- お役立ち記事
- Revolutionizing Japanese Manufacturing: How Robotics Applications Are Shaping the Future
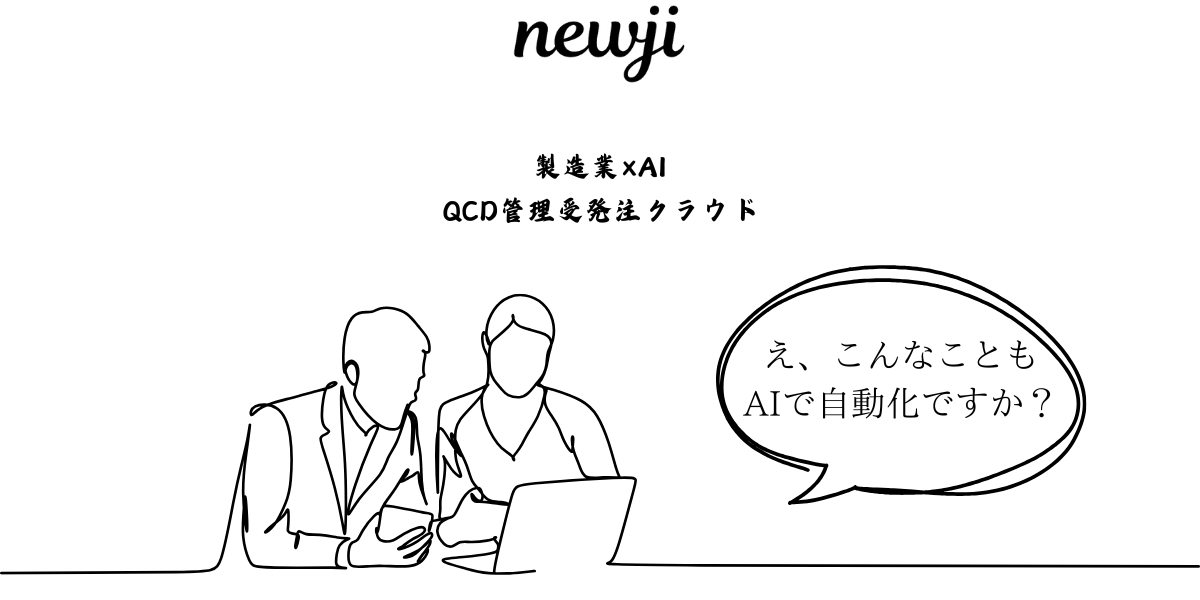
Revolutionizing Japanese Manufacturing: How Robotics Applications Are Shaping the Future
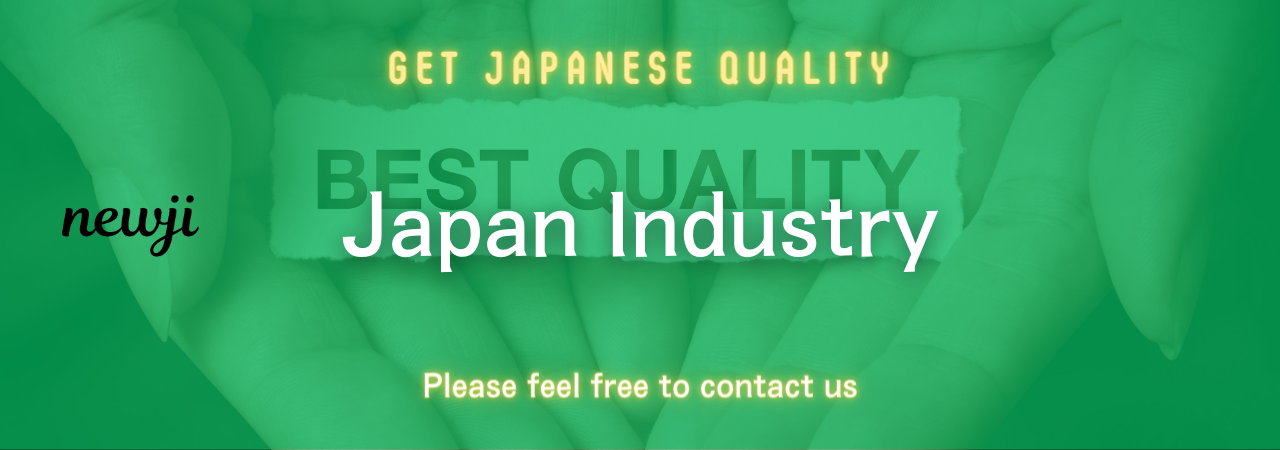
目次
Introduction to Robotics in Japanese Manufacturing
Japanese manufacturing has long been synonymous with innovation, precision, and efficiency. In recent years, the integration of robotics has further propelled this reputation, revolutionizing production processes and setting new standards in various industries. Robotics applications in Japanese manufacturing are not only enhancing productivity but also ensuring higher quality standards, reducing costs, and fostering sustainable practices. This article delves into how robotics is shaping the future of Japanese manufacturing, exploring its advantages, challenges, negotiation techniques with suppliers, market conditions, and best practices.
The Rise of Robotics in Japanese Manufacturing
Historical Context and Evolution
Japan’s commitment to technological advancement has its roots in the post-World War II era, where the country focused on rebuilding its economy through industrial growth. Robotics emerged as a key component in this strategy, with early applications in automotive and electronics manufacturing. Over the decades, Japanese companies like Toyota, Honda, and FANUC have become global leaders in robotics, continuously innovating to improve efficiency and precision.
Current Landscape
Today, robotics in Japanese manufacturing spans various sectors including automotive, electronics, pharmaceuticals, and consumer goods. The adoption rate is high, driven by the need to address labor shortages, enhance quality control, and maintain competitiveness in a global market. Advanced robotics systems are now integral to assembly lines, material handling, quality inspection, and even in roles that require complex decision-making and adaptability.
Advantages of Robotics Applications in Manufacturing
Increased Efficiency and Productivity
Robotic systems operate with high precision and consistency, significantly boosting production rates. They can work around the clock without fatigue, leading to continuous production cycles and higher output. This efficiency is crucial for meeting the demands of global markets and reducing lead times.
Enhanced Quality Control
Robots minimize human error, ensuring that products meet stringent quality standards. Advanced sensors and AI-driven systems enable real-time monitoring and adjustments, leading to higher accuracy and fewer defects. This consistency is vital for maintaining the reputation of Japanese manufacturing for excellence.
Cost Reduction
While the initial investment in robotics can be substantial, the long-term cost savings are significant. Robots reduce labor costs, minimize waste, and lower the expenses associated with errors and rework. Additionally, automation can lead to more efficient use of materials and energy, further driving down costs.
Safety and Workplace Improvement
Robots take over hazardous tasks, reducing the risk of workplace injuries and improving overall safety. This shift not only protects workers but also enhances morale and job satisfaction, as employees can focus on more skilled and less physically demanding roles.
Flexibility and Scalability
Modern robotics systems are highly adaptable, capable of performing a variety of tasks with minimal reprogramming. This flexibility allows manufacturers to quickly switch production lines to accommodate different products or respond to market changes. Scalability ensures that businesses can expand their operations without significant overhauls to their existing systems.
Challenges and Disadvantages
High Initial Investment
The cost of acquiring and implementing robotic systems can be a barrier, especially for small and medium-sized enterprises. This includes not only the purchase of robots but also the costs associated with installation, training, and maintenance.
Technical Complexity
Integrating robotics into existing manufacturing processes requires specialized knowledge and expertise. Companies may face challenges in terms of system integration, troubleshooting, and maintaining the complex machinery, necessitating continuous training and support.
Job Displacement Concerns
The automation of tasks traditionally performed by humans can lead to job displacement. While robots create new roles in programming, maintenance, and supervision, there is often a transition period where workers need to reskill, which can be challenging for both employees and employers.
Dependence on Technology
Reliance on robotic systems makes manufacturing processes vulnerable to technical failures, cyber-attacks, and software issues. Ensuring robust cybersecurity measures and having contingency plans are essential to mitigate these risks.
Maintenance and Downtime
Robotic systems require regular maintenance to function optimally. Unplanned downtime due to technical issues can disrupt production schedules and lead to significant losses, highlighting the need for efficient maintenance protocols.
Supplier Negotiation Techniques for Robotics Procurement
Understanding Supplier Capabilities
Before entering negotiations, it is crucial to thoroughly understand the capabilities and limitations of potential suppliers. This includes assessing their technological expertise, production capacity, quality standards, and track record in the industry.
Establishing Clear Requirements
Define precise specifications and requirements for the robotic systems needed. Clear communication ensures that suppliers can provide solutions that meet the specific needs of your manufacturing processes, reducing the risk of misunderstandings and mismatches.
Building Long-Term Relationships
Fostering strong relationships with suppliers can lead to better terms, priority support, and more favorable pricing. Long-term partnerships encourage suppliers to invest in understanding your business, leading to more customized and effective solutions.
Competitive Bidding
Engage in competitive bidding to leverage multiple offers and drive down costs. Presenting clear requirements to multiple suppliers can help in comparing proposals effectively and selecting the best value for your investment.
Negotiating Flexible Terms
Seek flexible payment terms, warranties, and support services. Flexibility in contract terms can provide financial cushioning and ensure that you have adequate support for ongoing maintenance and upgrades.
Emphasizing Quality and Reliability
Prioritize quality and reliability over initial cost savings. Investing in high-quality robotics systems can lead to long-term benefits through reduced downtime, lower maintenance costs, and higher productivity.
Market Conditions and Trends
Technological Advancements
The robotics industry is rapidly evolving, with advancements in artificial intelligence, machine learning, and sensor technologies driving more intelligent and autonomous systems. These innovations enhance the capabilities of robots, enabling them to perform more complex tasks and adapt to changing environments.
Demand for Customization
Manufacturers are increasingly seeking robotic solutions that can be tailored to their specific needs. Customizable robots offer greater flexibility and can integrate seamlessly into unique production lines, making them more attractive to diverse industries.
Global Supply Chain Dynamics
Global supply chain disruptions have highlighted the importance of resilient and adaptable manufacturing processes. Robotics can enhance supply chain flexibility by enabling quicker adjustments to production schedules and reducing dependence on manual labor.
Sustainability and Green Manufacturing
There is a growing emphasis on sustainable manufacturing practices. Robots can contribute by optimizing resource usage, reducing waste, and improving energy efficiency, aligning with environmental goals and regulatory requirements.
Labor Market Trends
A declining labor force and aging workforce in Japan are driving the adoption of robotics to fill labor gaps. Robots provide a solution to maintain production levels and meet market demands despite workforce challenges.
Cost Reduction Pressures
Global competition puts pressure on manufacturers to reduce costs while maintaining high quality. Robotics offers a pathway to achieve cost efficiencies through automation, waste reduction, and improved operational effectiveness.
Best Practices for Implementing Robotics in Manufacturing
Thorough Needs Assessment
Conduct a comprehensive analysis of your manufacturing processes to identify areas where robotics can add value. Assess the potential impact on productivity, quality, and cost, and prioritize applications that offer the greatest benefits.
Strategic Planning
Develop a clear implementation strategy that outlines goals, timelines, budgets, and key performance indicators (KPIs). Strategic planning ensures that the integration of robotics aligns with overall business objectives and supports long-term growth.
Employee Training and Engagement
Invest in training programs to equip employees with the necessary skills to operate, maintain, and collaborate with robotic systems. Engaging employees in the transition process fosters a culture of continuous improvement and innovation.
Collaborative Integration
Ensure that robotic systems are seamlessly integrated into existing workflows and infrastructure. Collaboration between different departments, such as IT, engineering, and operations, is essential for a smooth implementation process.
Continuous Monitoring and Optimization
Implement monitoring systems to track the performance of robotic applications and identify areas for improvement. Continuous optimization ensures that the systems remain efficient and adapt to evolving manufacturing needs.
Safety and Compliance
Adhere to safety standards and regulatory requirements during the implementation of robotics. Ensuring a safe working environment protects employees and minimizes the risk of accidents and legal issues.
Scalability and Future-Proofing
Choose robotic solutions that are scalable and can adapt to future technological advancements. Future-proofing your investments ensures that your manufacturing processes remain competitive and capable of handling new challenges.
Case Studies: Robotics Transforming Japanese Manufacturing
Automotive Industry
Japanese automotive giants like Toyota and Honda have been pioneers in adopting robotics for assembly line automation. Robots perform tasks such as welding, painting, and assembly with high precision, reducing production time and enhancing vehicle quality. The integration of collaborative robots (cobots) allows for human-robot collaboration, increasing flexibility and efficiency on the factory floor.
Electronics Manufacturing
Companies like Sony and Panasonic utilize robotics in electronics manufacturing to achieve intricate assembly and quality inspection. Robots handle delicate components with care, ensuring high standards and minimizing defects. Automation in electronics manufacturing also enables quicker response to market changes and technological advancements.
Pharmaceutical Production
In the pharmaceutical sector, robotics ensures stringent compliance with safety and quality regulations. Automated systems handle tasks such as packaging, labeling, and quality control, reducing the risk of contamination and errors. Robotics also facilitate the production of high-precision medications, supporting advancements in healthcare.
Consumer Goods Manufacturing
Robotics in consumer goods manufacturing enhances customization and rapid production. Companies like Uniqlo use robotics for tasks like fabric cutting and assembly, enabling efficient production of a wide range of products tailored to consumer preferences. Automation also supports increased production volumes during peak seasons without compromising quality.
Future Outlook
Advancements in Artificial Intelligence
The integration of AI with robotics is set to drive further innovations in manufacturing. Intelligent robots capable of learning and adapting to new tasks will enhance flexibility and efficiency, enabling more complex and dynamic production environments.
Human-Robot Collaboration
The future of manufacturing lies in enhanced human-robot collaboration. Cobots will work alongside humans, combining the strengths of both to achieve higher productivity and creativity. This synergy will lead to more innovative solutions and improved manufacturing processes.
Enhanced Data Analytics
Robotic systems equipped with advanced sensors and connected through the Internet of Things (IoT) will generate vast amounts of data. Leveraging this data through analytics will provide deeper insights into manufacturing processes, enabling predictive maintenance, quality improvements, and optimized production workflows.
Sustainability Initiatives
Robots will play a crucial role in advancing sustainability in manufacturing. Energy-efficient robotic systems, waste reduction through precise operations, and sustainable materials handling will contribute to greener manufacturing practices, aligning with global environmental goals.
Global Competitiveness
As robotics technology continues to evolve, Japanese manufacturers will maintain their competitive edge by adopting cutting-edge solutions. Staying ahead in robotics innovation will ensure that Japanese manufacturing remains a global leader in quality, efficiency, and technological advancements.
Conclusion
Robotics applications are undeniably transforming Japanese manufacturing, driving it towards a future characterized by higher efficiency, superior quality, and sustainable practices. While challenges such as high initial investments and technical complexities exist, the benefits of adopting robotics far outweigh the drawbacks. By implementing best practices, fostering strong supplier relationships, and staying abreast of market trends, Japanese manufacturers can harness the full potential of robotics to maintain their leadership in the global market. As technology continues to advance, the synergy between human expertise and robotic precision will pave the way for even greater innovations, ensuring that Japanese manufacturing remains at the forefront of industrial excellence.
資料ダウンロード
QCD調達購買管理クラウド「newji」は、調達購買部門で必要なQCD管理全てを備えた、現場特化型兼クラウド型の今世紀最高の購買管理システムとなります。
ユーザー登録
調達購買業務の効率化だけでなく、システムを導入することで、コスト削減や製品・資材のステータス可視化のほか、属人化していた購買情報の共有化による内部不正防止や統制にも役立ちます。
NEWJI DX
製造業に特化したデジタルトランスフォーメーション(DX)の実現を目指す請負開発型のコンサルティングサービスです。AI、iPaaS、および先端の技術を駆使して、製造プロセスの効率化、業務効率化、チームワーク強化、コスト削減、品質向上を実現します。このサービスは、製造業の課題を深く理解し、それに対する最適なデジタルソリューションを提供することで、企業が持続的な成長とイノベーションを達成できるようサポートします。
オンライン講座
製造業、主に購買・調達部門にお勤めの方々に向けた情報を配信しております。
新任の方やベテランの方、管理職を対象とした幅広いコンテンツをご用意しております。
お問い合わせ
コストダウンが利益に直結する術だと理解していても、なかなか前に進めることができない状況。そんな時は、newjiのコストダウン自動化機能で大きく利益貢献しよう!
(Β版非公開)