- お役立ち記事
- Revolutionizing Healthcare: How Japanese Manufacturing Leads the Way in Injectable Innovation
月間76,176名の
製造業ご担当者様が閲覧しています*
*2025年3月31日現在のGoogle Analyticsのデータより
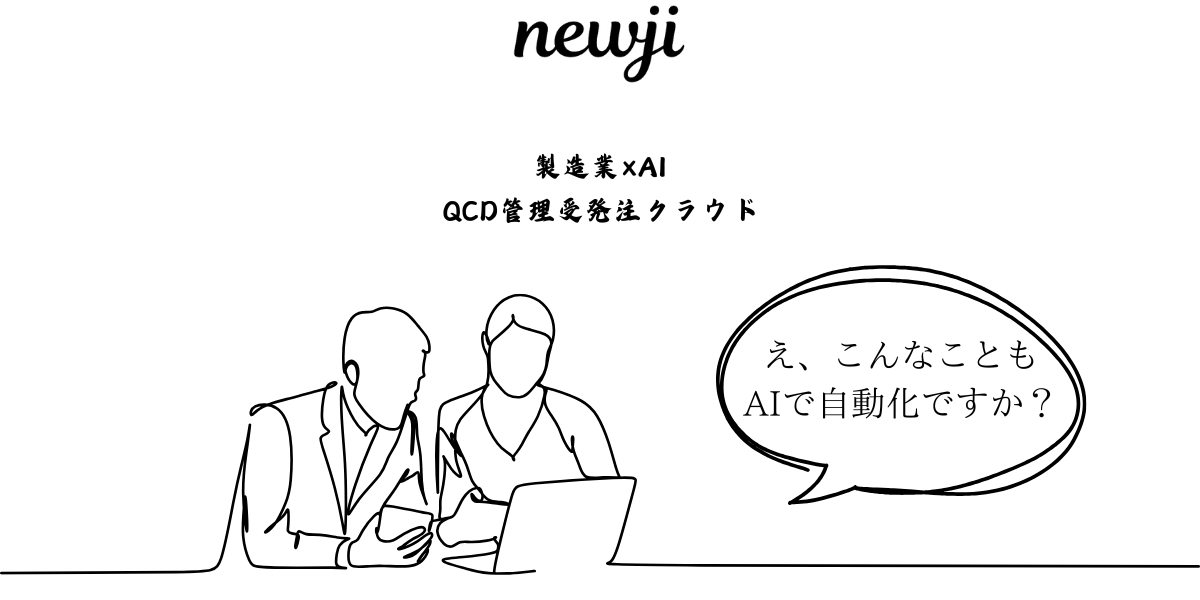
Revolutionizing Healthcare: How Japanese Manufacturing Leads the Way in Injectable Innovation
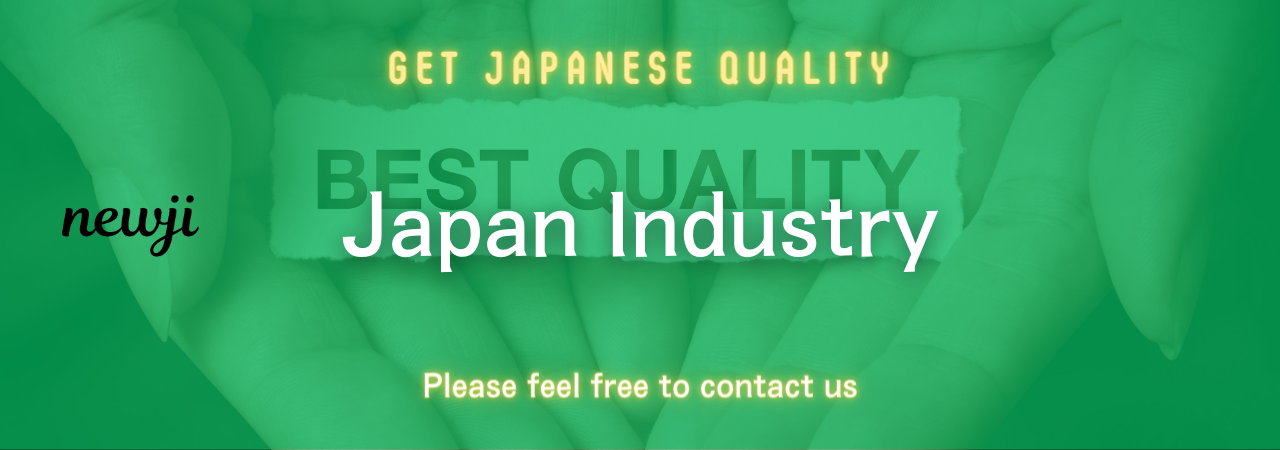
目次
Introduction to Japanese Injectable Manufacturing
Japanese manufacturing has long been synonymous with precision, quality, and innovation. In the healthcare sector, particularly in injectable products, Japanese manufacturers are setting new standards. Their commitment to excellence is revolutionizing the way injectable medicines are produced, ensuring higher efficacy, safety, and accessibility. This article delves into how Japanese manufacturing is leading the way in injectable innovation, exploring the benefits, challenges, and best practices from a procurement and purchasing perspective.
Advantages of Japanese Manufacturing in Injectable Innovation
Superior Quality Control
Japanese manufacturers implement stringent quality control measures that exceed international standards. This meticulous attention to detail ensures that injectable products are free from contaminants and maintain consistent potency.
Advanced Technology and Automation
Investment in cutting-edge technology and automation processes allows Japanese companies to enhance production efficiency. This not only reduces the time-to-market for new injectables but also minimizes human error, ensuring higher product reliability.
Strong Research and Development (R&D)
A robust R&D culture drives continuous innovation in the Japanese pharmaceutical sector. This focus on research leads to the development of novel injectable formulations and delivery systems, addressing unmet medical needs and improving patient outcomes.
Reliable Supply Chains
Japanese manufacturers are known for their resilient and well-organized supply chains. This reliability ensures a steady supply of injectable products, which is crucial for maintaining patient trust and meeting global healthcare demands.
Regulatory Compliance
Strict adherence to global regulatory standards, such as those set by the FDA and EMA, positions Japanese-manufactured injectables as trustworthy and safe options in the international market.
Challenges in Procuring Japanese Injectable Products
Higher Production Costs
The emphasis on quality and advanced technology often results in higher production costs. This can translate to increased prices for buyers, posing budgetary challenges for procurement departments.
Cultural and Communication Barriers
Navigating cultural nuances and language differences can complicate negotiations and collaborations with Japanese suppliers. Misunderstandings may lead to delays and increased transaction costs.
Lengthy Lead Times
While Japanese manufacturing is highly efficient, the complexity and precision involved can lead to longer lead times. This may affect procurement planning and inventory management.
Regulatory Hurdles
Adhering to international regulatory requirements can be complex and time-consuming. Ensuring compliance across different jurisdictions requires thorough knowledge and coordination.
Limited Flexibility
The highly standardized production processes in Japanese manufacturing may limit flexibility in custom orders or rapid changes in product specifications, potentially hindering responsiveness to market demands.
Supplier Negotiation Techniques with Japanese Manufacturers
Building Trust and Long-term Relationships
In Japanese business culture, establishing trust is paramount. Investing time in building strong, long-term relationships with suppliers can lead to more favorable negotiation outcomes and collaborative partnerships.
Understanding Cultural Norms
Respecting Japanese business etiquette, such as formal greetings, punctuality, and modesty, can facilitate smoother negotiations. Demonstrating cultural sensitivity shows respect and can enhance mutual understanding.
Clear Communication of Requirements
Providing detailed and precise specifications minimizes misunderstandings. Clear communication ensures that suppliers fully understand the procurement needs, leading to better alignment and product outcomes.
Leveraging Volume and Commitment
Negotiating larger order volumes or committing to long-term contracts can provide leverage in securing better pricing and terms. Japanese suppliers value reliability and may offer discounts for sustained partnerships.
Emphasizing Quality and Compliance
Highlighting the importance of quality and regulatory compliance aligns with Japanese manufacturers’ priorities. Demonstrating a commitment to maintaining high standards can facilitate trust and cooperation.
Market Conditions for Japanese Injectable Manufacturing
Global Demand for Injectables
The global demand for injectable medications is on the rise, driven by advancements in biotechnology and increasing prevalence of chronic diseases. Japanese manufacturers are well-positioned to meet this growing need with their expertise and innovation.
Competitive Landscape
While Japanese manufacturers are leaders in quality, the competitive landscape includes players from Europe, North America, and emerging markets. Differentiating through superior quality and advanced technology is crucial for maintaining market leadership.
Technological Advancements
Rapid technological advancements, such as the development of smart syringes and improved drug delivery systems, are shaping the injectable market. Japanese manufacturers are at the forefront of these innovations, enhancing product functionality and patient experience.
Regulatory Environment
Evolving regulatory frameworks globally require manufacturers to continuously adapt. Japanese companies’ proactive approach to compliance ensures they remain competitive and can swiftly navigate regulatory changes.
Supply Chain Resilience
Global disruptions, such as pandemics or geopolitical tensions, have highlighted the importance of resilient supply chains. Japanese manufacturers’ well-organized supply chain networks provide stability and reliability in uncertain times.
Best Practices in Procuring Injectables from Japan
Thorough Supplier Evaluation
Conduct comprehensive assessments of potential suppliers, evaluating their manufacturing capabilities, quality control processes, and compliance history. This ensures alignment with procurement standards and reduces risks.
Establishing Clear Contracts
Draft clear and detailed contracts outlining specifications, quality requirements, delivery schedules, and payment terms. This clarity prevents disputes and sets mutual expectations.
Regular Performance Reviews
Implement a system for ongoing performance evaluations of suppliers. Regular reviews help identify areas for improvement, ensure adherence to agreements, and foster continuous quality enhancement.
Collaboration on R&D
Engage suppliers in collaborative research and development initiatives. Joint R&D efforts can lead to innovative products and shared intellectual property benefits, strengthening the partnership.
Implementing Risk Management Strategies
Develop and enforce risk management plans to address potential supply chain disruptions, quality issues, and regulatory changes. Proactive risk management ensures procurement continuity and reliability.
Case Studies of Japanese Injectable Manufacturers
Takeda Pharmaceutical Company
Takeda is renowned for its precision in injectable drug manufacturing. Their investment in advanced automation and quality control systems has resulted in high-quality products that meet stringent global standards.
Astellas Pharma Inc.
Astellas focuses on innovative injectable therapies for chronic conditions. Their collaborative approach with global partners ensures the development of effective and accessible treatments, enhancing patient care worldwide.
Hosei Pharmaceutical Co.
Hosei Pharmaceutical specializes in biosimilars and complex injectables. Their commitment to R&D and quality has positioned them as a trusted supplier in the international market, catering to diverse healthcare needs.
Future Trends in Injectable Manufacturing
Personalized Medicine
The shift towards personalized medicine is driving the demand for customized injectable therapies. Japanese manufacturers are leveraging their advanced technology to develop tailored treatments that meet individual patient requirements.
Sustainable Manufacturing Practices
Environmental sustainability is becoming increasingly important. Japanese manufacturers are adopting green manufacturing practices, reducing waste, and minimizing their carbon footprint in the production of injectables.
Integration of Artificial Intelligence (AI)
AI and machine learning are being integrated into manufacturing processes to enhance predictive maintenance, optimize production schedules, and improve quality control, leading to more efficient and reliable injectable manufacturing.
Expansion into Emerging Markets
Japanese manufacturers are expanding their presence in emerging markets, catering to the growing healthcare needs in regions such as Asia-Pacific, Latin America, and Africa. This expansion is facilitated by strategic partnerships and localized production facilities.
Advanced Drug Delivery Systems
Innovation in drug delivery systems, such as microneedle patches and smart injectors, is transforming the injectable market. Japanese companies are at the forefront of developing these advanced systems, improving patient compliance and therapeutic outcomes.
Strategies for Successful Procurement from Japan
Developing Strategic Partnerships
Forming strategic alliances with Japanese manufacturers fosters collaboration, innovation, and mutual growth. These partnerships enable shared resources, knowledge transfer, and enhanced market access.
Continuous Market Research
Stay informed about market trends, technological advancements, and regulatory changes in Japan. Continuous market research ensures that procurement strategies are aligned with the evolving landscape.
Investing in Supplier Development
Support suppliers in enhancing their capabilities through training, technology upgrades, and process improvements. Supplier development initiatives lead to higher quality products and stronger, more reliable partnerships.
Optimizing Inventory Management
Implement effective inventory management systems to balance supply and demand. Techniques such as just-in-time (JIT) inventory and demand forecasting help reduce costs and minimize excess stock.
Embracing Digital Procurement Tools
Leverage digital procurement platforms to streamline processes, enhance transparency, and improve communication with Japanese suppliers. Digital tools facilitate efficient order management, tracking, and performance analysis.
Conclusion
Japanese manufacturing is at the forefront of injectable innovation, driven by a commitment to quality, technological advancement, and continuous improvement. For procurement and purchasing professionals, partnering with Japanese manufacturers offers access to high-quality, reliable, and innovative injectable products. While challenges such as higher costs and cultural barriers exist, effective negotiation techniques, strategic partnerships, and best procurement practices can mitigate these hurdles. As the healthcare landscape continues to evolve, Japanese manufacturers are well-positioned to lead the way in developing the next generation of injectable therapies, ultimately revolutionizing patient care worldwide.
資料ダウンロード
QCD管理受発注クラウド「newji」は、受発注部門で必要なQCD管理全てを備えた、現場特化型兼クラウド型の今世紀最高の受発注管理システムとなります。
ユーザー登録
受発注業務の効率化だけでなく、システムを導入することで、コスト削減や製品・資材のステータス可視化のほか、属人化していた受発注情報の共有化による内部不正防止や統制にも役立ちます。
NEWJI DX
製造業に特化したデジタルトランスフォーメーション(DX)の実現を目指す請負開発型のコンサルティングサービスです。AI、iPaaS、および先端の技術を駆使して、製造プロセスの効率化、業務効率化、チームワーク強化、コスト削減、品質向上を実現します。このサービスは、製造業の課題を深く理解し、それに対する最適なデジタルソリューションを提供することで、企業が持続的な成長とイノベーションを達成できるようサポートします。
製造業ニュース解説
製造業、主に購買・調達部門にお勤めの方々に向けた情報を配信しております。
新任の方やベテランの方、管理職を対象とした幅広いコンテンツをご用意しております。
お問い合わせ
コストダウンが利益に直結する術だと理解していても、なかなか前に進めることができない状況。そんな時は、newjiのコストダウン自動化機能で大きく利益貢献しよう!
(β版非公開)