automation led to a notable decrease in errors and product damage, enhancing overall product quality.
Additionally, the implementation of palletizing robots allowed Toyota to optimize its workflow, resulting in higher throughput and reduced operational costs.
Another case is Panasonic, which adopted palletizing robots in its electronics manufacturing facilities.
The robots were integrated into the packaging process, handling a wide range of electronic components with precision.
This automation ensured consistent packaging quality and minimized the risk of product damage during transportation.
Panasonic reported a significant increase in production efficiency and a reduction in labor costs, highlighting the benefits of palletizing robot integration.
These case studies illustrate the tangible benefits of palletizing robots in Japanese manufacturing, showcasing improvements in efficiency, quality, and cost-effectiveness.
Future Outlook: The Evolution of Palletizing Robotics in Japanese Manufacturing
The future of palletizing robotics in Japanese manufacturing is poised for continued growth and innovation.
Advancements in artificial intelligence and machine learning are expected to enhance the capabilities of palletizing robots, enabling greater adaptability and intelligence in automated systems.
These technologies will allow robots to better handle complex tasks, optimize stacking patterns, and respond dynamically to changes in production demands.
Moreover, the integration of the Internet of Things (IoT) will facilitate real-time monitoring and data analysis, providing insights into robotic performance and enabling predictive maintenance.
This connectivity will enhance the reliability and efficiency of palletizing robots, further solidifying their role in manufacturing operations.
Sustainability will also play a significant role in the evolution of palletizing robotics.
Japanese manufacturers are increasingly focusing on eco-friendly practices, and palletizing robots will be designed to be more energy-efficient and environmentally sustainable.
This aligns with global trends towards greener manufacturing and supports companies in meeting their sustainability goals.
Furthermore, collaboration between Japanese suppliers and global partners will drive the development of more advanced and versatile palletizing solutions.
This collaboration will foster the exchange of knowledge and innovation, leading to the creation of robotic systems that cater to diverse industry needs.
As palletizing robotics continue to evolve, Japanese manufacturing will remain at the forefront of automation technology, driving efficiency, quality, and innovation in the global market.
Conclusion
Palletizing robots are transforming Japanese manufacturing by revolutionizing efficiency, improving safety, ensuring consistent quality, and delivering substantial cost savings.
Despite challenges such as high initial investments and technical complexities, the advantages of adopting these robots far outweigh the drawbacks.
Effective supplier negotiation, understanding market conditions, and implementing best practices are essential for successful integration.
Japanese manufacturers benefit from sourcing high-quality robotic systems and leveraging the expertise of seasoned suppliers.
As technology advances, palletizing robots will continue to evolve, further enhancing their impact on manufacturing operations.
Embracing this transformative technology positions Japanese manufacturing at the pinnacle of innovation and operational excellence, sustaining its competitive edge in the global economy.
資料ダウンロード
QCD管理受発注クラウド「newji」は、受発注部門で必要なQCD管理全てを備えた、現場特化型兼クラウド型の今世紀最高の受発注管理システムとなります。
ユーザー登録
受発注業務の効率化だけでなく、システムを導入することで、コスト削減や製品・資材のステータス可視化のほか、属人化していた受発注情報の共有化による内部不正防止や統制にも役立ちます。
NEWJI DX
製造業に特化したデジタルトランスフォーメーション(DX)の実現を目指す請負開発型のコンサルティングサービスです。AI、iPaaS、および先端の技術を駆使して、製造プロセスの効率化、業務効率化、チームワーク強化、コスト削減、品質向上を実現します。このサービスは、製造業の課題を深く理解し、それに対する最適なデジタルソリューションを提供することで、企業が持続的な成長とイノベーションを達成できるようサポートします。
製造業ニュース解説
製造業、主に購買・調達部門にお勤めの方々に向けた情報を配信しております。
新任の方やベテランの方、管理職を対象とした幅広いコンテンツをご用意しております。
お問い合わせ
コストダウンが利益に直結する術だと理解していても、なかなか前に進めることができない状況。そんな時は、newjiのコストダウン自動化機能で大きく利益貢献しよう!
(β版非公開)