- お役立ち記事
- Revolutionizing Japanese Manufacturing: Exploring the Power of Single-Axis Robots
月間76,176名の
製造業ご担当者様が閲覧しています*
*2025年3月31日現在のGoogle Analyticsのデータより
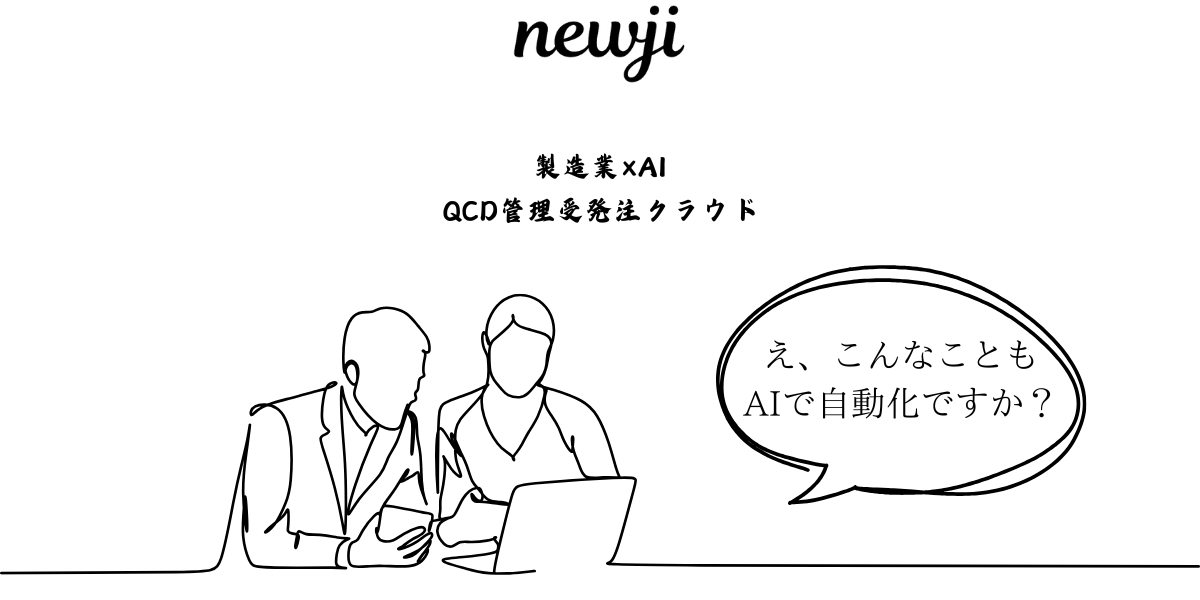
Revolutionizing Japanese Manufacturing: Exploring the Power of Single-Axis Robots
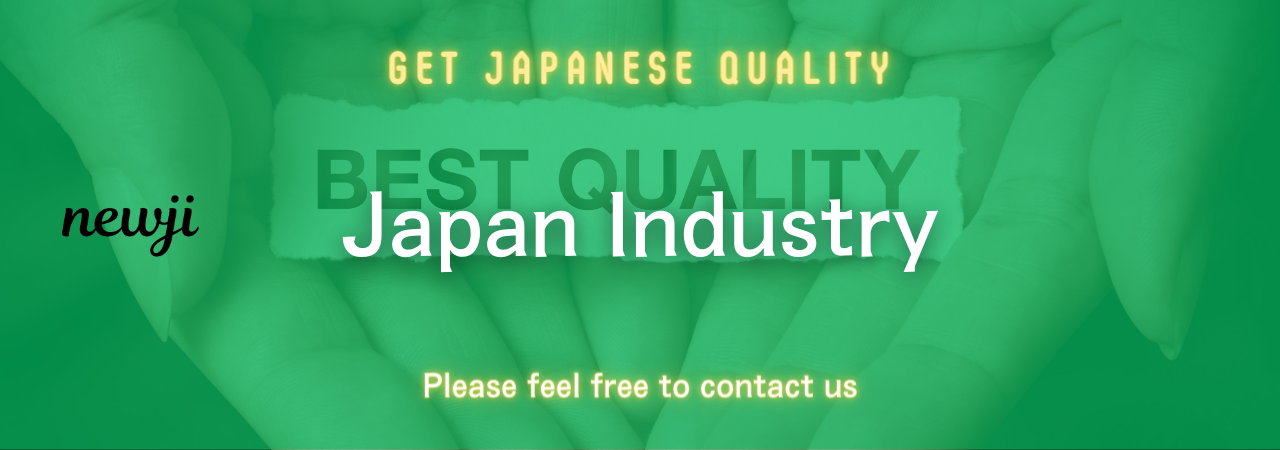
目次
Introduction: The Evolution of Single-Axis Robots in Japanese Manufacturing
In the landscape of modern manufacturing, Japan has long stood as a paragon of efficiency, precision, and innovation.
Among the myriad advancements contributing to this reputation are single-axis robots.
These robotic systems, while perhaps less heralded than their multi-axis counterparts, provide a specialized approach to automation that is transforming assembly lines, production processes, and procurement departments across the nation.
Deploying single-axis robots effectively can lead not only to enhanced productivity but also to substantial cost savings, improved quality control, and greater operational flexibility.
In this article, we will delve into the various dimensions of single-axis robots in Japanese manufacturing, covering their advantages and disadvantages, supplier negotiation techniques, current market conditions, and best practices for leveraging their potential.
Understanding Single-Axis Robots: A Primer
Single-axis robots, also known as linear actuators, are mechanical devices designed to move in a specific, linear path.
Unlike multi-axis robots, which operate on multiple planes and are capable of executing complex, multi-dimensional tasks, single-axis robots excel at repetitive, linear movements.
They are ideal for applications where precision, speed, and reliability are paramount, such as material handling, assembly, and processing.
Currently, the market for single-axis robots is witnessing rapid growth, driven by the increasing demands for automation and the push towards Industry 4.0.
These robots are also becoming more accessible due to advancements in technology and cost reductions resulting from economies of scale.
Advantages of Single-Axis Robots in Manufacturing
1. Cost-Efficiency
One of the key advantages of single-axis robots is their cost-efficiency.
Compared to multi-axis robots, single-axis models are generally less expensive to purchase, maintain, and operate.
Their simpler design results in fewer components that could malfunction, reducing maintenance costs and downtime.
2. Precision and Reliability
Single-axis robots offer exceptional precision and repeatability.
This makes them ideally suited for tasks requiring exact positioning, such as CNC machining, dispensing, or part placement.
High precision reduces errors, thereby enhancing product quality and consistency.
3. Flexibility and Scalability
Despite their seemingly limited range of motion, single-axis robots can be remarkably flexible.
They can be easily integrated into complex automation systems and are compatible with various peripheral devices and technologies.
Moreover, because they are modular by nature, it’s straightforward to scale operations by adding more units as needed.
4. Ease of Integration
Integrating single-axis robots into existing manufacturing processes is relatively straightforward.
They can be programmed using various control systems and are often compatible with industry-standard software and hardware.
This reduces the learning curve for operators and minimizes disruption during implementation.
Challenges and Disadvantages
1. Limited Range of Motion
The most obvious drawback is the limited range of motion.
Single-axis robots are designed for linear movement and thus cannot perform complex, multi-dimensional tasks.
This limits their utility in certain applications, necessitating the use of additional types of robots or equipment for more intricate tasks.
2. Initial Setup Costs
While single-axis robots are generally cost-effective in the long run, the initial setup can be expensive, particularly if specialized equipment or modifications to the existing system are required.
This is often a hurdle for smaller manufacturers or those with tight capital budgets.
3. Learning Curve for Operators
Despite being easier to integrate than some other robotic systems, there is still a learning curve involved.
Operators may require training to effectively program and manage single-axis robots, which can temporarily reduce productivity.
Supplier Negotiation Techniques
1. Understanding Market Dynamics
When negotiating with suppliers of single-axis robots, it is crucial to be well-informed about current market conditions.
Understanding factors like supply chain constraints, technological advancements, and the competitive landscape can provide a solid basis for negotiations.
2. Bulk Purchasing and Long-term Agreements
Leverage economies of scale by negotiating for bulk purchases or long-term agreements.
Suppliers are often willing to provide discounts or favorable terms for larger or extended orders, which can reduce overall procurement costs.
3. Technical Specifications and Customization
Clearly communicate your technical requirements and be open to customization options.
Suppliers may offer tailored solutions that better fit your manufacturing needs, often at a reduced cost compared to standardized options.
4. Service and Support Agreements
Pay attention to service and support terms during negotiations.
Ensure that the supplier offers comprehensive after-sales support, including maintenance, technical assistance, and training programs.
Reliable support can substantially reduce downtime and extend the lifespan of the robots.
Current Market Conditions
Growth and Trends
The market for single-axis robots is experiencing robust growth, fueled by increasing automation across various industries.
Technological advancements such as improved sensors, AI integration, and IoT capabilities are driving innovation and expanding the application range of these robots.
Key Players
Key players in the single-axis robot market include major Japanese manufacturers like Yamaha, IAI (Intelligent Actuator Inc.), and SMC Corporation.
These companies are renowned for their high-quality products and have a strong presence both domestically and internationally.
Understanding the strengths and offerings of each can guide procurement decisions.
Competitive Landscape
The competitive landscape is marked by intense competition and rapid innovation.
Emerging players and start-ups are introducing new technologies and cost-effective solutions, creating a dynamic market environment.
Staying abreast of these developments is crucial for making informed procurement decisions.
Best Practices for Implementation
1. Define Objectives Clearly
Start by clearly defining what you aim to achieve with the integration of single-axis robots.
Whether it’s improving speed, precision, or reducing costs, well-defined objectives guide the selection and deployment process.
2. Conduct a Thorough Needs Assessment
A thorough needs assessment should evaluate the specific requirements of your manufacturing process.
Identify tasks that can be automated and determine the technical specifications needed for those tasks.
This assessment helps in selecting the right robots and customizing them if necessary.
3. Pilot Testing
Before a full-scale rollout, conduct pilot tests.
This allows you to validate the performance of the single-axis robots in real-world conditions.
Pilot testing can reveal potential issues and provide insights into necessary adjustments or optimizations.
4. Train Operators
Invest in comprehensive training programs for operators.
Proficiency in programming and managing single-axis robots maximizes their utility and ensures smoother integration into existing processes.
Training also reduces the likelihood of operational errors.
5. Monitor Performance and Iterate
After deployment, continuously monitor the performance of the robots.
Use data analytics to track key performance indicators (KPIs) and identify areas for improvement.
Regular evaluation and iteration ensure that the robots consistently meet operational goals.
Conclusion: Maximizing the Benefits of Single-Axis Robots
Single-axis robots represent a powerful tool in the arsenal of modern Japanese manufacturing.
Their ability to enhance precision, reduce costs, and integrate seamlessly into existing processes makes them an invaluable asset.
However, successful adoption hinges on understanding their strengths and limitations, negotiating effectively with suppliers, and following best practices for implementation.
By applying these insights and strategies, manufacturers can not only optimize their operations but also position themselves at the forefront of the industry’s ongoing evolution.
In this way, the power of single-axis robots can be fully leveraged to drive innovation and excellence in manufacturing.
資料ダウンロード
QCD管理受発注クラウド「newji」は、受発注部門で必要なQCD管理全てを備えた、現場特化型兼クラウド型の今世紀最高の受発注管理システムとなります。
ユーザー登録
受発注業務の効率化だけでなく、システムを導入することで、コスト削減や製品・資材のステータス可視化のほか、属人化していた受発注情報の共有化による内部不正防止や統制にも役立ちます。
NEWJI DX
製造業に特化したデジタルトランスフォーメーション(DX)の実現を目指す請負開発型のコンサルティングサービスです。AI、iPaaS、および先端の技術を駆使して、製造プロセスの効率化、業務効率化、チームワーク強化、コスト削減、品質向上を実現します。このサービスは、製造業の課題を深く理解し、それに対する最適なデジタルソリューションを提供することで、企業が持続的な成長とイノベーションを達成できるようサポートします。
製造業ニュース解説
製造業、主に購買・調達部門にお勤めの方々に向けた情報を配信しております。
新任の方やベテランの方、管理職を対象とした幅広いコンテンツをご用意しております。
お問い合わせ
コストダウンが利益に直結する術だと理解していても、なかなか前に進めることができない状況。そんな時は、newjiのコストダウン自動化機能で大きく利益貢献しよう!
(β版非公開)