- お役立ち記事
- “Revolutionizing Japanese Manufacturing: How Ultrasound Examination Enhances Composite Materials Innovation”
月間77,185名の
製造業ご担当者様が閲覧しています*
*2025年2月28日現在のGoogle Analyticsのデータより
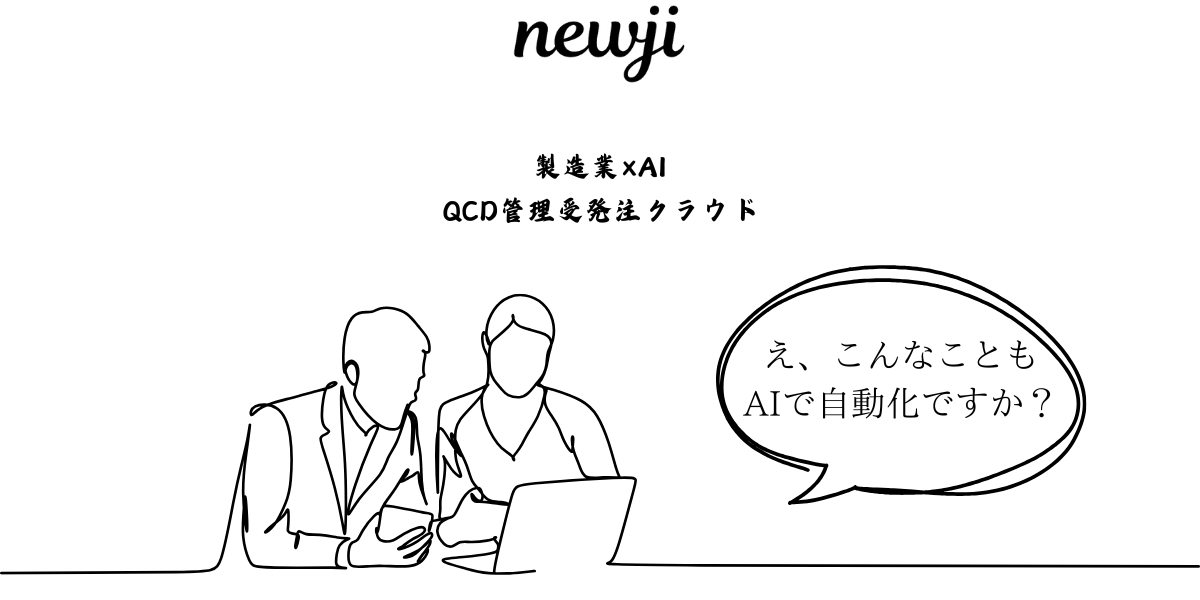
“Revolutionizing Japanese Manufacturing: How Ultrasound Examination Enhances Composite Materials Innovation”
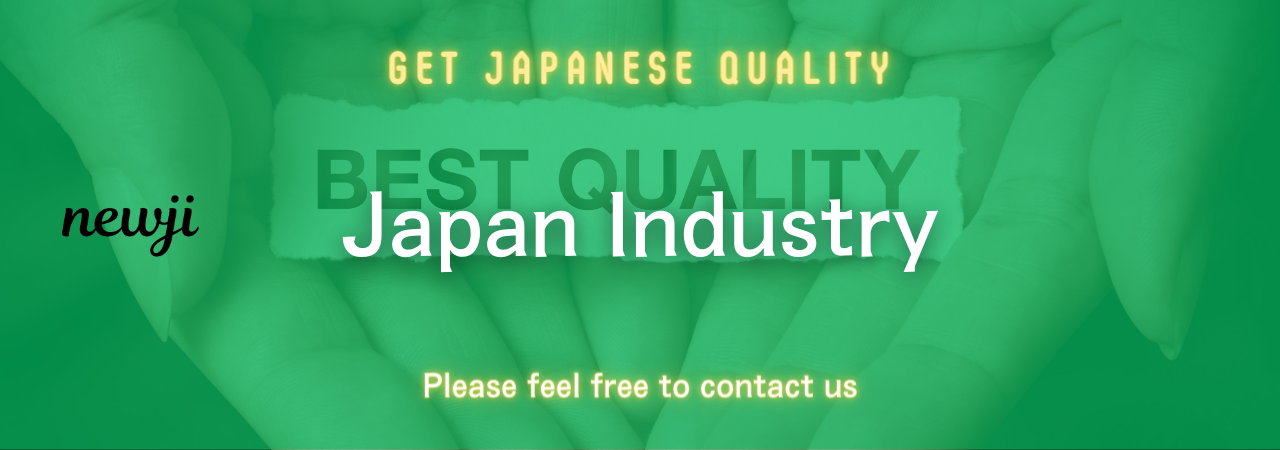
目次
Introduction to Ultrasound Examination in Japanese Manufacturing
Japanese manufacturing has long been synonymous with precision, efficiency, and innovation. Among the latest advancements contributing to this reputation is the integration of ultrasound examination in the development and production of composite materials. This technology not only enhances the quality and reliability of composite products but also streamlines the procurement and purchasing processes, ensuring that manufacturers maintain their competitive edge in the global market.
The Role of Ultrasound Examination in Composite Materials Innovation
Understanding Ultrasound Examination
Ultrasound examination involves the use of high-frequency sound waves to inspect the internal structure of materials without causing damage. In the context of composite materials, this technique is crucial for identifying flaws, assessing material integrity, and ensuring that the composites meet the stringent quality standards required in various industries such as automotive, aerospace, and electronics.
Enhancing Material Integrity
Composite materials, composed of two or more constituent materials with differing physical or chemical properties, offer superior strength-to-weight ratios and corrosion resistance. However, the manufacturing process can introduce defects such as voids, delaminations, and inclusions. Ultrasound examination facilitates the detection of these defects early in the production cycle, allowing manufacturers to address issues promptly and maintain high-quality standards.
Facilitating Continuous Improvement
The insights gained from ultrasound examinations enable manufacturers to implement continuous improvement strategies. By analyzing the types and frequencies of defects, companies can refine their production processes, select better-quality raw materials, and optimize their manufacturing techniques. This proactive approach not only enhances product quality but also reduces waste and operational costs.
Procurement and Purchasing: Leveraging Ultrasound Technology
Supplier Selection and Evaluation
Integrating ultrasound examination into the manufacturing process necessitates a reliable supply of high-quality composite materials. Procurement teams must collaborate closely with suppliers to ensure that raw materials meet specific ultrasound inspection criteria. This involves establishing stringent quality control measures and conducting regular audits to verify supplier compliance with industry standards.
Negotiation Techniques with Japanese Suppliers
Japanese suppliers are renowned for their commitment to quality and precision. Effective negotiation with these suppliers involves clear communication of quality expectations, leveraging long-term partnership benefits, and understanding cultural nuances that influence business interactions. Highlighting the importance of ultrasound examination in the procurement process can lead to better alignment on quality standards and mutually beneficial agreements.
Cost-Benefit Analysis
While the implementation of ultrasound examination may entail initial investment costs, the long-term benefits often outweigh these expenses. Reduced defect rates lead to lower rework and warranty costs, improved product longevity, and enhanced customer satisfaction. Procurement teams must conduct comprehensive cost-benefit analyses to justify the adoption of ultrasound technology and secure budget approvals from stakeholders.
Market Conditions and Competitive Advantage
Responding to Market Demands
In a competitive global market, the ability to produce high-quality composite materials efficiently can provide a significant advantage. Ultrasound examination enables manufacturers to meet the increasing demand for reliable and durable products, particularly in sectors where material failure can have severe consequences, such as aerospace and medical devices.
Adapting to Technological Advancements
The rapid pace of technological advancements requires manufacturers to stay abreast of the latest inspection techniques. By adopting ultrasound examination, Japanese manufacturers demonstrate their commitment to leveraging cutting-edge technology, which can enhance their reputation and attract clients seeking advanced material solutions.
Mitigating Supply Chain Risks
Global supply chains are susceptible to disruptions caused by geopolitical tensions, natural disasters, and economic fluctuations. Implementing ultrasound examination allows manufacturers to quickly assess the quality of materials from diverse suppliers, thereby reducing dependency on single sources and enhancing supply chain resilience.
Best Practices for Implementing Ultrasound Examination
Training and Skill Development
Effective utilization of ultrasound examination requires skilled technicians who understand both the technology and the intricacies of composite materials. Investing in comprehensive training programs ensures that staff can accurately interpret ultrasound data and integrate findings into the production workflow.
Integrating with Quality Control Systems
Ultrasound examination should be seamlessly integrated into existing quality control systems. This involves establishing standardized testing protocols, maintaining detailed records of inspection results, and using data analytics to identify trends and areas for improvement.
Collaboration with Research and Development
Collaborating with R&D departments can lead to innovative applications of ultrasound technology. Joint efforts can focus on developing new composite materials with enhanced properties, optimizing manufacturing processes, and exploring advanced inspection techniques that further improve material quality.
Continuous Monitoring and Feedback Loops
Creating continuous feedback loops between production, quality control, and procurement teams ensures that insights from ultrasound examinations are promptly acted upon. This dynamic approach fosters a culture of quality and accountability, driving ongoing enhancements in composite material manufacturing.
Advantages of Ultrasound Examination in Composite Manufacturing
- Non-Destructive Testing: Ultrasound examination allows for the inspection of materials without causing any damage, preserving the integrity of the composites for further use.
- Early Defect Detection: Identifying defects early in the manufacturing process reduces the likelihood of costly rework and rejects.
- Enhanced Product Reliability: Ensuring the absence of internal flaws enhances the durability and performance of composite products.
- Improved Efficiency: Integrating ultrasound technology can streamline the inspection process, leading to faster production cycles.
- Data-Driven Insights: The data obtained from ultrasound examinations provides valuable insights for continuous improvement and strategic decision-making.
Challenges and Considerations
Initial Investment Costs
Implementing ultrasound examination technology requires significant upfront investment in equipment, training, and process integration. Manufacturers must carefully plan and allocate resources to ensure a smooth transition and maximize return on investment.
Technical Expertise
The effectiveness of ultrasound examination depends on the expertise of the personnel conducting the inspections. Recruiting and retaining skilled technicians, as well as providing ongoing training, are essential for maintaining high inspection standards.
Integration with Existing Systems
Seamlessly integrating ultrasound examination with existing manufacturing and quality control systems can be complex. Manufacturers must ensure compatibility and develop protocols that align with their specific production workflows.
Maintaining Consistent Standards
Ensuring consistent inspection standards across different production lines and facilities is crucial. Establishing comprehensive guidelines and conducting regular audits can help maintain uniform quality control measures.
Case Studies: Successful Implementation in Japanese Manufacturing
Automotive Sector
A leading Japanese automotive manufacturer successfully integrated ultrasound examination into its composite component production. By detecting and addressing internal defects early, the company reduced waste by 15% and improved overall product reliability, leading to increased customer satisfaction and market share.
Aerospace Industry
In the aerospace sector, precision and reliability are paramount. A Japanese aerospace company adopted ultrasound technology to inspect composite materials used in aircraft structures. This implementation resulted in a 20% decrease in material failures and enhanced the company’s reputation for quality and innovation.
Electronics Manufacturing
A prominent electronics manufacturer in Japan utilized ultrasound examination to ensure the quality of composite materials in their devices. The technology enabled the identification of subtle defects that could impact device performance, ensuring that only the highest quality products reached the market.
Future Trends and Developments
Advancements in Ultrasound Technology
The future of ultrasound examination in composite manufacturing is promising, with ongoing advancements in sensor technology, data processing, and artificial intelligence. These developments will enable more accurate inspections, faster data analysis, and predictive maintenance capabilities.
Integration with Industry 4.0
As manufacturing moves towards Industry 4.0, the integration of ultrasound examination with smart factory systems will become increasingly important. Real-time data sharing, automated inspections, and interconnected production lines will enhance efficiency and responsiveness to quality issues.
Sustainability and Eco-Friendly Practices
Ultrasound examination contributes to sustainability by reducing material waste and improving the longevity of composite products. Future developments may focus on enhancing the eco-friendly aspects of manufacturing processes, aligning with global sustainability goals.
Conclusion
The incorporation of ultrasound examination in Japanese manufacturing represents a significant step forward in composite materials innovation. By enhancing material integrity, streamlining procurement processes, and providing valuable data for continuous improvement, this technology offers numerous benefits to manufacturers. While challenges such as initial investment costs and the need for technical expertise exist, the long-term advantages of improved product quality, reduced waste, and increased market competitiveness make ultrasound examination an indispensable tool in modern manufacturing. As Japanese manufacturers continue to lead in precision and innovation, ultrasound technology will play a pivotal role in shaping the future of composite materials and sustaining their global reputation for excellence.
資料ダウンロード
QCD管理受発注クラウド「newji」は、受発注部門で必要なQCD管理全てを備えた、現場特化型兼クラウド型の今世紀最高の受発注管理システムとなります。
ユーザー登録
受発注業務の効率化だけでなく、システムを導入することで、コスト削減や製品・資材のステータス可視化のほか、属人化していた受発注情報の共有化による内部不正防止や統制にも役立ちます。
NEWJI DX
製造業に特化したデジタルトランスフォーメーション(DX)の実現を目指す請負開発型のコンサルティングサービスです。AI、iPaaS、および先端の技術を駆使して、製造プロセスの効率化、業務効率化、チームワーク強化、コスト削減、品質向上を実現します。このサービスは、製造業の課題を深く理解し、それに対する最適なデジタルソリューションを提供することで、企業が持続的な成長とイノベーションを達成できるようサポートします。
製造業ニュース解説
製造業、主に購買・調達部門にお勤めの方々に向けた情報を配信しております。
新任の方やベテランの方、管理職を対象とした幅広いコンテンツをご用意しております。
お問い合わせ
コストダウンが利益に直結する術だと理解していても、なかなか前に進めることができない状況。そんな時は、newjiのコストダウン自動化機能で大きく利益貢献しよう!
(β版非公開)