- お役立ち記事
- Revolutionizing Industry: The Elegance of Simple Mechanical Mechanisms in Japanese Manufacturing
Revolutionizing Industry: The Elegance of Simple Mechanical Mechanisms in Japanese Manufacturing
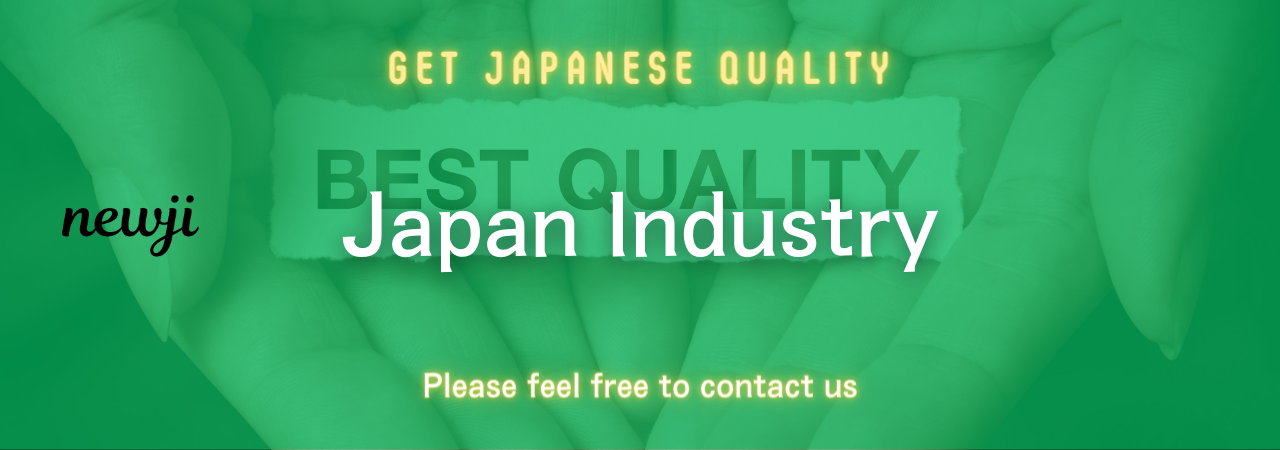
目次
Introduction to Japanese Manufacturing Excellence
Japanese manufacturing has long been synonymous with quality, precision, and innovation. At the heart of this reputation lies the elegance of simple mechanical mechanisms. These mechanisms not only embody the principles of efficiency and reliability but also reflect the deep-rooted culture of continuous improvement known as Kaizen. This article delves into the intricacies of simple mechanical mechanisms in Japanese manufacturing, exploring their impact on procurement and purchasing, supplier negotiations, market conditions, and best practices that have revolutionized industries worldwide.
The Essence of Simple Mechanical Mechanisms
Simple mechanical mechanisms are the backbone of many manufacturing processes. Unlike complex systems that require extensive maintenance and specialized knowledge, simple mechanisms offer ease of use, durability, and cost-effectiveness.
Design Philosophy
Japanese manufacturers prioritize designs that are straightforward yet highly functional. This philosophy ensures that machinery is not only easy to operate but also easy to maintain. By minimizing complexity, manufacturers reduce the likelihood of breakdowns and enhance the overall lifespan of their equipment.
Efficiency and Reliability
Simplicity in design translates to streamlined processes. Simple mechanical systems often have fewer moving parts, which means there are fewer points of failure. This reliability is crucial in maintaining consistent production schedules and meeting the high standards expected in various industries.
Cost-Effectiveness
Manufacturing simple mechanisms typically requires less material and fewer resources. This reduction in complexity leads to lower production costs, making the products more competitive in the global market. Additionally, simpler designs facilitate easier training for workers, further reducing operational expenses.
Procurement and Purchasing in Japanese Manufacturing
Effective procurement and purchasing are vital components of Japanese manufacturing success. The focus is on building strong relationships with suppliers, ensuring quality, and maintaining cost efficiency.
Supplier Selection and Management
Japanese companies meticulously select their suppliers based on stringent quality standards and reliability. Long-term partnerships are cultivated through continuous collaboration and mutual trust. This approach ensures a steady supply of high-quality materials and components essential for maintaining production excellence.
Quality Control
Quality is non-negotiable in Japanese manufacturing. Procurement teams work closely with suppliers to implement rigorous quality control measures. Regular audits, inspections, and feedback loops are established to identify and rectify any deviations from established standards promptly.
Cost Management
Japanese procurement strategies emphasize cost management without compromising quality. Techniques such as bulk purchasing, just-in-time inventory, and strategic sourcing are employed to optimize costs. This balance ensures that companies can offer competitive pricing while maintaining their reputation for excellence.
Advantages of Simple Mechanical Mechanisms
The use of simple mechanical mechanisms offers numerous advantages that contribute to the overall success of Japanese manufacturing.
Enhanced Durability
Simple mechanisms, with their fewer moving parts, are inherently more durable. They withstand wear and tear better, leading to longer-lasting machinery and equipment. This durability minimizes downtime and maintenance costs, ensuring continuous production flow.
Ease of Maintenance
Maintenance of simple systems is straightforward and requires less specialized knowledge. This ease of upkeep reduces the reliance on highly skilled technicians, making it easier to maintain machinery and keep production lines running smoothly.
Flexibility and Adaptability
Simple mechanical systems are often more adaptable to changes in production requirements. They can be easily modified or reconfigured to accommodate different products or processes, providing manufacturers with the flexibility to innovate and respond to market demands swiftly.
Disadvantages and Challenges
While simple mechanical mechanisms offer many benefits, they also present certain challenges that manufacturers must address.
Limited Functionality
The simplicity that characterizes these mechanisms can sometimes limit their functionality. In scenarios where complex operations are required, simple mechanisms may not suffice, necessitating the integration of more advanced systems.
Scalability Issues
Scaling simple mechanical systems to meet increased production demands can be challenging. As production volumes grow, the limitations of simple mechanisms may become apparent, requiring significant modifications or replacements to handle larger scales effectively.
Innovation Constraints
While simplicity fosters reliability, it can also restrict the scope for innovation. Manufacturers aiming to incorporate cutting-edge technologies or advanced features may find simple mechanisms less accommodating, necessitating a balance between simplicity and innovation.
Supplier Negotiation Techniques
Successful supplier negotiations are crucial in securing the best terms and maintaining strong partnerships. Japanese manufacturers employ several effective techniques to negotiate with suppliers.
Building Long-Term Relationships
Rather than focusing solely on immediate gains, Japanese companies prioritize long-term relationships. This approach fosters trust and collaboration, creating a foundation for mutually beneficial agreements and more favorable negotiation terms.
Mutual Gain Philosophy
Negotiations are approached with the mindset of achieving mutual gain. By understanding and addressing the supplier’s needs and constraints, Japanese manufacturers work towards agreements that benefit both parties, leading to sustainable partnerships.
Preparation and Knowledge
Thorough preparation is essential for successful negotiations. Japanese procurement teams conduct detailed research on suppliers, market conditions, and alternative options. This comprehensive knowledge empowers them to negotiate effectively and secure the best possible terms.
Effective Communication
Clear and respectful communication is fundamental in negotiations. Japanese companies emphasize transparency and clarity, ensuring that all parties understand the terms and expectations. This communication fosters trust and minimizes misunderstandings.
Market Conditions and Trends
Understanding market conditions and trends is vital for effective procurement and manufacturing strategies. Japanese manufacturers stay attuned to global market dynamics to remain competitive.
Globalization and Supply Chain Management
Globalization has expanded the reach of Japanese manufacturers, allowing them to source materials and sell products worldwide. Effective supply chain management ensures that they can navigate global challenges such as trade policies, tariffs, and logistical disruptions.
Technological Advancements
Advancements in technology continuously reshape manufacturing processes. Japanese companies leverage cutting-edge technologies to enhance their production capabilities, improve product quality, and streamline procurement operations.
Sustainability and Environmental Concerns
There is a growing emphasis on sustainability and environmental responsibility in the manufacturing sector. Japanese companies are increasingly adopting eco-friendly practices, such as reducing waste, minimizing energy consumption, and sourcing sustainable materials, to meet regulatory requirements and consumer expectations.
Economic Fluctuations
Economic cycles and fluctuations impact procurement and manufacturing strategies. Japanese manufacturers adapt by diversifying their supplier base, optimizing inventory levels, and implementing cost-control measures to mitigate the effects of economic downturns and capitalize on periods of growth.
Best Practices in Japanese Manufacturing
Japanese manufacturing has set benchmarks in various aspects of production and procurement. Adopting these best practices can significantly enhance operational efficiency and product quality.
Lean Manufacturing
Lean manufacturing principles focus on minimizing waste and maximizing value. By streamlining processes, eliminating non-essential activities, and optimizing resource utilization, Japanese manufacturers achieve higher efficiency and cost savings.
Kaizen – Continuous Improvement
Kaizen, the philosophy of continuous improvement, is integral to Japanese manufacturing. Employees at all levels are encouraged to identify areas for enhancement and contribute ideas to improve processes, leading to incremental advancements and sustained excellence.
Just-In-Time (JIT) Inventory
JIT inventory management reduces holding costs and minimizes waste by aligning production schedules with actual demand. This approach ensures that materials and components are available precisely when needed, enhancing responsiveness and flexibility.
Total Quality Management (TQM)
TQM emphasizes holistic quality control across all aspects of production. By integrating quality into every step of the manufacturing process, Japanese companies ensure that their products consistently meet or exceed customer expectations.
Employee Empowerment and Training
Investing in employee training and empowerment is a cornerstone of Japanese manufacturing. Skilled and motivated workers are essential for maintaining high standards of quality and efficiency. Continuous training programs and a culture of respect and collaboration contribute to a highly competent workforce.
Case Studies: Success Stories in Japanese Manufacturing
Examining real-world examples can provide valuable insights into the application of simple mechanical mechanisms and procurement practices in Japanese manufacturing.
Toyota Production System (TPS)
The Toyota Production System is a paradigmatic example of lean manufacturing and Kaizen in action. By focusing on eliminating waste, optimizing processes, and empowering workers, Toyota has become a global leader in the automotive industry. The simplicity and efficiency of their manufacturing mechanisms are central to their success.
Canon’s Quality Control
Canon is renowned for its stringent quality control measures. By integrating simple yet effective mechanical systems with robust quality management practices, Canon consistently produces high-quality imaging and optical products. Their approach ensures reliability and customer satisfaction.
Panasonic’s Supply Chain Collaboration
Panasonic exemplifies effective supplier collaboration. By fostering strong relationships with suppliers and implementing comprehensive supply chain management strategies, Panasonic ensures a steady flow of high-quality materials. This collaboration enhances production efficiency and product quality.
Challenges in Implementing Simple Mechanical Mechanisms
Despite their advantages, implementing simple mechanical mechanisms comes with its set of challenges that manufacturers must navigate.
Balancing Simplicity and Innovation
Striking the right balance between simplicity and the need for innovation is crucial. While simplicity offers reliability, manufacturers must ensure that their products remain competitive by integrating necessary advancements without overcomplicating the design.
Managing Supply Chain Complexity
Global supply chains can be inherently complex. Ensuring that all suppliers adhere to the high standards required for simple mechanical mechanisms demands rigorous oversight and effective communication. Managing this complexity is essential for maintaining production quality and timelines.
Adapting to Changing Market Demands
Market demands are constantly evolving, and manufacturers must be agile in their responses. Simple mechanical systems must be adaptable enough to accommodate changes without significant overhauls, requiring careful planning and flexible design strategies.
Maintaining Quality Standards
Consistently maintaining high quality across all production stages is a persistent challenge. Implementing standardized processes, continuous training, and effective quality control measures are necessary to uphold the standards that Japanese manufacturing is known for.
Future Outlook: The Evolution of Simple Mechanisms
The future of Japanese manufacturing is poised to integrate simple mechanical mechanisms with advanced technologies, creating a harmonious blend of tradition and innovation.
Integration with Automation and Robotics
Automation and robotics are increasingly becoming integral to manufacturing processes. By integrating these technologies with simple mechanical mechanisms, Japanese manufacturers can enhance production efficiency, precision, and scalability while retaining the reliability of simple systems.
Smart Manufacturing and IoT
The advent of the Internet of Things (IoT) allows for smarter manufacturing processes. Simple mechanical mechanisms can be equipped with sensors and connected to networks, enabling real-time monitoring, predictive maintenance, and data-driven decision-making, further enhancing their efficiency and reliability.
Sustainable Manufacturing Practices
Sustainability will continue to be a significant focus in the future of manufacturing. Developing simple mechanisms that are energy-efficient and environmentally friendly will align with global sustainability goals and meet consumer demand for responsible manufacturing.
Customized and Flexible Manufacturing
The trend towards customization requires manufacturing systems to be more flexible. Simple mechanical mechanisms, with their inherent adaptability, are well-suited to accommodate personalized production without extensive reengineering, allowing manufacturers to meet diverse customer needs efficiently.
Implementing Japanese Best Practices in Global Manufacturing
Adopting Japanese manufacturing principles can yield substantial benefits for global manufacturers seeking to enhance their operations.
Emphasizing Quality and Continuous Improvement
Global manufacturers can adopt the Japanese emphasis on quality and continuous improvement by implementing rigorous quality control systems and fostering a culture of Kaizen. This approach leads to higher product standards and operational efficiencies.
Building Strategic Supplier Relationships
Establishing long-term, strategic relationships with suppliers can enhance supply chain reliability and quality. By investing in supplier partnerships and collaborative practices, manufacturers can secure better terms and ensure consistent quality.
Adopting Lean and Just-In-Time Principles
Implementing lean manufacturing and JIT inventory systems can help reduce waste, lower costs, and improve responsiveness to market demands. These principles streamline operations and enhance overall efficiency.
Investing in Employee Training and Empowerment
A skilled and motivated workforce is essential for maintaining high standards. Investing in comprehensive training programs and fostering an empowering work environment can lead to increased productivity and job satisfaction.
Conclusion
The elegance of simple mechanical mechanisms is a testament to the ingenuity and disciplined approach of Japanese manufacturing. By prioritizing simplicity, quality, and continuous improvement, Japanese manufacturers have set a global standard in various industries. Effective procurement and purchasing strategies, coupled with robust supplier relationships and best manufacturing practices, have enabled them to revolutionize industry practices worldwide. As technology continues to evolve, the integration of simple mechanisms with advanced innovations will likely drive the next wave of manufacturing excellence, ensuring that the legacy of Japanese manufacturing remains influential and revered.
資料ダウンロード
QCD調達購買管理クラウド「newji」は、調達購買部門で必要なQCD管理全てを備えた、現場特化型兼クラウド型の今世紀最高の購買管理システムとなります。
ユーザー登録
調達購買業務の効率化だけでなく、システムを導入することで、コスト削減や製品・資材のステータス可視化のほか、属人化していた購買情報の共有化による内部不正防止や統制にも役立ちます。
NEWJI DX
製造業に特化したデジタルトランスフォーメーション(DX)の実現を目指す請負開発型のコンサルティングサービスです。AI、iPaaS、および先端の技術を駆使して、製造プロセスの効率化、業務効率化、チームワーク強化、コスト削減、品質向上を実現します。このサービスは、製造業の課題を深く理解し、それに対する最適なデジタルソリューションを提供することで、企業が持続的な成長とイノベーションを達成できるようサポートします。
オンライン講座
製造業、主に購買・調達部門にお勤めの方々に向けた情報を配信しております。
新任の方やベテランの方、管理職を対象とした幅広いコンテンツをご用意しております。
お問い合わせ
コストダウンが利益に直結する術だと理解していても、なかなか前に進めることができない状況。そんな時は、newjiのコストダウン自動化機能で大きく利益貢献しよう!
(Β版非公開)