- お役立ち記事
- Revolutionizing Japanese Manufacturing: Lessons from Shanghai Plastic Industry Innovations
Revolutionizing Japanese Manufacturing: Lessons from Shanghai Plastic Industry Innovations
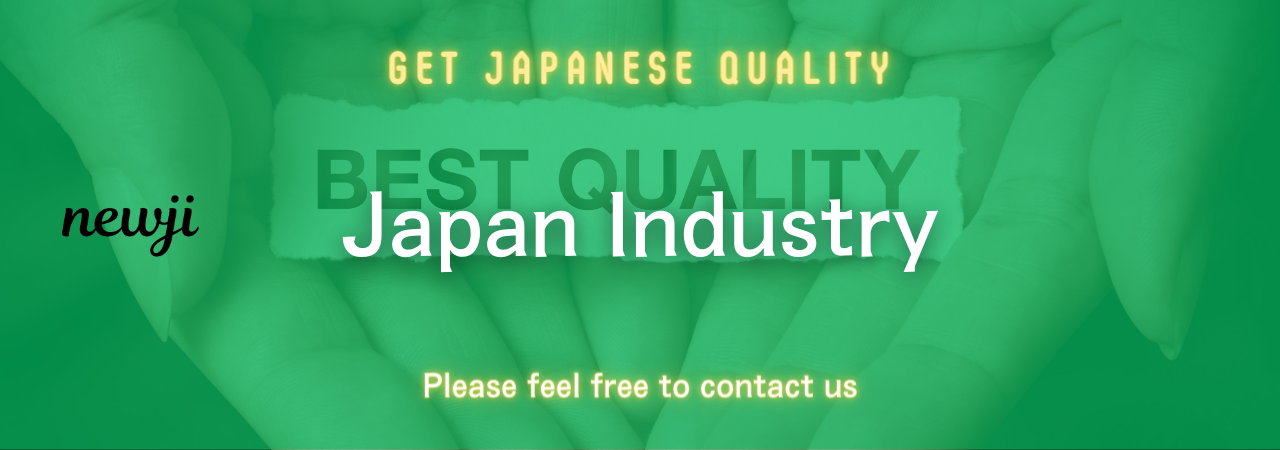
In the ever-evolving landscape of manufacturing, lessons from different regions worldwide offer invaluable insights. One such intriguing comparison can be drawn between the advanced methodologies utilized in Japanese manufacturing and the rapid innovations in the Shanghai plastic industry. This article delves into the revolutionary strides both have made, focusing on practical, field-proven perspectives related to procurement, purchasing, logistics, production management, quality control, and automation.
目次
Understanding the Japanese Manufacturing Ethos
Japanese manufacturing has long been celebrated for its precision, commitment to quality, and continuous improvement philosophies. Concepts such as Kaizen (continuous improvement) and JIT (Just-In-Time) inventory management are cornerstones of this approach.
Kaizen: Continuous Improvement
Kaizen emphasizes small, incremental improvements regularly. Originally implemented in Japanese car manufacturing, Kaizen’s principles are now ubiquitous across various industries. The focus is on employee involvement at all levels, forming a culture where minor innovations and efficiency gains are part of the daily routine.
JIT: Just-In-Time Inventory Management
The JIT model minimizes inventory costs by receiving goods only as they are needed. This requires a highly synchronized supply chain and close collaboration with suppliers. Japanese firms have mastered this approach, achieving reduced waste, lower storage costs, and a more responsive production system.
Comparative Insights from Shanghai’s Plastic Industry
While Japanese industries foster steady perfection, the Shanghai plastic industry epitomizes rapid innovation and flexibility. The volatile market conditions in China demand quick adaptation, which has spurred substantial advancements.
Logistics and Supply Chain Agility
Shanghai-based companies often face erratic market demands and component shortages. They have developed sophisticated logistics strategies to manage these challenges. Agile supply chains enable rapid changes in production schedules and inventory levels, reducing lead times and aligning more closely with market needs.
Lean Manufacturing Implementations
Echoing the lean principles of Japanese manufacturing, Shanghai’s plastic sector employs lean techniques to maximize productivity and minimize waste. However, they take this further by integrating smart factory technologies, enabling real-time data collection and analysis for continuous process optimization.
Supplier Management and Negotiation Techniques
Japanese best practices in procurement and supplier management are characterized by long-term relationships, mutual trust, and collaboration. Contracts often emphasize quality and timely delivery over the lowest cost. On the other hand, Shanghai’s suppliers thrive on competitive pricing and high flexibility. Japanese purchasing managers could anticipate market fluctuations and adjust purchase volumes dynamically, ensuring cost-effectiveness without compromising quality.
Market Conditions and Economic Influences
Understanding the market conditions and economic landscape is crucial for effective procurement and production strategies.
Stability versus Volatility
Japan’s industrial sectors enjoy more stable market conditions, benefiting from a robust regulatory framework and consistent demand patterns. This stability allows for precise forecasting and long-term planning. In contrast, the Shanghai plastic industry wrestles with high demand variability and frequent regulatory changes, fostering a culture of rapid response and innovation.
Impact of Global Trade Practices
Global trade practices significantly impact both regions. The Japanese focus on high-quality exports has garnered international market trust, leading to a premium pricing advantage. Conversely, Shanghai’s competitive pricing and high-volume exports face tighter margins but wider market penetration. Japanese procurement can benefit from understanding these dynamics to balance cost against quality and availability.
Quality Control Mechanisms
Quality control remains an integral component of successful manufacturing. Japan’s rigorous quality control processes are often seen as the gold standard, but the Shanghai plastic industry also offers unique practices worth emulating.
Japanese Quality Control Methods
Japanese manufacturers employ meticulous quality control processes, including Six Sigma methodologies and Total Quality Management (TQM). These practices aim to reduce defects, ensure consistency, and maintain high customer satisfaction levels.
Innovative Approaches in Shanghai
The Shanghai plastic industry incorporates AI and IoT technologies for quality control. Automated inspection systems leveraging machine learning can detect defects faster and more accurately than traditional methods. Implementing these advanced technologies can revolutionize quality assurance processes, reducing human error and enhancing efficiency.
Best Practices in Factory Efficiency and Automation
Efficiency and automation are critical for maintaining competitive advantage. Japanese factories are famous for their efficiency, resulting from years of refined practices and technological investment.
Automation in Japanese Manufacturing
Japanese industries have deeply integrated robotics and automation in their manufacturing processes. From assembly lines to automated material handling, these technologies significantly reduce labor costs, enhance precision, and increase output.
Shanghai’s Adaptation of Smart Technologies
Embracing Industry 4.0 concepts, Shanghai’s factories use smart sensors, cloud computing, and big data analytics to create highly automated and interconnected production environments. This connectivity allows for real-time monitoring and adjustments, contributing to higher efficiency and production adaptability.
Key Takeaways and Implementation Strategies
For procurement and purchasing professionals, blending the steadfast methodologies of Japanese manufacturing with the innovative practices of the Shanghai plastic industry can yield optimal results. Here are several implementation strategies:
Adopt a Hybrid Approach
Incorporate the continuous improvement and JIT principles from Japanese manufacturing for stable, long-term benefits while adopting Shanghai’s agile logistics and smart manufacturing technologies to stay responsive to market changes.
Enhance Supplier Relationships
Cultivate strong, transparent relationships with suppliers, inspired by Japanese practices, but remain open to negotiating competitive, flexible terms akin to Shanghai’s market approach. This balance ensures reliability and cost-effectiveness.
Invest in Technological Advances
Leverage automation and smart factory technologies already proving successful in Shanghai. Such investments can drastically improve quality control, reduce costs, and enhance factory efficiency.
Focus on Quality and Innovation
Ensure stringent quality control mechanisms, blending traditional Japanese methods with AI and IoT innovations from China’s advancements. Maintain a high standard while adapting rapidly to technological changes in quality assessment.
Conclusion
Revolutionizing manufacturing processes requires a strategic fusion of time-tested methodologies and cutting-edge innovations. The Japanese manufacturing ethos, rooted in quality and continuous improvement, combined with the dynamic and technology-driven approaches from the Shanghai plastic industry, presents a robust framework for modern manufacturing excellence.
Professionals in procurement and purchasing must stay informed on global practices, integrating the best methods to drive success and sustainability. With a balanced approach, the benefits of enhanced efficiency, superior quality, and agile response to market demands can be fully realized.
資料ダウンロード
QCD調達購買管理クラウド「newji」は、調達購買部門で必要なQCD管理全てを備えた、現場特化型兼クラウド型の今世紀最高の購買管理システムとなります。
ユーザー登録
調達購買業務の効率化だけでなく、システムを導入することで、コスト削減や製品・資材のステータス可視化のほか、属人化していた購買情報の共有化による内部不正防止や統制にも役立ちます。
NEWJI DX
製造業に特化したデジタルトランスフォーメーション(DX)の実現を目指す請負開発型のコンサルティングサービスです。AI、iPaaS、および先端の技術を駆使して、製造プロセスの効率化、業務効率化、チームワーク強化、コスト削減、品質向上を実現します。このサービスは、製造業の課題を深く理解し、それに対する最適なデジタルソリューションを提供することで、企業が持続的な成長とイノベーションを達成できるようサポートします。
オンライン講座
製造業、主に購買・調達部門にお勤めの方々に向けた情報を配信しております。
新任の方やベテランの方、管理職を対象とした幅広いコンテンツをご用意しております。
お問い合わせ
コストダウンが利益に直結する術だと理解していても、なかなか前に進めることができない状況。そんな時は、newjiのコストダウン自動化機能で大きく利益貢献しよう!
(Β版非公開)