- お役立ち記事
- Revolutionizing Japanese Manufacturing: How CAD/CAM/CAE is Shaping the Future of Industry
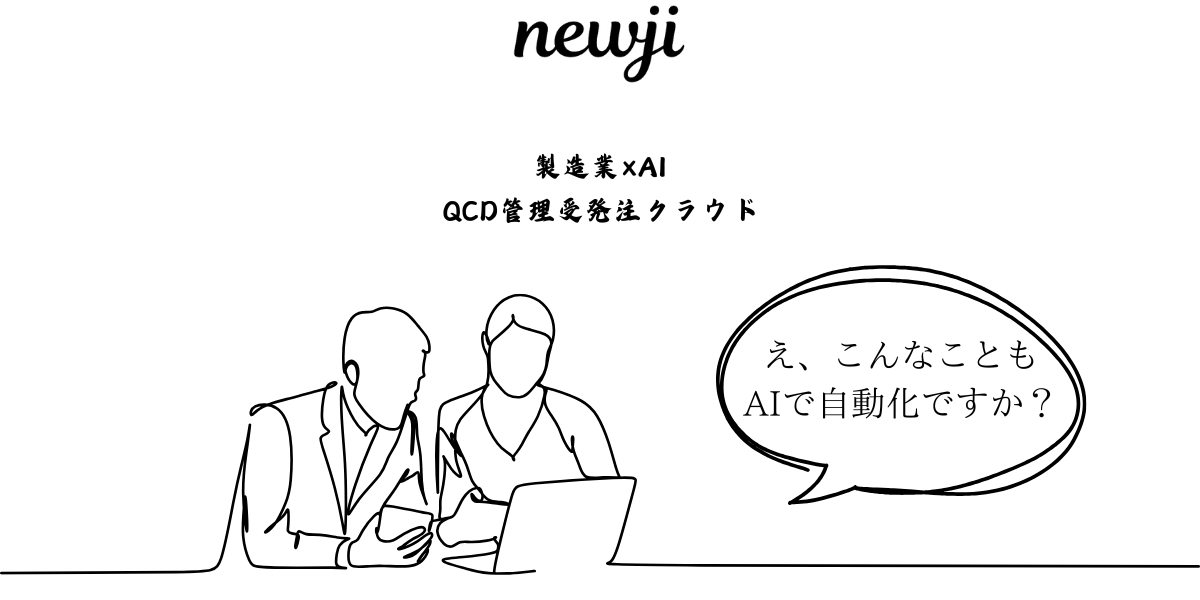
Revolutionizing Japanese Manufacturing: How CAD/CAM/CAE is Shaping the Future of Industry
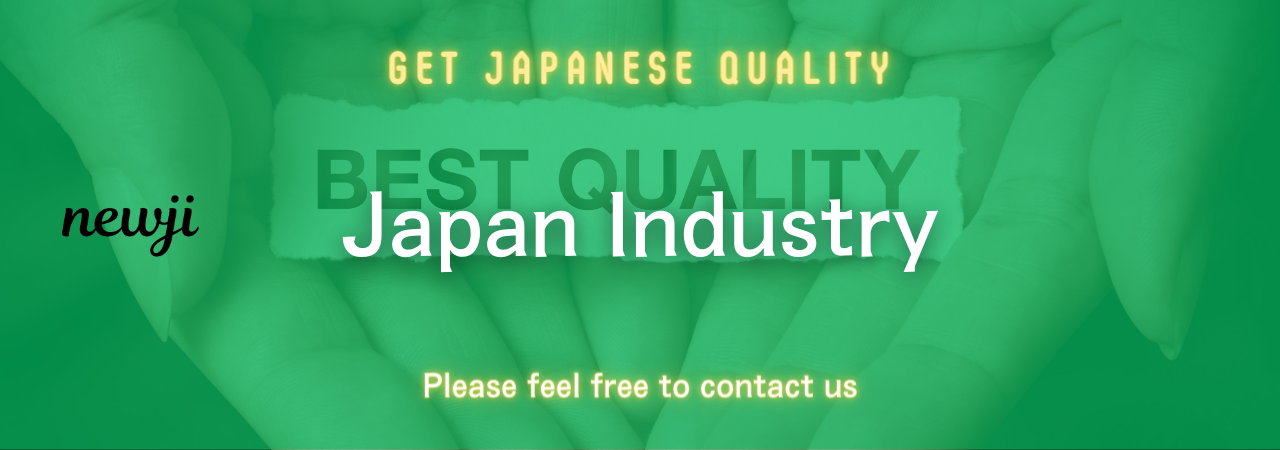
目次
Understanding CAD/CAM/CAE in Japanese Manufacturing
Computer-Aided Design (CAD), Computer-Aided Manufacturing (CAM), and Computer-Aided Engineering (CAE) are integral technologies in modern manufacturing.
In Japan, these tools have been pivotal in maintaining the country’s reputation for precision and quality.
CAD enables detailed design and visualization of products.
CAM facilitates the automation of manufacturing processes.
CAE provides advanced engineering analysis to ensure product reliability and performance.
Together, these technologies streamline the design-to-production workflow, reducing errors and enhancing efficiency.
Advantages of CAD/CAM/CAE in Japanese Manufacturing
Enhanced Precision and Quality
Japanese manufacturers are renowned for their high standards.
CAD/CAM/CAE technologies contribute significantly to this reputation by ensuring precise designs and manufacturing processes.
These tools minimize human error, leading to superior product quality and consistency.
Increased Efficiency and Productivity
Automation through CAM significantly reduces production time.
CAD/CAM integration allows for rapid prototyping and quicker iterations during the design phase.
CAE enables predictive analysis, preventing potential issues before they arise, thereby saving time and resources.
Cost Reduction
By optimizing processes and reducing waste, CAD/CAM/CAE contribute to lower production costs.
Predictive maintenance enabled by CAE can prevent costly downtime.
Efficient resource management ensures that materials are used effectively, further reducing expenses.
Innovation and Competitive Advantage
Access to advanced design and engineering tools fosters innovation.
Japanese manufacturers can develop complex and novel products that stand out in the global market.
Staying at the forefront of technology provides a significant competitive edge.
Disadvantages and Challenges
High Initial Investment
Implementing CAD/CAM/CAE systems requires substantial capital investment.
Small and medium-sized enterprises (SMEs) may find it financially challenging to adopt these technologies.
Complexity and Training
The complexity of CAD/CAM/CAE systems necessitates comprehensive training for staff.
There is a learning curve associated with mastering these tools, which can temporarily reduce productivity during the transition phase.
Integration with Existing Systems
Integrating CAD/CAM/CAE with legacy systems can be problematic.
Compatibility issues may arise, requiring additional resources to ensure seamless operation across different platforms.
Maintenance and Upgrades
Regular maintenance and timely upgrades are essential to keep CAD/CAM/CAE systems functioning optimally.
This ongoing requirement can lead to additional costs and resource allocation challenges.
Impact on Procurement and Purchasing
Streamlined Supplier Selection
CAD/CAM/CAE systems provide detailed specifications that facilitate precise supplier selection.
This ensures that suppliers can meet the exact requirements of the manufacturing process, enhancing product quality.
Improved Supplier Communication
Detailed designs and simulations generated by CAD/CAM/CAE enable clearer communication with suppliers.
This reduces misunderstandings and ensures that all parties are aligned on project objectives.
Efficient Inventory Management
Advanced planning capabilities allow for more accurate forecasting of material needs.
This leads to better inventory management, reducing excess stock and minimizing shortages.
Supplier Negotiation Techniques with Respect to CAD/CAM/CAE
Leveraging Detailed Data
Use the precise data from CAD/CAM/CAE systems to negotiate better terms with suppliers.
Detailed specifications can lead to more accurate pricing and reduce the likelihood of unexpected costs.
Building Collaborations
Foster collaborative relationships with suppliers by sharing insights from CAD/CAM/CAE analyses.
This partnership approach can lead to joint innovations and mutually beneficial agreements.
Establishing Clear Expectations
Clearly define quality and performance standards based on CAD/CAM/CAE data during negotiations.
Setting explicit expectations helps in holding suppliers accountable and ensures consistent product quality.
Negotiating for Flexibility
Utilize the flexibility of CAD/CAM/CAE to negotiate adaptable terms.
This allows for modifications in designs or processes without significant cost implications, benefiting both parties.
Market Conditions Influenced by CAD/CAM/CAE
Global Competitiveness
The adoption of CAD/CAM/CAE enhances the competitiveness of Japanese manufacturers in the global market.
Advanced technologies enable the production of high-quality, innovative products that meet international standards.
Supply Chain Dynamics
CAD/CAM/CAE integration affects supply chain dynamics by promoting closer collaboration and more efficient processes.
This leads to shorter lead times and more responsive manufacturing systems.
Market Demand for Customization
With the capabilities of CAD/CAM/CAE, manufacturers can better meet the growing demand for customized products.
This responsiveness to market trends can capture a larger market share and cater to niche segments.
Technological Advancements
Continuous advancements in CAD/CAM/CAE technologies drive market evolution.
Manufacturers must stay updated to maintain relevance and meet the ever-changing demands of the industry.
Best Practices for Implementing CAD/CAM/CAE
Comprehensive Training Programs
Invest in thorough training programs to ensure that staff are proficient in using CAD/CAM/CAE systems.
Continuous education helps maintain high productivity and maximizes the benefits of the technology.
Strategic Integration
Plan the integration of CAD/CAM/CAE systems carefully to align with existing workflows and systems.
A strategic approach minimizes disruptions and ensures a smooth transition.
Continuous Evaluation and Improvement
Regularly assess the performance of CAD/CAM/CAE systems and seek opportunities for improvement.
Feedback mechanisms can help identify areas where the technology can be better utilized.
Collaborative Supplier Relationships
Engage in open communication and collaboration with suppliers regarding CAD/CAM/CAE processes.
Strong relationships foster trust and facilitate the achievement of mutual goals.
Adoption of Industry Standards
Adhere to industry standards and best practices in the implementation of CAD/CAM/CAE systems.
Compliance with standards ensures interoperability and enhances overall system effectiveness.
Future Trends in CAD/CAM/CAE and Japanese Manufacturing
Integration with Artificial Intelligence
Artificial Intelligence (AI) is set to further enhance the capabilities of CAD/CAM/CAE.
AI-driven design and predictive analytics can lead to smarter manufacturing processes.
Internet of Things (IoT) Integration
Integrating CAD/CAM/CAE with IoT devices allows for real-time data collection and analysis.
This integration facilitates more responsive and adaptive manufacturing systems.
Additive Manufacturing
The rise of 3D printing and additive manufacturing will complement CAD/CAM/CAE technologies.
This combination enables the production of complex geometries and customized products with ease.
Sustainability and Eco-Friendly Practices
Future CAD/CAM/CAE systems will incorporate sustainability metrics to promote eco-friendly manufacturing.
This focus aligns with global trends towards reducing environmental impact and enhancing corporate responsibility.
Cloud-Based Solutions
Cloud-based CAD/CAM/CAE systems will offer greater flexibility, scalability, and collaboration opportunities.
This shift to the cloud can reduce costs and improve accessibility for manufacturers.
Conclusion
CAD/CAM/CAE technologies have revolutionized Japanese manufacturing, driving advancements in precision, efficiency, and innovation.
While there are challenges associated with their implementation, the benefits far outweigh the drawbacks.
For procurement and purchasing professionals, these technologies offer enhanced capabilities in supplier selection, communication, and inventory management.
By adopting best practices and staying abreast of future trends, Japanese manufacturers can continue to lead the industry and meet the evolving demands of the global market.
Embracing CAD/CAM/CAE is not merely a technological upgrade; it is a strategic imperative that shapes the future of manufacturing.
資料ダウンロード
QCD調達購買管理クラウド「newji」は、調達購買部門で必要なQCD管理全てを備えた、現場特化型兼クラウド型の今世紀最高の購買管理システムとなります。
ユーザー登録
調達購買業務の効率化だけでなく、システムを導入することで、コスト削減や製品・資材のステータス可視化のほか、属人化していた購買情報の共有化による内部不正防止や統制にも役立ちます。
NEWJI DX
製造業に特化したデジタルトランスフォーメーション(DX)の実現を目指す請負開発型のコンサルティングサービスです。AI、iPaaS、および先端の技術を駆使して、製造プロセスの効率化、業務効率化、チームワーク強化、コスト削減、品質向上を実現します。このサービスは、製造業の課題を深く理解し、それに対する最適なデジタルソリューションを提供することで、企業が持続的な成長とイノベーションを達成できるようサポートします。
オンライン講座
製造業、主に購買・調達部門にお勤めの方々に向けた情報を配信しております。
新任の方やベテランの方、管理職を対象とした幅広いコンテンツをご用意しております。
お問い合わせ
コストダウンが利益に直結する術だと理解していても、なかなか前に進めることができない状況。そんな時は、newjiのコストダウン自動化機能で大きく利益貢献しよう!
(Β版非公開)