- お役立ち記事
- Revolutionizing Japanese Manufacturing: The Future of Digital Photopatterning
月間77,185名の
製造業ご担当者様が閲覧しています*
*2025年2月28日現在のGoogle Analyticsのデータより
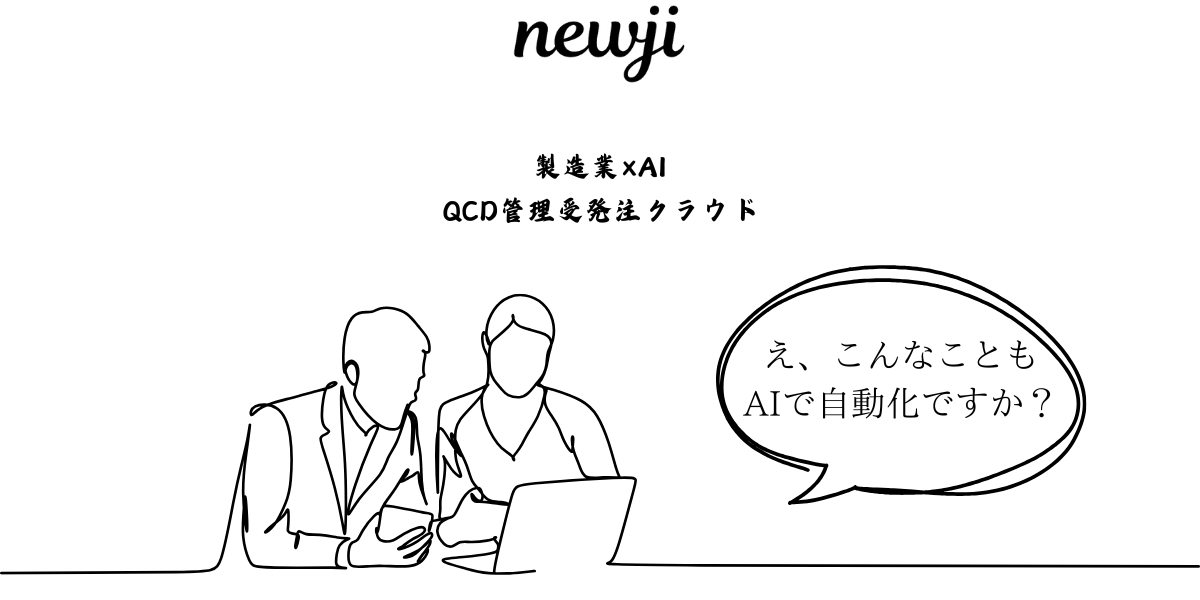
Revolutionizing Japanese Manufacturing: The Future of Digital Photopatterning
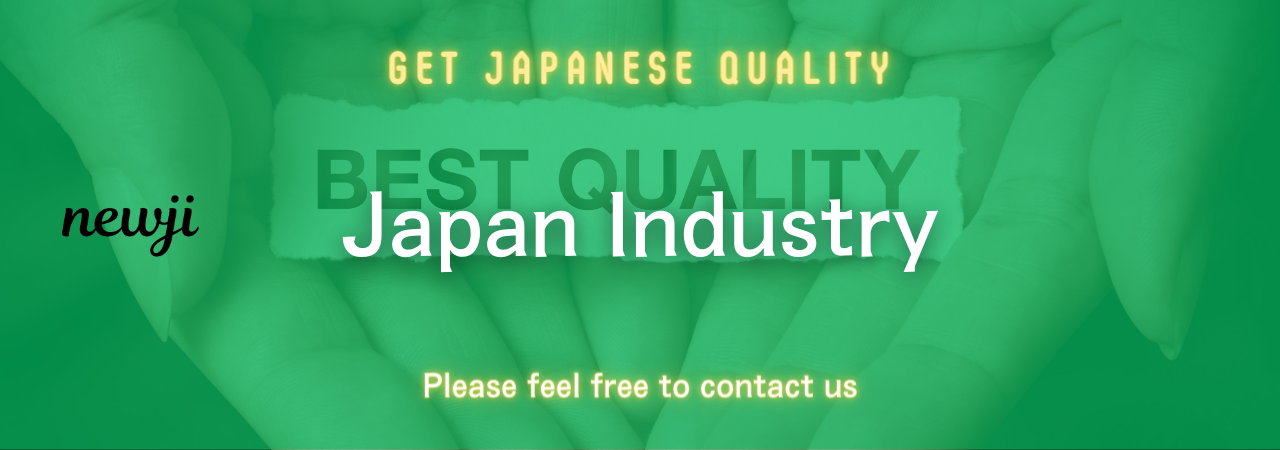
目次
Introduction to Digital Photopatterning in Japanese Manufacturing
Japanese manufacturing has long been synonymous with precision, quality, and innovation.
Digital photopatterning represents the latest advancement in manufacturing technology.
This technique is revolutionizing how products are designed and produced in Japan.
It enables higher accuracy, faster production times, and greater flexibility in manufacturing processes.
For procurement and purchasing professionals, understanding digital photopatterning is crucial.
This knowledge can lead to more informed decisions and stronger relationships with Japanese suppliers.
As digital photopatterning continues to evolve, it promises to reshape the future of manufacturing both in Japan and globally.
The Basics of Digital Photopatterning
Digital photopatterning is a process that uses light to create patterns on a substrate.
This technique is essential in the production of semiconductors, electronics, and various other high-precision industries.
Unlike traditional photolithography, digital photopatterning offers greater flexibility and efficiency.
It allows for rapid prototyping and shorter production cycles.
The technology relies on advanced software and hardware to accurately project patterns onto materials.
Japanese manufacturers have been at the forefront of developing and implementing digital photopatterning techniques.
Their expertise ensures high-quality outputs that meet stringent industry standards.
Understanding the technical aspects of digital photopatterning can significantly benefit procurement strategies.
Advantages of Digital Photopatterning in Japanese Manufacturing
Enhanced Precision and Quality
Digital photopatterning offers unparalleled precision in pattern creation.
Japanese manufacturers leverage this technology to produce components with exact specifications.
This reduces the margin of error and ensures consistent quality across production batches.
Increased Production Efficiency
The digital nature of photopatterning streamlines the manufacturing process.
It allows for faster setup times and quicker adjustments to production lines.
Japanese factories can achieve higher output rates without compromising quality.
Flexibility and Customization
Digital photopatterning enables easy customization of products.
Manufacturers can quickly adapt to changing market demands and client specifications.
This flexibility is particularly beneficial for industries that require bespoke solutions.
Cost-Effectiveness
While the initial investment in digital photopatterning technology may be high, the long-term benefits outweigh the costs.
Japanese manufacturers experience reduced waste, lower labor costs, and minimized production downtime.
Advanced Innovation and R&D
Japan’s commitment to research and development drives continuous improvements in digital photopatterning.
This ensures that manufacturers stay ahead of global competitors with cutting-edge technology.
Disadvantages and Challenges
High Initial Investment
The cost of acquiring and maintaining digital photopatterning equipment can be prohibitive.
Small to medium-sized enterprises may find it challenging to justify the investment.
Technical Expertise Required
Operating digital photopatterning machinery requires specialized knowledge.
Japanese manufacturers need to invest in training and education to ensure their workforce is skilled.
Integration with Existing Systems
Integrating new digital photopatterning technology with legacy systems can be complex.
This process may involve significant time and resources to ensure compatibility and efficiency.
Dependence on Technology
Relying heavily on digital systems makes manufacturers vulnerable to technical failures.
Ensuring robust maintenance and having contingency plans are essential to mitigate risks.
Intellectual Property Concerns
Sharing advanced technology with suppliers necessitates strong intellectual property agreements.
Japanese manufacturers must ensure that their innovations are protected to prevent unauthorized use or replication.
Supplier Negotiation Techniques in the Age of Digital Photopatterning
Understanding Supplier Capabilities
Before entering negotiations, assess the supplier’s expertise in digital photopatterning.
Evaluate their technology, quality standards, and production capabilities.
Building Strong Relationships
Japanese business culture emphasizes trust and long-term partnerships.
Invest time in building relationships with suppliers to foster cooperation and mutual benefit.
Clear Communication of Requirements
Clearly articulate your specifications and expectations related to digital photopatterning.
Ensure that suppliers understand the technical details and quality standards required.
Leveraging Technology for Transparency
Use digital tools to enhance transparency in the supply chain.
Implement systems that allow for real-time monitoring and reporting of production processes.
Negotiating Price and Value
Focus not only on the price but also on the value provided by the supplier.
Consider factors such as quality, reliability, and the supplier’s ability to innovate.
Flexibility in Contracts
Design contracts that allow for flexibility in production volumes and timelines.
This adaptability is crucial in the rapidly evolving landscape of digital photopatterning.
Market Conditions and Trends
Global Demand for Precision Manufacturing
As industries like electronics, automotive, and healthcare demand higher precision, digital photopatterning becomes increasingly essential.
Japanese manufacturers are well-positioned to meet this global demand with their advanced technology.
Technological Advancements
Continuous advancements in digital photopatterning technology drive market growth.
Innovations such as higher resolution patterns and faster processing times are setting new industry standards.
Shift Towards Sustainability
Sustainable manufacturing practices are gaining traction globally.
Digital photopatterning supports sustainability by reducing material waste and energy consumption.
Competitive Landscape
Japan remains a leader in manufacturing technology, but competition from other countries is intensifying.
Staying ahead requires ongoing investment in R&D and maintaining high-quality standards.
Impact of Global Supply Chains
Global supply chain dynamics, including disruptions and trade policies, influence Japanese manufacturing.
Diversifying supply sources and enhancing supply chain resilience are critical strategies.
Emerging Markets
Growing markets in Asia, Africa, and Latin America present new opportunities for Japanese manufacturers.
Expanding into these regions can drive growth and increase market share.
Best Practices for Procurement and Purchasing
Comprehensive Supplier Evaluation
Conduct thorough evaluations of potential suppliers’ capabilities in digital photopatterning.
Assess their technological infrastructure, quality control measures, and compliance with industry standards.
Strategic Sourcing
Develop a strategic sourcing plan that aligns with your company’s long-term goals.
Consider factors such as supplier reliability, cost-effectiveness, and technological innovation.
Risk Management
Identify potential risks in the supply chain, including technological failures and geopolitical factors.
Implement strategies to mitigate these risks, such as diversifying suppliers and establishing contingency plans.
Collaborative Partnerships
Foster collaborative relationships with suppliers to drive innovation and continuous improvement.
Encourage open communication and joint problem-solving initiatives.
Continuous Monitoring and Improvement
Regularly monitor supplier performance and provide feedback.
Use metrics and KPIs to assess efficiency, quality, and responsiveness.
Implement continuous improvement programs to enhance supplier performance over time.
Leveraging Technology
Utilize procurement software and digital tools to streamline processes.
Technology can enhance data analysis, improve decision-making, and increase transparency in the supply chain.
Implementing Digital Photopatterning: A Step-by-Step Guide
Assessment and Planning
Begin by assessing your current manufacturing processes and identifying areas where digital photopatterning can add value.
Develop a comprehensive plan that outlines the objectives, required resources, and timelines for implementation.
Technology Selection
Research and select the appropriate digital photopatterning technology that meets your production needs.
Consider factors such as resolution, speed, compatibility with existing systems, and scalability.
Supplier Engagement
Identify and engage with suppliers who specialize in digital photopatterning.
Evaluate their capabilities, conduct site visits, and negotiate terms that align with your strategic goals.
Training and Development
Invest in training programs to upskill your workforce in operating and maintaining digital photopatterning equipment.
This ensures smooth integration and maximizes the benefits of the new technology.
Integration and Testing
Integrate the digital photopatterning technology into your production line.
Conduct thorough testing to ensure compatibility and performance standards are met.
Continuous Optimization
After implementation, continuously monitor the performance of the digital photopatterning process.
Collect data, analyze results, and make necessary adjustments to optimize efficiency and quality.
Case Studies: Success Stories in Japanese Digital Photopatterning
Semiconductor Manufacturing
Japanese semiconductor manufacturers have successfully implemented digital photopatterning to produce high-density integrated circuits.
This has enabled them to stay competitive in the global market by delivering products with superior performance and reliability.
Automotive Components
In the automotive industry, Japanese manufacturers use digital photopatterning to create intricate components for electric vehicles.
The precision and speed of this technology support the rapid development and production of advanced automotive parts.
Consumer Electronics
Japanese consumer electronics companies leverage digital photopatterning to design and manufacture compact and efficient devices.
This has resulted in products that are not only innovative but also meet the high-quality expectations of global consumers.
Medical Devices
In the medical sector, Japanese manufacturers employ digital photopatterning to produce precise medical devices and implants.
The accuracy and reliability of this technology ensure that medical devices meet stringent regulatory standards and patient needs.
Future Prospects of Digital Photopatterning in Japan
Integration with Artificial Intelligence
The integration of AI with digital photopatterning promises to enhance pattern accuracy and predictive maintenance.
AI algorithms can optimize production processes and identify potential issues before they arise.
Advancements in Materials Science
Ongoing research in materials science will lead to the development of new substrates and materials compatible with digital photopatterning.
This will expand the applications and capabilities of the technology across various industries.
Expansion into New Markets
Japanese manufacturers are exploring opportunities in emerging markets where digital photopatterning technology can meet growing industrial demands.
This expansion will drive global adoption and further establish Japan as a leader in manufacturing innovation.
Sustainability Initiatives
Future developments in digital photopatterning will focus on increasing energy efficiency and reducing environmental impact.
Sustainable manufacturing practices will become integral to the technology’s evolution.
Collaborative Innovation
Collaborations between Japanese manufacturers, research institutions, and technology providers will fuel continuous innovation in digital photopatterning.
These partnerships will lead to breakthroughs that further enhance the technology’s capabilities and applications.
Conclusion
Digital photopatterning is transforming Japanese manufacturing, driving advancements in precision, efficiency, and flexibility.
For procurement and purchasing professionals, this technology presents both opportunities and challenges.
Understanding the intricacies of digital photopatterning, from its technical aspects to market trends, is essential for making informed decisions.
By adopting best practices in supplier negotiation, strategic sourcing, and risk management, companies can leverage the benefits of digital photopatterning.
As the technology continues to evolve, Japanese manufacturers will remain at the forefront of innovation, shaping the future of global manufacturing.
Embracing digital photopatterning will not only enhance product quality and production efficiency but also strengthen the competitive edge of manufacturing companies worldwide.
資料ダウンロード
QCD管理受発注クラウド「newji」は、受発注部門で必要なQCD管理全てを備えた、現場特化型兼クラウド型の今世紀最高の受発注管理システムとなります。
ユーザー登録
受発注業務の効率化だけでなく、システムを導入することで、コスト削減や製品・資材のステータス可視化のほか、属人化していた受発注情報の共有化による内部不正防止や統制にも役立ちます。
NEWJI DX
製造業に特化したデジタルトランスフォーメーション(DX)の実現を目指す請負開発型のコンサルティングサービスです。AI、iPaaS、および先端の技術を駆使して、製造プロセスの効率化、業務効率化、チームワーク強化、コスト削減、品質向上を実現します。このサービスは、製造業の課題を深く理解し、それに対する最適なデジタルソリューションを提供することで、企業が持続的な成長とイノベーションを達成できるようサポートします。
製造業ニュース解説
製造業、主に購買・調達部門にお勤めの方々に向けた情報を配信しております。
新任の方やベテランの方、管理職を対象とした幅広いコンテンツをご用意しております。
お問い合わせ
コストダウンが利益に直結する術だと理解していても、なかなか前に進めることができない状況。そんな時は、newjiのコストダウン自動化機能で大きく利益貢献しよう!
(β版非公開)