- お役立ち記事
- Revolutionizing Japanese Manufacturing: A Deep Dive into Electroactive Biomaterials
月間76,176名の
製造業ご担当者様が閲覧しています*
*2025年3月31日現在のGoogle Analyticsのデータより
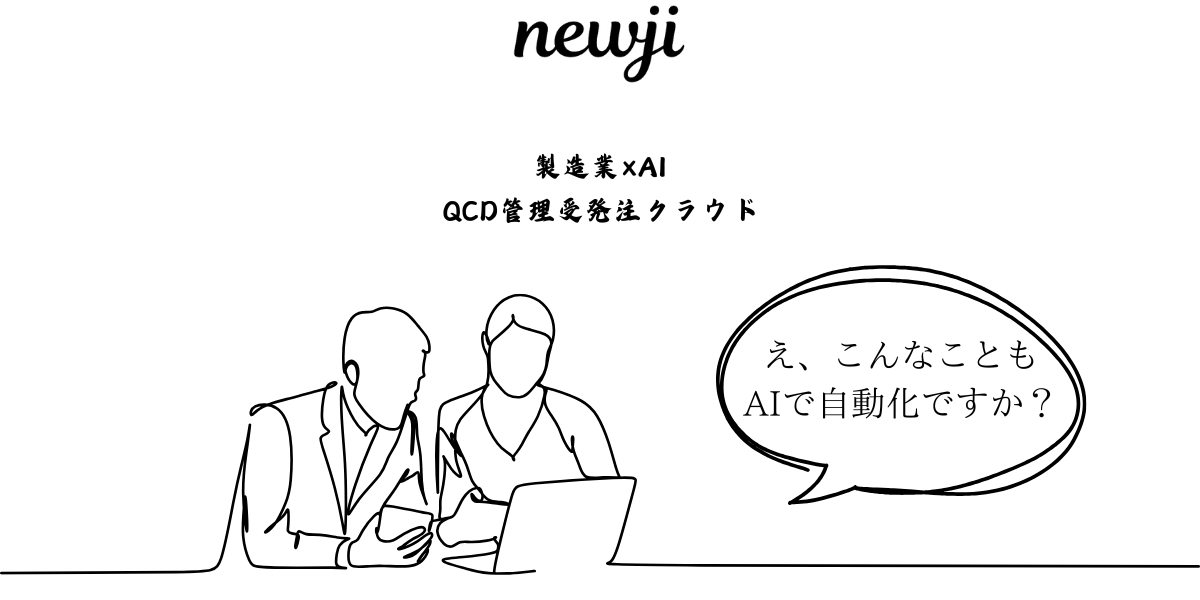
Revolutionizing Japanese Manufacturing: A Deep Dive into Electroactive Biomaterials
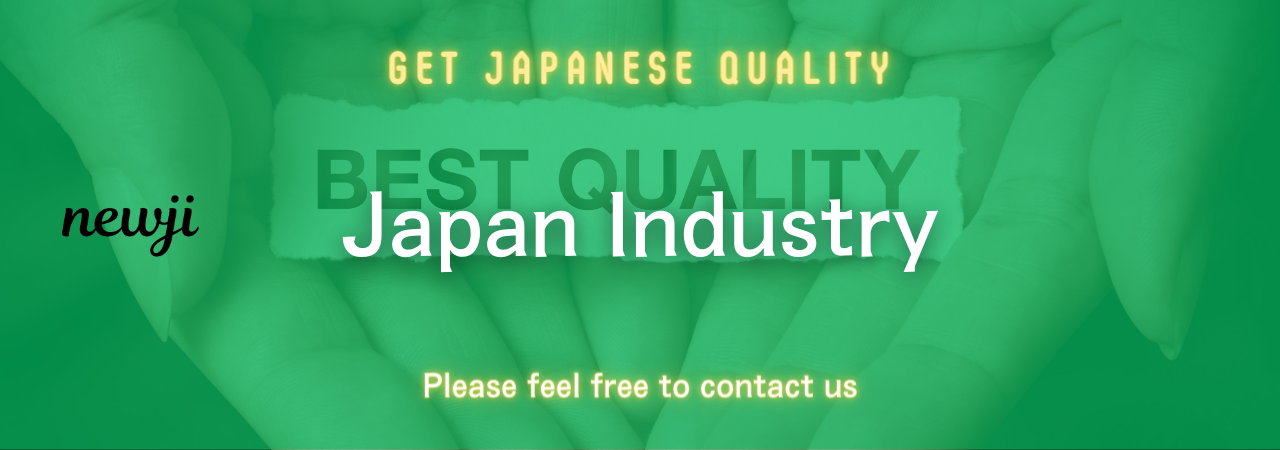
目次
Introduction
In the rapidly evolving landscape of manufacturing, innovation remains the cornerstone of competitiveness and sustainability. One such groundbreaking advancement is the integration of electroactive biomaterials into manufacturing processes. This technology is particularly revolutionizing Japanese manufacturing, a sector renowned for its precision, quality, and efficiency. Electroactive biomaterials, which respond to electrical stimuli with changes in their properties, offer unprecedented opportunities for enhancing product functionality, optimizing production processes, and fostering sustainable practices. This article delves deep into the role of electroactive biomaterials in Japanese manufacturing, exploring their advantages, challenges, procurement strategies, market conditions, and best practices for successful integration.
The Role of Electroactive Biomaterials in Modern Manufacturing
Understanding Electroactive Biomaterials
Electroactive biomaterials are a class of materials that exhibit significant changes in their physical or chemical properties in response to electrical stimuli. These materials can convert electrical energy into mechanical movement or vice versa, making them highly versatile for various applications. Common types include piezoelectric materials, which generate electricity when mechanically stressed, and shape-memory alloys, which return to a predefined shape when heated by an electrical current. In manufacturing, these materials enable the creation of smart components that can adapt to changing conditions, enhance performance, and extend the lifespan of products.
Applications in Industrial Manufacturing
The application of electroactive biomaterials spans multiple facets of manufacturing. In automotive manufacturing, for instance, these materials are used in sensors and actuators that improve vehicle safety and performance. In electronics, they facilitate the development of flexible devices and advanced circuitry. Additionally, electroactive biomaterials play a critical role in robotics and automation, enabling more precise and responsive movements. In the aerospace sector, they contribute to the development of lightweight and durable components, enhancing fuel efficiency and reliability. These applications demonstrate the transformative potential of electroactive biomaterials across diverse manufacturing industries.
Advantages of Adopting Electroactive Biomaterials
Enhanced Product Performance
One of the most significant advantages of electroactive biomaterials is their ability to enhance product performance. These materials can dynamically respond to environmental changes, allowing for the creation of adaptive and responsive products. For example, in electronics, electroactive biomaterials enable the development of touch-sensitive and flexible devices, improving user interaction and device versatility. In automotive applications, sensors made from these materials can provide real-time feedback, enhancing vehicle safety and performance.
Cost Efficiency
While the initial investment in electroactive biomaterials may be high, the long-term cost efficiencies are substantial. These materials often require less maintenance and have longer lifespans compared to traditional materials. Their ability to self-regulate and adapt reduces the need for frequent replacements and repairs, leading to lower operational costs. Furthermore, the integration of electroactive biomaterials can streamline manufacturing processes, minimizing waste and enhancing overall productivity.
Sustainability and Environmental Impact
Sustainability is a critical consideration in modern manufacturing, and electroactive biomaterials contribute positively to environmental goals. Many of these materials are designed to be energy-efficient, reducing the overall energy consumption of manufacturing processes. Additionally, their durability and longevity mean fewer resources are needed for replacements, decreasing the environmental footprint. Some electroactive materials are also biodegradable or recyclable, aligning with circular economy principles and promoting sustainable manufacturing practices.
Challenges and Disadvantages
High Initial Investment
Despite their numerous benefits, electroactive biomaterials come with significant upfront costs. Research and development, material acquisition, and the integration of new technologies into existing manufacturing systems require substantial financial investment. For smaller manufacturers or those with limited budgets, these costs can be prohibitive, potentially limiting widespread adoption.
Technical Complexity
The integration of electroactive biomaterials introduces a level of technical complexity that can be challenging for manufacturing operations. These materials often require specialized knowledge for handling, processing, and incorporating into products. Additionally, ensuring compatibility with existing manufacturing systems and processes necessitates careful planning and expertise, which may require additional training and resources.
Supply Chain Considerations
Securing a reliable supply of high-quality electroactive biomaterials can be challenging. The specialized nature of these materials means that suppliers are often limited, and disruptions in the supply chain can have significant impacts on manufacturing operations. Ensuring consistent quality and availability requires robust supplier relationships and strategic procurement practices, which can be resource-intensive.
Procurement and Purchasing Strategies for Electroactive Biomaterials
Identifying Reliable Suppliers
Finding reliable suppliers is paramount when procuring electroactive biomaterials. Manufacturers should conduct thorough market research to identify suppliers with a proven track record of quality and reliability. Evaluating potential suppliers based on their production capabilities, quality control measures, and compliance with industry standards ensures that the materials meet the required specifications and performance criteria.
Supplier Negotiation Techniques
Effective negotiation with suppliers is essential to secure favorable terms and pricing for electroactive biomaterials. Key strategies include:
– **Volume Discounts:** Negotiating bulk purchase discounts can reduce costs, especially for large-scale production needs.
– **Long-Term Contracts:** Establishing long-term agreements can guarantee material availability and price stability, mitigating risks associated with supply chain fluctuations.
– **Quality Assurance:** Negotiating terms that include strict quality control measures and warranties ensures that the materials meet the necessary standards and performance requirements.
– **Flexible Payment Terms:** Securing favorable payment terms, such as deferred payments or installment options, can improve cash flow management.
Managing Supplier Relationships
Building and maintaining strong relationships with suppliers is crucial for ensuring a steady supply of high-quality electroactive biomaterials. Regular communication, mutual trust, and collaboration can lead to improved reliability and responsiveness. Implementing supplier performance metrics and conducting periodic reviews helps in assessing and enhancing supplier performance, ensuring that they continue to meet the evolving needs of the manufacturing operation.
Market Conditions and Trends
Current Market Landscape
The market for electroactive biomaterials is experiencing robust growth, driven by advancements in technology and increasing demand across various industries. Japanese manufacturing, in particular, is at the forefront of adopting these materials, leveraging their unique properties to enhance product innovation and manufacturing efficiency. The demand is fueled by sectors such as automotive, electronics, aerospace, and healthcare, all of which seek to integrate smart and adaptive materials into their products and processes.
Future Predictions
Looking ahead, the market for electroactive biomaterials is expected to continue its upward trajectory. Innovations in material science are likely to lead to the development of more efficient, cost-effective, and sustainable electroactive biomaterials. Additionally, as manufacturing processes become more automated and integrated with digital technologies, the demand for smart materials that can interact seamlessly with these systems will rise. Collaborations between manufacturers, material scientists, and suppliers will play a critical role in advancing the capabilities and applications of electroactive biomaterials.
Best Practices in Integrating Electroactive Biomaterials
Risk Management
Effective risk management is essential when integrating electroactive biomaterials into manufacturing processes. Identifying potential risks, such as supply chain disruptions, technological failures, and quality control issues, enables manufacturers to develop mitigation strategies. Implementing contingency plans, diversifying supplier bases, and investing in research and development can help in addressing and minimizing these risks.
Quality Control Measures
Maintaining high-quality standards is critical for the successful integration of electroactive biomaterials. Implementing rigorous quality control measures, such as regular inspections, testing protocols, and adherence to industry standards, ensures that the materials perform as expected. Investing in advanced quality assurance technologies and training personnel in quality management practices enhances the reliability and consistency of the materials used in manufacturing processes.
Collaboration with R&D
Collaborating with research and development teams is vital for maximizing the benefits of electroactive biomaterials. Joint efforts between procurement, engineering, and R&D departments foster innovation and facilitate the development of optimized materials and processes. Engaging in collaborative projects with material scientists and academic institutions can also accelerate the advancement of electroactive biomaterials and their applications in manufacturing.
Case Studies: Success Stories in Japanese Manufacturing
Toyota Motor Corporation
Toyota has successfully integrated electroactive biomaterials into its vehicle manufacturing processes. By utilizing piezoelectric materials in sensors and actuators, Toyota has enhanced vehicle safety features and improved the responsiveness of automotive systems. The adoption of these materials has also contributed to the development of more efficient and reliable hybrid engines, aligning with Toyota’s commitment to sustainability and innovation.
Panasonic Corporation
Panasonic has leveraged electroactive biomaterials in the development of advanced electronic devices and robotics. By incorporating shape-memory alloys and other electroactive materials, Panasonic has created flexible and adaptive components that enhance the functionality and performance of its products. This integration has enabled the company to stay ahead in the competitive electronics market, offering cutting-edge solutions that meet evolving consumer demands.
Honda Motor Co., Ltd.
Honda has applied electroactive biomaterials in its robotics and automation initiatives. The use of these materials in robotic actuators has increased the precision and efficiency of manufacturing operations. Additionally, Honda’s exploration of electroactive biomaterials in energy storage systems has led to the development of more efficient and compact batteries, supporting the company’s advancements in electric vehicle technology.
Conclusion
The integration of electroactive biomaterials is revolutionizing Japanese manufacturing, driving significant advancements in product performance, cost efficiency, and sustainability. While the adoption of these materials presents challenges such as high initial investments and technical complexities, the long-term benefits far outweigh the drawbacks. Effective procurement and purchasing strategies, coupled with strong supplier relationships and best practices in risk management and quality control, are essential for successful integration. As the market for electroactive biomaterials continues to grow, Japanese manufacturers are well-positioned to lead the charge in innovation and excellence. Embracing these advanced materials not only enhances competitiveness but also paves the way for a more sustainable and technologically advanced manufacturing future.
資料ダウンロード
QCD管理受発注クラウド「newji」は、受発注部門で必要なQCD管理全てを備えた、現場特化型兼クラウド型の今世紀最高の受発注管理システムとなります。
ユーザー登録
受発注業務の効率化だけでなく、システムを導入することで、コスト削減や製品・資材のステータス可視化のほか、属人化していた受発注情報の共有化による内部不正防止や統制にも役立ちます。
NEWJI DX
製造業に特化したデジタルトランスフォーメーション(DX)の実現を目指す請負開発型のコンサルティングサービスです。AI、iPaaS、および先端の技術を駆使して、製造プロセスの効率化、業務効率化、チームワーク強化、コスト削減、品質向上を実現します。このサービスは、製造業の課題を深く理解し、それに対する最適なデジタルソリューションを提供することで、企業が持続的な成長とイノベーションを達成できるようサポートします。
製造業ニュース解説
製造業、主に購買・調達部門にお勤めの方々に向けた情報を配信しております。
新任の方やベテランの方、管理職を対象とした幅広いコンテンツをご用意しております。
お問い合わせ
コストダウンが利益に直結する術だと理解していても、なかなか前に進めることができない状況。そんな時は、newjiのコストダウン自動化機能で大きく利益貢献しよう!
(β版非公開)