- お役立ち記事
- Revolutionizing Efficiency: LCC Strategies Adapted in Japanese Manufacturing
Revolutionizing Efficiency: LCC Strategies Adapted in Japanese Manufacturing
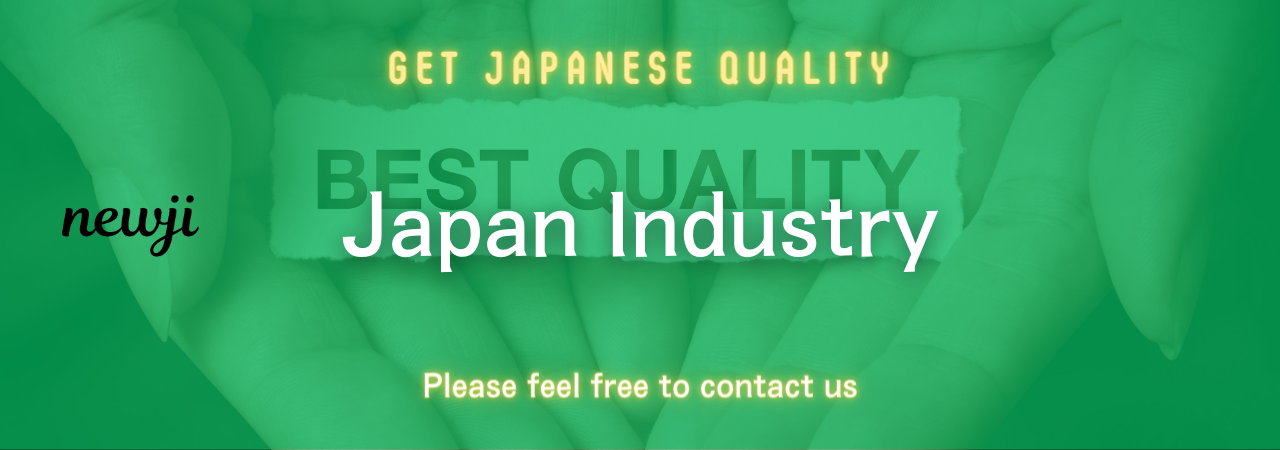
目次
Introduction
The manufacturing landscape across the globe is continually evolving, driven by technological advancements, competitive pressures, and the constant quest for efficiency.
In this context, Japanese manufacturing companies have consistently stood out for their Lean Production practices and operational efficiency.
One strategic approach that has significantly contributed to their success is the Low-Cost Country (LCC) sourcing strategy.
This article delves into the essence of LCC strategies adapted in Japanese manufacturing, offering a practical perspective on procurement and purchasing, advantages and disadvantages, supplier negotiation techniques, market conditions, and best practices.
Understanding LCC Sourcing Strategy
Low-Cost Country (LCC) sourcing refers to procuring products or services from countries with lower labor and production costs compared to the company’s home country.
For Japanese manufacturers, this strategy has proven to be highly effective in maintaining competitiveness while ensuring high-quality standards.
This approach involves identifying and working with suppliers in regions like Southeast Asia, Eastern Europe, or South America, where production costs are relatively low.
Importance in Japanese Manufacturing
Japanese manufacturers have always emphasized quality, efficiency, and cost-effectiveness.
LCC sourcing complements these principles by enabling companies to reduce expenses without compromising on quality.
This strategy also aligns well with Continuous Improvement (Kaizen) and Just-In-Time (JIT) production methodologies prevalent in Japanese manufacturing.
Advantages of LCC Sourcing in Japanese Manufacturing
Cost Reduction
The primary advantage of LCC sourcing is significant cost savings.
By procuring raw materials, components, or finished goods from low-cost regions, Japanese manufacturers can reduce their overall production expenses.
This cost advantage can be reinvested in R&D, technology upgrades, and process improvements.
Access to Diverse Suppliers
LCC sourcing provides Japanese manufacturers with access to an extensive network of suppliers.
This diversity ensures a steady supply of materials and components, reducing dependency on a single source and enhancing supply chain resilience.
Enhanced Competitiveness
Companies that successfully implement LCC strategies can offer competitive pricing for their products.
This competitiveness is crucial in maintaining market share and expanding into new markets.
Risk Mitigation
Diversifying the supplier base through LCC sourcing helps mitigate risks associated with geopolitical uncertainties, natural disasters, and other disruptions.
A well-distributed sourcing strategy ensures continuity in production, even if one region faces challenges.
Technological Advancements
Many low-cost countries are rapidly advancing in technology and infrastructure.
Collaborating with suppliers in these regions can lead to knowledge transfer and technological enhancements for Japanese manufacturers.
Such partnerships foster innovation and drive process improvements.
Disadvantages of LCC Sourcing in Japanese Manufacturing
Quality Control Issues
While cost savings are a significant advantage, maintaining consistent quality across LCC suppliers can be challenging.
Differences in production standards, quality management systems, and workforce skills may lead to quality issues that need stringent monitoring and control.
Communication Barriers
Working with suppliers in different countries often involves language and cultural differences.
These barriers can lead to misunderstandings and miscommunications, affecting the procurement process and overall efficiency.
Logistical Challenges
LCC sourcing involves long-distance transportation and extended supply chains.
This can result in longer lead times, potential delays, and increased shipping costs.
Effective logistics management is crucial to minimizing these challenges.
Intellectual Property Risks
Collaborating with suppliers in regions with different intellectual property (IP) regulations can expose Japanese manufacturers to IP theft or infringement risks.
Protecting proprietary technology and designs while working with LCC suppliers requires diligent legal and contractual measures.
Supplier Negotiation Techniques
Building Strong Relationships
Cultivating robust relationships with LCC suppliers is vital for successful negotiations.
Regular visits, transparent communication, and mutual trust foster collaboration and ensure suppliers are committed to meeting quality standards and delivery timelines.
Setting Clear Expectations
Clearly defining quality standards, delivery schedules, and performance metrics in contracts and agreements is essential.
Setting precise expectations helps minimize misunderstandings and ensures suppliers are aligned with your company’s requirements.
Leverage Volume for Better Deals
Japanese manufacturers can leverage their purchasing volume to negotiate favorable terms with LCC suppliers.
Bulk orders and long-term commitments often lead to cost reductions, favorable payment terms, and priority in production schedules.
Conducting Thorough Assessments
Before partnering with LCC suppliers, conducting comprehensive assessments is crucial.
Evaluate their production capabilities, quality management systems, financial stability, and compliance with ethical and environmental standards.
Emphasizing Continuous Improvement
Encouraging suppliers to adopt Continuous Improvement (Kaizen) practices promotes a culture of efficiency and quality.
Collaborative efforts to identify and implement process improvements benefit both parties in the long run.
Market Conditions and Trends
Rising Labor Costs
In some traditional LCC regions such as China, labor costs have been steadily increasing.
This trend necessitates exploring new low-cost regions or adopting automation to maintain cost advantages.
Focus on Sustainable Sourcing
Sustainability has become a critical focus in global manufacturing.
Japanese manufacturers are increasingly seeking LCC suppliers who adhere to sustainable practices, minimizing environmental impact and ensuring ethical labor conditions.
Technological Integration
Advanced technologies such as Artificial Intelligence (AI), Internet of Things (IoT), and Blockchain are being integrated into supply chain management.
These technologies enhance transparency, traceability, and efficiency in LCC sourcing strategies.
Geopolitical Uncertainties
Geopolitical uncertainties and trade conflicts can disrupt supply chains.
Diversifying LCC sourcing regions and building flexible supply chain networks are essential to mitigating such risks.
Best Practices for Effective LCC Sourcing
Strategic Supplier Selection
Select suppliers not solely based on cost but also on their capability to meet quality standards, delivery timelines, and compliance with ethical practices.
Regular Audits and Assessments
Conduct regular audits and assessments of LCC suppliers to ensure they maintain quality, compliance, and operational efficiency.
Frequent evaluations help identify and address potential issues proactively.
Investing in Technology
Implement advanced supply chain management technologies to enhance visibility, track shipments in real-time, and optimize inventory levels.
Technological integration fosters seamless coordination with LCC suppliers.
Training and Development
Invest in training and development programs for both in-house procurement teams and LCC suppliers.
Equipping teams with the necessary skills and knowledge ensures effective collaboration and quality management.
Collaborative Problem-Solving
Encourage a collaborative approach to problem-solving with LCC suppliers.
Sharing best practices, joint brainstorming sessions, and leveraging each other’s strengths lead to innovative solutions and continuous improvement.
Conclusion
Revolutionizing efficiency through LCC strategies has been a cornerstone of success for Japanese manufacturing companies.
The benefits of cost reduction, enhanced competitiveness, and access to diverse suppliers are significant.
However, challenges related to quality control, communication barriers, and logistical complexities require strategic management and diligent efforts.
By adopting best practices, leveraging technological advancements, and fostering strong supplier relationships, Japanese manufacturers can optimize their LCC sourcing strategies.
In an ever-changing global market, flexibility, adaptability, and a commitment to continuous improvement will remain crucial to maintaining a competitive edge.
The insights provided in this article aim to guide procurement and purchasing professionals in effectively implementing LCC strategies, reaping the benefits, and navigating the associated challenges.
With a focus on collaboration, innovation, and efficiency, Japanese manufacturers can continue to revolutionize their operations and achieve sustainable success in the international arena.
資料ダウンロード
QCD調達購買管理クラウド「newji」は、調達購買部門で必要なQCD管理全てを備えた、現場特化型兼クラウド型の今世紀最高の購買管理システムとなります。
ユーザー登録
調達購買業務の効率化だけでなく、システムを導入することで、コスト削減や製品・資材のステータス可視化のほか、属人化していた購買情報の共有化による内部不正防止や統制にも役立ちます。
NEWJI DX
製造業に特化したデジタルトランスフォーメーション(DX)の実現を目指す請負開発型のコンサルティングサービスです。AI、iPaaS、および先端の技術を駆使して、製造プロセスの効率化、業務効率化、チームワーク強化、コスト削減、品質向上を実現します。このサービスは、製造業の課題を深く理解し、それに対する最適なデジタルソリューションを提供することで、企業が持続的な成長とイノベーションを達成できるようサポートします。
オンライン講座
製造業、主に購買・調達部門にお勤めの方々に向けた情報を配信しております。
新任の方やベテランの方、管理職を対象とした幅広いコンテンツをご用意しております。
お問い合わせ
コストダウンが利益に直結する術だと理解していても、なかなか前に進めることができない状況。そんな時は、newjiのコストダウン自動化機能で大きく利益貢献しよう!
(Β版非公開)