- お役立ち記事
- Revolutionizing Efficiency: How the Kanban System Transformed Japanese Manufacturing
月間76,176名の
製造業ご担当者様が閲覧しています*
*2025年3月31日現在のGoogle Analyticsのデータより
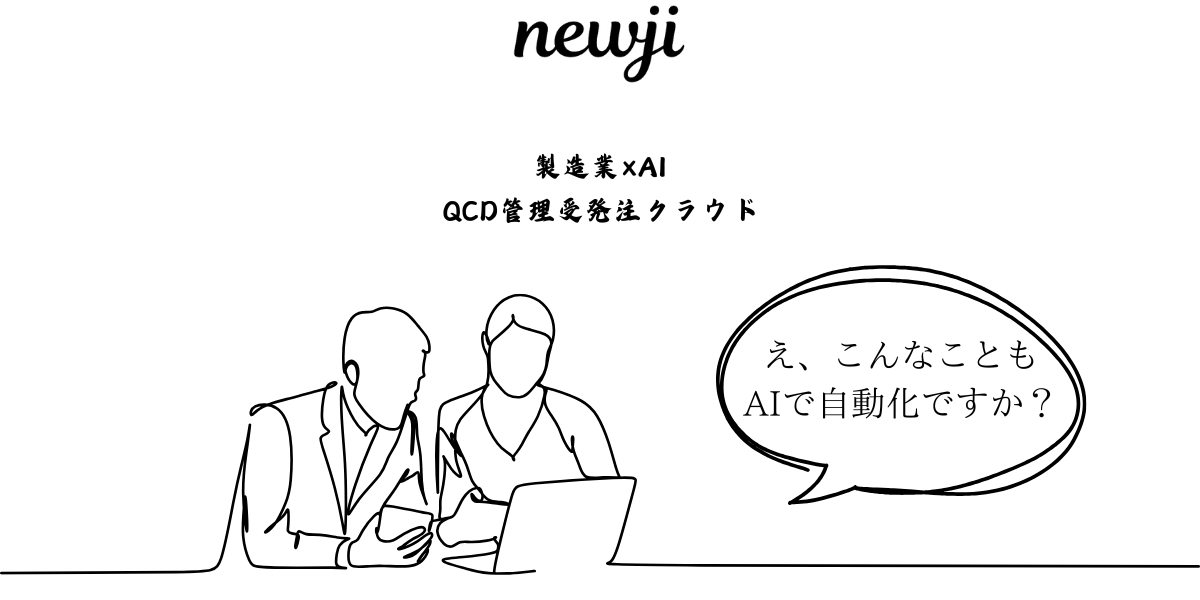
Revolutionizing Efficiency: How the Kanban System Transformed Japanese Manufacturing
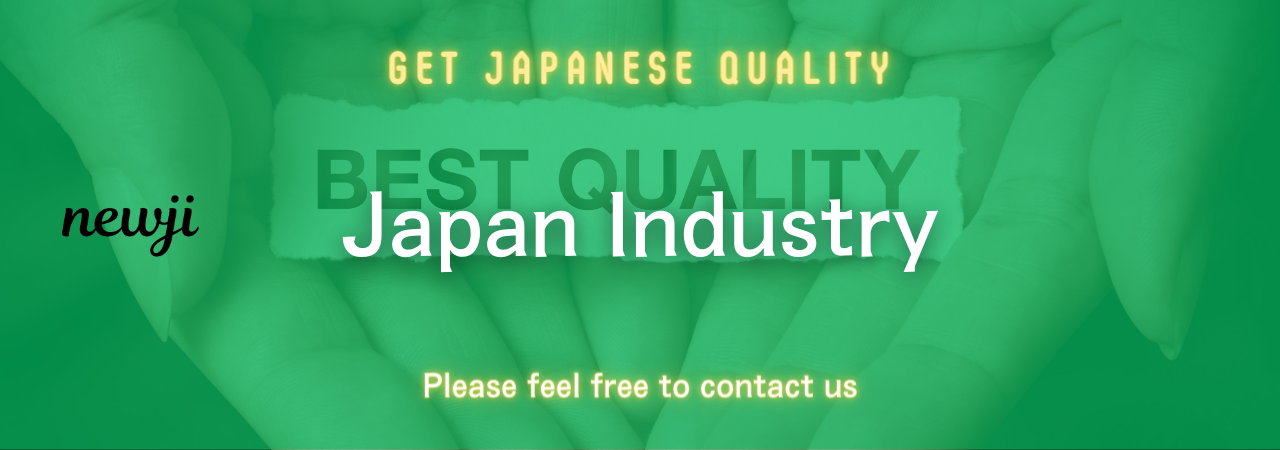
The Kanban system, originating from Japan, has long provided a significant competitive edge to Japanese manufacturers. Conceived by Taiichi Ohno of Toyota in the mid-20th century, this lean manufacturing tool has revolutionized efficiency and streamlined production processes. Its core principle revolves around just-in-time (JIT) inventory management, operating as a visual signaling system that helps manage workflow and inventory levels effectively.
目次
The Foundation of the Kanban System
Historical Context and Development
The genesis of Kanban can be traced back to Toyota’s efforts to enhance its production efficiency during the 1950s. Inspired by the way supermarkets managed their inventory—replenishing stocks according to consumption patterns—Ohno devised a system to facilitate smoother production line operations. By minimizing waste and ensuring timely resource availability, Toyota aimed to reduce costs and increase productivity.
Basic Principles of Kanban
Kanban is fundamentally based on the principles of lean manufacturing. Central to its operation are visual cues, typically in the form of cards or electronic signals, which indicate the status of the production process, inventory levels, or the need for materials. The underlying philosophy emphasizes continuous improvement (Kaizen), reduction of waste (Muda), and respect for human resources (respect for people). These principles guide the efficient flow and delivery of products.
Advantages of Implementing the Kanban System
Enhanced Efficiency and Productivity
The most prominent advantage of the Kanban system is its ability to enhance efficiency and productivity. By providing real-time visual indicators of production flow, operations can be dynamically adjusted to prevent bottlenecks and overproduction. This leads to optimal use of resources and a more streamlined production process that responds quickly to changes in demand.
Reduced Waste and Lower Inventory Costs
Kanban significantly reduces waste through its just-in-time approach. This means that materials and components are only ordered and manufactured as needed, drastically lowering storage costs and reducing idle inventory. The result is a leaner inventory system that minimizes excess and eliminates unnecessary expenditure on storage and obsolescence.
Improved Quality Control
Kanban’s focus on continuous improvement and waste reduction naturally extends to quality control. By implementing Kanban, manufacturers can achieve heightened quality assurance as defects are quickly identified and rectified before they impact subsequent production stages. Moreover, the system supports in-process inspections and encourages workers to take proactive measures, thus maintaining high-quality standards.
Increased Flexibility and Responsiveness
The dynamic nature of Kanban ensures that the production line can flexibly respond to changing demands. This adaptability is critical in today’s fast-paced market where consumer preferences fluctuate rapidly. By efficiently aligning production with real-time demand, manufacturers can reduce lead times and increase customer satisfaction.
Challenges and Disadvantages of Kanban
Initial Implementation Complexity
One of the significant challenges of adopting Kanban is the initial complexity of implementation. It requires a thorough understanding of current workflow processes and a strategic shift in operations management. Transitioning from traditional manufacturing practices to a Kanban system involves comprehensive employee training and significant changes in organizational culture.
Dependency on Predictable Demand
Kanban performs optimally in environments with relatively stable and predictable demand. In cases of highly volatile demand, the system may struggle to maintain efficiency. Overly fluctuating consumer demand can lead to frequent adjustments, causing delays and destabilizing production schedules.
Potential for Over-reliance on Visual Signals
While visual cues are instrumental in Kanban’s effectiveness, over-reliance on such signals can be a drawback. If these signals are misread or fail, it can lead to disruptions in the workflow. Therefore, it is crucial for organizations to maintain robust communication and backup systems to mitigate such risks.
Best Practices for Implementing Kanban
Conduct Thorough Process Analysis
Before implementing Kanban, conduct a detailed analysis of current workflows, inventory systems, and production processes. Understand the specific needs of your operations and identify areas where Kanban can provide the most benefit. This foundational knowledge is crucial for ensuring a smooth transition.
Train Employees and Foster a Culture of Continuous Improvement
Invest in comprehensive training programs for employees at all levels. Ensure they understand the principles of Kanban, their role within it, and how to use the system effectively. Moreover, foster a culture that embraces continuous improvement, encouraging employees to identify inefficiencies and contribute to ongoing process enhancements.
Gradual Implementation and Iterative Improvement
Implement Kanban gradually, starting with one segment of the production process before scaling up. This allows for fine-tuning and adapting the system based on real-world feedback. Use iterative improvement cycles to continuously refine operations, making necessary adjustments based on performance data.
Supplier Negotiation Techniques in a Kanban System
Establish Clear Communication Channels
Effective communication with suppliers is critical in a Kanban system. Establish clear protocols for real-time information sharing regarding inventory levels, order statuses, and production requirements. This transparency ensures that suppliers can respond promptly to changing demands and maintain seamless supply chain operations.
Negotiate Flexible Supply Agreements
Craft supply agreements that allow for flexibility in order quantities and delivery schedules. This flexibility is vital for accommodating the just-in-time nature of Kanban. By negotiating such terms, both parties can manage disruptions more effectively and ensure continuous production.
Build Strong Collaborative Relationships
Foster strong collaborative relationships with suppliers. This partnership approach encourages mutual understanding and cooperation, which are essential for achieving the goals of Kanban. Regularly engage with suppliers to discuss performance, address challenges, and explore opportunities for joint improvements.
Market Conditions Influencing Kanban Effectiveness
Stable Demand Patterns
Industries with relatively stable demand patterns are ideal for Kanban implementation. For such markets, the predictable nature of demand allows for the smooth functioning of just-in-time inventory systems without frequent disruptions.
Technological Advancements and Automation
The integration of advanced technologies and automation can significantly enhance the effectiveness of Kanban. Leveraging IoT-based monitoring systems, machine learning, and data analytics can provide real-time insights and predictive capabilities, further streamlining inventory management and production processes.
Global Supply Chain Dynamics
Global supply chain dynamics, including geopolitical factors, trade policies, and transportation logistics, can impact the efficiency of a Kanban system. It is essential to continuously monitor these conditions and develop strategies to mitigate potential disruptions, such as diversifying suppliers or establishing contingency plans.
Case Studies of Kanban in Action
Toyota’s Success with Kanban
Toyota’s pioneering use of Kanban has become the golden standard in the manufacturing industry. By effectively implementing the system, Toyota achieved remarkable improvements in production efficiency, waste reduction, and quality control. The company’s ability to swiftly adapt to market changes and deliver high-quality vehicles has cemented its reputation as a leader in innovative manufacturing practices.
Adoption in the Electronics Industry
The electronics industry, characterized by rapid technological advancements and short product lifecycles, has also benefited from Kanban. Companies like Sony and Panasonic have adopted the system to manage their complex production processes. Through Kanban, these firms have been able to maintain lean inventories, ensure timely delivery of components, and rapidly respond to evolving market demands.
Kanban in Healthcare Manufacturing
The healthcare manufacturing sector has increasingly embraced Kanban to improve its supply chain efficiency. Medical device manufacturers, for instance, use Kanban to manage the production of critical components and ensure compliance with stringent regulatory standards. This has resulted in faster production cycles and consistent product quality, enhancing overall operational effectiveness.
Conclusion
The Kanban system has undeniably transformed Japanese manufacturing, setting a benchmark for efficiency and productivity. By leveraging the principles of just-in-time inventory management, continuous improvement, and respect for people, it has enabled manufacturers to optimize their operations and deliver high-quality products consistently.
While the system presents certain challenges, best practices such as thorough process analysis, employee training, and gradual implementation can mitigate these issues, enabling organizations to fully reap the benefits of Kanban.
Additionally, effective supplier negotiation techniques and an understanding of market conditions play critical roles in ensuring the system’s success.
As industries continue to evolve, the adaptability and efficiency brought about by the Kanban system will remain pivotal in driving manufacturing excellence and maintaining a competitive edge in the global market.
資料ダウンロード
QCD管理受発注クラウド「newji」は、受発注部門で必要なQCD管理全てを備えた、現場特化型兼クラウド型の今世紀最高の受発注管理システムとなります。
ユーザー登録
受発注業務の効率化だけでなく、システムを導入することで、コスト削減や製品・資材のステータス可視化のほか、属人化していた受発注情報の共有化による内部不正防止や統制にも役立ちます。
NEWJI DX
製造業に特化したデジタルトランスフォーメーション(DX)の実現を目指す請負開発型のコンサルティングサービスです。AI、iPaaS、および先端の技術を駆使して、製造プロセスの効率化、業務効率化、チームワーク強化、コスト削減、品質向上を実現します。このサービスは、製造業の課題を深く理解し、それに対する最適なデジタルソリューションを提供することで、企業が持続的な成長とイノベーションを達成できるようサポートします。
製造業ニュース解説
製造業、主に購買・調達部門にお勤めの方々に向けた情報を配信しております。
新任の方やベテランの方、管理職を対象とした幅広いコンテンツをご用意しております。
お問い合わせ
コストダウンが利益に直結する術だと理解していても、なかなか前に進めることができない状況。そんな時は、newjiのコストダウン自動化機能で大きく利益貢献しよう!
(β版非公開)