- お役立ち記事
- Revolutionizing Japanese Manufacturing: Harnessing the Power of ICC Profiles
月間76,176名の
製造業ご担当者様が閲覧しています*
*2025年3月31日現在のGoogle Analyticsのデータより
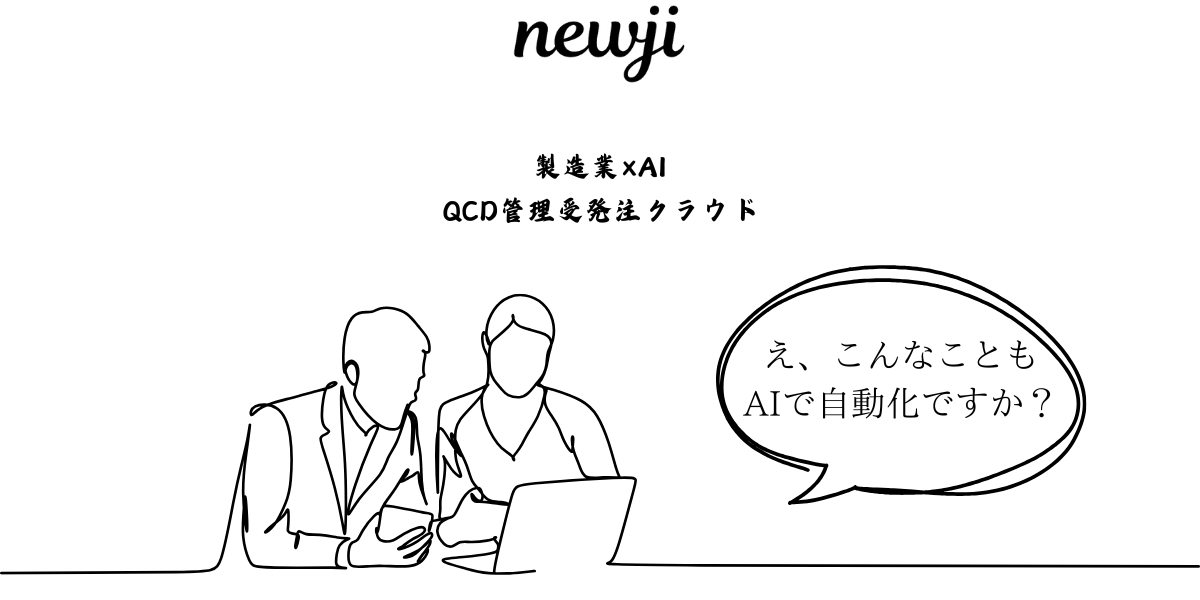
Revolutionizing Japanese Manufacturing: Harnessing the Power of ICC Profiles
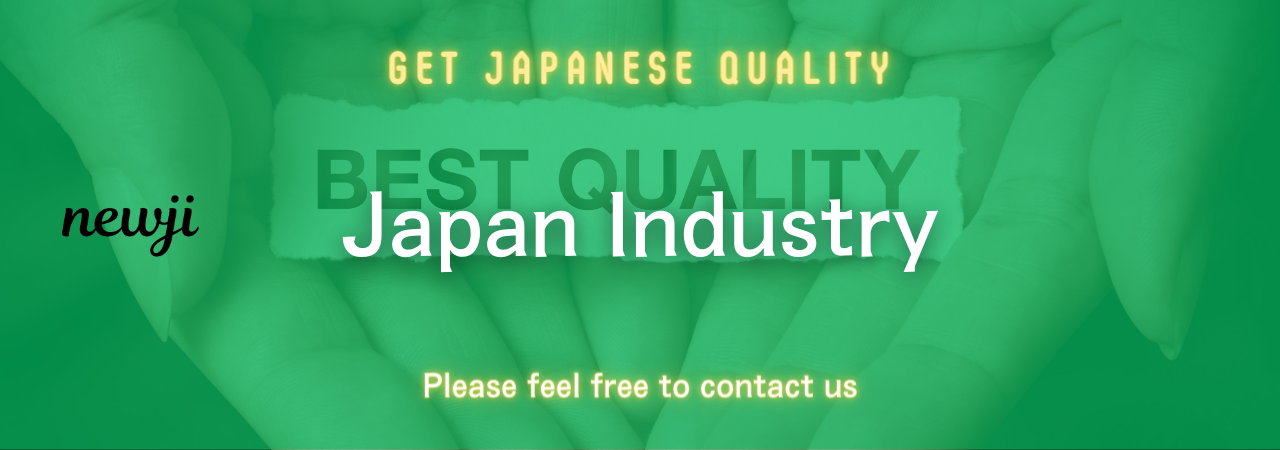
目次
Introduction to ICC Profiles in Japanese Manufacturing
Japanese manufacturing has long been synonymous with precision, quality, and innovation.
The integration of ICC (International Color Consortium) profiles is revolutionizing this landscape.
ICC profiles are essential tools for color management, ensuring consistency and accuracy across various devices and stages of production.
In the context of manufacturing, especially in sectors like automotive, electronics, and consumer goods, color fidelity plays a crucial role.
This article explores how Japanese manufacturers are leveraging ICC profiles to enhance their processes, the advantages and challenges involved, and best practices for successful implementation.
Understanding ICC Profiles
What Are ICC Profiles?
ICC profiles are standardized color profiles that define how colors are represented across different devices.
They ensure that colors remain consistent from the digital design stage to the final physical product.
By translating color information between devices such as scanners, monitors, printers, and cameras, ICC profiles maintain color accuracy.
In manufacturing, this consistency is vital for product quality and brand integrity.
Importance of Color Management in Manufacturing
Color management ensures that products meet specified color standards, which is essential for maintaining brand identity.
In industries like automotive, precise color matching is crucial for components that must fit seamlessly.
Similarly, in electronics, consistent color coding can enhance usability and aesthetics.
Accurate color representation also reduces waste and increases efficiency by minimizing errors during production.
Advantages of Implementing ICC Profiles in Japanese Manufacturing
Enhanced Quality Control
Implementing ICC profiles allows for meticulous color quality control.
Manufacturers can detect and correct color deviations early in the production process.
This leads to higher quality products that meet customer expectations consistently.
Increased Efficiency and Reduced Waste
With accurate color management, manufacturers can reduce trial and error in the production process.
This minimizes material waste and lowers production costs.
Automated color checks streamline workflows, enhancing overall efficiency.
Strengthened Brand Consistency
Consistent color representation reinforces brand identity across all products.
Customers recognize and trust brands that maintain high-quality standards.
Improved Supplier Collaboration
ICC profiles facilitate better communication and understanding between manufacturers and suppliers.
Clear color specifications ensure that suppliers deliver components that meet exact requirements.
This minimizes the need for rework and fosters stronger business relationships.
Challenges in Adopting ICC Profiles
Initial Implementation Costs
Setting up a robust color management system requires investment in software, hardware, and training.
Small and medium-sized enterprises may find the initial costs prohibitive.
Technical Complexity
Effective use of ICC profiles demands specialized knowledge and expertise.
Manufacturers must ensure that all devices in the production chain are properly calibrated.
Integration with Existing Systems
Integrating ICC profiles into established manufacturing systems can be challenging.
Legacy systems may require significant modifications or upgrades.
Maintaining Consistency Across Global Operations
For Japanese manufacturers operating internationally, maintaining color consistency across different regions and suppliers adds another layer of complexity.
Supplier Negotiation Techniques Using ICC Profiles
Setting Clear Color Standards
Establishing precise color standards is crucial when negotiating with suppliers.
Using ICC profiles allows manufacturers to communicate exact color requirements clearly.
Collaborative Training and Support
Providing suppliers with training on ICC profile usage ensures they understand and can meet color specifications.
This collaborative approach fosters trust and reliability.
Leveraging Technology for Transparency
Utilizing technology to share and validate ICC profiles enhances transparency in the supply chain.
Manufacturers can monitor and verify color consistency in real-time.
Incentivizing Compliance
Offering incentives for suppliers who consistently meet color standards can encourage adherence.
This can include long-term contracts or preferred supplier status.
Market Conditions and Trends
Growing Demand for Customization
Consumers increasingly seek personalized products with unique color variations.
Japanese manufacturers can leverage ICC profiles to efficiently manage and reproduce these custom colors.
Advancements in Digital Printing
The rise of digital printing technologies in manufacturing processes enhances the applicability of ICC profiles.
These technologies rely heavily on accurate color management for high-quality outputs.
Sustainability and Waste Reduction
There is a growing emphasis on sustainable manufacturing practices.
Accurate color management reduces waste, aligning with environmentally friendly initiatives.
Globalization and Supply Chain Complexity
As supply chains become more global, maintaining color consistency across various regions and suppliers is increasingly important.
ICC profiles offer a standardized solution to this challenge.
Best Practices for Implementing ICC Profiles
Comprehensive Training Programs
Investing in training ensures that all employees understand the importance of color management and how to use ICC profiles effectively.
Regular Calibration and Maintenance
Regularly calibrating devices and updating ICC profiles is essential to maintain color accuracy.
Collaborative Supplier Relationships
Building strong relationships with suppliers facilitates better communication and adherence to color standards.
Investment in Quality Tools and Software
Utilizing advanced color management tools and software ensures precise control over color processes.
Continuous Monitoring and Improvement
Implementing a system for continuous monitoring allows manufacturers to identify and address color discrepancies promptly.
This commitment to improvement enhances overall product quality.
Case Studies: Successful Implementation of ICC Profiles
Automotive Industry
A leading Japanese automotive manufacturer integrated ICC profiles into their paint production process.
This led to a 20% reduction in color discrepancies and improved customer satisfaction.
Electronics Sector
An electronics company adopted ICC profiles for their consumer products, ensuring consistent color across different batches.
This consistency strengthened their brand reputation and reduced returns due to color mismatches.
Consumer Goods Manufacturers
A packaging manufacturer implemented ICC profiles for their clients, resulting in more accurate color reproduction and higher client retention rates.
Future Outlook
The adoption of ICC profiles in Japanese manufacturing is expected to grow as industries continue to prioritize quality and consistency.
Advancements in color management technologies will further enhance the capabilities of ICC profiles.
Integration with emerging technologies like artificial intelligence and machine learning could lead to even more precise color control.
As global markets become more competitive, the ability to maintain high color standards will be a significant differentiator for Japanese manufacturers.
Conclusion
Harnessing the power of ICC profiles represents a significant advancement in Japanese manufacturing.
By ensuring color consistency and accuracy, manufacturers can enhance product quality, reduce waste, and strengthen brand identity.
While challenges such as implementation costs and technical complexities exist, the long-term benefits far outweigh the initial hurdles.
Adopting best practices and fostering collaborative relationships with suppliers are essential for successful integration.
As the manufacturing landscape evolves, ICC profiles will continue to play a pivotal role in driving innovation and excellence in Japanese industries.
資料ダウンロード
QCD管理受発注クラウド「newji」は、受発注部門で必要なQCD管理全てを備えた、現場特化型兼クラウド型の今世紀最高の受発注管理システムとなります。
ユーザー登録
受発注業務の効率化だけでなく、システムを導入することで、コスト削減や製品・資材のステータス可視化のほか、属人化していた受発注情報の共有化による内部不正防止や統制にも役立ちます。
NEWJI DX
製造業に特化したデジタルトランスフォーメーション(DX)の実現を目指す請負開発型のコンサルティングサービスです。AI、iPaaS、および先端の技術を駆使して、製造プロセスの効率化、業務効率化、チームワーク強化、コスト削減、品質向上を実現します。このサービスは、製造業の課題を深く理解し、それに対する最適なデジタルソリューションを提供することで、企業が持続的な成長とイノベーションを達成できるようサポートします。
製造業ニュース解説
製造業、主に購買・調達部門にお勤めの方々に向けた情報を配信しております。
新任の方やベテランの方、管理職を対象とした幅広いコンテンツをご用意しております。
お問い合わせ
コストダウンが利益に直結する術だと理解していても、なかなか前に進めることができない状況。そんな時は、newjiのコストダウン自動化機能で大きく利益貢献しよう!
(β版非公開)