- お役立ち記事
- Revolutionizing Japanese Manufacturing: How 3D Sensors are Driving Unprecedented Innovation
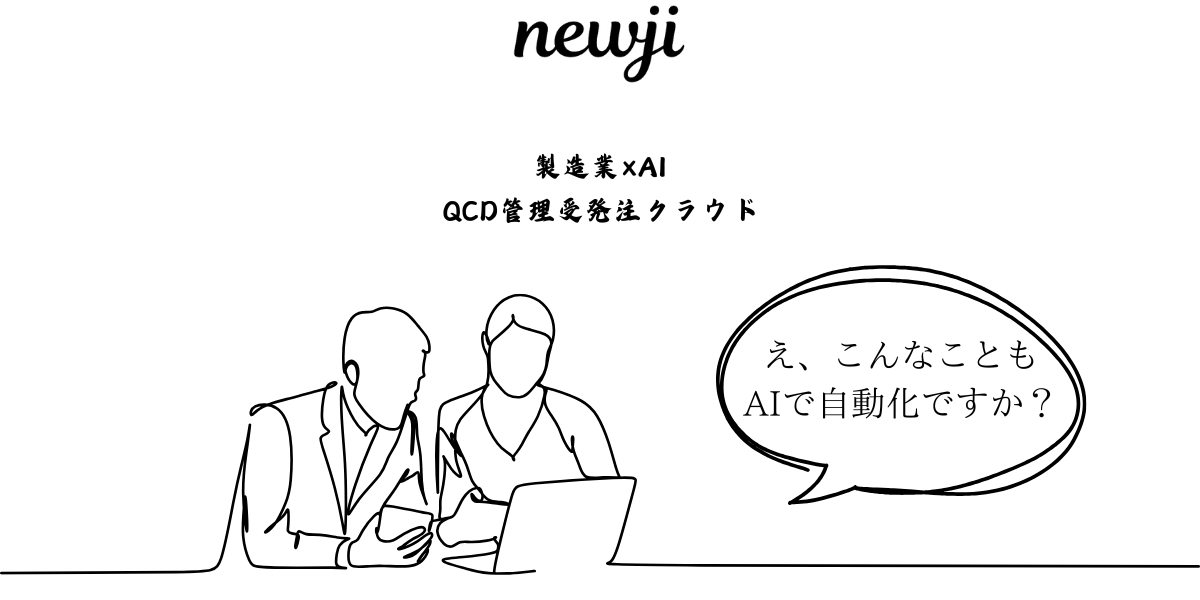
Revolutionizing Japanese Manufacturing: How 3D Sensors are Driving Unprecedented Innovation
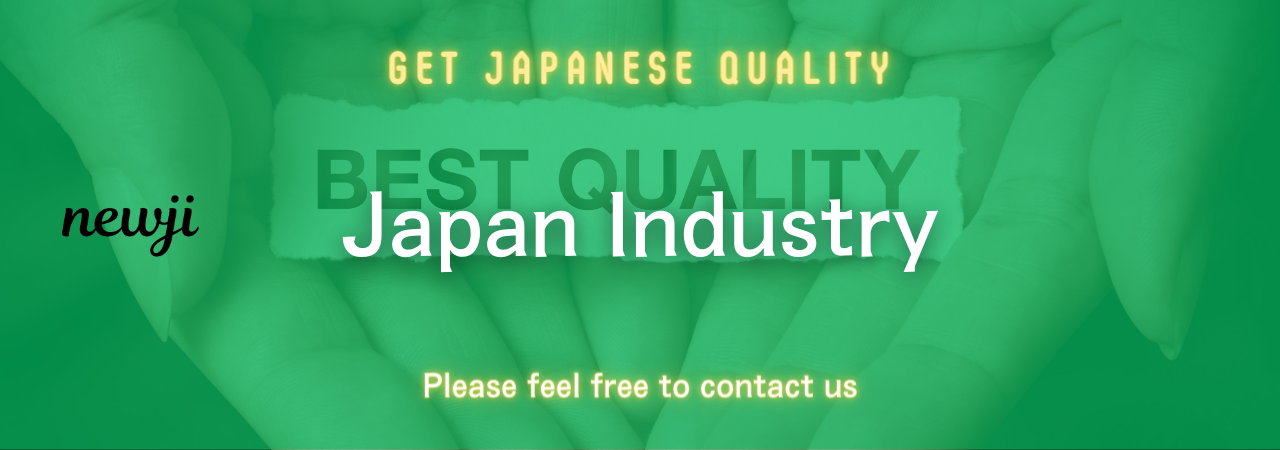
目次
Introduction
Japanese manufacturing has long been synonymous with precision, quality, and innovation.
As global markets become increasingly competitive, maintaining these standards while embracing new technologies is essential for staying ahead.
One such technological advancement is the advent of 3D sensors.
Initially seen as a high-tech luxury, 3D sensors are now driving an unprecedented wave of innovation across various Japanese industries.
This article delves into how 3D sensors are revolutionizing Japanese manufacturing, examining their practical applications, advantages, disadvantages, negotiation techniques with suppliers, market conditions, and best practices for their deployment.
Understanding 3D Sensors
What are 3D Sensors?
3D sensors are devices that capture spatial data about objects in their environment.
Unlike traditional 2D sensors, which only capture information on a single plane, 3D sensors provide depth information, enabling a richer, more detailed understanding of the surroundings.
These sensors employ various methods such as structured light, time-of-flight, and stereo vision to gather data.
Types of 3D Sensors
1. Structured Light Sensors – Use projected light patterns to determine object shape and depth.
2. Time-of-Flight (ToF) Sensors – Measure the time it takes for light to bounce off an object and return to the sensor, offering precise distance measurements.
3. Stereo Vision Sensors – Use two or more cameras to mimic human binocular vision, calculating depth through triangulation.
The Role of 3D Sensors in Manufacturing
Precision and Quality Control
One of the most immediate benefits of integrating 3D sensors into the manufacturing process is enhanced precision and quality control.
With their ability to capture intricate details, 3D sensors can identify minute defects in real-time, enabling rapid corrective actions.
This capability is particularly valuable in high-stakes industries such as automotive and aerospace, where component precision is crucial.
Automation and Efficiency
3D sensors play a pivotal role in powering automated systems, robots, and production lines.
They provide the spatial awareness necessary for machines to navigate complex environments autonomously.
For instance, automated guided vehicles (AGVs) equipped with 3D sensors can move through factory floors with greater accuracy and safety.
This level of automation reduces human error, minimizes downtime, and boosts overall productivity.
Enhancing Design and Prototyping
In the design and prototyping phases, 3D sensors allow for rapid, accurate measurements and scans of physical objects.
These data points can then be used to create highly detailed 3D models, accelerating the iterative design process.
This capability is incredibly beneficial for industries that rely on customized or bespoke products, as it reduces the time from concept to market.
Advantages and Disadvantages of 3D Sensors
Advantages
1. **Enhanced Accuracy** – 3D sensors provide high-resolution data that significantly improve the accuracy of measurements and inspections.
2. **Increased Automation** – By enabling more sophisticated robotic systems, 3D sensors reduce the need for manual labor, leading to cost savings and efficiency gains.
3. **Improved Safety** – With better spatial awareness, automated systems can operate more safely, reducing the risk of accidents on the factory floor.
4. **Versatility** – 3D sensors can be used in a wide range of applications, from quality control and inspection to logistics and material handling.
Disadvantages
1. **High Initial Costs** – The investment required for 3D sensor systems and the associated equipment can be considerable.
2. **Complex Integration** – Integrating 3D sensors into existing systems may require substantial modifications and technical expertise.
3. **Data Overload** – The sheer volume of data generated by 3D sensors can be overwhelming, necessitating advanced data management and processing solutions.
Supplier Negotiation Techniques
Research and Preparation
Before entering into negotiations with suppliers, it is crucial to conduct thorough research.
Understand the market landscape, the key players, and the typical pricing structures.
Familiarize yourself with the technical specifications of the 3D sensors you require and have a clear understanding of your production needs.
Building Relationships
In Japanese business culture, building strong, long-term relationships with suppliers is essential.
Take the time to establish trust and demonstrate your commitment to mutual success.
This approach often leads to better terms and more reliable partnerships.
Leverage Existing Relationships
If you already have a network of suppliers in Japan, leverage these existing relationships to negotiate better deals on 3D sensors.
Suppliers may be more willing to offer favorable terms to a known and trusted customer.
Cost-Benefit Analysis
Present a detailed cost-benefit analysis to the supplier, demonstrating how the 3D sensors will improve your production processes and lead to long-term savings.
This can help justify your pricing proposals and lead to more favorable terms.
Volume Negotiations
Consider negotiating based on volume commitments.
Suppliers are often willing to offer discounts for larger orders, which can be beneficial if you anticipate scaling up production in the future.
Market Conditions
Current Landscape
The market for 3D sensors is rapidly growing, driven by advancements in technology and increasing adoption across various industries.
Japan remains a leader in sensor technology, with several prominent companies dominating the market.
The demand for high-precision sensors, particularly in sectors such as automotive, healthcare, and consumer electronics, is fueling this growth.
Competitive Landscape
While Japanese manufacturers are at the forefront, they face competition from global counterparts, particularly from South Korea, Germany, and the United States.
Staying competitive requires continuous innovation and maintaining high standards of quality.
Regulatory Considerations
Compliance with local and international regulations is a critical factor.
Ensure that the 3D sensors meet all relevant standards and certifications, which can vary depending on the industry and the specific application.
Supply Chain Resilience
Given the global nature of supply chains, it is important to consider the resilience of your suppliers.
Assess their ability to deliver consistently, even in times of disruption.
Diversifying your supplier base can mitigate risks and ensure a steady supply of high-quality sensors.
Best Practices for Deploying 3D Sensors
Comprehensive Training Programs
Ensure that your workforce is well-trained in the use of 3D sensors.
Comprehensive training programs will maximize the effectiveness of the technology and minimize errors.
Gradual Integration
Implement 3D sensors gradually, starting with pilot projects to identify potential challenges and fine-tune the integration process.
This approach reduces the risk of disruptions to ongoing operations.
Collaboration Across Departments
Foster collaboration between different departments, including engineering, procurement, and production management.
A holistic approach ensures that the benefits of 3D sensors are fully realized across the organization.
Data Management Strategy
Develop a robust data management strategy to handle the large volumes of data generated by 3D sensors.
Invest in advanced analytics and data processing tools to extract actionable insights and drive continuous improvement.
Regular Maintenance and Calibration
Regular maintenance and calibration of 3D sensors are essential to ensure their ongoing accuracy and reliability.
Schedule periodic checks and updates to keep the systems in top condition.
Conclusion
The integration of 3D sensors into Japanese manufacturing processes marks a significant step forward in the pursuit of precision, efficiency, and innovation.
From enhancing quality control to driving automation and improving safety, the benefits are substantial.
However, realizing these advantages requires careful planning, strategic supplier negotiations, and a commitment to continuous improvement.
By staying informed about market conditions and adopting best practices, manufacturers can leverage 3D sensor technology to revolutionize their operations and remain competitive in the global market.
資料ダウンロード
QCD調達購買管理クラウド「newji」は、調達購買部門で必要なQCD管理全てを備えた、現場特化型兼クラウド型の今世紀最高の購買管理システムとなります。
ユーザー登録
調達購買業務の効率化だけでなく、システムを導入することで、コスト削減や製品・資材のステータス可視化のほか、属人化していた購買情報の共有化による内部不正防止や統制にも役立ちます。
NEWJI DX
製造業に特化したデジタルトランスフォーメーション(DX)の実現を目指す請負開発型のコンサルティングサービスです。AI、iPaaS、および先端の技術を駆使して、製造プロセスの効率化、業務効率化、チームワーク強化、コスト削減、品質向上を実現します。このサービスは、製造業の課題を深く理解し、それに対する最適なデジタルソリューションを提供することで、企業が持続的な成長とイノベーションを達成できるようサポートします。
オンライン講座
製造業、主に購買・調達部門にお勤めの方々に向けた情報を配信しております。
新任の方やベテランの方、管理職を対象とした幅広いコンテンツをご用意しております。
お問い合わせ
コストダウンが利益に直結する術だと理解していても、なかなか前に進めることができない状況。そんな時は、newjiのコストダウン自動化機能で大きく利益貢献しよう!
(Β版非公開)