- お役立ち記事
- Revolutionizing Japanese Manufacturing: The Cutting-Edge Role of Product Safety Testing
月間76,176名の
製造業ご担当者様が閲覧しています*
*2025年3月31日現在のGoogle Analyticsのデータより
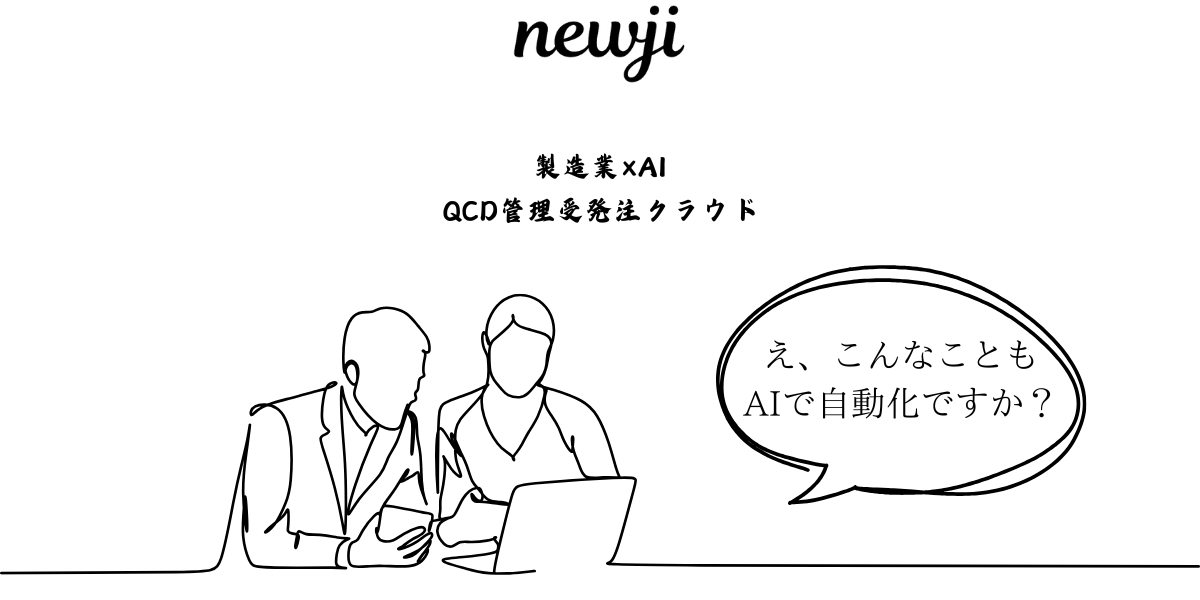
Revolutionizing Japanese Manufacturing: The Cutting-Edge Role of Product Safety Testing
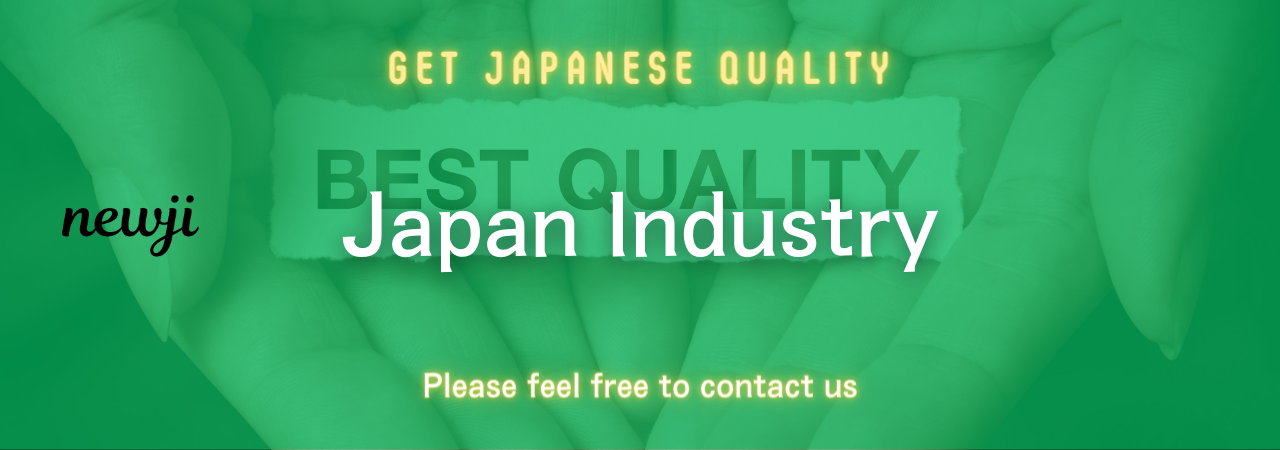
目次
Introduction to Product Safety Testing in Japanese Manufacturing
Product safety testing has become a pivotal aspect of Japanese manufacturing, driving innovation and ensuring that products meet the highest standards of quality and safety. This comprehensive approach not only safeguards consumers but also enhances the reputation of Japanese brands globally. The integration of advanced safety testing methods is revolutionizing the manufacturing landscape, making Japanese products synonymous with reliability and excellence.
Product safety testing encompasses a range of procedures designed to evaluate the safety, durability, and performance of products before they reach the market.
Japanese manufacturers prioritize these tests to adhere to both domestic and international regulations, ensuring that their products can compete on a global scale.
This commitment to safety and quality is a cornerstone of Japan’s manufacturing prowess, setting benchmarks for industries worldwide.
The Importance of Product Safety Testing in Procurement and Purchasing
In the realms of procurement and purchasing, product safety testing plays a crucial role in decision-making processes.
When sourcing materials or finished goods, ensuring that suppliers adhere to stringent safety standards is paramount.
This not only mitigates risks associated with defective products but also fosters long-term partnerships built on trust and reliability.
By incorporating product safety testing into procurement strategies, companies can:
– **Ensure Compliance:** Adhering to international safety standards and regulations.
– **Enhance Quality Control:** Maintaining consistent product quality across batches.
– **Reduce Liability Risks:** Minimizing potential legal issues arising from product failures.
– **Boost Consumer Confidence:** Elevating brand reputation through commitment to safety.
These benefits underscore the necessity of integrating product safety testing into the procurement and purchasing lifecycle, particularly when dealing with Japanese suppliers known for their meticulous standards.
Advantages of Japanese Product Safety Testing
Japanese manufacturers are renowned for their rigorous approach to product safety testing, which offers numerous advantages:
1. High Quality Standards
Japanese manufacturers maintain some of the highest quality standards in the world.
Their commitment to perfection ensures that products are not only safe but also durable and efficient.
This focus on quality reduces the likelihood of recalls and enhances customer satisfaction.
2. Innovation and Technological Advancement
Japan is at the forefront of technological innovation, continuously developing advanced testing methodologies.
These innovations enable more accurate and comprehensive safety assessments, leading to superior product performance.
The integration of cutting-edge technology in safety testing processes sets Japanese products apart in the global market.
3. Compliance with International Regulations
Japanese manufacturers are adept at navigating complex international regulations.
Their thorough understanding of global safety standards ensures that products meet the necessary requirements for various markets.
This expertise facilitates smoother market entry and reduces barriers to international trade.
4. Strong Supplier Relationships
Japanese businesses prioritize building and maintaining strong relationships with their suppliers.
This collaborative approach ensures that suppliers are aligned with the company’s safety and quality standards.
Such partnerships foster mutual growth and reliability, enhancing the overall procurement process.
5. Enhanced Brand Reputation
Commitment to product safety testing significantly bolsters a brand’s reputation.
Consumers associate Japanese products with trust and reliability, which can lead to increased market share and loyalty.
A strong brand reputation is a valuable asset in competitive industries, providing a distinct advantage over rivals.
Challenges and Disadvantages
Despite its numerous advantages, the emphasis on product safety testing in Japanese manufacturing can present certain challenges:
1. Increased Costs
Comprehensive safety testing can lead to higher production costs.
The investment in advanced testing equipment and processes may strain budgets, particularly for smaller manufacturers.
Balancing cost with quality is essential to maintain competitiveness without compromising safety standards.
2. Longer Production Timelines
Rigorous testing procedures can extend production timelines.
Delays in product development and release may impact time-to-market, a critical factor in fast-paced industries.
Efficiently managing testing schedules is necessary to mitigate potential delays.
3. Complexity in Compliance
Navigating the myriad of international safety regulations can be complex and resource-intensive.
Ensuring compliance across different regions requires specialized knowledge and continuous monitoring of regulatory changes.
This complexity can pose challenges for manufacturers aiming to enter multiple markets.
4. Supplier Limitations
High safety standards may limit the pool of qualified suppliers.
Finding suppliers who can meet stringent requirements may be challenging, potentially leading to dependency on a few key partners.
Diversifying the supplier base while maintaining safety standards is crucial to mitigate risks.
Supplier Negotiation Techniques for Product Safety
Effectively negotiating with suppliers is essential to ensure that product safety standards are met without compromising on cost or efficiency.
Japanese suppliers are known for their meticulous attention to detail and quality, making negotiation a strategic process.
1. Building Strong Relationships
Establishing trust and rapport with suppliers is fundamental.
Japanese business culture emphasizes long-term relationships, mutual respect, and collaboration.
Investing time in understanding suppliers’ capabilities and constraints fosters a cooperative negotiation environment.
2. Clear Communication of Standards
Clearly outlining safety and quality standards from the outset is crucial.
Detailed specifications and expectations help prevent misunderstandings and ensure that suppliers are aligned with the company’s requirements.
Regular communication and feedback loops contribute to maintaining consistent standards.
3. Leveraging Volume for Better Terms
Negotiating based on order volumes can lead to more favorable terms.
Commitment to larger or long-term orders may incentivize suppliers to invest in better safety measures or offer competitive pricing.
Volume-based negotiations can enhance the overall value proposition for both parties.
4. Collaborative Problem-Solving
Adopting a collaborative approach to problem-solving during negotiations can lead to win-win outcomes.
Addressing challenges together and jointly developing solutions strengthens the partnership and ensures mutual benefits.
This approach fosters a sense of shared responsibility for product safety and quality.
5. Flexibility and Adaptability
Being flexible and adaptable during negotiations allows for the accommodation of suppliers’ unique circumstances.
Understanding and addressing suppliers’ limitations can lead to more effective and sustainable agreements.
Flexibility ensures that negotiations remain productive and focused on common goals.
Current Market Conditions Impacting Product Safety Testing
The global market landscape is continually evolving, influencing the dynamics of product safety testing in Japanese manufacturing.
1. Increasing Regulatory Standards
With growing consumer awareness, regulatory bodies are imposing stricter safety standards.
Manufacturers must stay abreast of these changes to ensure compliance and avoid penalties.
This trend necessitates ongoing investment in safety testing and quality assurance processes.
2. Technological Advancements
Emerging technologies such as artificial intelligence and automation are transforming product safety testing.
These advancements enable more efficient and accurate assessments, reducing the time and cost associated with traditional testing methods.
Adopting new technologies is essential for maintaining competitiveness in the market.
3. Supply Chain Disruptions
Global events such as pandemics and geopolitical tensions can disrupt supply chains, affecting product safety testing.
Manufacturers must develop resilient supply chains that can adapt to unforeseen challenges while maintaining safety standards.
This resilience is critical for sustaining production and meeting market demands.
4. Sustainability and Environmental Concerns
Environmental sustainability is becoming a key consideration in product safety testing.
Manufacturers are increasingly required to assess the environmental impact of their products and adopt sustainable practices.
Incorporating sustainability into safety testing not only meets regulatory requirements but also aligns with consumer values.
5. Consumer Demand for Transparency
Modern consumers demand greater transparency regarding product safety and manufacturing practices.
Manufacturers must provide detailed information about safety testing processes and results to meet these expectations.
Transparency builds consumer trust and enhances brand loyalty.
Best Practices in Product Safety Testing for Japanese Manufacturers
Adopting best practices in product safety testing is essential for maintaining high standards and achieving operational excellence.
1. Implementing Comprehensive Testing Protocols
Developing detailed and thorough testing protocols ensures that all aspects of product safety are evaluated.
Comprehensive protocols cover a wide range of scenarios and stress conditions, providing a holistic assessment of product performance.
2. Investing in Advanced Testing Technologies
Utilizing state-of-the-art testing equipment and software enhances the accuracy and efficiency of safety assessments.
Investments in technology enable manufacturers to conduct more sophisticated tests, leading to better product quality.
3. Continuous Training and Development
Regular training programs for staff involved in product safety testing are crucial.
Continuous skill development ensures that personnel are proficient in the latest testing techniques and industry standards.
4. Collaborating with External Experts
Partnering with external experts and research institutions can provide valuable insights and innovations in safety testing.
These collaborations facilitate the adoption of best practices and the integration of new methodologies.
5. Regular Review and Improvement of Processes
Establishing a system for regular review and improvement of testing processes ensures ongoing enhancement of safety standards.
Continuous improvement initiatives help identify and rectify inefficiencies, maintaining the effectiveness of safety testing.
6. Integrating Quality Management Systems
Incorporating quality management systems such as ISO 9001 ensures a standardized approach to product safety testing.
These systems provide a framework for maintaining consistent quality and continuous improvement.
7. Engaging in Risk Management
Implementing robust risk management strategies helps identify potential safety issues early in the development process.
Proactive risk assessment enables manufacturers to address vulnerabilities before they translate into real-world problems.
Impact of Product Safety Testing on Factory Efficiency and Automation
Product safety testing significantly influences factory efficiency and the adoption of automation technologies.
1. Streamlining Production Processes
Efficient safety testing protocols streamline production by identifying and eliminating defects early.
This reduces waste and minimizes downtime caused by quality issues, enhancing overall factory productivity.
2. Facilitating Automation Integration
Automation technologies can be seamlessly integrated into safety testing processes, increasing speed and accuracy.
Automated systems handle repetitive and time-consuming tasks, allowing human resources to focus on more complex analyses.
3. Enhancing Data Management
Advanced testing technologies generate vast amounts of data, which can be effectively managed through automated systems.
Data-driven insights enable manufacturers to make informed decisions, optimizing production and safety processes.
4. Reducing Human Error
Automation minimizes the risk of human error in safety testing, ensuring consistent and reliable results.
Consistent testing outcomes are crucial for maintaining high safety standards and product quality.
5. Improving Resource Allocation
Automated safety testing allows for better allocation of resources, as machinery handles routine tasks.
This leads to more efficient use of labor and capital, contributing to overall factory efficiency.
6. Enabling Predictive Maintenance
Data from safety testing can support predictive maintenance strategies, reducing unexpected equipment failures.
Predictive maintenance ensures that testing equipment remains in optimal condition, preventing production delays.
Case Studies: Success Stories in Japanese Manufacturing
Examining real-world examples provides valuable insights into the effective implementation of product safety testing.
1. Toyota’s Commitment to Quality and Safety
Toyota has long been a leader in the automotive industry, setting standards for safety testing.
Their rigorous testing protocols ensure that vehicles meet the highest safety and quality benchmarks.
This commitment has earned Toyota a reputation for reliability and safety, contributing to their global success.
2. Sony’s Technological Innovations
Sony leverages advanced technologies in product safety testing to maintain its position as a leading electronics manufacturer.
By integrating automation and data analytics into their testing processes, Sony ensures that their products are both safe and cutting-edge.
Their proactive approach to safety has reinforced consumer trust and brand loyalty.
3. Panasonic’s Sustainable Manufacturing Practices
Panasonic integrates sustainability into their product safety testing, assessing the environmental impact of their products.
Their comprehensive testing protocols ensure that products are not only safe but also environmentally responsible.
This holistic approach enhances Panasonic’s reputation and aligns with global sustainability trends.
4. Mitsubishi Electric’s Precision Manufacturing
Mitsubishi Electric employs precise safety testing methods to ensure the reliability of their electrical components.
Their meticulous attention to detail in testing processes guarantees product performance and longevity, strengthening their market position.
5. Hitachi’s Collaborative Safety Initiatives
Hitachi collaborates with suppliers and research institutions to enhance product safety testing.
These partnerships facilitate the exchange of knowledge and the adoption of innovative testing methodologies, driving continuous improvement.
Future Trends in Product Safety Testing
The landscape of product safety testing is continually evolving, influenced by technological advancements and shifting market demands.
1. Integration of Artificial Intelligence
Artificial intelligence (AI) is set to revolutionize product safety testing by enabling more sophisticated data analysis and predictive modeling.
AI can identify patterns and anomalies that may be missed by traditional methods, enhancing the accuracy of safety assessments.
2. Expansion of IoT in Testing Processes
The Internet of Things (IoT) allows for real-time monitoring and data collection during safety testing.
Connected devices can provide continuous feedback, enabling more dynamic and responsive testing procedures.
3. Enhanced Focus on Cybersecurity
As products become more connected, cybersecurity becomes an integral aspect of product safety testing.
Ensuring that products are secure against cyber threats is essential for maintaining consumer trust and safety.
4. Adoption of Virtual and Augmented Reality
Virtual and augmented reality technologies offer new ways to simulate and assess product safety scenarios.
These tools provide immersive testing environments, allowing for more comprehensive evaluations without physical risks.
5. Emphasis on Circular Economy Practices
Product safety testing is increasingly incorporating principles of the circular economy, assessing the recyclability and environmental impact of products.
This shift supports sustainable manufacturing practices and aligns with global environmental goals.
6. Global Standardization of Safety Protocols
Efforts towards the standardization of safety testing protocols across different regions are underway.
Standardization facilitates more seamless international trade and ensures consistent safety standards worldwide.
Conclusion: The Future of Japanese Manufacturing and Product Safety Testing
The role of product safety testing in Japanese manufacturing is undeniably transformative, driving advancements in quality, efficiency, and innovation.
As global markets become increasingly competitive and consumer expectations continue to rise, the emphasis on rigorous safety testing will remain a critical factor in sustaining Japan’s manufacturing dominance.
Japanese manufacturers’ commitment to excellence in product safety testing not only ensures compliance with international standards but also fosters trust and loyalty among consumers.
By embracing technological advancements and adopting best practices, Japanese companies are well-positioned to navigate the evolving landscape of global manufacturing.
The future of Japanese manufacturing lies in the continuous enhancement of product safety testing methodologies, integrating sustainability, and leveraging automation and artificial intelligence.
These developments will not only uphold Japan’s reputation for quality and reliability but also set new benchmarks for manufacturing excellence worldwide.
For procurement and purchasing professionals, understanding and leveraging the strengths of Japanese product safety testing can unlock substantial benefits.
From ensuring high-quality standards to fostering resilient supplier relationships, the insights gained from Japanese manufacturing practices can inform strategic decision-making and drive business success.
In conclusion, the cutting-edge role of product safety testing is revolutionizing Japanese manufacturing, cementing its status as a global leader in quality and innovation.
Embracing these practices offers a pathway to enhanced product reliability, consumer trust, and sustained competitive advantage in the ever-evolving manufacturing landscape.
資料ダウンロード
QCD管理受発注クラウド「newji」は、受発注部門で必要なQCD管理全てを備えた、現場特化型兼クラウド型の今世紀最高の受発注管理システムとなります。
ユーザー登録
受発注業務の効率化だけでなく、システムを導入することで、コスト削減や製品・資材のステータス可視化のほか、属人化していた受発注情報の共有化による内部不正防止や統制にも役立ちます。
NEWJI DX
製造業に特化したデジタルトランスフォーメーション(DX)の実現を目指す請負開発型のコンサルティングサービスです。AI、iPaaS、および先端の技術を駆使して、製造プロセスの効率化、業務効率化、チームワーク強化、コスト削減、品質向上を実現します。このサービスは、製造業の課題を深く理解し、それに対する最適なデジタルソリューションを提供することで、企業が持続的な成長とイノベーションを達成できるようサポートします。
製造業ニュース解説
製造業、主に購買・調達部門にお勤めの方々に向けた情報を配信しております。
新任の方やベテランの方、管理職を対象とした幅広いコンテンツをご用意しております。
お問い合わせ
コストダウンが利益に直結する術だと理解していても、なかなか前に進めることができない状況。そんな時は、newjiのコストダウン自動化機能で大きく利益貢献しよう!
(β版非公開)