- お役立ち記事
- Revolutionizing Electronics: The Art and Science of PCB Assembly in Japanese Manufacturing
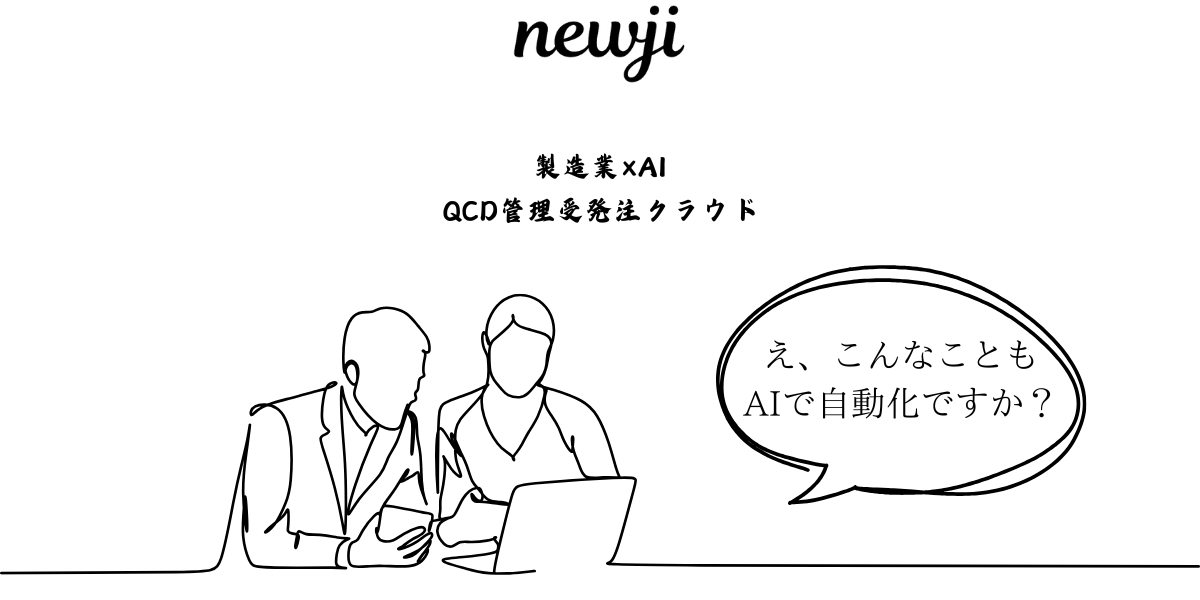
Revolutionizing Electronics: The Art and Science of PCB Assembly in Japanese Manufacturing
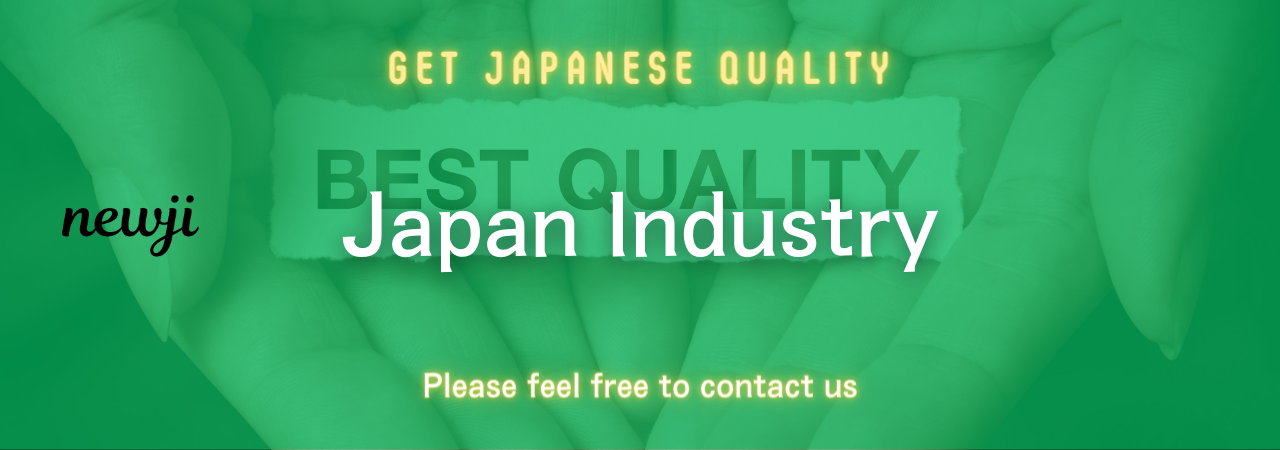
目次
Introduction to PCB Assembly in Japanese Manufacturing
Printed Circuit Board (PCB) assembly is a critical process in the electronics manufacturing industry.
Japan has long been recognized for its excellence in PCB assembly.
This reputation is built on a foundation of precision, quality, and innovative manufacturing techniques.
In this article, we will explore the art and science of PCB assembly in Japanese manufacturing from a procurement and purchasing perspective.
We will delve into the advantages and disadvantages, supplier negotiation techniques, market conditions, and best practices to equip you with comprehensive knowledge in this field.
The Importance of PCB Assembly in Electronics
PCB assembly is the process of mounting electronic components onto a PCB to create a functional electronic device.
It is a foundational step in the production of all electronic products, from smartphones to industrial machinery.
Quality PCB assembly ensures the reliability and performance of the final product.
In Japanese manufacturing, the emphasis on meticulous PCB assembly contributes significantly to the high standards of electronic goods produced.
Advantages of Japanese PCB Assembly
Unmatched Quality Standards
Japanese manufacturers are renowned for their stringent quality control measures.
They implement rigorous testing at every stage of the PCB assembly process.
This ensures that defects are minimized and the final products meet high reliability standards.
Advanced Technology and Automation
Japan is at the forefront of technological innovation in PCB assembly.
Advanced automated machinery enhances precision and efficiency.
Automation reduces human error and increases production speeds, enabling high-volume manufacturing without compromising quality.
Skilled Workforce
The craftsmanship of Japanese technicians is a key advantage.
Skilled workers ensure meticulous assembly and adherence to complex specifications.
Continuous training programs keep the workforce updated with the latest techniques and technologies.
Strong Supplier Networks
Japanese manufacturers maintain robust relationships with a network of reliable suppliers.
This ensures a steady supply of high-quality components and materials.
Strong supplier relationships also facilitate better pricing and more favorable contract terms.
Commitment to Innovation
Japanese companies invest heavily in research and development.
This commitment drives continuous improvement in PCB assembly processes and materials.
Innovative approaches lead to the development of more efficient and reliable electronic products.
Disadvantages of Japanese PCB Assembly
Higher Costs
Quality comes at a premium, and Japanese PCB assembly can be more expensive compared to other regions.
Higher labor and material costs contribute to the overall expense.
This can be a significant factor for companies operating on tight budgets.
Long Lead Times
The emphasis on quality and thoroughness can result in longer production times.
Strict quality control processes may extend the time required to complete an assembly.
This can impact project timelines, especially for urgent orders.
Language and Cultural Barriers
Working with Japanese suppliers may present language and cultural challenges.
Effective communication is essential for successful procurement and purchasing.
Misunderstandings can lead to delays and errors in order fulfillment.
Complex Negotiation Processes
Negotiating contracts with Japanese manufacturers can be more complex.
Japanese business practices emphasize building long-term relationships over quick deals.
This approach may require more time and effort to reach mutually beneficial agreements.
Supplier Negotiation Techniques
Building Strong Relationships
In Japanese business culture, trust and mutual respect are paramount.
Invest time in building a strong relationship with your suppliers.
Regular communication and visits can help establish a foundation of trust.
Understanding Cultural Norms
Familiarize yourself with Japanese business etiquette and cultural norms.
Respectful communication and patience are key.
Understanding the cultural context can facilitate smoother negotiations.
Clear Communication of Requirements
Clearly articulate your technical and quality requirements.
Provide detailed specifications and expectations to avoid misunderstandings.
Use clear and concise language to ensure that both parties are aligned.
Leverage Local Expertise
Consider hiring a local representative or consultant who understands the Japanese market.
Local expertise can bridge language and cultural gaps.
They can provide valuable insights and aid in negotiations.
Long-Term Partnership Focus
Emphasize the potential for a long-term partnership.
Japanese suppliers value stability and long-term collaborations.
Demonstrating your commitment to ongoing business can lead to more favorable terms.
Market Conditions in Japanese PCB Assembly
High Demand for Quality Electronics
Japan has a strong demand for high-quality electronic products.
This demand drives continuous advancements in PCB assembly technologies.
Manufacturers must stay abreast of market trends to meet evolving requirements.
Competitive Landscape
The PCB assembly market in Japan is highly competitive.
Numerous manufacturers vie for contracts, driving innovation and quality improvements.
Companies must differentiate themselves through superior quality, technology, and service.
Regulatory Environment
Japanese manufacturing is subject to strict regulatory standards.
Compliance with local and international regulations is mandatory.
Manufacturers must stay informed about regulatory changes and ensure adherence to all requirements.
Technological Advancements
Rapid technological advancements influence the PCB assembly market.
Adoption of Industry 4.0 technologies, such as IoT and smart manufacturing, is on the rise.
Manufacturers must integrate these technologies to stay competitive and meet market demands.
Supply Chain Dynamics
Global supply chain disruptions can impact PCB assembly in Japan.
Manufacturers need robust supply chain strategies to mitigate risks.
Diversifying suppliers and maintaining buffer inventories are effective strategies to ensure continuity.
Best Practices in Japanese PCB Assembly
Emphasize Quality Control
Implement comprehensive quality control measures at every stage of PCB assembly.
Regular inspections, testing, and adherence to standards are crucial.
Quality control helps prevent defects and ensures the reliability of the final product.
Adopt Lean Manufacturing Principles
Incorporate lean manufacturing principles to enhance efficiency.
Eliminate waste, streamline processes, and optimize resource utilization.
Lean practices contribute to cost savings and improved production timelines.
Invest in Training and Development
Provide continuous training for your workforce.
Skilled and knowledgeable employees are essential for maintaining high-quality standards.
Investing in training ensures that your team is equipped with the latest skills and knowledge.
Utilize Advanced Technologies
Adopt advanced technologies and automation in PCB assembly.
Invest in state-of-the-art machinery to enhance precision and efficiency.
Advanced technologies enable higher production volumes and better quality control.
Maintain Strong Supplier Relationships
Foster strong relationships with your suppliers.
Collaborate closely to ensure timely delivery and high-quality components.
Effective supplier relationships can lead to better pricing and more favorable contract terms.
Focus on Continuous Improvement
Implement a culture of continuous improvement within your organization.
Regularly review and refine assembly processes to enhance efficiency and quality.
Encourage feedback and innovation to drive ongoing improvements.
Procurement and Purchasing Strategies
Strategic Sourcing
Adopt strategic sourcing practices to identify and select the best suppliers.
Evaluate suppliers based on quality, reliability, cost, and innovation capabilities.
Strategic sourcing ensures that you partner with suppliers who align with your business goals.
Cost Management
Implement effective cost management strategies to control expenses.
Negotiate favorable pricing, bulk discounts, and long-term contracts.
Balancing cost with quality is crucial for maintaining profitability.
Risk Mitigation
Develop strategies to mitigate risks in the procurement process.
Identify potential risks such as supply chain disruptions, price volatility, and quality issues.
Implement contingency plans to address these risks proactively.
Supplier Evaluation and Selection
Conduct thorough evaluations when selecting suppliers.
Assess their capabilities, financial stability, and track record.
Supplier audits and site visits can provide deeper insights into their operations.
Contract Management
Effective contract management ensures that all parties adhere to agreed terms.
Clearly define expectations, deliverables, and performance metrics.
Regularly review contracts to ensure compliance and address any issues promptly.
Collaboration and Integration
Promote collaboration between procurement, manufacturing, and other departments.
Integrated processes enhance communication and alignment across the organization.
Collaborative efforts lead to more efficient and effective procurement outcomes.
Technology Integration in PCB Assembly
Automation and Robotics
Incorporate automation and robotics to enhance PCB assembly processes.
Automated systems improve precision, reduce errors, and increase production speeds.
Robots can handle repetitive tasks, allowing human workers to focus on more complex activities.
Industry 4.0 and Smart Manufacturing
Adopt Industry 4.0 principles to transform your manufacturing processes.
Integrate IoT devices, data analytics, and smart systems to optimize operations.
Smart manufacturing enhances visibility, decision-making, and overall efficiency.
Advanced Testing and Inspection
Utilize advanced testing and inspection technologies to ensure quality.
Automated optical inspection (AOI) and X-ray systems detect defects with high accuracy.
Advanced testing ensures that only high-quality PCBs proceed to the next stage.
Supply Chain Digitalization
Digitize your supply chain to improve transparency and efficiency.
Implement supply chain management software to track components and manage inventories.
Digitalization enhances coordination and reduces the risk of delays and errors.
Data Analytics and Predictive Maintenance
Leverage data analytics to gain insights into manufacturing processes.
Predictive maintenance uses data to anticipate equipment failures and schedule maintenance proactively.
Data-driven approaches enhance operational reliability and reduce downtime.
Case Studies: Success Stories in Japanese PCB Assembly
Case Study 1: Enhancing Quality Through Lean Practices
A leading electronics manufacturer partnered with a Japanese PCB assembly provider to implement lean manufacturing principles.
Through waste elimination and process optimization, they achieved a 20% increase in production efficiency.
Quality improvements led to a 15% reduction in defects, enhancing overall product reliability.
Case Study 2: Leveraging Automation for Scalability
An international smartphone company collaborated with a Japanese PCB assembler to integrate advanced automation systems.
The automation increased production capacity by 30%, enabling the company to meet rising demand without compromising quality.
Enhanced scalability supported the company’s global expansion plans.
Case Study 3: Building a Long-Term Supplier Relationship
A medical device manufacturer established a long-term partnership with a Japanese PCB assembly supplier.
Regular communication and joint development initiatives fostered innovation.
The collaboration resulted in the development of custom PCBs tailored to specific medical applications, enhancing product performance and market competitiveness.
Challenges and Solutions in Japanese PCB Assembly Procurement
Managing High Costs
Challenge: High costs associated with Japanese PCB assembly can strain budgets.
Solution: Implement strategic sourcing to negotiate better pricing.
Explore bulk purchasing and long-term contracts to secure favorable terms.
Additionally, optimize internal processes to reduce waste and control expenses.
Overcoming Language Barriers
Challenge: Language differences can hinder effective communication.
Solution: Hire bilingual staff or engage professional translation services.
Utilize clear and concise communication methods, supplemented with visual aids and detailed documentation.
Ensuring Timely Deliveries
Challenge: Longer lead times can impact project schedules.
Solution: Plan ahead and account for extended production times in your project timelines.
Establish buffer stocks and work closely with suppliers to monitor progress and address delays promptly.
Maintaining Consistent Quality
Challenge: Sustaining high-quality standards across all orders.
Solution: Implement robust quality control procedures and conduct regular audits.
Collaborate with suppliers to address any quality issues promptly and ensure continuous improvement.
Future Trends in Japanese PCB Assembly
Miniaturization and High-Density Interconnects
The trend towards smaller, more compact electronic devices drives the need for miniaturization in PCB assembly.
High-density interconnects (HDI) allow for more complex and efficient circuit designs, meeting the demands of advanced electronics.
Sustainable Manufacturing Practices
Sustainability is becoming increasingly important in manufacturing.
Japanese PCB assemblers are adopting eco-friendly practices, such as reducing waste, using recyclable materials, and minimizing energy consumption.
Sustainable manufacturing aligns with global environmental standards and consumer preferences.
Integration of Artificial Intelligence
Artificial Intelligence (AI) is revolutionizing PCB assembly processes.
AI-driven systems can optimize production schedules, predict maintenance needs, and enhance quality control.
The integration of AI leads to smarter, more efficient manufacturing operations.
Expansion of Smart Electronics
The rise of smart electronics, including IoT devices and wearable technology, is expanding the scope of PCB assembly.
Manufacturers must adapt to the unique requirements of smart devices, such as flexibility and connectivity.
Global Supply Chain Resilience
Building resilient global supply chains is crucial for future PCB assembly.
Japanese manufacturers are enhancing supply chain strategies to withstand disruptions and ensure continuity.
Resilience efforts include diversifying suppliers, increasing local sourcing, and leveraging digital supply chain technologies.
Conclusion
Japanese PCB assembly stands out in the global electronics manufacturing landscape due to its unwavering commitment to quality, advanced technology, and skilled workforce.
While challenges such as higher costs and cultural barriers exist, strategic procurement and purchasing practices can effectively address these issues.
By building strong supplier relationships, adopting best practices, and embracing technological advancements, companies can fully leverage the advantages of Japanese PCB assembly.
As the electronics industry continues to evolve, Japanese manufacturers are well-positioned to lead in innovation and quality, making them valuable partners in the realm of PCB assembly.
References for Further Reading
- “Japanese Manufacturing: The Real Future of Creating Value,” by Takashi Yamaguchi
- “Lean Thinking: Banish Waste and Create Wealth in Your Corporation,” by James P. Womack and Daniel T. Jones
- “The Toyota Way: 14 Management Principles from the World’s Greatest Manufacturer,” by Jeffrey K. Liker
- “Industry 4.0: The Industrial Internet of Things,” by Alasdair Gilchrist
- “Supply Chain Management: Strategy, Planning, and Operation,” by Sunil Chopra and Peter Meindl
資料ダウンロード
QCD調達購買管理クラウド「newji」は、調達購買部門で必要なQCD管理全てを備えた、現場特化型兼クラウド型の今世紀最高の購買管理システムとなります。
ユーザー登録
調達購買業務の効率化だけでなく、システムを導入することで、コスト削減や製品・資材のステータス可視化のほか、属人化していた購買情報の共有化による内部不正防止や統制にも役立ちます。
NEWJI DX
製造業に特化したデジタルトランスフォーメーション(DX)の実現を目指す請負開発型のコンサルティングサービスです。AI、iPaaS、および先端の技術を駆使して、製造プロセスの効率化、業務効率化、チームワーク強化、コスト削減、品質向上を実現します。このサービスは、製造業の課題を深く理解し、それに対する最適なデジタルソリューションを提供することで、企業が持続的な成長とイノベーションを達成できるようサポートします。
オンライン講座
製造業、主に購買・調達部門にお勤めの方々に向けた情報を配信しております。
新任の方やベテランの方、管理職を対象とした幅広いコンテンツをご用意しております。
お問い合わせ
コストダウンが利益に直結する術だと理解していても、なかなか前に進めることができない状況。そんな時は、newjiのコストダウン自動化機能で大きく利益貢献しよう!
(Β版非公開)