- お役立ち記事
- Revolutionizing Japanese Manufacturing: How the “Dynamo” Powers Innovation and Efficiency
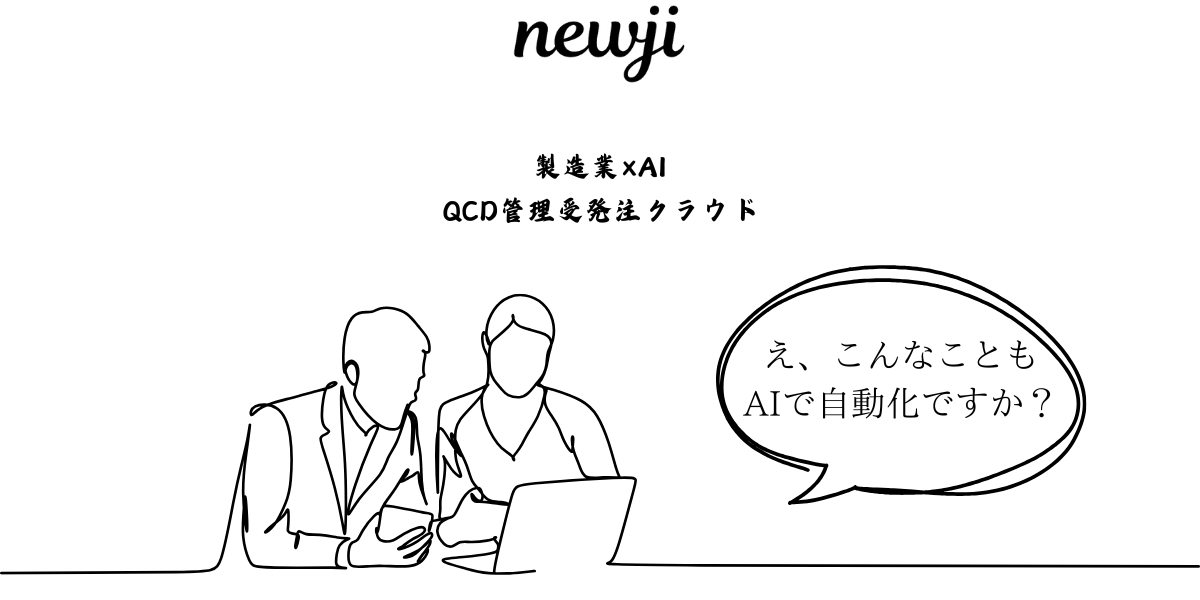
Revolutionizing Japanese Manufacturing: How the “Dynamo” Powers Innovation and Efficiency
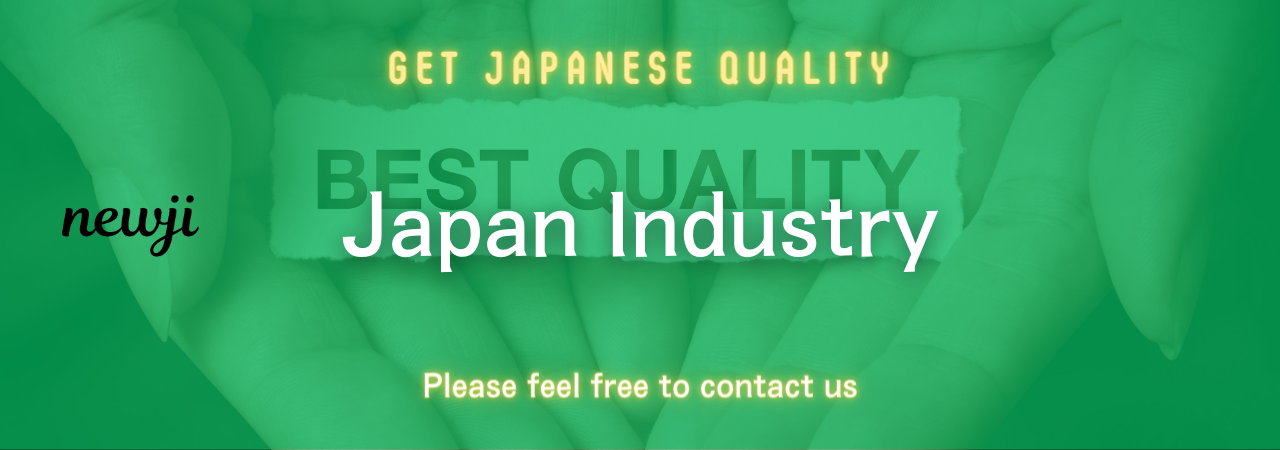
The world of manufacturing is ever-evolving, with new technologies and methodologies constantly pushing the envelope of what is possible. One country that has continually positioned itself at the forefront of this evolution is Japan. Japanese manufacturing is renowned for its precision, efficiency, and innovative approaches. A keystone concept within this ecosystem is the “Dynamo,” which serves as a symbol of power, capability, and relentless drive. In this article, we will explore how the Dynamo powers innovation and efficiency in Japanese manufacturing, delve into the advantages and disadvantages, and share best practices for working effectively with Japanese suppliers.
目次
Understanding the “Dynamo” in Japanese Manufacturing
Japanese manufacturing has ingrained within it a culture of continuous improvement and quality. The term “Dynamo” in this context refers to the collective commitment to manufacturing excellence and innovation. This ethos manifests itself in various forms, from technological advancements to rigorous quality control.
The Spirit of Kaizen
At the heart of the Dynamo is the concept of Kaizen, or continuous improvement. Originating in the post-World War II era, Kaizen emphasizes small, incremental changes that collectively lead to significant enhancements in productivity and quality. Every employee, from the shop floor to senior management, is encouraged to contribute ideas for improvement. This inclusiveness fosters a sense of ownership and responsibility among workers, driving innovation from the ground up.
Jidoka and Automation
Another crucial component of the Dynamo is Jidoka, or “automation with a human touch.” Japanese manufacturers have long recognized that while automation can significantly boost efficiency, human oversight is essential for maintaining quality. Jidoka empowers workers to halt production when a problem is detected, ensuring that defects are caught early and quality is maintained.
Advantages of Japanese Manufacturing Practices
The practices encapsulated by the Dynamo offer several compelling advantages for manufacturers and their global partners. Understanding these benefits can provide valuable insights into why Japan continues to excel in manufacturing.
Superior Quality Control
Japanese manufacturers are renowned for their stringent quality control standards. From raw materials to finished products, every stage of the manufacturing process is monitored meticulously. This rigorous approach minimizes defects, ensuring that end products consistently meet or exceed customer expectations.
Efficiency and Waste Reduction
The emphasis on efficiency and waste reduction is another hallmark of Japanese manufacturing. Lean manufacturing principles, which minimize waste without sacrificing productivity, are widely adopted. Techniques such as Just-in-Time (JIT) production ensure that inventory levels are kept low, reducing holding costs and freeing up resources for other operations.
Innovation and Adaptability
The culture of continuous improvement and employee involvement fosters an environment ripe for innovation. Japanese companies are quick to adapt to new technologies and market demands, maintaining their competitive edge. This adaptability is further enhanced by robust R&D departments and a willingness to invest in new technologies.
Challenges and Disadvantages
While the benefits of Japanese manufacturing are manifold, it is essential to acknowledge the challenges and disadvantages that can arise when working with Japanese suppliers.
Cultural Differences
Understanding and navigating cultural differences can be a significant challenge for international partners. Japanese business culture prioritizes respect, hierarchy, and consensus. Building strong relationships and gaining trust can take time, and misunderstandings may occur if cultural nuances are overlooked.
Long Lead Times
While Japanese manufacturers excel in quality and efficiency, the emphasis on meticulous planning and rigorous quality control can result in longer lead times. For companies that require rapid turnaround times, this can pose a challenge. It is crucial to factor in these lead times when planning procurement and production schedules.
Cost Implications
The high standards of quality and efficiency come at a cost. Products manufactured in Japan may carry a higher price tag compared to those produced in countries with lower labor and production costs. However, it is important to weigh these costs against the potential long-term benefits of superior quality and reliability.
Effective Supplier Negotiation Techniques
Navigating negotiations with Japanese suppliers requires a nuanced approach that takes into account cultural and business practices. Successful negotiation tactics can lead to mutually beneficial agreements and long-term partnerships.
Building Relationships
In Japanese business culture, building strong, trust-based relationships is paramount. Before diving into negotiations, invest time in getting to know your counterparts and establishing rapport. Demonstrating genuine interest in their business and showing respect for their expertise can lay the groundwork for productive negotiations.
Patience and Persistence
Negotiations with Japanese suppliers may take longer than those with counterparts from other cultures. Be patient and persistent, and avoid rushing the process. Japanese negotiators value thorough discussion and consensus-building, so allow ample time for them to review proposals and seek internal approval.
Clarity and Precision
Clear and precise communication is crucial when negotiating with Japanese suppliers. Present your proposals in a structured and detailed manner, outlining specific terms and conditions. Avoid ambiguity and provide as much information as possible to facilitate informed decision-making.
Current Market Conditions in Japanese Manufacturing
Staying abreast of market conditions is essential for effectively navigating the landscape of Japanese manufacturing. Understanding trends and developments can inform procurement strategies and help identify opportunities.
Technological Advancements
Japan continues to be a leader in technological innovation, particularly in fields such as robotics, automation, and materials science. Manufacturers are increasingly adopting Industry 4.0 technologies, such as the Internet of Things (IoT) and artificial intelligence (AI), to enhance productivity and quality.
Supply Chain Resilience
In recent years, Japanese manufacturers have focused on enhancing supply chain resilience in response to global disruptions. Strategies such as diversifying suppliers and increasing transparency have become more prevalent. Companies are also investing in digital solutions to improve supply chain visibility and responsiveness.
Sustainability Initiatives
Sustainability is gaining traction as a key priority for Japanese manufacturers. Companies are implementing eco-friendly practices, such as reducing emissions, minimizing waste, and using renewable energy sources. These initiatives are not only environmentally responsible but also align with global market demands for sustainable products.
Best Practices for Working with Japanese Suppliers
Leveraging the strengths of Japanese manufacturing requires adherence to best practices that foster positive and productive relationships.
Open Communication
Fostering open communication is essential for successful collaboration. Regularly update your Japanese suppliers on your requirements, expectations, and any changes in your supply chain. Encourage them to share insights and feedback, and be responsive to their inquiries.
Quality Assurance
Ensure that quality assurance processes are aligned with Japanese standards. Conduct regular audits and inspections to verify compliance with specifications. Collaborate closely with suppliers to address any issues promptly and implement corrective actions.
Flexibility and Adaptability
Flexibility and adaptability are key to navigating the dynamic landscape of Japanese manufacturing. Be prepared to adjust your strategies and plans in response to market changes, technological advancements, and supplier capabilities. Demonstrating flexibility can strengthen relationships and enhance collaboration.
Recognition and Appreciation
Recognizing and appreciating the efforts of your Japanese suppliers can go a long way in building strong partnerships. Acknowledge their contributions and successes, and express gratitude for their hard work. Celebratory gestures, such as sending tokens of appreciation or hosting joint events, can further cement positive relationships.
Conclusion
The Dynamo of Japanese manufacturing stands as a testament to the power of innovation, efficiency, and relentless pursuit of excellence. By embracing the principles of Kaizen, Jidoka, and lean manufacturing, Japanese companies have set a high standard for the industry.
While there are challenges to navigate, the advantages of superior quality, efficiency, and adaptability make Japanese manufacturing a valuable partner in the global supply chain. By adopting effective negotiation techniques, staying informed about market conditions, and adhering to best practices, companies can unlock the full potential of working with Japanese suppliers.
In doing so, they can leverage the power of the Dynamo to drive their own success and contribute to the ongoing evolution of manufacturing excellence.
資料ダウンロード
QCD調達購買管理クラウド「newji」は、調達購買部門で必要なQCD管理全てを備えた、現場特化型兼クラウド型の今世紀最高の購買管理システムとなります。
ユーザー登録
調達購買業務の効率化だけでなく、システムを導入することで、コスト削減や製品・資材のステータス可視化のほか、属人化していた購買情報の共有化による内部不正防止や統制にも役立ちます。
NEWJI DX
製造業に特化したデジタルトランスフォーメーション(DX)の実現を目指す請負開発型のコンサルティングサービスです。AI、iPaaS、および先端の技術を駆使して、製造プロセスの効率化、業務効率化、チームワーク強化、コスト削減、品質向上を実現します。このサービスは、製造業の課題を深く理解し、それに対する最適なデジタルソリューションを提供することで、企業が持続的な成長とイノベーションを達成できるようサポートします。
オンライン講座
製造業、主に購買・調達部門にお勤めの方々に向けた情報を配信しております。
新任の方やベテランの方、管理職を対象とした幅広いコンテンツをご用意しております。
お問い合わせ
コストダウンが利益に直結する術だと理解していても、なかなか前に進めることができない状況。そんな時は、newjiのコストダウン自動化機能で大きく利益貢献しよう!
(Β版非公開)