- お役立ち記事
- Revolutionizing Japanese Manufacturing: The Future of Planar Space Exploration in Industry
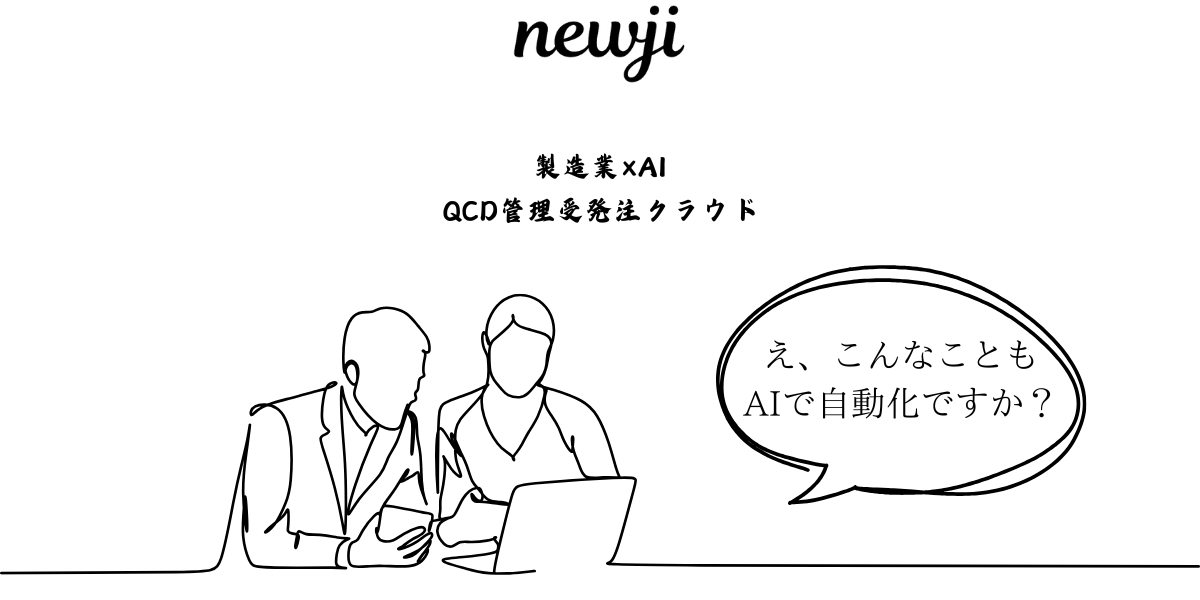
Revolutionizing Japanese Manufacturing: The Future of Planar Space Exploration in Industry
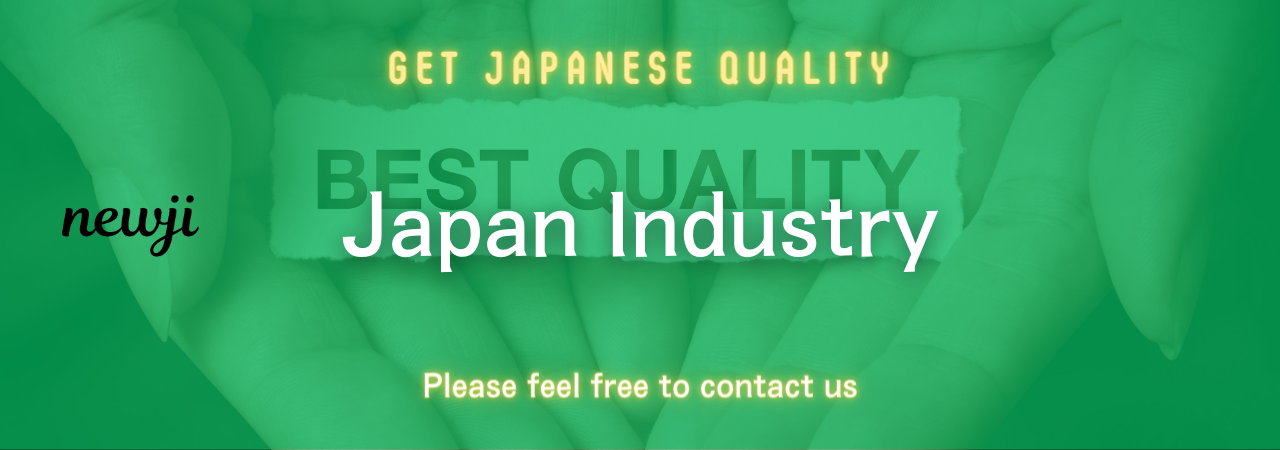
目次
Introduction
The landscape of Japanese manufacturing is ever-evolving, continuously adapting to technological advancements and global market dynamics.
One of the fascinating avenues garnering interest is planar space exploration within the industrial sector.
Planar space exploration translates to optimizing the use of surfaces within a manufacturing setup, potentially revolutionizing factory layouts, logistics, and production processes.
In this article, we will delve into how Japanese manufacturing is revolutionizing itself through planar space exploration and what this implies for the future of the industry.
The Concept of Planar Space Exploration
Defining Planar Space Exploration
Planar space exploration involves the strategic use of 2D surfaces within a 3D space, aiming to maximize efficiency and optimize resources.
In a manufacturing setting, this means efficient layout planning, effective utilization of workspaces, and minimization of waste both spatially and resource-wise.
Japanese manufacturers are well-known for their commitment to efficiency, and the planar space exploration concept is a testament to this dedication.
Historical Context
Historically, Japanese manufacturing has always been synonymous with precision and efficiency.
The introduction of techniques like the Toyota Production System (TPS) and Kaizen has set global benchmarks.
Planar space exploration can be seen as an extension of these principles, integrating modern technology to achieve unparalleled levels of productivity.
The Advantages of Planar Space Exploration
Enhanced Efficiency
Maximizing floor space usage means more streamlined workflows and less time wasted moving between stations.
This results in higher productivity and lower operational costs.
Quality Control
A well-planned workspace can significantly improve quality control.
Efficient layouts facilitate the easy monitoring of production lines, making it easier to identify and rectify defects.
Optimized Resources
Planar space exploration allows for the optimal use of materials, reducing waste.
This aligns perfectly with Japan’s philosophy of Muda (waste reduction), Mura (unevenness elimination), and Muri (overburden mitigation).
Eco-Friendly Initiatives
Sustainable practices are receiving ever-increasing importance globally.
Efficient space utilization cuts down on energy consumption, reducing the carbon footprint of manufacturing operations.
The Disadvantages
High Initial Costs
Implementing planar space exploration technologies often requires significant initial investment.
Upgrading equipment, redesigning factory layouts, and training staff can lead to substantial costs.
Complexity in Implementation
The transition from conventional systems to planar space-focused setups can be complex.
It requires meticulous planning and seamless execution to avoid disruptions in production.
Dependency on Technology
Planar space exploration relies heavily on cutting-edge technology for data collection, analysis, and implementation.
This could make the system vulnerable to technological failures or cyber-attacks.
Supplier Negotiation Techniques
Understanding the Supplier’s Perspective
Understanding the needs and constraints of your Japanese suppliers is crucial.
Most Japanese suppliers prioritize long-term relationships over short-term gains.
This can often result in favorable conditions for both parties if navigated correctly.
Building Trust
Trust is the cornerstone of any successful negotiation.
Credibility, transparency, and consistent communication go a long way in building a strong rapport with Japanese suppliers.
Leverage Quality as a Priority
Japanese suppliers often place a high emphasis on quality.
Presenting your commitment to quality can often result in favorable terms and conditions during negotiations.
Flexible Payment Terms
Offering flexible payment terms can sometimes tilt the negotiations in your favor.
Japanese suppliers appreciate flexibility as it indicates a commitment to long-term collaboration.
Market Conditions
Current Landscape
The Japanese manufacturing sector is currently navigating several challenges, including labor shortages and increasing material costs.
These conditions are shaping the way planar space exploration is being adopted.
Technological Advancements
With the rise of Industry 4.0, technologies like IoT, AI, and robotics are being integrated into manufacturing processes.
These advancements are not only simplifying the implementation of planar space exploration but also are making it more efficient.
Global Competition
Competition from neighboring countries like China and South Korea is pushing Japanese manufacturers to innovate rapidly.
Planar space exploration offers a competitive edge by enhancing efficiency and reducing costs.
Best Practices
Adopting a Holistic Approach
For successful implementation, it’s imperative to adopt a holistic approach.
This means considering every aspect of the manufacturing process, from procurement and production to logistics and quality control.
Employee Training and Involvement
Employees should be adequately trained and involved in the planning and implementation stages.
Their feedback can provide valuable insights that may be overlooked by management.
Continuous Monitoring and Improvement
The principles of Kaizen hold true even in planar space exploration.
Continuous monitoring and incremental improvements can lead to sustained excellence.
Leveraging Technology
Automated systems, IoT, and AI can simplify the complexities involved in planar space exploration.
Utilizing these technological advancements can streamline the entire process, ensuring more efficient use of space and resources.
Implementing Planar Space Exploration
Initial Assessment
Begin with a comprehensive assessment of the current manufacturing setup.
Identify inefficiencies and potential areas for improvement.
Developing a Strategy
Develop a detailed strategy focusing on layout changes, equipment upgrades, and workflow optimizations.
This strategy should align with your business goals and operational capabilities.
Pilot Testing
Before full-scale implementation, conduct pilot tests to gauge the effectiveness of the proposed changes.
This allows you to make necessary adjustments without disrupting the entire production line.
Full-Scale Rollout
After successful pilot testing, proceed with the full-scale rollout.
Ensure that all employees are on board and adequately trained to handle the new system.
Future Prospects
Technological Integration
As technology continues to evolve, the scope for planar space exploration within Japanese manufacturing will expand.
Future developments like machine learning and advanced analytics will enable even more precise and efficient space utilization.
Global Implications
Japan’s success in planar space exploration can serve as a model for manufacturing sectors worldwide.
The principles and technologies could be adapted to fit various industrial contexts, promoting global manufacturing efficiency.
Sustainability Goals
Sustainable manufacturing practices are becoming increasingly important in today’s world.
Planar space exploration aligns with these goals by optimizing resources and reducing waste.
Continuous Innovation
The future of planar space exploration in Japanese manufacturing will be marked by continuous innovation.
As new challenges and opportunities arise, Japanese manufacturers will need to adapt and evolve, maintaining their competitive edge on the global stage.
Conclusion
Planar space exploration holds immense potential to revolutionize Japanese manufacturing.
By leveraging this concept, manufacturers can achieve higher efficiency, improved quality control, and significant cost reductions.
However, implementing this concept comes with its own set of challenges, including high initial costs and complexities in execution.
By adopting best practices and leveraging technological advancements, these challenges can be effectively navigated.
The future of planar space exploration in Japanese manufacturing promises an exciting blend of tradition and innovation, setting new benchmarks for global manufacturing excellence.
資料ダウンロード
QCD調達購買管理クラウド「newji」は、調達購買部門で必要なQCD管理全てを備えた、現場特化型兼クラウド型の今世紀最高の購買管理システムとなります。
ユーザー登録
調達購買業務の効率化だけでなく、システムを導入することで、コスト削減や製品・資材のステータス可視化のほか、属人化していた購買情報の共有化による内部不正防止や統制にも役立ちます。
NEWJI DX
製造業に特化したデジタルトランスフォーメーション(DX)の実現を目指す請負開発型のコンサルティングサービスです。AI、iPaaS、および先端の技術を駆使して、製造プロセスの効率化、業務効率化、チームワーク強化、コスト削減、品質向上を実現します。このサービスは、製造業の課題を深く理解し、それに対する最適なデジタルソリューションを提供することで、企業が持続的な成長とイノベーションを達成できるようサポートします。
オンライン講座
製造業、主に購買・調達部門にお勤めの方々に向けた情報を配信しております。
新任の方やベテランの方、管理職を対象とした幅広いコンテンツをご用意しております。
お問い合わせ
コストダウンが利益に直結する術だと理解していても、なかなか前に進めることができない状況。そんな時は、newjiのコストダウン自動化機能で大きく利益貢献しよう!
(Β版非公開)