- お役立ち記事
- Revolutionizing Japanese Manufacturing: The Future of Tuck OEM Solutions
月間76,176名の
製造業ご担当者様が閲覧しています*
*2025年3月31日現在のGoogle Analyticsのデータより
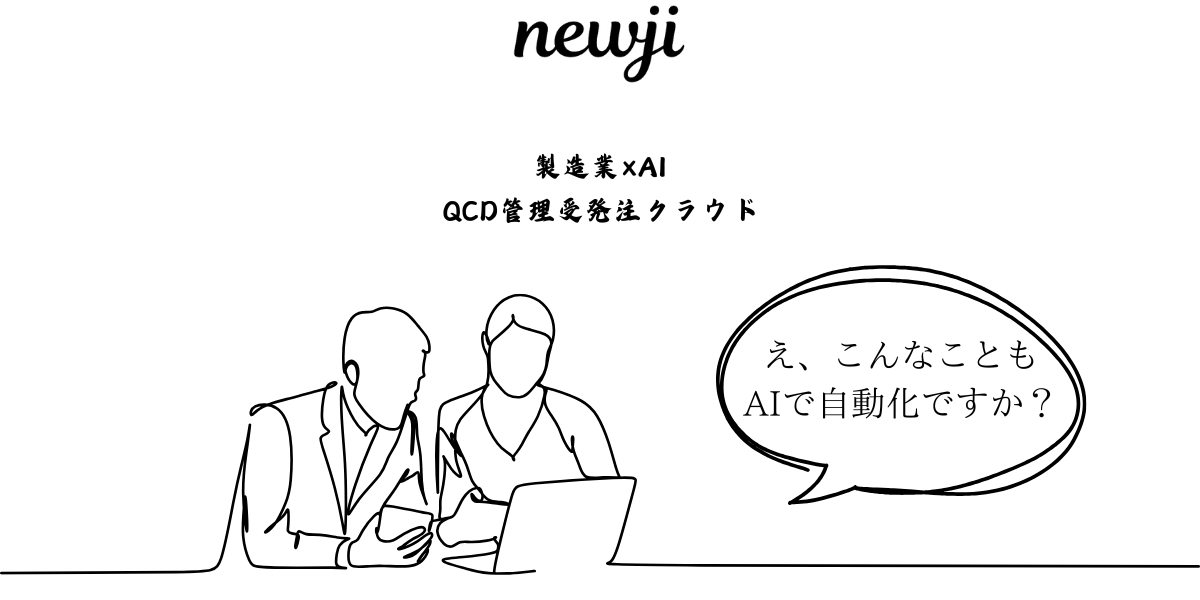
Revolutionizing Japanese Manufacturing: The Future of Tuck OEM Solutions
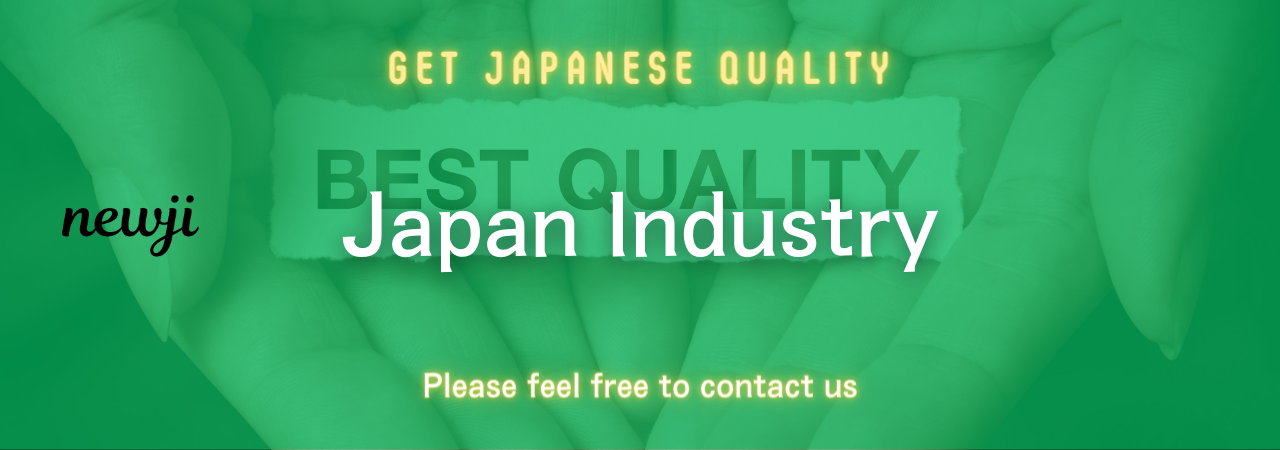
目次
Introduction to Tuck OEM Solutions in Japanese Manufacturing
Japan has long been recognized for its excellence in manufacturing, driven by a culture of precision, quality, and continuous improvement. Among the various strategies that have contributed to this success, Original Equipment Manufacturing (OEM) solutions stand out as a pivotal element in revolutionizing the industry. Tuck OEM solutions, in particular, have emerged as a frontrunner, offering innovative approaches that align with the dynamic demands of global markets. This article delves into the future of Tuck OEM solutions, exploring their impact on procurement and purchasing, supplier negotiations, market conditions, and best practices within the Japanese manufacturing sector.
The Evolution of Tuck OEM Solutions
Understanding Tuck OEM
Tuck OEM solutions refer to a comprehensive approach where manufacturers not only produce components or complete products based on another company’s specifications but also integrate advanced technologies and processes to enhance overall efficiency and quality. This model goes beyond traditional OEM practices by emphasizing collaboration, innovation, and adaptability.
Historical Context
The roots of OEM can be traced back to the post-World War II era, where Japanese manufacturers began collaborating with foreign companies to rebuild and modernize their industries. Over the decades, this partnership has evolved, with Japanese firms adopting lean manufacturing, Just-In-Time (JIT) production, and Total Quality Management (TQM) principles to refine OEM processes. Tuck OEM solutions represent the latest iteration of this evolution, incorporating digital transformation and smart manufacturing techniques to stay ahead in a competitive global landscape.
Advantages of Tuck OEM Solutions
Enhanced Quality Control
Japanese manufacturers are renowned for their stringent quality control measures. Tuck OEM solutions leverage this expertise to ensure that every component meets high standards, reducing defects and enhancing product reliability. Advanced quality assurance tools and methodologies are integrated into the OEM process, facilitating real-time monitoring and continuous improvement.
Cost Efficiency
By optimizing manufacturing processes and leveraging economies of scale, Tuck OEM solutions can significantly reduce production costs. Efficient procurement and purchasing strategies ensure that materials are sourced at competitive prices without compromising quality. Additionally, streamlined logistics and inventory management minimize overhead expenses, contributing to overall cost savings.
Flexibility and Scalability
Tuck OEM solutions offer greater flexibility in production, allowing manufacturers to adapt quickly to changing market demands. Whether scaling up production to meet increased demand or customizing products to suit specific client needs, the OEM framework supports agile responses. This scalability is crucial in today’s fast-paced market environment, where consumer preferences can shift rapidly.
Access to Advanced Technologies
Japanese manufacturers are at the forefront of technological innovation. Tuck OEM solutions provide access to cutting-edge technologies such as automation, robotics, and Industry 4.0 practices. These advancements enhance production efficiency, reduce human error, and enable the creation of sophisticated products that meet modern standards.
Disadvantages and Challenges
Cultural and Communication Barriers
One of the significant challenges in Tuck OEM solutions is navigating cultural differences and communication barriers between Japanese manufacturers and their international partners. Misunderstandings can arise from varying business etiquettes, language differences, and differing expectations, potentially hindering collaboration and efficiency.
Dependency Risks
Relying heavily on OEM partners can create dependency risks. Any disruption in the supplier’s operations, such as natural disasters, economic downturns, or political instability, can adversely affect the entire supply chain. Diversifying suppliers and implementing robust risk management strategies are essential to mitigate these risks.
Intellectual Property Concerns
Protecting intellectual property (IP) is a critical concern in OEM partnerships. Sharing proprietary designs and technologies with OEM partners requires stringent IP protection measures to prevent unauthorized use or replication. Establishing clear contracts and legal frameworks is necessary to safeguard intellectual assets.
Supply Chain Complexity
Managing a global supply chain introduces complexity in logistics, inventory management, and quality control. Coordinating multiple suppliers across different regions demands sophisticated systems and processes to ensure seamless operations. This complexity can increase operational costs and require specialized expertise to manage effectively.
Supplier Negotiation Techniques
Building Strong Relationships
In Japanese business culture, relationships are paramount. Building trust and fostering long-term partnerships with suppliers is essential for successful negotiations. Regular communication, site visits, and mutual respect contribute to stronger relationships, enabling more favorable negotiation outcomes.
Understanding Supplier Motivations
Effective negotiation requires a deep understanding of the supplier’s motivations and constraints. By identifying what drives the supplier—be it cost reduction, market expansion, or technological advancement—negotiators can craft proposals that align with the supplier’s interests, facilitating win-win agreements.
Leveraging Data and Analytics
Utilizing data and analytics in negotiations can provide valuable insights into market trends, pricing benchmarks, and supplier performance. Data-driven strategies enable more informed decision-making, strengthening the negotiating position and ensuring that agreements are based on objective information.
Implementing Collaborative Negotiation
Collaborative negotiation approaches, where both parties work together to find mutually beneficial solutions, are effective in OEM contexts. This method fosters cooperation, reduces adversarial tensions, and leads to more sustainable agreements that support long-term partnerships.
Market Conditions and Trends
Globalization and Supply Chain Diversification
Globalization continues to shape the manufacturing landscape, driving the need for diversified supply chains. Japanese manufacturers adopting Tuck OEM solutions must navigate the complexities of international trade, including tariffs, trade agreements, and geopolitical tensions. Diversifying suppliers across different regions can enhance resilience and mitigate risks associated with geopolitical uncertainties.
Digital Transformation and Industry 4.0
The integration of digital technologies is transforming manufacturing processes. Industry 4.0, characterized by automation, data exchange, and cyber-physical systems, is becoming a cornerstone of modern OEM solutions. Japanese manufacturers are leveraging these technologies to enhance production efficiency, improve quality control, and enable real-time monitoring and decision-making.
Sustainability and Green Manufacturing
Sustainability is increasingly influencing manufacturing practices. Consumers and regulators are demanding environmentally friendly products and processes. Tuck OEM solutions are evolving to incorporate green manufacturing practices, such as reducing waste, minimizing energy consumption, and using sustainable materials. This shift not only meets regulatory requirements but also appeals to environmentally conscious consumers.
Customization and Personalization
The demand for customized and personalized products is on the rise. Tuck OEM solutions are adapting to this trend by offering greater flexibility in production processes. Advanced manufacturing techniques, such as 3D printing and modular production systems, enable the creation of tailored products that meet specific customer needs without significantly increasing costs.
Best Practices in Tuck OEM Solutions
Implementing Lean Manufacturing Principles
Lean manufacturing focuses on minimizing waste and optimizing efficiency. Applying lean principles in Tuck OEM solutions involves streamlining processes, reducing inventory, and enhancing workflow. This approach not only lowers production costs but also improves delivery times and product quality.
Embracing Continuous Improvement
A culture of continuous improvement, or Kaizen, is essential for the success of OEM partnerships. Regularly reviewing and refining processes, soliciting feedback from all stakeholders, and fostering an environment of innovation are key to maintaining high standards and adapting to evolving market demands.
Investing in Technology and Automation
Investing in advanced technologies and automation is critical for staying competitive. Automated systems enhance precision, reduce human error, and increase production speed. Additionally, technologies such as the Internet of Things (IoT) and Artificial Intelligence (AI) provide valuable data insights that drive strategic decision-making and process optimization.
Ensuring Robust Quality Control
Maintaining robust quality control systems is non-negotiable in OEM manufacturing. Implementing comprehensive quality management systems, conducting regular audits, and fostering a quality-centric culture ensure that products consistently meet or exceed standards. Leveraging technologies like machine vision and real-time monitoring systems further enhance quality assurance efforts.
Enhancing Communication and Collaboration
Effective communication and collaboration are vital for successful OEM partnerships. Utilizing collaborative platforms, regular meetings, and transparent communication channels ensures that all parties are aligned and informed. This transparency fosters trust, facilitates problem-solving, and enhances overall partnership effectiveness.
Future Outlook of Tuck OEM Solutions
Integration of Artificial Intelligence
Artificial Intelligence (AI) is set to play a significant role in the future of Tuck OEM solutions. AI-driven predictive analytics can anticipate market trends, optimize supply chain management, and enhance quality control. Machine learning algorithms can also improve production processes by identifying inefficiencies and suggesting improvements.
Expansion of Smart Manufacturing
Smart manufacturing, characterized by interconnected systems and real-time data exchange, will become increasingly prevalent. Tuck OEM solutions will leverage these advancements to create more responsive and adaptive manufacturing environments. Smart factories equipped with sensors and IoT devices will enable seamless integration and automation, driving higher productivity and flexibility.
Emphasis on Sustainable Practices
Sustainability will continue to shape OEM strategies. Future Tuck OEM solutions will prioritize eco-friendly materials, energy-efficient processes, and waste reduction techniques. Manufacturers will adopt circular economy principles, focusing on reusing and recycling materials to minimize environmental impact and promote long-term sustainability.
Customization Through Advanced Manufacturing Techniques
Advanced manufacturing techniques, such as additive manufacturing and flexible production systems, will enable greater customization. Tuck OEM solutions will support the creation of highly personalized products without sacrificing efficiency or escalating costs. This capability will cater to the growing consumer demand for unique and tailored products.
Global Collaboration and Innovation
Global collaboration will drive innovation in Tuck OEM solutions. Cross-border partnerships and knowledge sharing will accelerate technological advancements and process improvements. Japanese manufacturers will continue to collaborate with international partners to harness diverse expertise and foster a culture of innovation, ensuring sustained competitiveness in the global market.
Conclusion
Tuck OEM solutions represent a transformative approach in Japanese manufacturing, blending traditional excellence with modern innovation. As global markets evolve, the ability to adapt through advanced technologies, sustainable practices, and robust partnerships will determine the success of OEM strategies. By embracing these changes and implementing best practices, Japanese manufacturers can continue to lead the way in delivering high-quality, cost-effective, and customized products. The future of Tuck OEM solutions is poised to redefine manufacturing paradigms, offering unparalleled opportunities for growth, efficiency, and innovation in the ever-competitive global landscape.
資料ダウンロード
QCD管理受発注クラウド「newji」は、受発注部門で必要なQCD管理全てを備えた、現場特化型兼クラウド型の今世紀最高の受発注管理システムとなります。
ユーザー登録
受発注業務の効率化だけでなく、システムを導入することで、コスト削減や製品・資材のステータス可視化のほか、属人化していた受発注情報の共有化による内部不正防止や統制にも役立ちます。
NEWJI DX
製造業に特化したデジタルトランスフォーメーション(DX)の実現を目指す請負開発型のコンサルティングサービスです。AI、iPaaS、および先端の技術を駆使して、製造プロセスの効率化、業務効率化、チームワーク強化、コスト削減、品質向上を実現します。このサービスは、製造業の課題を深く理解し、それに対する最適なデジタルソリューションを提供することで、企業が持続的な成長とイノベーションを達成できるようサポートします。
製造業ニュース解説
製造業、主に購買・調達部門にお勤めの方々に向けた情報を配信しております。
新任の方やベテランの方、管理職を対象とした幅広いコンテンツをご用意しております。
お問い合わせ
コストダウンが利益に直結する術だと理解していても、なかなか前に進めることができない状況。そんな時は、newjiのコストダウン自動化機能で大きく利益貢献しよう!
(β版非公開)