- お役立ち記事
- “Revolutionizing Japanese Manufacturing: Insights from the EMS Panel”
月間76,176名の
製造業ご担当者様が閲覧しています*
*2025年3月31日現在のGoogle Analyticsのデータより
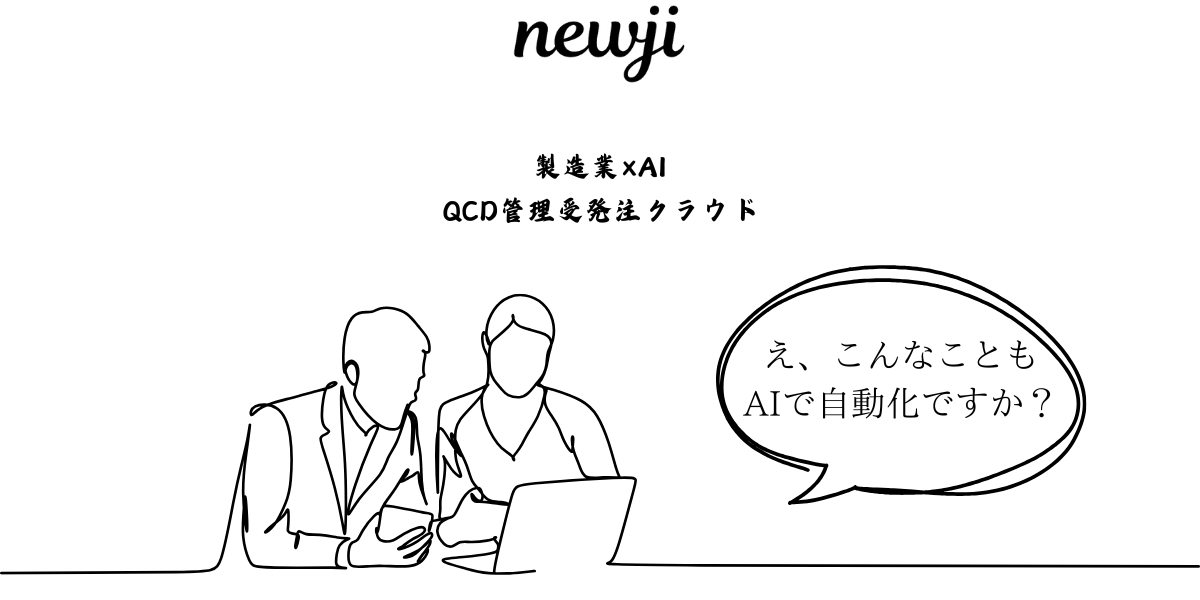
“Revolutionizing Japanese Manufacturing: Insights from the EMS Panel”
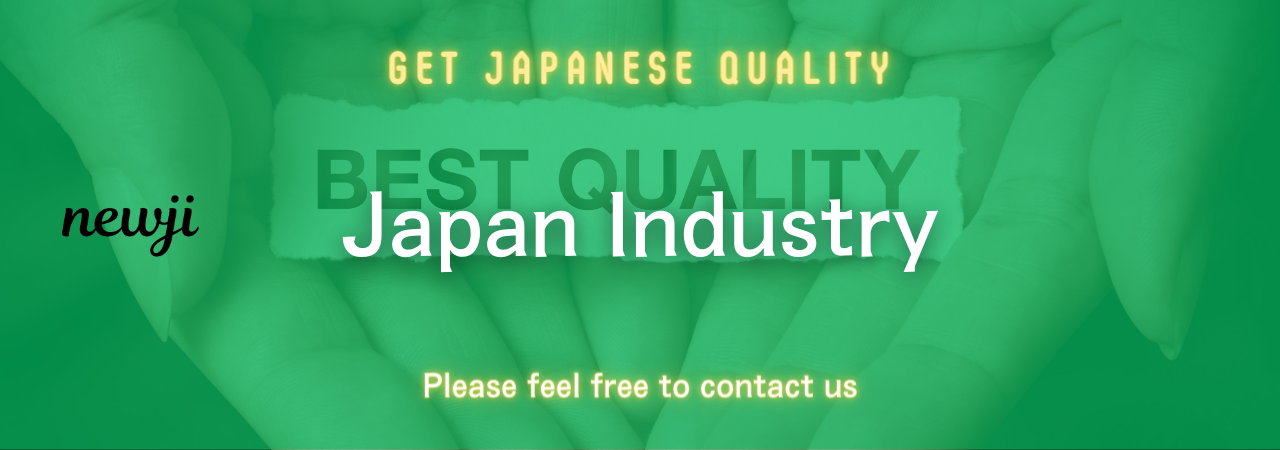
目次
Introduction to Japanese Manufacturing Excellence
Japanese manufacturing has long been synonymous with quality, efficiency, and innovation. The country’s commitment to continuous improvement, known as “Kaizen,” has set global standards in various industries. Among the key players in this landscape are companies within the Electronic Manufacturing Services (EMS) sector. The EMS panel in Japan offers unique insights into the strengths and challenges of procuring from Japanese suppliers. This article explores the multifaceted aspects of Japanese manufacturing, drawing on extensive experience in procurement and purchasing to provide practical guidance for international companies seeking to collaborate with Japanese manufacturers.
Advantages of Partnering with Japanese Suppliers
Unparalleled Quality Control
Japanese manufacturers are renowned for their stringent quality control measures. The implementation of Total Quality Management (TQM) ensures that every product meets high standards. This meticulous approach minimizes defects and guarantees consistency, providing peace of mind to international partners.
Japanese companies often adopt the Deming Cycle—Plan, Do, Check, Act—to foster continuous improvement. This methodology allows for the early detection of issues and the implementation of corrective actions, ensuring that quality is maintained throughout the production process.
Advanced Technical Expertise
Japan’s investment in research and development is one of the highest globally, resulting in cutting-edge technologies and innovative manufacturing processes. Suppliers equipped with advanced technical skills can offer products that meet the evolving demands of the global market.
The integration of Industry 4.0 technologies, such as the Internet of Things (IoT) and artificial intelligence (AI), enhances manufacturing precision and efficiency. This technological prowess allows Japanese manufacturers to offer customized solutions tailored to specific client needs.
Efficient Supply Chain Management
Japanese suppliers excel in supply chain management, ensuring timely delivery and efficient inventory control. Practices such as Just-In-Time (JIT) reduce waste and lower inventory costs, which can be beneficial for international partners looking to optimize their own operations.
The reliability of Japanese logistics ensures that materials and products are transported swiftly and securely. This reliability is a significant advantage for businesses that rely on timely deliveries to maintain their production schedules.
Strong Supplier Relationships
Building long-term relationships is a cornerstone of Japanese business culture. Suppliers are committed to fostering trust and mutual respect with their partners, leading to more stable and collaborative business relationships.
This approach facilitates better communication and cooperation, which can result in more favorable terms and enhanced flexibility in addressing any challenges that may arise during the procurement process.
Challenges of Procuring from Japanese Manufacturers
Cultural and Language Barriers
One of the primary challenges when dealing with Japanese suppliers is navigating cultural and language differences. Understanding Japanese business etiquette and communication styles is essential for successful negotiations and ongoing collaborations.
Misinterpretations can occur if cultural nuances are not respected, potentially leading to misunderstandings or conflicts. Investing time in cultural training and employing bilingual professionals can help bridge this gap.
High Initial Costs
Japanese manufacturers often demand higher initial investments due to their focus on quality and advanced technologies. While the long-term benefits of superior products and reliable service are substantial, the upfront costs can be a barrier for some international businesses.
It’s important to evaluate the return on investment (ROI) carefully. The durability and performance of Japanese products often lead to cost savings over time, offsetting the initial expenditure.
Strict Compliance Requirements
Adhering to Japanese regulatory standards and compliance requirements can be demanding. International partners must ensure that their products and processes align with Japanese norms, which may necessitate additional documentation and adjustments.
Failure to comply can result in delays or rejection of shipments, impacting the overall supply chain and project timelines. Working closely with Japanese suppliers to understand and meet these requirements is crucial.
Long Lead Times
Due to the high level of customization and quality assurance, lead times for Japanese suppliers can be longer compared to competitors from other regions. This extended timeline can pose challenges for businesses with tight schedules or urgent production needs.
Effective planning and clear communication about deadlines are essential to mitigate the impact of longer lead times. Building a buffer into project schedules can help accommodate any unforeseen delays.
Effective Supplier Negotiation Techniques in Japan
Building Trust and Relationships
In Japanese business culture, establishing trust and strong relationships is fundamental before entering into negotiations. Taking the time to engage in non-business-related conversations and showing genuine interest in the supplier’s business can lay the foundation for successful negotiations.
Patience is key, as relationships often develop gradually. Demonstrating commitment to a long-term partnership rather than seeking immediate gains can enhance the negotiation process.
Understanding Decision-Making Hierarchies
Japanese companies typically have hierarchical decision-making structures. It’s important to identify and engage with the key decision-makers to ensure that negotiations are effective.
Presenting proposals in a clear and respectful manner, considering the hierarchical context, can facilitate smoother discussions and approvals.
Emphasizing Mutual Benefits
Highlighting how a partnership can provide mutual benefits is an effective negotiation strategy. Japanese suppliers appreciate proposals that demonstrate a win-win scenario, where both parties gain value from the collaboration.
Detailing the potential for shared growth, improved efficiency, or enhanced product offerings can make the proposal more attractive and increase the likelihood of agreement.
Being Prepared for Detail-Oriented Discussions
Japanese negotiations are often meticulous and detail-oriented. Being well-prepared with comprehensive information, data, and documentation can facilitate more productive discussions.
Addressing potential questions and providing clear, evidence-based responses can build credibility and trust, making it easier to reach favorable terms.
Market Conditions for Japanese Manufacturers
Stable Economic Environment
Japan boasts a stable economic environment with robust infrastructure and a highly skilled workforce. This stability provides a reliable foundation for manufacturing operations, attracting international investors and partners.
The country’s emphasis on innovation and technological advancement ensures that Japanese manufacturers remain competitive in the global market.
Strong Supply Chain Networks
Japan’s well-developed supply chain networks enable efficient sourcing of raw materials and components. This efficiency reduces lead times and enhances the overall reliability of the manufacturing process.
International partners benefit from the seamless integration of supply chains, which can lead to more streamlined operations and reduced logistical complexities.
Competitive Labor Costs
While Japan is known for its high-quality labor, labor costs are competitive compared to other advanced economies. The combination of skilled workers and efficient processes ensures that production costs remain manageable without compromising on quality.
This cost-effectiveness is a significant advantage for international companies looking to maintain high standards while optimizing expenses.
Focus on Sustainability
Japanese manufacturers are increasingly prioritizing sustainability and environmentally friendly practices. This focus aligns with global trends towards responsible manufacturing and can enhance the reputation of international partners associated with sustainable sourcing.
Implementing eco-friendly processes not only meets regulatory requirements but also appeals to environmentally conscious consumers, providing a competitive edge in the market.
Best Practices for International Procurement from Japan
Comprehensive Supplier Evaluation
Conducting thorough evaluations of potential Japanese suppliers is essential to ensure alignment with your company’s standards and requirements. Assess factors such as capacity, quality control measures, financial stability, and past performance.
Visiting supplier facilities and conducting audits can provide deeper insights into their operations and reliability.
Clear Communication and Expectations
Establishing clear lines of communication and setting explicit expectations can prevent misunderstandings and ensure that both parties are aligned on project goals, timelines, and quality standards.
Using detailed contracts and service level agreements (SLAs) can formalize these expectations and provide a framework for accountability.
Leveraging Technology for Collaboration
Utilizing collaborative technologies such as project management software, video conferencing, and real-time data sharing tools can enhance coordination with Japanese suppliers.
These technologies facilitate seamless communication, allowing for real-time updates and swift resolution of any issues that may arise during the procurement process.
Implementing Continuous Improvement Practices
Adopting continuous improvement methodologies, such as Lean and Six Sigma, can enhance the efficiency and effectiveness of the procurement process. Collaborating with Japanese suppliers to identify areas for improvement can lead to mutual benefits and enhanced performance.
Regularly reviewing processes and seeking feedback can foster a culture of excellence and innovation in the partnership.
Quality Control and Technical Skills in Japanese Manufacturing
Robust Quality Assurance Systems
Japanese manufacturers implement robust quality assurance systems that encompass every stage of the production process. Techniques such as Statistical Process Control (SPC) and Failure Mode and Effects Analysis (FMEA) are commonly employed to identify and mitigate potential defects.
These systems ensure that products consistently meet or exceed the required specifications, enhancing the confidence of international partners in the procurement process.
Skilled Workforce and Technical Training
The emphasis on technical education and continuous training in Japan results in a highly skilled workforce. Employees are proficient in the latest manufacturing technologies and methodologies, contributing to the overall excellence of the manufacturing process.
This skilled workforce enhances the ability of Japanese suppliers to adapt to new technologies and meet the complex demands of international markets.
Advanced Manufacturing Technologies
Japanese manufacturers leverage advanced technologies such as robotics, automation, and precision engineering to optimize production efficiency and product quality. Integrating these technologies reduces human error and increases consistency across production batches.
The adoption of smart manufacturing practices allows for real-time monitoring and adjustments, ensuring that production remains aligned with quality standards.
Comprehensive Testing and Validation
Extensive testing and validation procedures are integral to Japanese manufacturing. Products undergo rigorous testing to ensure functionality, durability, and compliance with international standards.
This thorough validation process minimizes the risk of defects and failures, providing international partners with assurance regarding the reliability of sourced products.
Logistics and Production Efficiency in Japanese Factories
Optimized Production Planning
Japanese factories excel in production planning, utilizing techniques such as Just-In-Time (JIT) to streamline operations and reduce waste. This optimization ensures that resources are utilized efficiently, lowering production costs and enhancing scalability.
Effective production planning also facilitates flexibility in adapting to changes in demand, allowing manufacturers to respond swiftly to market fluctuations.
Lean Manufacturing Principles
The implementation of Lean manufacturing principles is prevalent in Japanese factories. By eliminating non-value-added activities and focusing on process efficiency, Japanese manufacturers achieve higher productivity and lower operational costs.
Lean practices contribute to shorter lead times and improved product quality, benefiting both the manufacturer and their international partners.
Integrated Logistics Systems
Japanese manufacturers utilize integrated logistics systems to manage the flow of materials and products throughout the supply chain. This integration ensures a seamless transition from raw material procurement to final product delivery.
Efficient logistics management reduces the risk of delays and ensures that products reach their destinations on time, maintaining the reliability of the supply chain.
Automation and Smart Manufacturing
Automation plays a significant role in enhancing production efficiency in Japanese factories. Automated systems and smart manufacturing technologies enable precise and consistent production processes, reducing variability and increasing output.
The use of automation not only speeds up production but also allows for greater flexibility in manufacturing, enabling quick adjustments to production lines in response to changing demands.
Automation and Factory Efficiency in Japan
Embracing Industry 4.0
Japanese manufacturers are at the forefront of adopting Industry 4.0 technologies, integrating automation, data analytics, and interconnected systems into their production processes. This integration enhances factory efficiency by enabling real-time monitoring, predictive maintenance, and data-driven decision-making.
Industry 4.0 technologies facilitate greater transparency and control over manufacturing operations, allowing for continuous optimization and improvement.
Robotics and AI in Manufacturing
The deployment of robotics and artificial intelligence (AI) in Japanese factories increases precision and reduces the need for manual labor. Robots handle repetitive and hazardous tasks, improving safety and allowing human workers to focus on more complex and value-added activities.
AI algorithms analyze production data to identify patterns and optimize processes, leading to increased efficiency and productivity.
Energy Efficiency and Sustainability
Japanese factories prioritize energy efficiency and sustainability as part of their automation strategies. Implementing energy-saving technologies and sustainable practices reduces operational costs and minimizes the environmental impact of manufacturing activities.
Sustainable manufacturing not only aligns with global environmental standards but also enhances the reputation of Japanese suppliers as responsible and forward-thinking partners.
Smart Supply Chain Management
Automation extends to supply chain management, where smart systems track and manage inventory, logistics, and order fulfillment. These systems enhance coordination and reduce lead times, ensuring that materials and products move smoothly through the supply chain.
Smart supply chain management increases the overall resilience and flexibility of the manufacturing process, allowing for quicker responses to disruptions or changes in demand.
Conclusion: Embracing Japanese Procurement for Manufacturing Success
Collaborating with Japanese manufacturers offers significant advantages in terms of quality, technical expertise, and efficiency. However, it also presents challenges such as cultural differences and higher initial costs. By understanding these dynamics and employing effective procurement strategies, international companies can harness the strengths of Japanese manufacturing to drive their own success.
Building strong relationships, leveraging advanced technologies, and adopting best practices in procurement and quality control are essential for maximizing the benefits of sourcing from Japan. Embracing these insights from the EMS panel can lead to enhanced product offerings, improved operational efficiency, and sustained competitive advantage in the global market.
Investing in the partnership with Japanese suppliers is not merely a transactional decision but a strategic move towards achieving excellence and innovation in manufacturing. By navigating the complexities and capitalizing on the strengths of Japanese manufacturing, businesses can position themselves for long-term growth and success.
資料ダウンロード
QCD管理受発注クラウド「newji」は、受発注部門で必要なQCD管理全てを備えた、現場特化型兼クラウド型の今世紀最高の受発注管理システムとなります。
ユーザー登録
受発注業務の効率化だけでなく、システムを導入することで、コスト削減や製品・資材のステータス可視化のほか、属人化していた受発注情報の共有化による内部不正防止や統制にも役立ちます。
NEWJI DX
製造業に特化したデジタルトランスフォーメーション(DX)の実現を目指す請負開発型のコンサルティングサービスです。AI、iPaaS、および先端の技術を駆使して、製造プロセスの効率化、業務効率化、チームワーク強化、コスト削減、品質向上を実現します。このサービスは、製造業の課題を深く理解し、それに対する最適なデジタルソリューションを提供することで、企業が持続的な成長とイノベーションを達成できるようサポートします。
製造業ニュース解説
製造業、主に購買・調達部門にお勤めの方々に向けた情報を配信しております。
新任の方やベテランの方、管理職を対象とした幅広いコンテンツをご用意しております。
お問い合わせ
コストダウンが利益に直結する術だと理解していても、なかなか前に進めることができない状況。そんな時は、newjiのコストダウン自動化機能で大きく利益貢献しよう!
(β版非公開)