- お役立ち記事
- Revolutionizing Japanese Manufacturing: Automating the Checklist for CAD Feature Inspection
月間76,176名の
製造業ご担当者様が閲覧しています*
*2025年3月31日現在のGoogle Analyticsのデータより
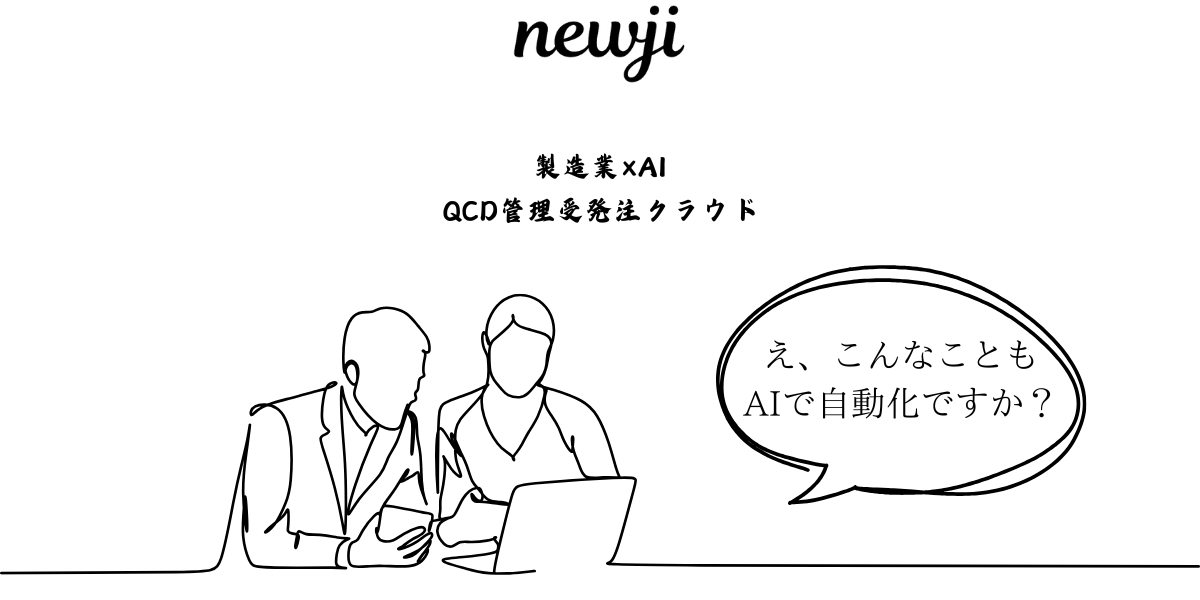
Revolutionizing Japanese Manufacturing: Automating the Checklist for CAD Feature Inspection
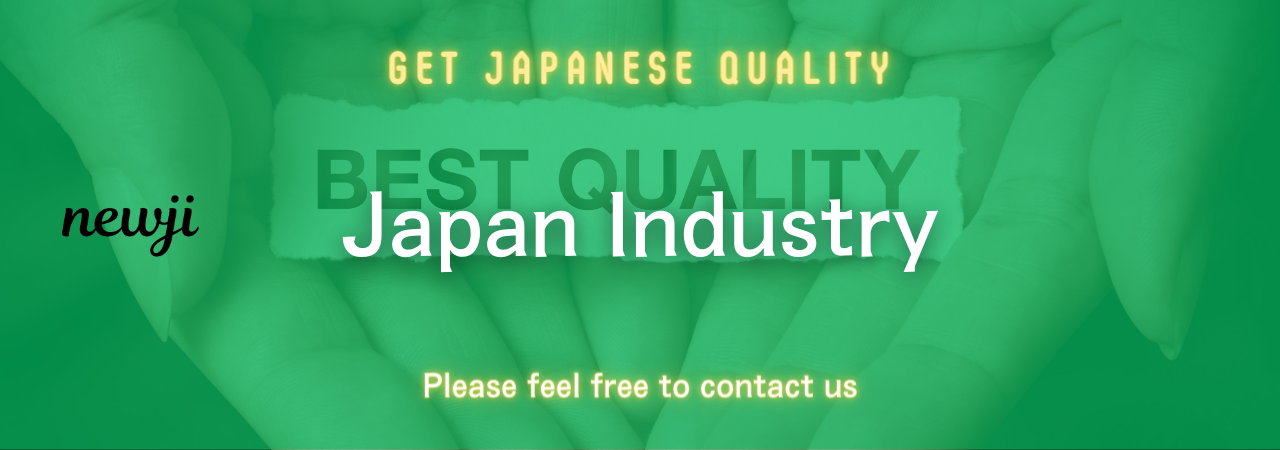
目次
Introduction
The landscape of Japanese manufacturing is undergoing a significant transformation as companies integrate automation into their quality inspection processes.
In particular, the automation of checklists for CAD feature inspection is revolutionizing the way manufacturers ensure product quality and efficiency.
This advancement not only enhances the precision of inspections but also streamlines procurement and purchasing operations.
By leveraging automated systems, manufacturers can achieve greater consistency, reduce human error, and optimize their supply chain management.
This article delves into the practical aspects of implementing automated checklists for CAD feature inspections in Japanese manufacturing.
We will explore the advantages and disadvantages of this approach, discuss supplier negotiation techniques, analyze current market conditions, and outline best practices for successful adoption.
Advantages of Automation in CAD Feature Inspection
Automation in CAD feature inspection offers numerous benefits that can significantly improve manufacturing processes.
Enhanced Accuracy and Consistency
Automated checklists eliminate the variability associated with manual inspections.
They ensure that every feature is evaluated against standardized criteria, resulting in higher accuracy and consistency in quality assessments.
This precision is crucial in maintaining the high standards synonymous with Japanese manufacturing.
Increased Efficiency
Automation accelerates the inspection process by systematically evaluating CAD features without the need for manual intervention.
This increase in speed allows manufacturers to meet tight production schedules and reduces the time-to-market for products.
Cost Reduction
By minimizing the reliance on manual labor for inspections, companies can reduce labor costs and reallocate resources to more strategic areas of the business.
Additionally, the reduction in errors leads to fewer defects and less waste, further cutting costs.
Integration with Procurement and Purchasing
Automated inspection systems can be seamlessly integrated with procurement and purchasing departments.
This integration facilitates better communication between suppliers and manufacturers, ensuring that any issues with CAD features are promptly addressed and resolved.
Disadvantages of Automation in CAD Feature Inspection
While automation offers numerous benefits, it also presents certain challenges that manufacturers must address.
High Initial Investment
Implementing automated inspection systems requires significant upfront investment in technology and infrastructure.
This cost can be a barrier for smaller manufacturers or those with limited budgets.
Technical Complexity
The integration of automated systems into existing manufacturing processes can be complex.
It requires specialized knowledge and expertise to ensure that the systems operate seamlessly and effectively.
Dependence on Technology
Reliance on automated systems necessitates robust technical support and maintenance.
Any system failures or technical issues can disrupt the production process and impact overall efficiency.
Resistance to Change
Adopting new technologies often encounters resistance from employees accustomed to traditional methods.
Effective change management strategies are essential to address this resistance and ensure successful implementation.
Supplier Negotiation Techniques in Automated CAD Inspection
Effective negotiation with suppliers is critical to the successful adoption of automated CAD inspection systems.
Here are some key techniques:
Establish Clear Objectives
Before entering negotiations, clearly define your objectives and what you aim to achieve through the implementation of automated inspection systems.
This clarity helps in articulating your requirements and expectations to suppliers.
Conduct Thorough Market Research
Understand the market landscape and evaluate different suppliers based on their offerings, reputation, and ability to meet your specific needs.
This research enables you to make informed decisions and negotiate from a position of strength.
Leverage Long-Term Relationships
Building and maintaining strong relationships with suppliers can lead to more favorable terms and collaborative problem-solving.
Long-term partnerships often result in better support and service quality.
Focus on Total Cost of Ownership
Consider not only the initial cost but also the long-term expenses associated with the automated inspection system, including maintenance, upgrades, and training.
Negotiating based on the total cost of ownership ensures that you account for all financial aspects.
Emphasize Quality and Reliability
Prioritize suppliers that offer high-quality and reliable systems.
Emphasize the importance of system performance and reliability in your negotiations to ensure you receive products that meet your standards.
Market Conditions for Automated CAD Inspection Systems
The market for automated CAD inspection systems is influenced by various factors that affect both supply and demand.
Growing Demand for Precision
As manufacturing industries strive for higher precision and quality, the demand for advanced CAD inspection systems continues to rise.
This trend is particularly strong in sectors where product quality is critical, such as automotive and aerospace.
Technological Advancements
Ongoing advancements in automation, artificial intelligence, and machine learning are driving the development of more sophisticated CAD inspection systems.
These technologies enhance the capabilities and effectiveness of automated inspections.
Competitive Landscape
The market is becoming increasingly competitive, with numerous suppliers offering a wide range of solutions.
Manufacturers have access to diverse options, which can drive innovation and lower costs but also require careful supplier evaluation.
Economic Factors
Economic conditions, including manufacturing sector growth and investment trends, influence the adoption of automated systems.
In times of economic growth, companies are more likely to invest in new technologies to improve efficiency and maintain competitive advantages.
Regulatory Standards
Compliance with industry standards and regulations is a significant factor driving the adoption of automated inspection systems.
Manufacturers need to ensure that their processes meet regulatory requirements, which often necessitates precise and reliable quality inspections.
Best Practices for Implementing Automated CAD Feature Inspection
Successful implementation of automated CAD feature inspection requires careful planning and execution.
Here are some best practices to ensure a smooth transition and maximize the benefits:
Assess Organizational Readiness
Evaluate your organization’s readiness for automation by assessing your current processes, technology infrastructure, and workforce capabilities.
Identify any gaps and address them before implementing new systems.
Engage Stakeholders Early
Involve key stakeholders from different departments, including procurement, engineering, and quality control, early in the planning process.
This collaboration ensures that all perspectives are considered and that the implementation meets the organization’s needs.
Choose the Right Technology
Select automated CAD inspection systems that align with your specific requirements and integrate seamlessly with your existing software and hardware.
Consider factors such as scalability, ease of use, and compatibility with other systems.
Provide Comprehensive Training
Ensure that your workforce is adequately trained to use the new automated inspection systems.
Comprehensive training programs help employees adapt to new technologies and maximize their effectiveness.
Implement Robust Data Management
Automated inspection systems generate vast amounts of data.
Implementing robust data management practices ensures that this data is stored securely, analyzed effectively, and utilized to drive continuous improvement.
Monitor and Evaluate Performance
Regularly monitor the performance of your automated inspection systems to identify any issues and ensure they are functioning as intended.
Continuous evaluation allows for timely adjustments and improvements to maintain optimal performance.
Foster a Culture of Continuous Improvement
Encourage a culture that embraces continuous improvement and innovation.
This mindset supports the ongoing optimization of your inspection processes and the adoption of new technologies as they become available.
The Role of Procurement and Purchasing in Automated CAD Inspection
Procurement and purchasing departments play a pivotal role in the successful adoption of automated CAD inspection systems.
They are responsible for sourcing the right technology, negotiating with suppliers, and ensuring that the procurement process aligns with the organization’s strategic goals.
Strategic Sourcing
Adopt a strategic sourcing approach that considers not only the cost but also the quality, reliability, and long-term benefits of the automated inspection systems.
This comprehensive evaluation helps in selecting suppliers that can provide value beyond the initial purchase.
Supplier Relationship Management
Develop strong relationships with key suppliers to facilitate better communication, collaboration, and problem-solving.
Effective supplier relationship management can lead to improved support and service, enhancing the overall performance of the automated systems.
Risk Management
Identify and mitigate risks associated with the procurement of automated inspection systems, such as supplier reliability, technology obsolescence, and integration challenges.
Implementing robust risk management strategies ensures that potential issues are addressed proactively.
Cost Optimization
Work closely with suppliers to negotiate favorable terms that optimize costs while maintaining quality and reliability.
Consider factors such as bulk purchasing discounts, long-term agreements, and value-added services in your negotiations.
Compliance and Standards
Ensure that the automated inspection systems comply with industry standards and regulatory requirements.
Collaborate with suppliers to verify that their products meet the necessary specifications and certifications.
Conclusion
Automating the checklist for CAD feature inspection is a transformative step for Japanese manufacturing, offering enhanced accuracy, efficiency, and integration with procurement and purchasing operations.
While the initial investment and technical complexities pose challenges, the long-term benefits outweigh the disadvantages by fostering higher quality standards, reducing costs, and enabling better supply chain management.
By employing effective supplier negotiation techniques and adhering to market best practices, manufacturers can successfully implement automated inspection systems and maintain their competitive edge in the global market.
Embracing this technological advancement not only aligns with the renowned precision of Japanese manufacturing but also paves the way for sustained innovation and excellence in the industry.
資料ダウンロード
QCD管理受発注クラウド「newji」は、受発注部門で必要なQCD管理全てを備えた、現場特化型兼クラウド型の今世紀最高の受発注管理システムとなります。
ユーザー登録
受発注業務の効率化だけでなく、システムを導入することで、コスト削減や製品・資材のステータス可視化のほか、属人化していた受発注情報の共有化による内部不正防止や統制にも役立ちます。
NEWJI DX
製造業に特化したデジタルトランスフォーメーション(DX)の実現を目指す請負開発型のコンサルティングサービスです。AI、iPaaS、および先端の技術を駆使して、製造プロセスの効率化、業務効率化、チームワーク強化、コスト削減、品質向上を実現します。このサービスは、製造業の課題を深く理解し、それに対する最適なデジタルソリューションを提供することで、企業が持続的な成長とイノベーションを達成できるようサポートします。
製造業ニュース解説
製造業、主に購買・調達部門にお勤めの方々に向けた情報を配信しております。
新任の方やベテランの方、管理職を対象とした幅広いコンテンツをご用意しております。
お問い合わせ
コストダウンが利益に直結する術だと理解していても、なかなか前に進めることができない状況。そんな時は、newjiのコストダウン自動化機能で大きく利益貢献しよう!
(β版非公開)