- お役立ち記事
- Revolutionizing Efficiency: The Role of Task Scheduling in Japanese Manufacturing Success
Revolutionizing Efficiency: The Role of Task Scheduling in Japanese Manufacturing Success
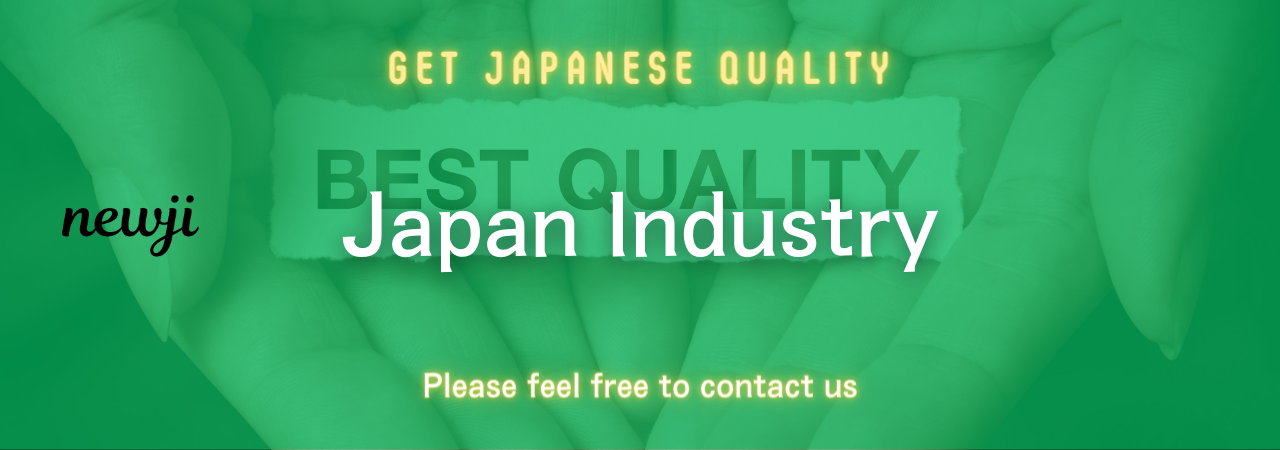
目次
Introduction
In the competitive landscape of global manufacturing, efficiency stands as a pivotal factor determining success. Japanese manufacturing, renowned for its precision and productivity, exemplifies how meticulous task scheduling can revolutionize operational workflows. Task scheduling involves the strategic arrangement of tasks to optimize resources, reduce waste, and enhance overall productivity. This article delves into the role of task scheduling in Japanese manufacturing, exploring its benefits, challenges, and best practices that contribute to the industry’s exemplary performance.
The Importance of Task Scheduling in Manufacturing
Task scheduling is integral to manufacturing as it ensures that processes run smoothly and efficiently. It involves planning the sequence of operations, allocating resources effectively, and minimizing downtime. Proper task scheduling leads to lower production costs, timely delivery of products, and higher customer satisfaction. In the context of Japanese manufacturing, task scheduling is deeply embedded in the culture of continuous improvement and lean manufacturing principles.
Enhancing Production Efficiency
Efficient task scheduling minimizes idle time and ensures that machinery and labor are utilized optimally. By aligning tasks in a logical sequence, manufacturers can reduce bottlenecks and maintain a steady flow of production. This not only accelerates the manufacturing process but also enhances the ability to meet tight deadlines.
Resource Optimization
Task scheduling facilitates the optimal use of resources, including materials, labor, and machinery. By planning tasks meticulously, manufacturers can ensure that resources are available when needed, reducing waste and avoiding unnecessary expenditures. This level of optimization is particularly crucial in Japanese manufacturing, where resource efficiency is a core principle.
Task Scheduling Techniques in Japanese Manufacturing
Japanese manufacturers employ a variety of task scheduling techniques tailored to their specific production needs. These techniques are often aligned with broader manufacturing philosophies such as Just-In-Time (JIT) and Total Quality Management (TQM).
Kanban System
The Kanban system is a visual task scheduling method that helps manage work by signaling the need to move materials within a production process. It promotes a just-in-time production approach, reducing inventory levels and minimizing waste. By using Kanban cards, Japanese manufacturers can easily track the status of tasks and ensure timely completion.
Heijunka (Level Scheduling)
Heijunka aims to level the production schedule by distributing the workload evenly over a specific period. This approach helps in mitigating the fluctuations in demand and prevents overburdening of resources. By implementing Heijunka, Japanese manufacturers can achieve a balanced workflow, enhancing both productivity and flexibility.
Lean Manufacturing
Lean manufacturing emphasizes the elimination of waste and the optimization of processes. Task scheduling within lean manufacturing involves identifying value-adding activities and ensuring that tasks are scheduled to support these activities. This method enhances efficiency by focusing on processes that contribute directly to customer value.
Advantages of Effective Task Scheduling
Effective task scheduling offers numerous benefits that collectively contribute to the success of manufacturing operations.
Increased Productivity
By organizing tasks efficiently, manufacturers can significantly boost their productivity. Effective scheduling ensures that all tasks are completed within the allocated time, thus maximizing output without compromising on quality.
Cost Reduction
Optimizing task schedules leads to a reduction in operational costs. By minimizing downtime and avoiding resource wastage, manufacturers can lower their production expenses and improve their profit margins.
Improved Quality
Task scheduling plays a crucial role in maintaining product quality. By ensuring that tasks are performed in a systematic manner, manufacturers can uphold high-quality standards and reduce the incidence of defects and errors.
Enhanced Flexibility
With a well-planned schedule, manufacturers can quickly adapt to changes in demand or unforeseen disruptions. This flexibility is essential for maintaining smooth operations and meeting customer expectations in a dynamic market environment.
Disadvantages and Challenges of Task Scheduling
While task scheduling offers significant advantages, it also presents certain challenges that manufacturers must navigate.
Complexity in Implementation
Implementing an effective task scheduling system can be complex, especially in large manufacturing operations with multiple processes and tasks. It requires careful planning, coordination, and often, the adoption of sophisticated software tools.
Resistance to Change
Employees may resist changes in task scheduling processes, particularly if it disrupts established workflows. Overcoming this resistance requires effective change management strategies and clear communication of the benefits.
Dependence on Accurate Data
Effective task scheduling relies on accurate and timely data regarding production processes, resource availability, and demand forecasts. Inaccurate data can lead to suboptimal scheduling decisions and negatively impact operations.
Balancing Flexibility and Stability
While flexibility is essential, excessive changes in task schedules can lead to instability and confusion. Striking the right balance between flexibility and stability is crucial for maintaining efficient operations.
Supplier Negotiation Techniques in Task Scheduling
Supplier negotiation is a critical aspect of procurement and purchasing, especially when task scheduling heavily relies on timely delivery of materials and components.
Building Strong Relationships
Japanese manufacturers emphasize building long-term relationships with suppliers. Strong relationships foster trust and collaboration, making it easier to negotiate favorable terms and ensure reliable supply chains.
Collaborative Planning
Engaging suppliers in the task scheduling process allows for better alignment of production schedules. Collaborative planning helps in anticipating demand fluctuations and ensures that suppliers can adjust their deliveries accordingly.
Performance Metrics
Setting clear performance metrics with suppliers enables manufacturers to measure and evaluate supplier performance. Metrics such as on-time delivery rates and quality standards are essential for maintaining efficient task scheduling.
Flexible Contracts
Negotiating flexible contracts that allow for adjustments in delivery schedules can help accommodate changes in production needs. Flexible contracts provide manufacturers with the agility to respond to market dynamics without disrupting operational flows.
Market Conditions Affecting Task Scheduling
The effectiveness of task scheduling is influenced by various market conditions that manufacturers must consider.
Demand Fluctuations
Variations in market demand can significantly impact task scheduling. Manufacturers need to be agile in adjusting their schedules to match changing demand patterns, ensuring that production levels are aligned with market needs.
Supply Chain Disruptions
Disruptions in the supply chain, such as delays in material deliveries or transportation issues, can adversely affect task scheduling. Proactive risk management and contingency planning are essential to mitigate the impact of such disruptions.
Technological Advancements
Advancements in technology, such as automation and data analytics, can enhance task scheduling processes. Staying abreast of technological trends and integrating relevant tools can lead to improved efficiency and competitiveness.
Regulatory Changes
Changes in regulations and industry standards can influence task scheduling practices. Manufacturers must stay informed about regulatory developments to ensure compliance and adjust their schedules as required.
Best Practices for Task Scheduling
Adopting best practices in task scheduling can help manufacturers achieve optimal efficiency and maintain a competitive edge.
Implementing Advanced Scheduling Software
Utilizing advanced scheduling software can streamline the task scheduling process. These tools offer features such as real-time monitoring, predictive analytics, and automated scheduling, which enhance precision and efficiency.
Continuous Improvement
Embracing a culture of continuous improvement enables manufacturers to regularly evaluate and refine their task scheduling practices. Techniques such as Kaizen encourage incremental improvements that accumulate over time, leading to significant enhancements in efficiency.
Training and Development
Investing in the training and development of employees ensures that the workforce is equipped with the necessary skills to manage and execute task schedules effectively. Well-trained personnel can better adapt to scheduling changes and contribute to operational excellence.
Integrating Lean Principles
Incorporating lean manufacturing principles into task scheduling helps minimize waste and enhance value creation. Techniques such as value stream mapping can identify inefficiencies and guide the optimization of task schedules.
Effective Communication
Clear and effective communication is essential for successful task scheduling. Ensuring that all stakeholders are informed about schedule changes and expectations fosters collaboration and prevents misunderstandings.
Conclusion
Task scheduling is a cornerstone of Japanese manufacturing success, driving efficiency, quality, and productivity. By employing sophisticated scheduling techniques, fostering strong supplier relationships, and adhering to best practices, Japanese manufacturers have set benchmarks in the global manufacturing arena. While challenges such as implementation complexity and market volatility exist, the continuous pursuit of improvement and adaptability ensures that task scheduling remains a dynamic and integral component of manufacturing excellence. As the manufacturing landscape continues to evolve, the principles and practices of effective task scheduling will undoubtedly remain essential for sustaining competitive advantage and achieving long-term success.
資料ダウンロード
QCD調達購買管理クラウド「newji」は、調達購買部門で必要なQCD管理全てを備えた、現場特化型兼クラウド型の今世紀最高の購買管理システムとなります。
ユーザー登録
調達購買業務の効率化だけでなく、システムを導入することで、コスト削減や製品・資材のステータス可視化のほか、属人化していた購買情報の共有化による内部不正防止や統制にも役立ちます。
NEWJI DX
製造業に特化したデジタルトランスフォーメーション(DX)の実現を目指す請負開発型のコンサルティングサービスです。AI、iPaaS、および先端の技術を駆使して、製造プロセスの効率化、業務効率化、チームワーク強化、コスト削減、品質向上を実現します。このサービスは、製造業の課題を深く理解し、それに対する最適なデジタルソリューションを提供することで、企業が持続的な成長とイノベーションを達成できるようサポートします。
オンライン講座
製造業、主に購買・調達部門にお勤めの方々に向けた情報を配信しております。
新任の方やベテランの方、管理職を対象とした幅広いコンテンツをご用意しております。
お問い合わせ
コストダウンが利益に直結する術だと理解していても、なかなか前に進めることができない状況。そんな時は、newjiのコストダウン自動化機能で大きく利益貢献しよう!
(Β版非公開)