- お役立ち記事
- Revolutionizing Japanese Manufacturing: How Advanced Detection Systems are Leading the Way
月間76,176名の
製造業ご担当者様が閲覧しています*
*2025年3月31日現在のGoogle Analyticsのデータより
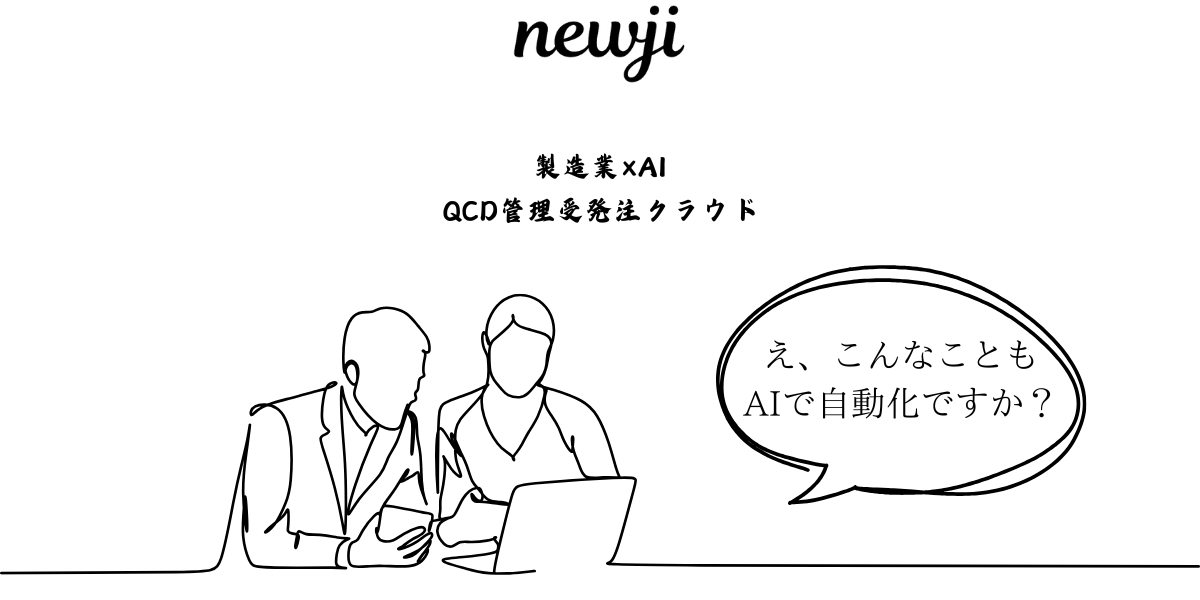
Revolutionizing Japanese Manufacturing: How Advanced Detection Systems are Leading the Way
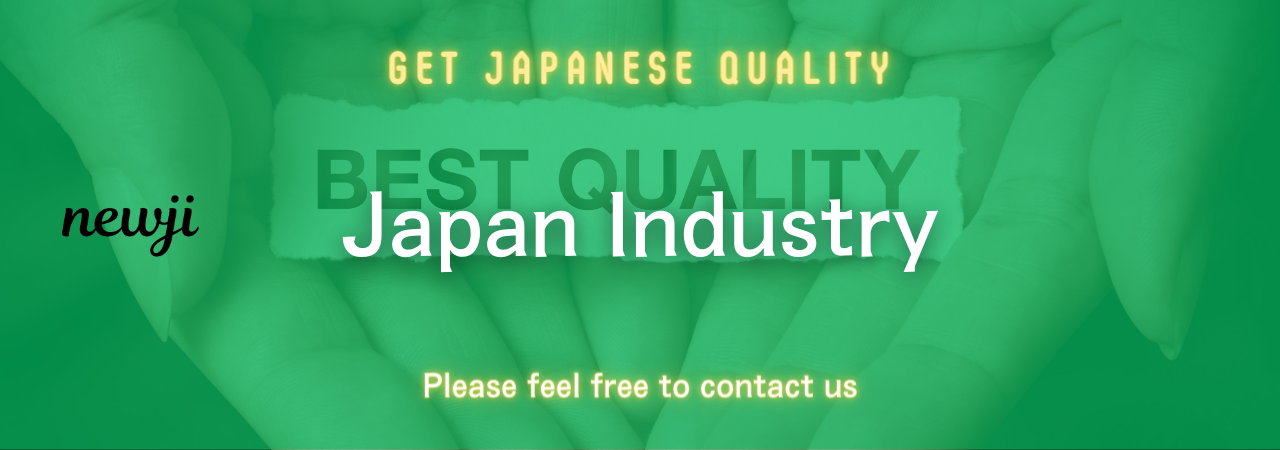
目次
Introduction to Advanced Detection Systems in Japanese Manufacturing
Japanese manufacturing has long been synonymous with precision, quality, and innovation. In recent years, the integration of advanced detection systems has further elevated the industry, setting new benchmarks for efficiency and excellence. These systems encompass a range of technologies, including machine vision, artificial intelligence (AI), and sensor-based monitoring, all of which play pivotal roles in transforming manufacturing processes.
The adoption of these advanced detection systems is not merely a technological upgrade but a strategic move that influences procurement, supplier relationships, and overall supply chain dynamics. Understanding the impact of these systems is crucial for companies looking to collaborate with Japanese suppliers and leverage the benefits of cutting-edge manufacturing practices.
The Role of Advanced Detection Systems in Enhancing Manufacturing Processes
Advanced detection systems contribute significantly to various stages of the manufacturing process. Their applications span from quality control to predictive maintenance, ensuring that manufacturing operations run smoothly and efficiently.
Quality Control and Assurance
One of the primary applications of advanced detection systems is in quality control. Machine vision systems equipped with high-resolution cameras and sophisticated algorithms can inspect products with unparalleled accuracy. These systems can detect minute defects that might be overlooked by the human eye, ensuring that only products meeting stringent quality standards reach the market.
The implementation of AI-driven inspection tools allows for real-time data analysis, enabling immediate corrective actions. This proactive approach minimizes waste, reduces rework, and enhances overall product reliability.
Predictive Maintenance
Advanced detection systems play a critical role in predictive maintenance by monitoring the condition of machinery and equipment in real-time. Sensors embedded in manufacturing equipment collect data on various parameters such as temperature, vibration, and pressure. AI algorithms analyze this data to predict potential failures before they occur.
By anticipating equipment malfunctions, companies can schedule timely maintenance, thereby preventing costly downtime and extending the lifespan of their machinery. This approach not only improves operational efficiency but also contributes to significant cost savings over time.
Process Optimization
AI-powered detection systems facilitate process optimization by analyzing production data to identify bottlenecks and inefficiencies. Through continuous monitoring and data-driven insights, these systems enable manufacturers to streamline their operations, reduce cycle times, and enhance overall productivity.
Moreover, advanced detection systems support the implementation of smart manufacturing practices, where interconnected machines communicate seamlessly to optimize workflows. This level of integration fosters a more agile and responsive manufacturing environment, capable of adapting to changing market demands swiftly.
Advantages of Implementing Advanced Detection Systems
The adoption of advanced detection systems in Japanese manufacturing offers a multitude of benefits that extend beyond immediate operational improvements.
Enhanced Precision and Accuracy
Advanced detection systems provide unparalleled precision in monitoring and controlling manufacturing processes. The ability to detect minute variations ensures that products meet exact specifications, reducing the likelihood of defects and enhancing overall product quality.
Increased Efficiency and Productivity
By automating inspection and monitoring tasks, advanced detection systems free up human resources to focus on more strategic activities. This leads to a more efficient allocation of labor and a significant increase in productivity. Additionally, the ability to identify and address inefficiencies in real-time ensures that production processes are optimized for maximum output.
Cost Reduction
Implementing advanced detection systems can lead to substantial cost savings in various areas. Improved quality control reduces the costs associated with rework and returns. Predictive maintenance minimizes downtime and extends the lifespan of equipment, thereby lowering maintenance and replacement costs. Furthermore, process optimization results in more efficient resource utilization, contributing to overall cost reduction.
Competitive Advantage
Companies that leverage advanced detection systems gain a competitive edge in the market. Enhanced product quality, increased efficiency, and reduced costs translate into better market positioning and higher customer satisfaction. Additionally, the ability to innovate and adapt quickly to market changes fosters long-term sustainability and growth.
Challenges and Disadvantages
While the benefits of advanced detection systems are substantial, their implementation is not without challenges.
High Initial Investment
The adoption of advanced detection systems requires significant upfront investment in technology, infrastructure, and training. For smaller companies or those with limited budgets, the initial costs can be a substantial barrier to entry.
Integration Complexity
Integrating advanced detection systems with existing manufacturing processes and legacy systems can be complex and time-consuming. Ensuring seamless communication and data flow between different technologies requires careful planning and expertise, which may necessitate additional resources.
Skill Gap
Operating and maintaining advanced detection systems often require specialized skills that may not be readily available within the existing workforce. Companies may need to invest in training or hire new talent, adding to the overall costs and complexity of implementation.
Data Security and Privacy
The extensive data collection and analysis involved in advanced detection systems raise concerns about data security and privacy. Ensuring that sensitive manufacturing data is protected against cyber threats is paramount, necessitating robust cybersecurity measures and protocols.
Supplier Negotiation Techniques in the Context of Advanced Detection Systems
Effective supplier negotiation is crucial when procuring advanced detection systems from Japanese manufacturers. Given the complexity and criticality of these systems, developing strong partnerships and clear communication channels with suppliers is essential.
Understanding Supplier Capabilities
Before entering negotiations, it is important to thoroughly understand the capabilities and expertise of potential suppliers. Assessing their experience with advanced detection systems, their technological competencies, and their track record in delivering high-quality solutions will inform negotiation strategies.
Establishing Clear Requirements
Clearly defining the technical specifications, performance expectations, and quality standards for advanced detection systems ensures that both parties have a mutual understanding of the project scope. Detailed requirements help prevent misunderstandings and set the foundation for effective collaboration.
Value-Based Negotiation
Focusing on the value that suppliers can bring beyond just the product cost is a key negotiation tactic. This includes aspects such as ongoing support, customization capabilities, and the ability to collaborate on future innovations. Emphasizing long-term partnerships over short-term gains can lead to more favorable terms and stronger supplier relationships.
Leveraging Local Relationships
Japanese business culture places significant emphasis on building strong, trust-based relationships. Leveraging local connections and demonstrating respect for cultural norms can enhance negotiation outcomes. Engaging in face-to-face meetings, investing time in relationship-building, and showing commitment to mutual success are important strategies.
Market Conditions Affecting Procurement of Advanced Detection Systems
The global market dynamics play a crucial role in the procurement of advanced detection systems from Japanese suppliers. Understanding these conditions helps in making informed purchasing decisions and negotiating better terms.
Technological Advancements
Rapid advancements in technology continually reshape the capabilities of detection systems. Staying abreast of the latest developments ensures that procurement strategies align with current and future technological trends, allowing companies to adopt state-of-the-art solutions.
Supply Chain Disruptions
Global events, such as pandemics or geopolitical tensions, can disrupt supply chains and impact the availability of advanced detection systems. Diversifying suppliers and developing contingency plans are essential strategies to mitigate the risks associated with such disruptions.
Economic Factors
Exchange rates, inflation, and economic stability influence the cost and feasibility of procuring advanced detection systems. Monitoring economic indicators helps in timing purchases to take advantage of favorable conditions and avoid potential cost escalations.
Regulatory Environment
Compliance with international and local regulations regarding manufacturing, data security, and trade is imperative. Understanding the regulatory landscape ensures that the procurement and implementation of advanced detection systems adhere to all relevant laws and standards.
Best Practices for Procuring Advanced Detection Systems from Japan
Adhering to best practices can significantly enhance the effectiveness and efficiency of procuring advanced detection systems from Japanese suppliers.
Comprehensive Needs Assessment
Conducting a thorough needs assessment helps in identifying the specific requirements and objectives for advanced detection systems. This involves evaluating current processes, identifying areas for improvement, and determining the desired outcomes from the implementation of these systems.
Collaborative Planning
Engaging in collaborative planning with suppliers fosters a deeper understanding of mutual goals and facilitates the development of tailored solutions. Joint planning sessions can help in aligning expectations, addressing potential challenges, and ensuring that the procurement process progresses smoothly.
Quality Assurance and Testing
Implementing stringent quality assurance measures and comprehensive testing protocols ensures that the advanced detection systems meet the required standards. This includes conducting pilot projects, performing rigorous evaluations, and validating performance metrics before full-scale deployment.
Continuous Improvement and Feedback
Establishing mechanisms for continuous improvement and regular feedback loops promotes the ongoing enhancement of advanced detection systems. Collaborative reviews and feedback sessions with suppliers help in identifying areas for refinement and fostering innovation.
Case Studies: Success Stories in Japanese Manufacturing
Examining real-world examples of successful implementation of advanced detection systems in Japanese manufacturing provides valuable insights and lessons.
Automotive Industry: Enhancing Precision in Production
A leading Japanese automotive manufacturer integrated AI-powered machine vision systems into their assembly line. These systems enabled real-time identification of defects in components, significantly reducing the rate of faulty parts reaching the final product. The improved quality control not only enhanced customer satisfaction but also decreased production costs by minimizing waste and rework.
Electronics Manufacturing: Streamlining Quality Assurance
A prominent electronics company adopted advanced sensor-based detection systems to monitor the production of microchips. The system’s ability to detect minuscule variations in the manufacturing process ensured that only chips meeting exact specifications were approved. This led to a marked improvement in product reliability and a reduction in warranty claims.
Precision Engineering: Optimizing Production Efficiency
A Japanese precision engineering firm implemented predictive maintenance using advanced detection systems to monitor their CNC machines. By predicting potential failures before they occurred, the company minimized downtime and optimized maintenance schedules. This proactive approach resulted in increased operational efficiency and extended machinery lifespan.
Future Trends in Advanced Detection Systems
The landscape of advanced detection systems is continually evolving, with several emerging trends poised to shape the future of Japanese manufacturing.
Integration of Internet of Things (IoT)
The integration of IoT technologies with advanced detection systems promises enhanced connectivity and data sharing across the manufacturing ecosystem. Smart sensors and interconnected devices facilitate seamless communication, enabling more sophisticated monitoring and control capabilities.
Advancements in AI and Machine Learning
Continued advancements in AI and machine learning are set to enhance the capabilities of detection systems. These technologies enable more accurate data analysis, predictive analytics, and autonomous decision-making, further improving manufacturing processes.
Augmented Reality (AR) for Maintenance and Training
AR technologies are increasingly being used in conjunction with advanced detection systems to support maintenance activities and training programs. AR can provide technicians with real-time visual guidance, improving accuracy and efficiency in maintenance tasks.
Sustainability and Eco-Friendly Manufacturing
As sustainability becomes a key focus, advanced detection systems are being designed to support eco-friendly manufacturing practices. These systems help in monitoring energy consumption, reducing waste, and ensuring compliance with environmental regulations, contributing to greener manufacturing processes.
Conclusion
Advanced detection systems are revolutionizing Japanese manufacturing by enhancing precision, efficiency, and quality across various production processes. The strategic implementation of these technologies offers significant advantages, including cost reduction, increased productivity, and competitive differentiation. However, companies must navigate challenges such as high initial investments, integration complexities, and skill gaps to fully realize the benefits.
Effective procurement strategies, including comprehensive needs assessment, collaborative planning, and strong supplier relationships, are essential for successfully acquiring and implementing advanced detection systems. By adhering to best practices and staying informed about market conditions and future trends, manufacturing companies can leverage these technologies to drive innovation and sustain long-term growth.
Japanese manufacturing continues to lead the way in technological advancements, and embracing advanced detection systems is a critical step for companies aiming to excel in the global market. Through careful planning, strategic partnerships, and a commitment to continuous improvement, businesses can harness the transformative power of advanced detection systems to achieve excellence in manufacturing.
資料ダウンロード
QCD管理受発注クラウド「newji」は、受発注部門で必要なQCD管理全てを備えた、現場特化型兼クラウド型の今世紀最高の受発注管理システムとなります。
ユーザー登録
受発注業務の効率化だけでなく、システムを導入することで、コスト削減や製品・資材のステータス可視化のほか、属人化していた受発注情報の共有化による内部不正防止や統制にも役立ちます。
NEWJI DX
製造業に特化したデジタルトランスフォーメーション(DX)の実現を目指す請負開発型のコンサルティングサービスです。AI、iPaaS、および先端の技術を駆使して、製造プロセスの効率化、業務効率化、チームワーク強化、コスト削減、品質向上を実現します。このサービスは、製造業の課題を深く理解し、それに対する最適なデジタルソリューションを提供することで、企業が持続的な成長とイノベーションを達成できるようサポートします。
製造業ニュース解説
製造業、主に購買・調達部門にお勤めの方々に向けた情報を配信しております。
新任の方やベテランの方、管理職を対象とした幅広いコンテンツをご用意しております。
お問い合わせ
コストダウンが利益に直結する術だと理解していても、なかなか前に進めることができない状況。そんな時は、newjiのコストダウン自動化機能で大きく利益貢献しよう!
(β版非公開)