- お役立ち記事
- Revolutionizing Japanese Manufacturing: How Productivity Improvement Consulting Can Boost Efficiency and Innovation
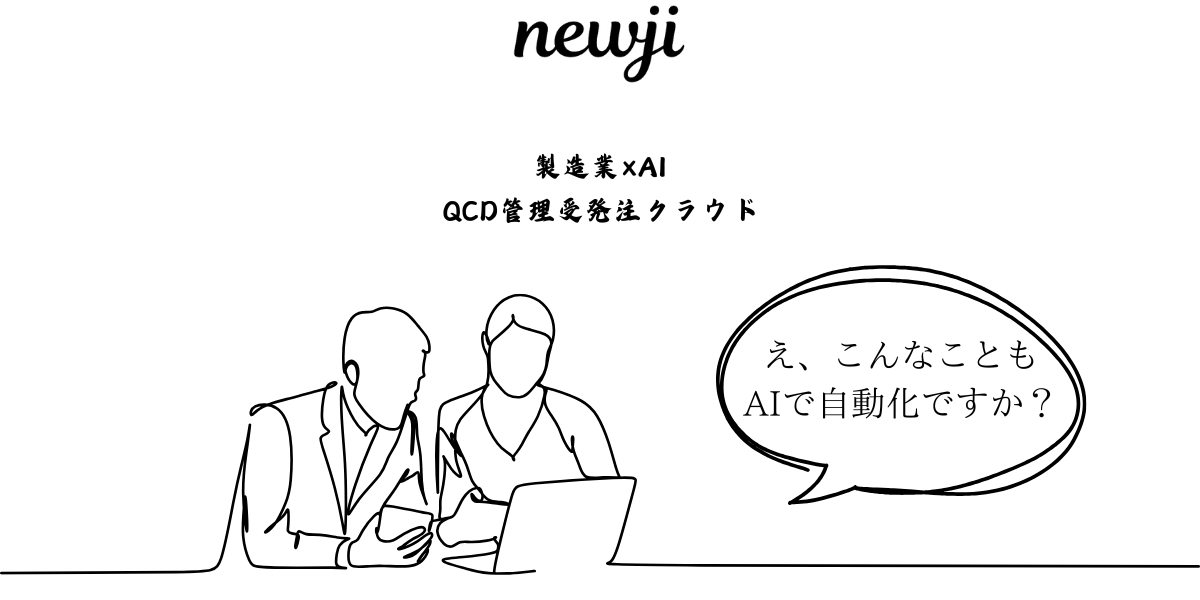
Revolutionizing Japanese Manufacturing: How Productivity Improvement Consulting Can Boost Efficiency and Innovation
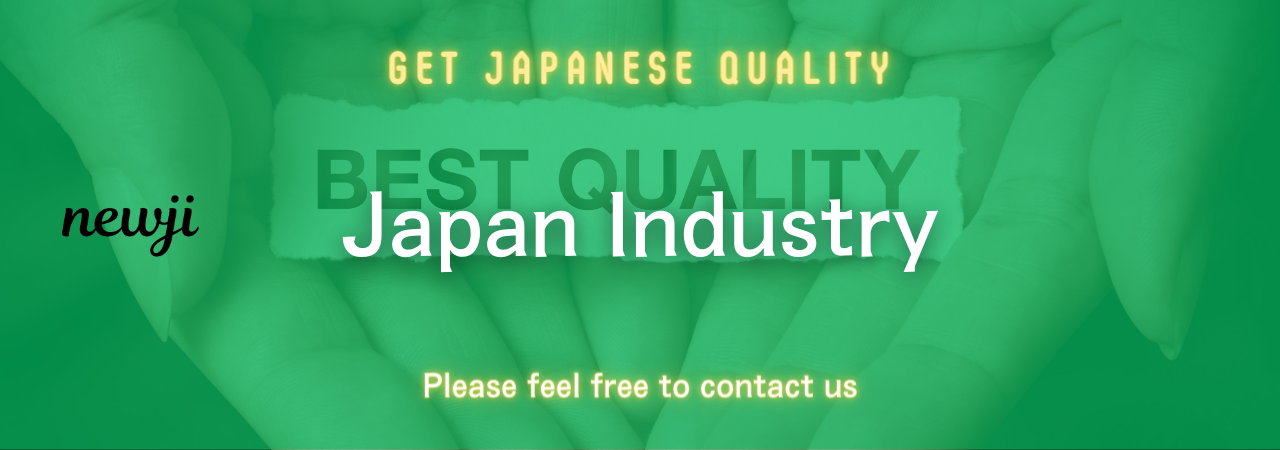
目次
Introduction
In the rapidly evolving landscape of global manufacturing, the importance of productivity improvement cannot be overstated.
The adoption of productivity improvement consulting in Japanese manufacturing has shown tremendous potential to elevate efficiency and foster innovation.
Leveraging extensive experience in procurement, trade practices, logistics, and production management, this article delves into how Japanese manufacturing can benefit from productivity improvement consulting.
The State of Japanese Manufacturing
Strengths of Japanese Manufacturing
Japanese manufacturing has long been renowned for its exceptional quality and reliability.
Companies like Toyota and Panasonic have set global benchmarks in terms of precision, innovation, and efficiency.
The industry is characterized by stringent quality control measures, a culture of continuous improvement (Kaizen), and robust supplier relationships.
Challenges Facing Japanese Manufacturing
Despite its strengths, Japanese manufacturing faces several challenges.
Global competition has intensified, with countries like China and South Korea emerging as formidable competitors.
Aging infrastructure, a rapidly aging workforce, and rigid traditional practices have also posed significant difficulties.
Moreover, adapting to new technologies such as AI and IoT can be slow due to existing legacy systems.
What is Productivity Improvement Consulting?
Productivity improvement consulting involves analyzing and optimizing various aspects of the production process to increase efficiency, reduce costs, and enhance product quality.
Consultants employ a plethora of methodologies including lean manufacturing, Six Sigma, and the Theory of Constraints, among others.
Lean Manufacturing
Lean manufacturing, a methodology that originated in Japan, focuses on minimizing waste and maximizing value.
The core principles include identifying value streams, creating continuous workflows, and fostering a culture of continuous improvement.
Six Sigma
Six Sigma employs statistical methods to identify and eliminate defects in manufacturing processes.
It aims for near-perfection in quality and is usually integrated with lean principles to create a lean Six Sigma approach.
Theory of Constraints
The Theory of Constraints identifies the most limiting factor (constraint) in a manufacturing system and systematically improves it.
This methodology ensures that the entire system benefits from incremental optimizations.
Advantages of Implementing Productivity Improvement Consulting
Increased Efficiency and Reduced Costs
One of the most immediate benefits of productivity improvement consulting is the enhanced efficiency of manufacturing processes.
Optimized workflows and reduced waste result in significant cost savings.
Consultants often identify bottlenecks and streamline operations to facilitate smoother production cycles.
Enhanced Product Quality
Adopting productivity improvement measures can also lead to substantial improvements in product quality.
The emphasis on precision and defect reduction ensures that the end products meet stringent quality standards.
This directly translates into higher customer satisfaction and fewer returns or complaints.
Fostering Innovation
Productivity improvement consulting isn’t solely about refining existing processes.
It also opens avenues for innovation.
By adopting modern methodologies and technologies, companies can develop new products faster and more efficiently.
This gives them a competitive edge in the market.
Building a Culture of Continuous Improvement
One of the key tenets of productivity improvement is the establishment of a culture of continuous improvement.
Employees are encouraged to identify and solve problems proactively.
This not only improves processes but also fosters a more engaged and motivated workforce.
Challenges in Implementing Productivity Improvement Consulting
Resistance to Change
One of the primary challenges in implementing productivity improvement consulting is resistance to change.
Employees accustomed to traditional manufacturing methods may be hesitant to adopt new processes.
Effective change management and clear communication are essential to overcoming this obstacle.
Initial Investment Costs
While the long-term benefits are considerable, there are initial investment costs associated with hiring consultants and implementing new methodologies.
Small to medium-sized enterprises (SMEs) may find these costs prohibitive and may require financial assistance or phased implementation plans.
Time-Consuming Implementation
Productivity improvement consulting is not a quick fix.
Implementing new processes can be time-consuming and may require substantial training for employees.
This might temporarily disrupt production cycles, requiring careful planning and scheduling.
Best Practices for Effective Productivity Improvement Consulting
Conducting Comprehensive Assessments
One of the first steps in productivity improvement is conducting a thorough assessment of the existing production processes.
Consultants typically analyze various aspects, such as workflow efficiency, quality control measures, and supply chain dynamics.
An in-depth assessment helps identify key areas that require improvement.
Customized Solutions
Every manufacturing entity is unique, and a one-size-fits-all approach is rarely effective.
Customized solutions that are tailored to the specific needs and challenges of the organization tend to yield the best results.
Consultants must work closely with internal teams to develop bespoke strategies.
Engaging All Stakeholders
Effective productivity improvement requires the engagement of all stakeholders, including management, employees, and suppliers.
A collaborative approach ensures that everyone is invested in the improvement process and is more likely to embrace changes.
Continuous Monitoring and Improvement
Productivity improvement is not a one-time effort.
Continuous monitoring and incremental improvements are crucial for sustained benefits.
Key performance indicators (KPIs) should be established to measure progress and identify areas for further enhancement.
Supplier Negotiation Techniques
Building Strong Supplier Relationships
In Japanese manufacturing, strong supplier relationships are paramount.
Long-term partnerships based on mutual trust and respect lead to better negotiation outcomes.
Open communication channels ensure that both parties are aligned on goals and expectations.
Leveraging Data Analytics
Data analytics can play a crucial role in supplier negotiations.
Detailed data on supplier performance, market conditions, and cost structures can provide valuable insights that enhance negotiation strategies.
Predictive analytics can also forecast market trends and help in making informed decisions.
Emphasizing Total Cost of Ownership
When negotiating with suppliers, it’s essential to consider the total cost of ownership (TCO) rather than just the initial purchase price.
TCO includes factors such as quality, reliability, logistics, and after-sales support.
This holistic approach often results in more favorable terms and long-term savings.
Market Conditions and Their Impact
Global Competition
The global manufacturing landscape is highly competitive, with emerging markets offering lower production costs.
Japanese manufacturers must continually innovate and improve productivity to stay competitive.
Productivity improvement consulting can provide the necessary edge to compete effectively on a global scale.
Technological Advancements
The rapid pace of technological advancements presents both opportunities and challenges.
Adopting new technologies can significantly enhance productivity, but it also requires substantial investment and a willingness to change.
Productivity improvement consulting can help navigate these complexities and maximize technological benefits.
Economic Factors
Economic conditions, such as currency fluctuations and trade policies, can impact manufacturing operations.
Productivity improvement consulting can mitigate these risks by optimizing costs and enhancing operational efficiency.
A more efficient operation is better equipped to weather economic uncertainties.
Conclusion
Productivity improvement consulting offers an invaluable opportunity for Japanese manufacturing companies to enhance efficiency, reduce costs, and foster innovation.
While the implementation may present challenges, the long-term benefits far outweigh the initial hurdles.
By adopting best practices and leveraging advanced methodologies, Japanese manufacturers can maintain their global leadership and continue to set industry benchmarks.
In the ever-changing landscape of global manufacturing, the ability to adapt and continuously improve is paramount.
Productivity improvement consulting provides the tools and strategies necessary to achieve sustained success.
By embracing these practices, Japanese manufacturers can not only enhance their own operations but also contribute to the advancement of the industry as a whole.
The insights and practical knowledge gained from working closely with Japanese suppliers can be harnessed to drive significant improvements.
By building strong relationships, employing effective negotiation techniques, and staying abreast of market conditions, procurement and purchasing departments can play a pivotal role in revolutionizing Japanese manufacturing.
資料ダウンロード
QCD調達購買管理クラウド「newji」は、調達購買部門で必要なQCD管理全てを備えた、現場特化型兼クラウド型の今世紀最高の購買管理システムとなります。
ユーザー登録
調達購買業務の効率化だけでなく、システムを導入することで、コスト削減や製品・資材のステータス可視化のほか、属人化していた購買情報の共有化による内部不正防止や統制にも役立ちます。
NEWJI DX
製造業に特化したデジタルトランスフォーメーション(DX)の実現を目指す請負開発型のコンサルティングサービスです。AI、iPaaS、および先端の技術を駆使して、製造プロセスの効率化、業務効率化、チームワーク強化、コスト削減、品質向上を実現します。このサービスは、製造業の課題を深く理解し、それに対する最適なデジタルソリューションを提供することで、企業が持続的な成長とイノベーションを達成できるようサポートします。
オンライン講座
製造業、主に購買・調達部門にお勤めの方々に向けた情報を配信しております。
新任の方やベテランの方、管理職を対象とした幅広いコンテンツをご用意しております。
お問い合わせ
コストダウンが利益に直結する術だと理解していても、なかなか前に進めることができない状況。そんな時は、newjiのコストダウン自動化機能で大きく利益貢献しよう!
(Β版非公開)