- お役立ち記事
- Revolutionizing Japanese Manufacturing: The Future of Digital Skills Training
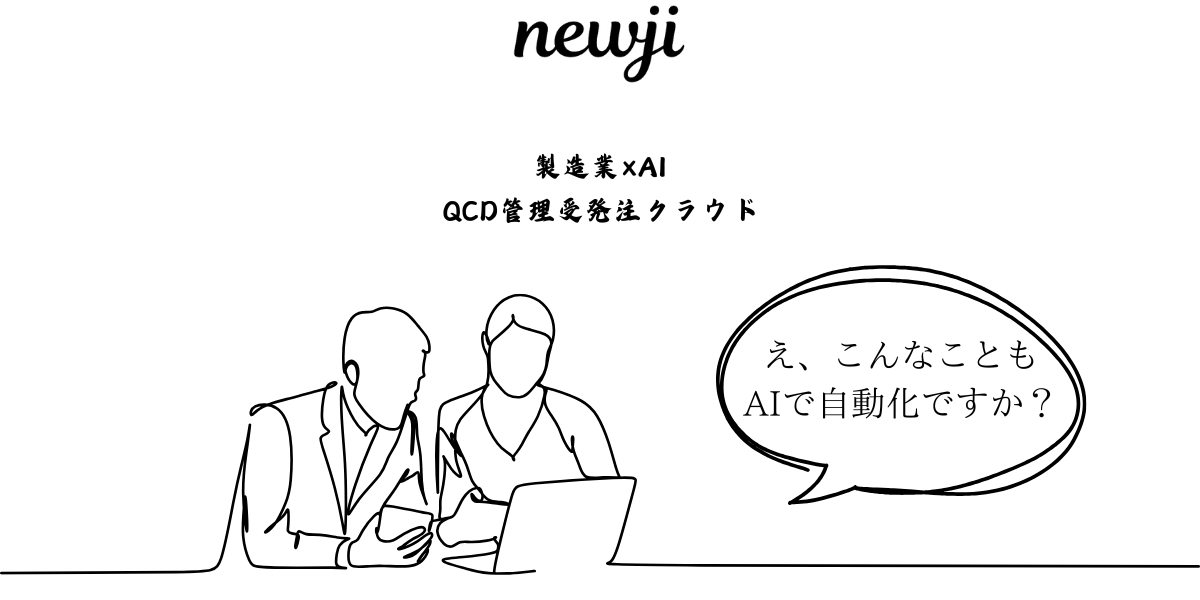
Revolutionizing Japanese Manufacturing: The Future of Digital Skills Training
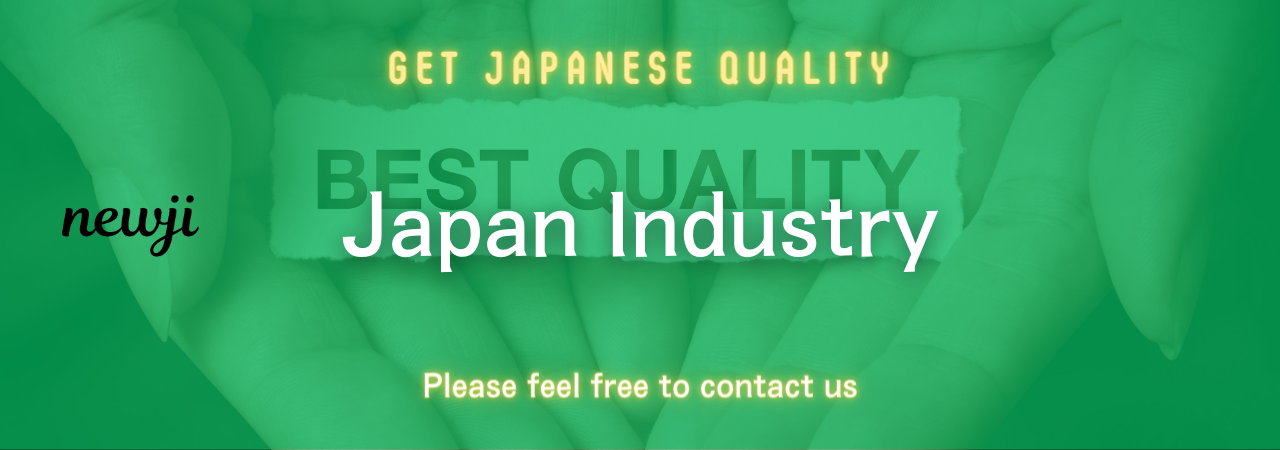
目次
Introduction
The landscape of manufacturing is undergoing a seismic shift, largely driven by rapid advancements in digital technologies.
Nowhere is this more evident than in Japan—a nation renowned for its manufacturing prowess and commitment to quality.
As the industry evolves, so too must the skills and capabilities of its workforce.
This article delves into the future of digital skills training, examining its transformative effect on Japanese manufacturing.
We’ll explore practical field perspectives, advantages and disadvantages, supplier negotiation techniques, market conditions, best practices, and more.
The Importance of Digital Skills in Manufacturing
Digital skills have become the cornerstone of modern manufacturing.
They enable the seamless integration of new technologies such as artificial intelligence (AI), the Internet of Things (IoT), and robotics into production workflows.
For decades, Japanese manufacturers have thrived on principles like Kaizen (continuous improvement) and JIT (Just-In-Time) production.
However, as industries become more data-driven, there’s a pressing need for digital skills to complement these traditional methodologies.
Bridging the Digital Skills Gap
Despite Japan’s reputation for technological innovation, there’s a noticeable gap in the adoption of digital skills among manufacturing employees.
Bridging this gap requires targeted training programs that focus on both existing and emerging technologies.
Companies must invest in training modules that include basics like data analytics and cybersecurity, as well as advanced topics such as machine learning and augmented reality.
Advantages of Digital Skills Training
Enhanced Efficiency and Productivity
One of the most significant advantages of digital skills training is enhanced efficiency.
By equipping workers with the necessary digital tools and knowledge, manufacturers can streamline processes, reduce waste, and improve overall productivity.
Digitally-savvy employees can easily adapt to new software platforms, optimize machine settings, and troubleshoot problems in real-time.
Improved Quality Control
Digital skills also empower workers to leverage advanced quality control techniques.
For example, machine learning algorithms can predict potential defects before they occur, allowing preemptive adjustments.
Data analytics can help in monitoring production variables closely, ensuring that quality standards are consistently met or exceeded.
Better Supplier Management
With the inclusion of digital skills, procurement and purchasing departments can enhance their supplier management strategies.
Real-time data analytics can facilitate better negotiation tactics, price benchmarking, and contract management.
Digital tools also enable transparent communication channels, which are vital for maintaining strong supplier relationships.
Agility and Adaptability
Digital training programs enable a workforce to become more agile and adaptable.
This is particularly valuable in a dynamic market where customer demands and technological advancements are constantly changing.
Employees skilled in digital technologies can pivot quickly, adopting new tools and processes as needed.
Challenges in Implementing Digital Skills Training
Resistance to Change
One of the primary obstacles to digital skills training is resistance to change.
Many employees, particularly those with long tenure, may be hesitant to adopt new technologies.
It’s crucial for management to address these concerns through transparent communication and by demonstrating the long-term benefits of digital skills.
Initial Costs
Another challenge is the initial cost of implementing digital training programs.
These costs can include investments in new software, hiring specialized trainers, and developing training materials.
However, the long-term gains in productivity and efficiency can far outweigh the initial expenditure.
Lack of Expertise
There is also a shortage of experts who can design and deliver effective digital skills training programs.
Partnerships with educational institutions, industry bodies, and technology providers can help bridge this gap.
Supplier Negotiation Techniques
Utilizing Data Analytics
One of the most potent tools in supplier negotiations is data analytics.
Being able to present empirical data on market conditions, supplier performance, and internal needs enhances your bargaining position.
Companies can use digital tools to analyze historical data, forecast future requirements, and identify potential bottlenecks in the supply chain.
Transparent Communication
Transparency is crucial in establishing trust and fostering long-term relationships with suppliers.
Digital platforms can facilitate more consistent and accurate communication.
For example, sharing real-time inventory levels and demand forecasts can help suppliers better plan their production schedules, leading to mutually beneficial outcomes.
Automated Contract Management
Automating contract management through digital platforms can streamline the procurement process.
These tools can manage contract lifecycles, track compliance, and even alert you to upcoming renewals or expirations.
This not only saves time but also minimizes the risk of oversight.
Market Conditions
Globalization and Competition
The global manufacturing landscape is becoming increasingly competitive.
Japanese manufacturers must stay ahead by adopting digital skills that enable them to compete on a global scale.
This includes not only production-related technologies but also digital marketing and customer relationship management tools.
Resource Scarcity
As natural resources become scarcer, manufacturers need to adopt more efficient production techniques.
Digital skills training can provide the knowledge required to optimize resource usage, reducing both costs and environmental impact.
Regulatory Changes
The regulatory environment is also evolving, particularly concerning data privacy and cybersecurity.
Manufacturers must ensure that their workforce is well-versed in these areas to remain compliant with international standards.
Best Practices for Digital Skills Training
Customization
Effective training programs should be tailored to the specific needs of the organization.
This includes custom modules that address the unique challenges and opportunities within the company.
For instance, a factory specializing in automotive components may require different digital skills compared to one producing consumer electronics.
Continuous Learning
Digital skills training should not be a one-time event but an ongoing process.
Regular updates and new modules should be introduced to keep pace with technological advancements.
Encouraging a culture of continuous learning can help sustain the momentum of digital transformation.
Hands-On Training
Practical, hands-on training is often more effective than theoretical instruction.
Using real-world scenarios and case studies can help employees understand the practical applications of their newly acquired skills.
Simulations and virtual reality can also enhance hands-on learning experiences.
Monitoring and Evaluation
Regular monitoring and evaluation are crucial for assessing the effectiveness of training programs.
Feedback loops can help identify areas for improvement, ensuring that the training remains relevant and impactful.
Key performance indicators (KPIs) such as productivity metrics and employee feedback can provide valuable insights.
Case Study: Toyota’s Digital Transformation
Toyota, one of Japan’s most iconic manufacturers, provides a compelling case study in digital skills training.
The company has embraced digital transformation through initiatives like its Toyota Production System (TPS), which now incorporates advanced digital tools.
By investing in digital skills training, Toyota has been able to enhance its lean manufacturing principles, improve quality control, and boost efficiency.
Building a Digital Culture
Toyota recognized that successful digital transformation goes beyond technology implementation.
It requires building a digital culture where employees are encouraged to innovate and experiment with new tools.
This cultural shift was achieved through comprehensive training programs and leadership support.
Employee Empowerment
One of the key aspects of Toyota’s digital transformation was empowering employees at all levels to leverage digital tools.
Frontline workers received training in data analytics and machine operation, while managers were educated in advanced planning and forecasting techniques.
This holistic approach ensured that digital skills permeated every aspect of the organization.
Conclusion
As the manufacturing sector continues to evolve, digital skills training will become increasingly vital for maintaining competitive advantage.
Japanese manufacturers, renowned for their commitment to quality and efficiency, must embrace this shift to remain industry leaders.
By investing in targeted training programs, fostering a culture of continuous learning, and leveraging advanced technologies, organizations can revolutionize their production processes and achieve new heights of success.
The road to digital transformation may be fraught with challenges, but the rewards are well worth the effort.
From enhanced efficiency and improved quality control to better supplier management and increased agility, the benefits of digital skills training are manifold.
As we look to the future, it is clear that the integration of digital and traditional manufacturing skills will be the key to sustaining Japan’s manufacturing excellence.
資料ダウンロード
QCD調達購買管理クラウド「newji」は、調達購買部門で必要なQCD管理全てを備えた、現場特化型兼クラウド型の今世紀最高の購買管理システムとなります。
ユーザー登録
調達購買業務の効率化だけでなく、システムを導入することで、コスト削減や製品・資材のステータス可視化のほか、属人化していた購買情報の共有化による内部不正防止や統制にも役立ちます。
NEWJI DX
製造業に特化したデジタルトランスフォーメーション(DX)の実現を目指す請負開発型のコンサルティングサービスです。AI、iPaaS、および先端の技術を駆使して、製造プロセスの効率化、業務効率化、チームワーク強化、コスト削減、品質向上を実現します。このサービスは、製造業の課題を深く理解し、それに対する最適なデジタルソリューションを提供することで、企業が持続的な成長とイノベーションを達成できるようサポートします。
オンライン講座
製造業、主に購買・調達部門にお勤めの方々に向けた情報を配信しております。
新任の方やベテランの方、管理職を対象とした幅広いコンテンツをご用意しております。
お問い合わせ
コストダウンが利益に直結する術だと理解していても、なかなか前に進めることができない状況。そんな時は、newjiのコストダウン自動化機能で大きく利益貢献しよう!
(Β版非公開)