- お役立ち記事
- Revolutionizing Japanese Manufacturing: The Art and Science of Anodizing
Revolutionizing Japanese Manufacturing: The Art and Science of Anodizing
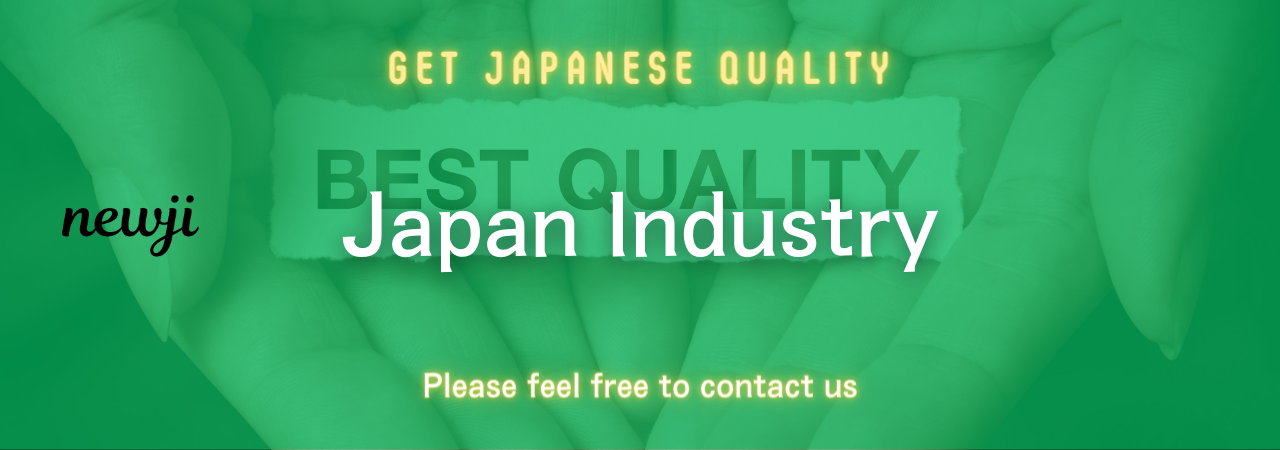
目次
Introduction to Anodizing in Japanese Manufacturing
Anodizing has emerged as a pivotal process in Japanese manufacturing, revolutionizing the way industries enhance the durability and aesthetic appeal of their products. This electrochemical process transforms the surface of aluminum and other metals, creating a protective oxide layer that significantly improves resistance to corrosion and wear. In Japan, where precision and quality are paramount, anodizing plays a crucial role in various sectors, including automotive, electronics, and consumer goods. The integration of advanced anodizing techniques aligns with Japan’s commitment to excellence, fostering innovation and maintaining its competitive edge in the global market.
The Importance of Procurement and Purchasing in Anodizing
Effective procurement and purchasing strategies are fundamental to the success of anodizing operations in Japanese manufacturing. These functions ensure that high-quality raw materials, such as aluminum alloys, are sourced efficiently and cost-effectively. By establishing strong relationships with reliable suppliers, manufacturers can secure consistent material quality, which is essential for achieving uniform anodized finishes. Additionally, strategic procurement practices help manage costs, mitigate risks related to supply chain disruptions, and support sustainable sourcing initiatives, all of which contribute to the overall efficiency and profitability of anodizing processes.
Selecting the Right Suppliers
Selecting the right suppliers is a critical aspect of the procurement process in anodizing. Japanese manufacturers prioritize suppliers who demonstrate a commitment to quality, reliability, and innovation. This involves rigorous evaluation of potential suppliers through assessments of their production capabilities, quality control measures, and adherence to industry standards. Building long-term partnerships with trusted suppliers enables manufacturers to benefit from consistent material quality, timely deliveries, and collaborative problem-solving. Moreover, suppliers who invest in research and development can provide access to cutting-edge materials and technologies, further enhancing the anodizing process.
Negotiation Techniques for Japanese Suppliers
Negotiating with Japanese suppliers requires a nuanced approach that respects cultural norms and business etiquette. Japanese business culture values harmony, mutual respect, and long-term relationships over short-term gains. Effective negotiation techniques include thorough preparation, clear communication of expectations, and a focus on building trust. Understanding the supplier’s perspective and demonstrating a willingness to collaborate can lead to mutually beneficial agreements. Additionally, incorporating flexibility in negotiations allows for adjustments based on market conditions and evolving business needs, fostering a cooperative and sustainable partnership.
Trade Practices and Market Conditions
Navigating trade practices and understanding market conditions are essential for optimizing anodizing operations in Japan. The Japanese market is characterized by its demand for high-quality products and adherence to stringent regulatory standards. Manufacturers must stay abreast of changes in trade policies, tariffs, and international trade agreements that can impact the cost and availability of raw materials. Additionally, understanding consumer preferences and market trends allows manufacturers to tailor their anodizing processes to meet specific demands, ensuring that their products remain competitive both domestically and internationally.
Understanding the Japanese Market
The Japanese market is renowned for its discerning consumers and emphasis on product quality. Manufacturers must align their anodizing processes with these expectations to succeed in this competitive landscape. This involves adopting advanced quality control measures, investing in state-of-the-art equipment, and continuously improving production techniques. Furthermore, understanding regional market variations and consumer preferences can help manufacturers tailor their offerings to meet specific demands, enhancing their market position and driving growth.
Adapting to Japanese Business Culture
Adapting to Japanese business culture is crucial for successful trade practices in anodizing. Japanese businesses prioritize relationship-building, attention to detail, and a commitment to continuous improvement. Manufacturers must demonstrate respect for these cultural values by fostering transparent communication, honoring commitments, and engaging in collaborative problem-solving. Embracing the principles of kaizen, or continuous improvement, encourages a culture of excellence and innovation, aligning with the expectations of Japanese partners and customers.
Logistics in Anodizing Supply Chains
Efficient logistics management is vital for the seamless operation of anodizing supply chains in Japan. The process involves the coordination of multiple stages, from the procurement of raw materials to the delivery of finished products. Effective logistics strategies ensure timely deliveries, minimize lead times, and reduce costs associated with transportation and inventory management. Leveraging advanced logistics technologies, such as real-time tracking and automated inventory systems, enhances the visibility and responsiveness of the supply chain, enabling manufacturers to address potential bottlenecks proactively.
Production Management and Engineering
Robust production management and engineering practices underpin the success of anodizing operations in Japanese manufacturing. This involves the meticulous planning and execution of production schedules, resource allocation, and process optimization. Advanced engineering techniques contribute to the efficiency and scalability of anodizing processes, enabling manufacturers to meet varying production demands without compromising quality. Additionally, integrating automation and smart manufacturing technologies enhances precision, reduces human error, and increases overall productivity.
Efficiency and Automation in Anodizing Processes
Efficiency and automation are at the forefront of modern anodizing processes in Japan. Automated systems facilitate consistent and precise application of anodizing treatments, ensuring uniformity across large batches of products. These technologies also enable real-time monitoring and control of critical parameters, such as temperature, voltage, and electrolyte composition, optimizing the anodizing outcome. Furthermore, automation reduces labor costs and enhances safety by minimizing manual intervention in potentially hazardous processes, aligning with Japan’s emphasis on workplace safety and operational excellence.
Quality Control in Anodizing
Quality control is paramount in anodizing, particularly within the rigorous standards of Japanese manufacturing. Implementing comprehensive quality control measures ensures that anodized products meet or exceed industry specifications and customer expectations. This includes regular inspection of raw materials, meticulous monitoring of the anodizing process, and thorough testing of finished products. Advanced quality control techniques, such as statistical process control and non-destructive testing, enable manufacturers to identify and rectify defects in real time, maintaining the highest levels of product integrity and reliability.
Advantages and Disadvantages of Anodizing in Japanese Manufacturing
Anodizing offers numerous advantages that align with the principles of Japanese manufacturing, such as enhanced durability, improved corrosion resistance, and superior aesthetic appeal. These benefits contribute to the longevity and reliability of products, reinforcing the reputation of Japanese manufacturers for quality and excellence. Additionally, anodizing can be tailored to achieve specific color finishes and surface textures, providing flexibility in product design and customization.
However, there are also challenges associated with anodizing. The process can be energy-intensive and may involve the use of hazardous chemicals, necessitating stringent environmental and safety protocols. Additionally, achieving uniform anodized finishes requires precise control of process parameters, which can be technically demanding. Balancing the benefits of anodizing with these challenges requires continuous innovation and investment in process optimization and environmental management.
Best Practices for Successful Anodizing Operations
Implementing best practices is essential for optimizing anodizing operations and ensuring sustained success in Japanese manufacturing. These practices encompass various aspects, from process management and quality control to supplier relationships and workforce training. Adopting a holistic approach that integrates these elements fosters a culture of excellence and continuous improvement, driving operational efficiency and product quality.
Implementing Continuous Improvement
Continuous improvement, or kaizen, is a foundational principle in Japanese manufacturing that is highly applicable to anodizing operations. This involves regularly assessing and refining processes to enhance efficiency, reduce waste, and improve product quality. Engaging employees in problem-solving and innovation initiatives encourages a proactive approach to addressing challenges and seizing opportunities for advancement. By fostering a mindset of ongoing improvement, manufacturers can maintain competitiveness and adapt to evolving market demands.
Leveraging Technology for Enhanced Quality
Leveraging advanced technologies is crucial for enhancing the quality and efficiency of anodizing processes. Automation, real-time monitoring systems, and data analytics provide valuable insights into process performance, enabling manufacturers to make informed decisions and implement timely corrective actions. Additionally, investing in research and development facilitates the exploration of new anodizing techniques and materials, contributing to product innovation and differentiation. Embracing technological advancements ensures that anodizing operations remain at the forefront of industry standards and customer expectations.
Conclusion
Anodizing represents a harmonious blend of art and science in Japanese manufacturing, embodying the nation’s dedication to quality, precision, and innovation. By mastering procurement and purchasing strategies, understanding trade practices and market conditions, optimizing logistics, and implementing robust production and quality control measures, Japanese manufacturers can leverage anodizing to enhance product performance and aesthetic appeal. Embracing best practices and continuous improvement ensures that anodizing operations remain efficient, sustainable, and competitive in a dynamic global marketplace. As Japanese manufacturing continues to evolve, the art and science of anodizing will undoubtedly play a pivotal role in shaping the future of high-quality, durable, and visually appealing products.
資料ダウンロード
QCD調達購買管理クラウド「newji」は、調達購買部門で必要なQCD管理全てを備えた、現場特化型兼クラウド型の今世紀最高の購買管理システムとなります。
ユーザー登録
調達購買業務の効率化だけでなく、システムを導入することで、コスト削減や製品・資材のステータス可視化のほか、属人化していた購買情報の共有化による内部不正防止や統制にも役立ちます。
NEWJI DX
製造業に特化したデジタルトランスフォーメーション(DX)の実現を目指す請負開発型のコンサルティングサービスです。AI、iPaaS、および先端の技術を駆使して、製造プロセスの効率化、業務効率化、チームワーク強化、コスト削減、品質向上を実現します。このサービスは、製造業の課題を深く理解し、それに対する最適なデジタルソリューションを提供することで、企業が持続的な成長とイノベーションを達成できるようサポートします。
オンライン講座
製造業、主に購買・調達部門にお勤めの方々に向けた情報を配信しております。
新任の方やベテランの方、管理職を対象とした幅広いコンテンツをご用意しております。
お問い合わせ
コストダウンが利益に直結する術だと理解していても、なかなか前に進めることができない状況。そんな時は、newjiのコストダウン自動化機能で大きく利益貢献しよう!
(Β版非公開)