- お役立ち記事
- Revolutionizing Japanese Manufacturing: How “Industrial Robots” Transform the Industry
Revolutionizing Japanese Manufacturing: How “Industrial Robots” Transform the Industry
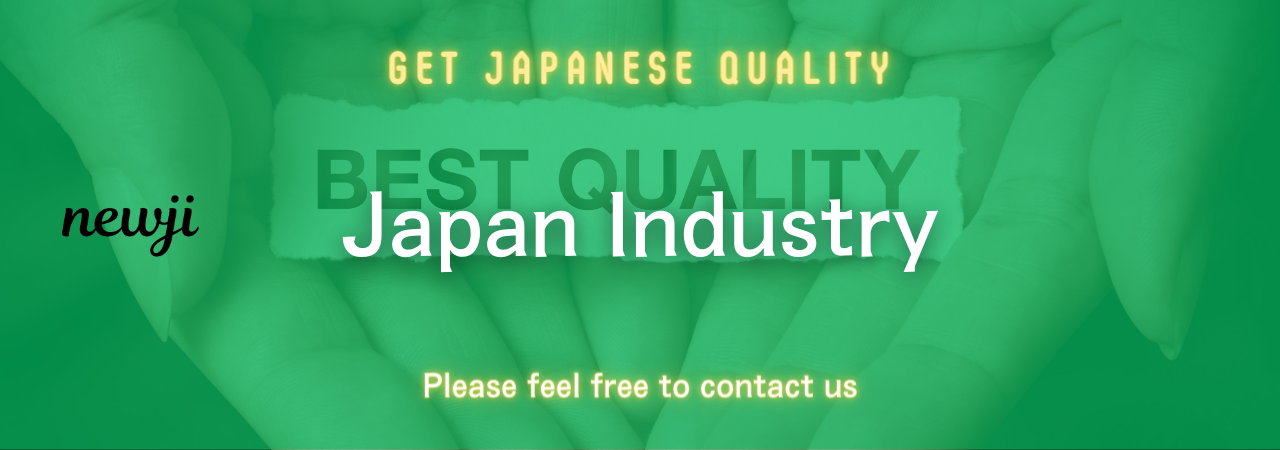
目次
Introduction to Japanese Manufacturing and the Rise of Industrial Robots
Japan has long been recognized as a global leader in manufacturing, renowned for its precision, quality, and innovation.
The culture of continuous improvement, or “kaizen,” has driven the country to the forefront of industrial advancement.
In recent years, a significant transformation has been underway, powered by the integration of industrial robots into manufacturing processes.
Industrial robots are increasingly becoming a cornerstone of Japanese manufacturing, offering immense potential to revolutionize production methods, enhance efficiency, and maintain the high-quality standards for which Japan is famed.
This new wave of automation presents both opportunities and challenges to the industry, shaping the future of manufacturing in the country.
The Role of Industrial Robots in Japanese Manufacturing
Japan’s manufacturing sector is characterized by highly specialized and sophisticated processes.
From automotive to electronics, the integration of industrial robots has been pivotal in optimizing performance and productivity.
Enhancing Productivity and Precision
Industrial robots excel in tasks that require high degrees of precision and repeatability.
They are used extensively in applications such as welding, assembly, painting, and material handling.
By automating these processes, companies can achieve higher throughput and minimize errors and defects.
Addressing Labor Shortages
Japan faces demographic challenges, with an aging population and a shrinking workforce.
Robots help mitigate the impact of labor shortages by taking on repetitive and labor-intensive tasks, allowing human workers to focus on more creative and strategic activities.
Maintaining Competitive Edge
In a highly competitive global market, maintaining a competitive edge is crucial for Japanese manufacturers.
Adopting industrial robots helps streamline operations, reduce production costs, and enhance the ability to respond to market demands quickly.
Advantages of Implementing Industrial Robots in Manufacturing
The deployment of industrial robots offers numerous benefits that appeal to manufacturers seeking to advance their operations and competitiveness.
Improved Quality and Consistency
Robots ensure high-quality output by performing tasks with consistency and precision.
This reduces variability in products and enhances customer satisfaction.
Increased Efficiency and Cost Reduction
Automation leads to faster production cycles and significant reductions in manufacturing costs.
Robots can work long hours without fatigue, increasing utilization rates and enabling companies to optimize resource allocation.
Enhanced Safety
Automating hazardous tasks such as handling dangerous materials or working in extreme environments reduces the risks associated with workplace accidents and injuries.
This leads to safer working conditions for employees.
Flexibility and Scalability
Industrial robots can be reprogrammed and reconfigured to handle new tasks, making them versatile across various production lines.
This flexibility allows manufacturers to scale operations in response to changes in consumer demands and market conditions.
Challenges and Disadvantages of Industrial Robot Integration
While the benefits are significant, integrating industrial robots into manufacturing is not without its challenges.
These need careful consideration to maximize the effectiveness of automation.
High Initial Costs
The investment required for purchasing and installing industrial robots can be substantial.
This may pose financial challenges for smaller companies that lack the capital to adopt such advanced technologies.
Complexity and Technical Expertise
Operating and maintaining industrial robots require specific technical skills and knowledge.
Companies must invest in training or hire skilled personnel to ensure effective management of robotic systems.
Potential Job Displacement
The adoption of automation can lead to concerns about job displacement.
Organizations need to manage workforce transformations and ensure that employees have opportunities for skill development in areas less susceptible to automation.
Integration with Existing Systems
Seamlessly integrating robots with legacy systems remains a challenge.
Ensuring that new robotic solutions work in harmony with existing processes involves careful planning and execution.
Best Practices for Successful Industrial Robot Integration
To successfully integrate industrial robots into manufacturing processes, companies must leverage best practices that ensure smooth transitions and maximize the benefits of automation.
Comprehensive Needs Assessment
Conducting a thorough needs assessment helps identify specific areas where automation can bring the most value.
Analyzing current processes and pinpointing inefficiencies will guide strategic robot deployment.
Clear Objectives and Metrics
Establishing clear objectives and performance metrics enables companies to measure the success of robotic integration.
Goals should focus on productivity, quality improvements, cost savings, and return on investment.
Collaboration with Suppliers
Building strong relationships with suppliers of industrial robots can lead to customized solutions tailored to specific manufacturing needs.
Effective collaboration enhances support services and ensures rapid response to maintenance issues.
Focus on Employee Training
Training programs should equip employees with the necessary skills to program, operate, and maintain robots efficiently.
Empowering workers with knowledge will facilitate smoother transitions and encourage acceptance of automation.
Regular Review and Optimization
Continuous monitoring and analysis of robot performance allow companies to optimize processes over time.
Adjustments and improvements should be made based on data-driven insights to achieve desired outcomes.
Supplier Negotiation Techniques for Procuring Industrial Robots
Negotiating with suppliers is a critical aspect of procuring industrial robots.
Effective negotiation ensures favorable terms, cost savings, and strong partnerships.
Research and Compare
Conduct comprehensive research to understand the offerings of different suppliers.
Comparing features, technology, support, and pricing will inform better negotiation strategies.
Leverage Volume and Value
Demonstrating purchasing power through bulk orders or long-term partnerships can lead to more favorable pricing.
Negotiating value-added services like maintenance or training as part of the contract enhances the overall deal.
Emphasize Quality and Flexibility
Highlighting the importance of quality and flexibility in supplier agreements ensures that robots meet production standards and can be adapted to evolving requirements.
Consider Long-Term Relationships
Cultivating long-term relationships with suppliers promotes collaboration and trust, leading to more favorable terms over time.
Aim for mutually beneficial agreements that align with strategic business objectives.
Market Conditions and Trends Influencing Industrial Robots
The market landscape for industrial robots is dynamic, shaped by emerging trends and evolving technologies.
Understanding these conditions helps companies navigate future challenges and opportunities.
Technological Advancements
Rapid advancements in robotics, artificial intelligence, and machine learning continually enhance robot capabilities.
Companies must stay informed of technological developments to remain competitive.
Demographic and Economic Factors
Labor demographics and economic conditions significantly impact demand for industrial robots.
The need to address labor shortages and reduce operational costs drives automation adoption.
Environmental and Sustainability Concerns
Robotic automation contributes to energy-efficient production processes, aligning with sustainability goals.
Adopting green technologies paves the way for eco-friendly manufacturing practices.
Regulatory and Legislative Considerations
Adhering to safety regulations, industry standards, and legislation is crucial.
Staying informed of regulatory changes ensures compliance and minimizes operational risks.
Conclusion: The Future of Industrial Robots in Japanese Manufacturing
The integration of industrial robots in Japanese manufacturing represents a transformative force that enhances efficiency, precision, and competitiveness.
As the industry continues to evolve, it will be crucial for companies to address the challenges and maximize the opportunities presented by this technology.
By embracing best practices, negotiating effectively with suppliers, and keeping abreast of market trends, Japanese manufacturers can harness the full potential of industrial robots.
These efforts will ensure that Japan maintains its leadership as a global manufacturing powerhouse in the era of automated production.
資料ダウンロード
QCD調達購買管理クラウド「newji」は、調達購買部門で必要なQCD管理全てを備えた、現場特化型兼クラウド型の今世紀最高の購買管理システムとなります。
ユーザー登録
調達購買業務の効率化だけでなく、システムを導入することで、コスト削減や製品・資材のステータス可視化のほか、属人化していた購買情報の共有化による内部不正防止や統制にも役立ちます。
NEWJI DX
製造業に特化したデジタルトランスフォーメーション(DX)の実現を目指す請負開発型のコンサルティングサービスです。AI、iPaaS、および先端の技術を駆使して、製造プロセスの効率化、業務効率化、チームワーク強化、コスト削減、品質向上を実現します。このサービスは、製造業の課題を深く理解し、それに対する最適なデジタルソリューションを提供することで、企業が持続的な成長とイノベーションを達成できるようサポートします。
オンライン講座
製造業、主に購買・調達部門にお勤めの方々に向けた情報を配信しております。
新任の方やベテランの方、管理職を対象とした幅広いコンテンツをご用意しております。
お問い合わせ
コストダウンが利益に直結する術だと理解していても、なかなか前に進めることができない状況。そんな時は、newjiのコストダウン自動化機能で大きく利益貢献しよう!
(Β版非公開)