- お役立ち記事
- Revolutionizing Japanese Manufacturing: How Maintenance IoT is Creating Smart Factories of the Future
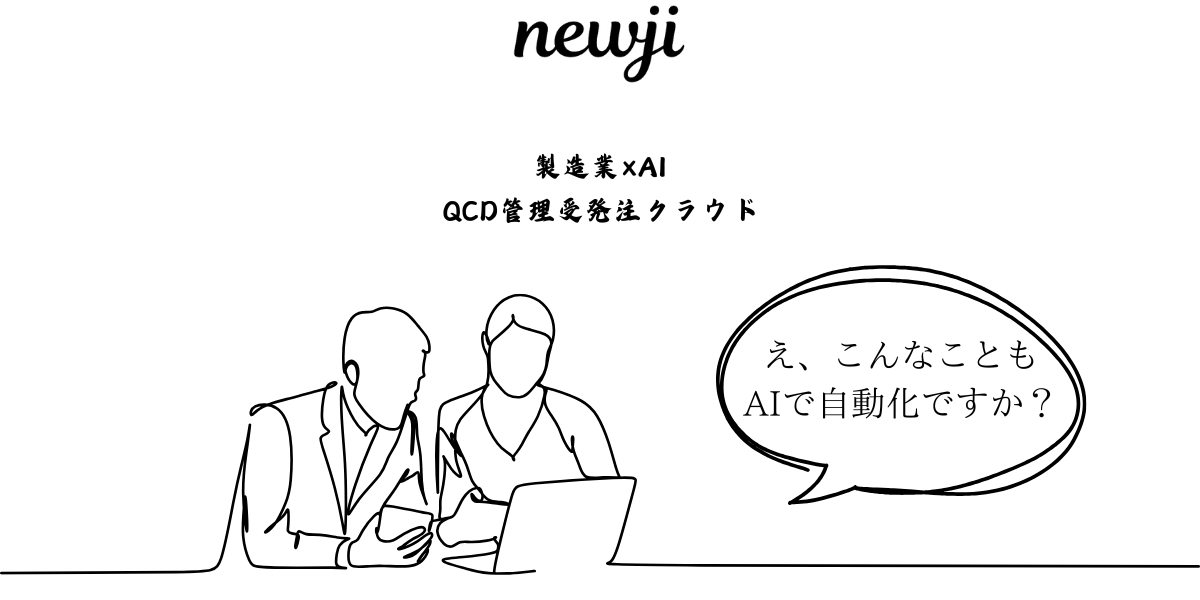
Revolutionizing Japanese Manufacturing: How Maintenance IoT is Creating Smart Factories of the Future
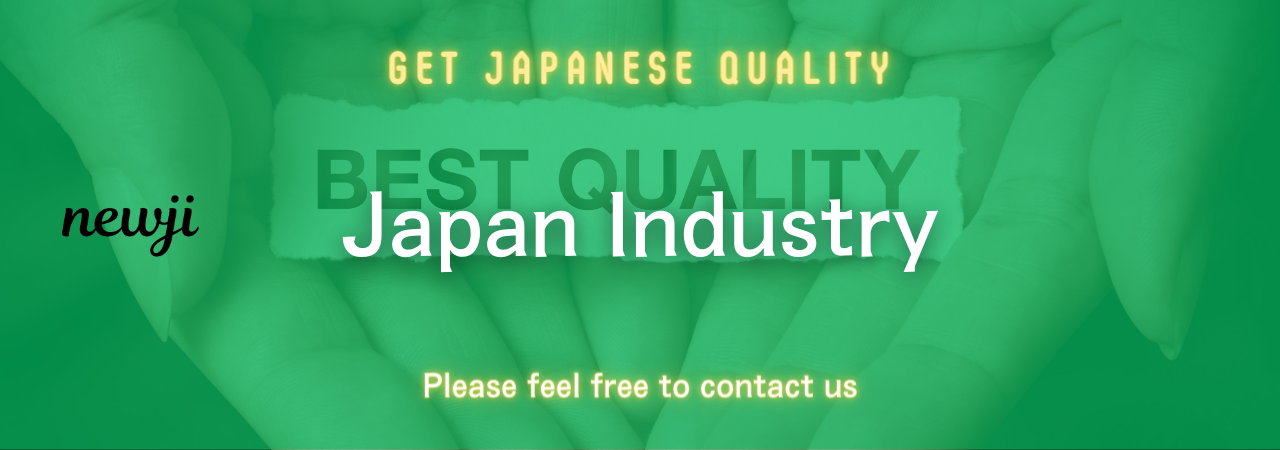
目次
Introduction
The landscape of manufacturing is undergoing a seismic shift, driven by innovations in technology and digital transformation.
One such game-changing innovation is the rise of Maintenance IoT (Internet of Things), which is steadily revolutionizing Japanese manufacturing.
These smart factories of the future are leveraging IoT for predictive maintenance, real-time monitoring, and optimized production processes.
In this article, we delve into the intricacies of Maintenance IoT, exploring its advantages, disadvantages, and practical applications, specifically in the context of Japanese manufacturing.
The Evolution of Maintenance Practices in Japanese Manufacturing
Traditionally, Japanese manufacturing has been celebrated for its rigorous quality control, efficient production processes, and focus on continuous improvement, often exemplified by methodologies like Kaizen and Just-in-Time (JIT) production.
For decades, maintenance in Japanese factories relied on preventative and reactive strategies, where regular inspections and fixes were scheduled or performed as-needed after a breakdown.
However, the advent of IoT has introduced a paradigm shift from these traditional practices to a more predictive and proactive approach.
By embedding IoT sensors and devices into manufacturing equipment, factories can now gather vast amounts of real-time data, which can be analyzed to predict equipment failures before they occur, ensuring minimal downtime and enhanced productivity.
Advantages of Maintenance IoT in Manufacturing
Reduced Downtime
One of the most significant benefits of Maintenance IoT is the drastic reduction in machine downtime.
IoT-enabled sensors continuously monitor the health of machinery, allowing for the prediction of potential failures.
By addressing issues before they lead to breakdowns, manufacturers mitigate the risk of costly production halts.
Enhanced Productivity
With minimized machine downtime, production lines can operate more smoothly and efficiently.
Maintenance IoT allows for planned interventions rather than unexpected disruptions, facilitating a more consistent production flow, leading to higher output and productivity.
Cost Savings
Predictive maintenance reduces the need for frequent, often unnecessary, preventive maintenance.
By focusing on precise interventions, manufacturers save on labor and material costs.
The ROI from IoT investments can be substantial when considering the reduction in avoided breakdowns and extended equipment lifespan.
Data-Driven Decision Making
The integration of IoT devices provides an abundance of data that can be analyzed to make informed decisions.
Manufacturers can identify trends and patterns, optimize operational processes, predict demand, and even innovate production techniques based on data insights.
Improved Safety
IoT devices can also enhance workplace safety.
By continuously monitoring equipment and predicting failures, the risk of sudden malfunctions that could endanger employees is significantly reduced.
In addition, environmental sensors can monitor for hazardous conditions and alert workers before accidents occur.
Challenges and Disadvantages of Implementing Maintenance IoT
High Initial Investment
The deployment of IoT technology requires a significant upfront investment.
Purchasing sensors, upgrading legacy equipment, integrating multiple systems, and training staff can be costly.
However, these costs need to be weighed against the long-term savings and efficiency gains.
Data Security and Privacy
The more connected the factory, the higher the vulnerability to cyber-attacks.
Manufacturers must invest in robust cybersecurity measures to protect sensitive information and avoid disruptions caused by potential breaches.
Integration with Legacy Systems
Many Japanese factories still operate with legacy systems that are not inherently compatible with modern IoT technology.
The integration process can be technologically challenging and require significant time and resources.
In some cases, a full overhaul of existing systems may be necessary, further driving up initial costs.
Skilled Workforce Requirement
Implementing and maintaining IoT systems requires a skilled workforce proficient in both manufacturing and IT.
There can be a learning curve, and hiring or upskilling employees to handle these new technologies may present challenges.
Best Practices for Implementing Maintenance IoT in Japanese Factories
Strategic Planning
Any IoT implementation should start with a well-thought-out strategic plan.
Identify the specific needs and pain points within your manufacturing processes that IoT can address.
Create a roadmap for deployment, considering budget, timeline, and scalable solutions for future expansion.
Pilot Projects
Before a full-scale rollout, conduct pilot projects to gauge the effectiveness of IoT solutions in your specific context.
This allows for the identification of potential issues and the adjustment of strategies without significant risk.
Partnership with Technology Providers
Collaborate with reliable IoT technology providers who understand the unique demands of manufacturing.
These partnerships can provide critical support in the stages of planning, implementation, and ongoing management of IoT systems.
Employee Training
Invest in comprehensive training programs for employees to ensure they are competent in managing and troubleshooting IoT systems.
Continuous professional development can help keep your workforce adept at utilizing evolving technologies.
Maintain Robust Cybersecurity Protocols
Integrate cybersecurity measures as a fundamental component of your IoT strategy.
Regularly update security protocols, conduct audits, and train employees on cybersecurity best practices to protect your data and systems.
Supplier Negotiation Techniques in the Era of Maintenance IoT
Understanding Supplier Capabilities
When procuring IoT solutions for maintenance, it’s imperative to thoroughly understand the capabilities of your suppliers.
Assess their technological offerings, track record, and how well their solutions integrate with your existing systems.
Collaborative Approach
Adopt a collaborative approach in negotiations.
Engage suppliers as partners who can provide ongoing support and innovation rather than merely sellers.
This partnership can lead to better customized solutions that align with your manufacturing needs.
Cost-Benefit Analysis
Conduct a thorough cost-benefit analysis during negotiations.
Evaluate both the upfront and long-term costs of implementing IoT solutions against the potential savings and productivity gains to justify investments.
Performance Guarantees
Ensure performance guarantees are part of the contract.
Agree on Service Level Agreements (SLAs) and performance metrics that suppliers must adhere to after the deployment of IoT systems.
This provides assurances of reliability and effectiveness.
Use Case: Toyota’s Smart Factory Transformation
One of the most compelling examples of successful Maintenance IoT implementation in Japan is Toyota’s smart factory transformation.
Toyota has long been an industry leader in manufacturing excellence, and its embrace of IoT further cements this position.
By integrating IoT sensors across its production lines, Toyota has achieved near-zero downtimes.
Real-time data collected from the machinery is analyzed to predict failures, enabling preemptive maintenance actions.
This proactive approach has led to significant cost savings and increased production efficiency.
Moreover, Toyota’s use of IoT extends to supply chain management, where real-time tracking of parts and materials results in a highly synchronized production environment.
Toyota’s example highlights the substantial benefits of IoT implementation, with improved uptime, reduced maintenance costs, and enhanced overall productivity.
The Future Outlook of Maintenance IoT in Japanese Manufacturing
The adoption of Maintenance IoT in Japanese manufacturing is poised to accelerate.
As IoT technology continues to evolve, smarter and more efficient devices and systems are anticipated.
The integration of AI and machine learning with IoT can take predictive maintenance to new heights, providing deeper insights and automated decision-making capabilities.
Further, the concept of Industry 4.0, centered around smart factories, is increasingly becoming a focal point for Japanese manufacturers.
The synergy between Maintenance IoT and other Industry 4.0 technologies, such as robotics, big data, and cloud computing, will drive the next generation of efficient, resilient, and innovative manufacturing.
Conclusion
The revolutionary impact of Maintenance IoT on Japanese manufacturing cannot be overstated.
From predictive maintenance and enhanced productivity to cost savings and safety improvements, the advantages are compelling.
Yet, these benefits come with challenges such as high initial investments, integration complexities, and data security concerns.
With strategic planning, strong partnerships, and a commitment to continuous improvement, these challenges can be effectively managed.
By following best practices and learning from industry leaders like Toyota, manufacturers can successfully navigate the IoT landscape.
As we look to the future, the continued evolution of IoT and its integration with other advanced technologies promises even greater transformations.
For Japanese manufacturing, embracing Maintenance IoT is not just an option; it is the pathway to creating the smart factories of the future.
資料ダウンロード
QCD調達購買管理クラウド「newji」は、調達購買部門で必要なQCD管理全てを備えた、現場特化型兼クラウド型の今世紀最高の購買管理システムとなります。
ユーザー登録
調達購買業務の効率化だけでなく、システムを導入することで、コスト削減や製品・資材のステータス可視化のほか、属人化していた購買情報の共有化による内部不正防止や統制にも役立ちます。
NEWJI DX
製造業に特化したデジタルトランスフォーメーション(DX)の実現を目指す請負開発型のコンサルティングサービスです。AI、iPaaS、および先端の技術を駆使して、製造プロセスの効率化、業務効率化、チームワーク強化、コスト削減、品質向上を実現します。このサービスは、製造業の課題を深く理解し、それに対する最適なデジタルソリューションを提供することで、企業が持続的な成長とイノベーションを達成できるようサポートします。
オンライン講座
製造業、主に購買・調達部門にお勤めの方々に向けた情報を配信しております。
新任の方やベテランの方、管理職を対象とした幅広いコンテンツをご用意しております。
お問い合わせ
コストダウンが利益に直結する術だと理解していても、なかなか前に進めることができない状況。そんな時は、newjiのコストダウン自動化機能で大きく利益貢献しよう!
(Β版非公開)