- お役立ち記事
- Revolutionizing Industrial Success: The High Precision World of Japanese Steel Component OEM Manufacturing
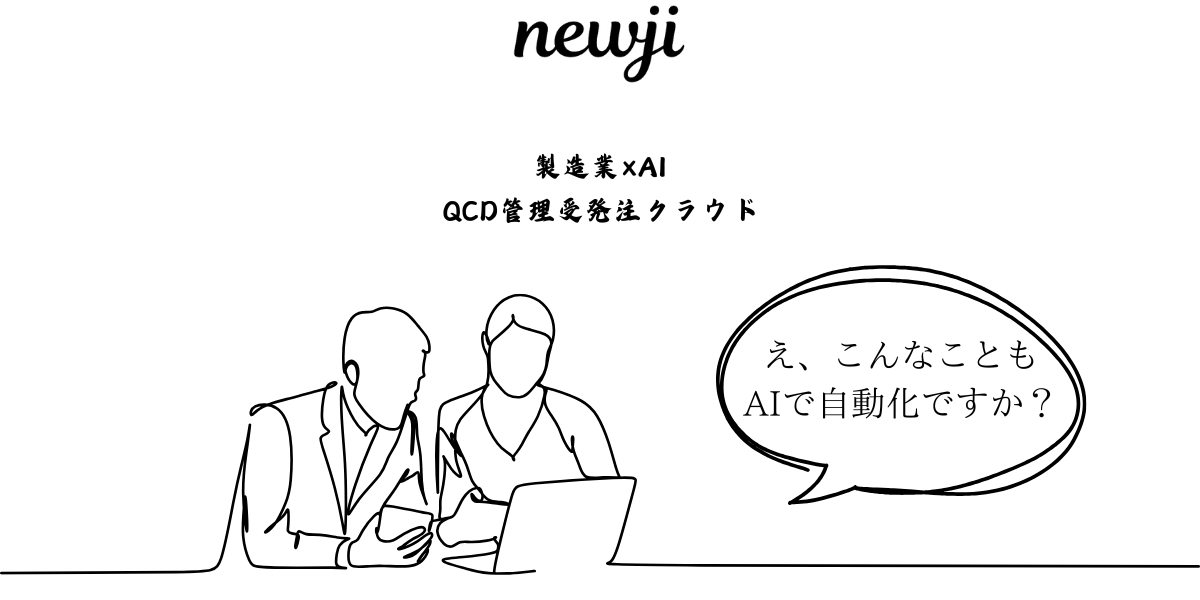
Revolutionizing Industrial Success: The High Precision World of Japanese Steel Component OEM Manufacturing
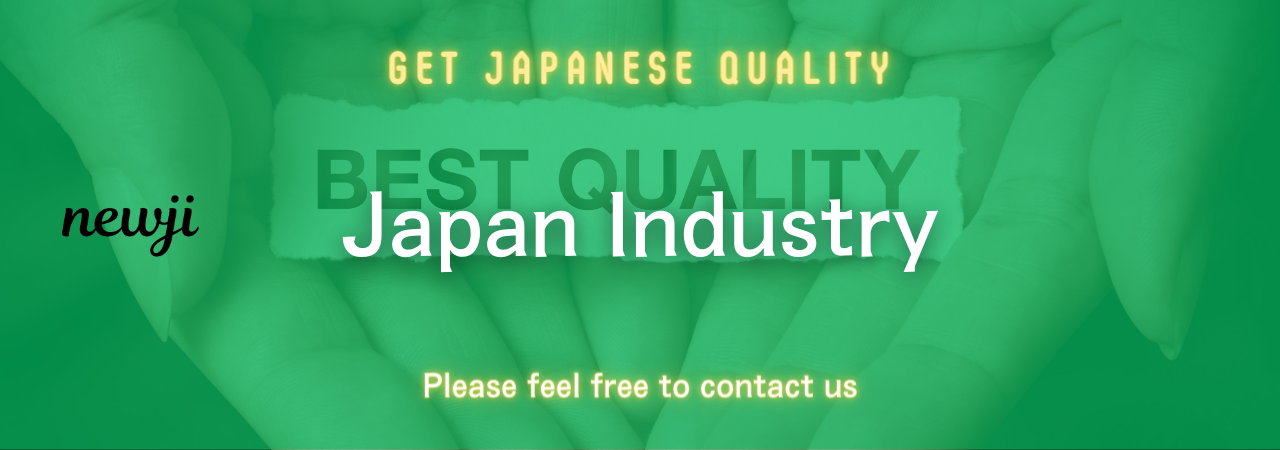
目次
Introduction
In the competitive landscape of global manufacturing, precision and reliability are paramount. Japanese steel component OEM (Original Equipment Manufacturer) manufacturing has emerged as a beacon of excellence, driving industrial success across various sectors. This article delves into the high-precision world of Japanese steel component OEM manufacturing, exploring its advantages, challenges, procurement strategies, supplier negotiation techniques, market conditions, and best practices. Drawing on over two decades of expertise in procurement and purchasing within major manufacturing companies, this piece aims to provide valuable insights for businesses looking to leverage the strengths of Japanese suppliers.
Advantages of Japanese Steel Component OEM Manufacturing
Unmatched Precision and Quality
Japanese manufacturers are renowned for their commitment to precision and quality. Advanced manufacturing technologies and stringent quality control processes ensure that steel components meet the highest standards. This dedication minimizes defects, reduces waste, and ensures consistency across production batches.
Technological Innovation
Japan is at the forefront of technological innovation in manufacturing. Continuous investment in research and development leads to the creation of cutting-edge production techniques and materials. This innovation translates into superior product performance and longevity, providing a competitive edge to businesses that incorporate these components into their products.
Reliability and Consistency
Reliability is a cornerstone of Japanese manufacturing. Suppliers maintain consistent delivery schedules and uphold quality standards, which is crucial for maintaining smooth supply chains. This reliability reduces the risk of production delays and ensures that businesses can meet their own production timelines effectively.
Strong Supplier Relationships
Japanese suppliers often foster long-term relationships with their clients. This collaborative approach facilitates better communication, mutual understanding, and tailored solutions that align with the specific needs of the purchasing company. Such relationships can lead to preferential treatment, such as priority in order fulfillment and access to the latest innovations.
Efficient Production Processes
Japanese manufacturers excel in lean manufacturing and just-in-time (JIT) production methodologies. These approaches enhance efficiency, reduce inventory costs, and minimize lead times. Businesses benefit from streamlined operations and the ability to respond swiftly to market changes.
Disadvantages of Japanese Steel Component OEM Manufacturing
Higher Costs
While Japanese manufacturers offer high quality, this often comes at a higher cost compared to suppliers from other regions. The premium is justified by the superior quality, but it can be a barrier for businesses with tight budgets or those in cost-sensitive markets.
Language and Cultural Barriers
Communication can be challenging due to language differences and cultural nuances. These barriers may lead to misunderstandings, delays in information exchange, and difficulties in negotiating terms. Overcoming these challenges often requires dedicated resources and efforts to bridge the cultural gap.
Longer Lead Times
Depending on the geographic location of the purchasing company, lead times can be longer due to shipping distances and logistical complexities. This can affect inventory management and require businesses to plan their procurement cycles carefully to avoid production interruptions.
Limited Flexibility
Some Japanese manufacturers may have rigid production processes and less flexibility in accommodating customizations or last-minute changes. This can be a drawback for businesses that require quick adjustments or bespoke solutions to meet specific project requirements.
Procurement and Purchasing Strategies
Comprehensive Supplier Evaluation
Effective procurement begins with a thorough evaluation of potential suppliers. This involves assessing their manufacturing capabilities, quality certifications, financial stability, and track record. On-site visits and audits can provide deeper insights into the supplier’s operations and commitment to quality.
Diversifying Supplier Base
Relying on a single supplier can be risky. Diversifying the supplier base by including multiple Japanese manufacturers can mitigate risks related to supply chain disruptions, price fluctuations, and geopolitical factors. It also fosters competitive pricing and innovation.
Strategic Sourcing
Strategic sourcing involves aligning procurement practices with the overall business strategy. This includes identifying key components, understanding market dynamics, and leveraging supplier strengths to enhance product offerings. By strategically sourcing from Japanese suppliers, businesses can capitalize on their technological advancements and quality standards.
Long-term Contracts
Establishing long-term contracts with Japanese suppliers can secure favorable terms, such as better pricing, priority in production schedules, and access to new technologies. These contracts also foster a stable and predictable supply chain, essential for long-term planning and growth.
Supplier Negotiation Techniques
Building Trust and Rapport
Negotiations with Japanese suppliers should focus on building trust and establishing a strong rapport. Demonstrating respect for their culture, understanding their business practices, and showing a genuine interest in a mutually beneficial partnership can significantly impact negotiation outcomes.
Understanding Cultural Nuances
Japanese negotiation styles emphasize harmony, patience, and indirect communication. Being mindful of these cultural nuances, such as avoiding aggressive bargaining and allowing time for deliberation, can lead to more successful negotiations and stronger supplier relationships.
Value-based Negotiation
Rather than focusing solely on price, value-based negotiation considers the overall value offered by the supplier, including quality, reliability, and service. Highlighting the long-term benefits of a partnership can justify higher costs and lead to agreements that are beneficial for both parties.
Leveraging Data and Analytics
Utilizing data and analytics to support negotiation positions can enhance credibility and effectiveness. Detailed information on market prices, quality metrics, and performance indicators can provide a solid foundation for discussions and help in reaching favorable terms.
Flexibility and Compromise
Successful negotiations often require flexibility and a willingness to compromise. Being open to alternative solutions and creative arrangements can facilitate agreements that satisfy both the purchasing company and the Japanese supplier.
Market Conditions
Global Supply Chain Dynamics
The global supply chain landscape is constantly evolving, influenced by factors such as geopolitical tensions, trade policies, and economic shifts. Understanding these dynamics is crucial for effectively navigating procurement from Japanese suppliers and anticipating potential disruptions.
Technological Advancements
Rapid technological advancements in manufacturing processes and materials impact the market conditions for steel component OEM manufacturing. Staying abreast of these developments allows businesses to leverage the latest innovations and maintain a competitive edge.
Economic Factors
Economic indicators, such as exchange rates, inflation rates, and economic growth, can affect the cost and availability of steel components. Monitoring these factors helps in making informed procurement decisions and managing budgetary constraints.
Environmental Regulations
Increasingly stringent environmental regulations influence manufacturing practices and market conditions. Japanese manufacturers are often at the forefront of sustainable practices, which can align with the environmental goals of purchasing companies and open up opportunities for eco-friendly products.
Market Demand and Trends
Understanding market demand and emerging trends is essential for effective procurement. Demand fluctuations, shifts in consumer preferences, and technological trends can influence the types and quantities of steel components required, guiding procurement strategies accordingly.
Best Practices in OEM Manufacturing with Japanese Suppliers
Collaborative Planning
Engaging in collaborative planning with Japanese suppliers enhances alignment on production schedules, quality standards, and delivery expectations. Joint planning sessions can identify potential issues early and facilitate proactive solutions.
Continuous Improvement (Kaizen)
Embracing the Japanese philosophy of continuous improvement, known as Kaizen, fosters a culture of ongoing enhancement in processes and products. Working with suppliers who prioritize Kaizen can lead to incremental improvements that collectively result in significant advancements.
Quality Assurance Programs
Implementing robust quality assurance programs ensures that steel components meet the required specifications and standards. Regular quality audits, performance reviews, and feedback mechanisms are essential for maintaining high-quality outputs.
Effective Communication Channels
Establishing clear and effective communication channels with suppliers is vital for coordinating activities, addressing issues, and sharing information. Utilizing modern communication tools and maintaining regular contact helps in building a transparent and responsive supply chain.
Leveraging Technology
Adopting technologies such as Enterprise Resource Planning (ERP) systems, supply chain management software, and data analytics can streamline procurement processes and enhance visibility into supplier performance. These technologies enable more efficient decision-making and better management of the supplier relationship.
Training and Development
Investing in training and development for procurement teams equips them with the skills and knowledge necessary to manage relationships with Japanese suppliers effectively. Understanding Japanese business practices, cultural norms, and negotiation techniques can improve collaboration and outcomes.
Case Studies and Real-world Examples
Automotive Industry Collaboration
In the automotive sector, partnerships with Japanese steel component manufacturers have led to the development of high-strength, lightweight components that enhance vehicle performance and fuel efficiency. Companies that leveraged Japanese OEM expertise have been able to innovate and meet stringent industry standards.
Electronics Manufacturing Success
Electronics manufacturers have benefited from Japanese steel components’ precision and reliability, critical for miniaturized and high-performance devices. These collaborations have enabled companies to produce cutting-edge electronics with superior durability and functionality.
Aerospace Industry Advances
The aerospace industry relies on the exceptional quality and precision of Japanese steel components for critical applications such as aircraft frames and engine parts. Collaborations with Japanese OEMs have ensured compliance with stringent safety and performance regulations, contributing to advancements in aerospace technology.
Challenges and Solutions
Overcoming Language Barriers
Language differences can hinder effective communication with Japanese suppliers. Solutions include hiring bilingual staff, utilizing professional translation services, and adopting communication platforms designed for multilingual interactions to ensure clarity and understanding.
Managing Lead Times
Long lead times can disrupt production schedules. Mitigating this issue involves strategic inventory management, establishing safety stock levels, and working closely with suppliers to forecast demand accurately and streamline production processes.
Balancing Cost and Quality
Finding the right balance between cost and quality is crucial. Strategies include negotiating value-based pricing, exploring cost-saving opportunities without compromising quality, and leveraging long-term partnerships to secure favorable terms.
Adapting to Regulatory Changes
Navigating changing regulations requires staying informed and agile. Building a compliance-focused procurement strategy, collaborating with suppliers on regulatory adherence, and investing in compliance training can ensure smooth operations despite regulatory shifts.
Future Trends in Japanese Steel Component OEM Manufacturing
Emphasis on Sustainability
Sustainability is becoming increasingly important in manufacturing. Japanese OEMs are adopting eco-friendly practices, such as reducing carbon footprints, recycling materials, and developing sustainable production methods. This trend aligns with global sustainability goals and presents opportunities for businesses to partner with environmentally conscious suppliers.
Integration of Industry 4.0
Industry 4.0 technologies, including the Internet of Things (IoT), artificial intelligence (AI), and automation, are transforming manufacturing processes. Japanese steel component OEMs are integrating these technologies to enhance precision, efficiency, and adaptability, setting new standards for the industry.
Customization and Flexibility
The demand for customized and flexible manufacturing solutions is rising. Japanese suppliers are responding by offering more tailored services, flexible production capabilities, and rapid prototyping, enabling businesses to meet specific market demands and innovate swiftly.
Global Expansion and Localization
Japanese OEMs are expanding their global footprint and establishing localized production facilities. This trend facilitates closer proximity to key markets, reduces lead times, and improves responsiveness to regional demand fluctuations.
Advanced Materials Development
Research into advanced steel materials, such as high-strength alloys and corrosion-resistant composites, is driving innovation in OEM manufacturing. These materials offer enhanced performance characteristics, opening new possibilities for applications across various industries.
Conclusion
Japanese steel component OEM manufacturing stands as a pillar of precision, quality, and reliability in the global manufacturing arena. The advantages of partnering with Japanese suppliers—ranging from unmatched quality and technological innovation to strong supplier relationships and efficient production processes—are significant drivers of industrial success. However, navigating challenges such as higher costs, language and cultural barriers, and longer lead times requires strategic procurement and negotiation approaches.
By adopting best practices, leveraging technological advancements, and fostering collaborative relationships, businesses can harness the full potential of Japanese OEM manufacturing. As market conditions evolve and future trends emerge, staying informed and adaptable will be key to sustaining and enhancing the benefits of partnering with Japanese steel component manufacturers. Embracing these insights and strategies will position businesses to achieve long-term success and maintain a competitive edge in their respective industries.
資料ダウンロード
QCD調達購買管理クラウド「newji」は、調達購買部門で必要なQCD管理全てを備えた、現場特化型兼クラウド型の今世紀最高の購買管理システムとなります。
ユーザー登録
調達購買業務の効率化だけでなく、システムを導入することで、コスト削減や製品・資材のステータス可視化のほか、属人化していた購買情報の共有化による内部不正防止や統制にも役立ちます。
NEWJI DX
製造業に特化したデジタルトランスフォーメーション(DX)の実現を目指す請負開発型のコンサルティングサービスです。AI、iPaaS、および先端の技術を駆使して、製造プロセスの効率化、業務効率化、チームワーク強化、コスト削減、品質向上を実現します。このサービスは、製造業の課題を深く理解し、それに対する最適なデジタルソリューションを提供することで、企業が持続的な成長とイノベーションを達成できるようサポートします。
オンライン講座
製造業、主に購買・調達部門にお勤めの方々に向けた情報を配信しております。
新任の方やベテランの方、管理職を対象とした幅広いコンテンツをご用意しております。
お問い合わせ
コストダウンが利益に直結する術だと理解していても、なかなか前に進めることができない状況。そんな時は、newjiのコストダウン自動化機能で大きく利益貢献しよう!
(Β版非公開)