- お役立ち記事
- “Revolutionizing Japanese Manufacturing: The Impact of Autonomous Mobile Robots (AMR) on Efficiency and Innovation”
月間76,176名の
製造業ご担当者様が閲覧しています*
*2025年3月31日現在のGoogle Analyticsのデータより
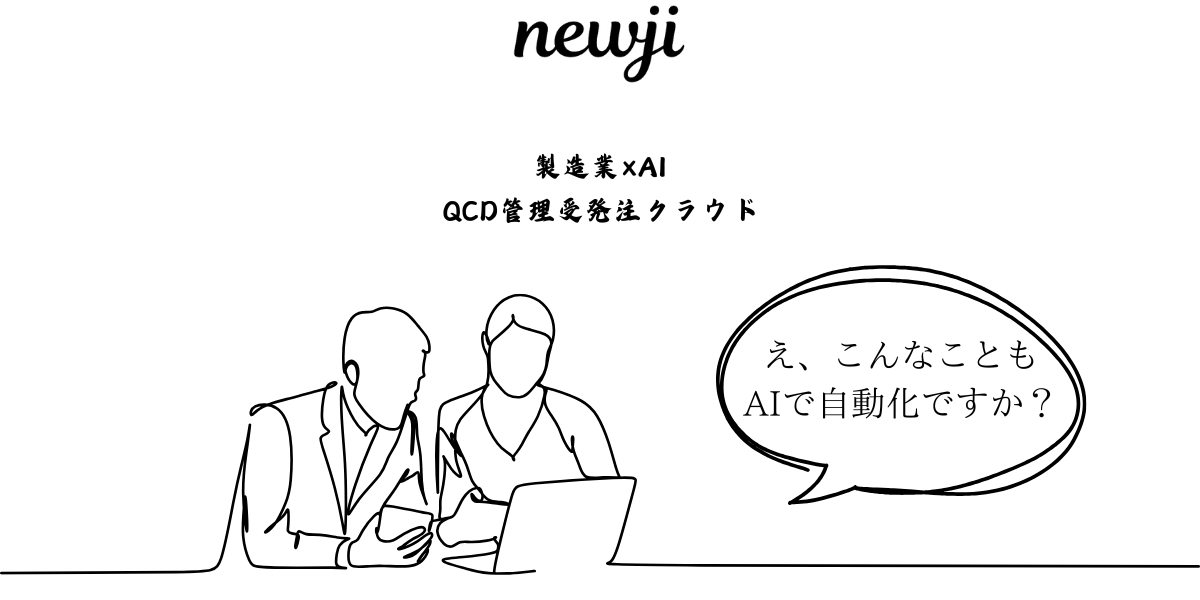
“Revolutionizing Japanese Manufacturing: The Impact of Autonomous Mobile Robots (AMR) on Efficiency and Innovation”
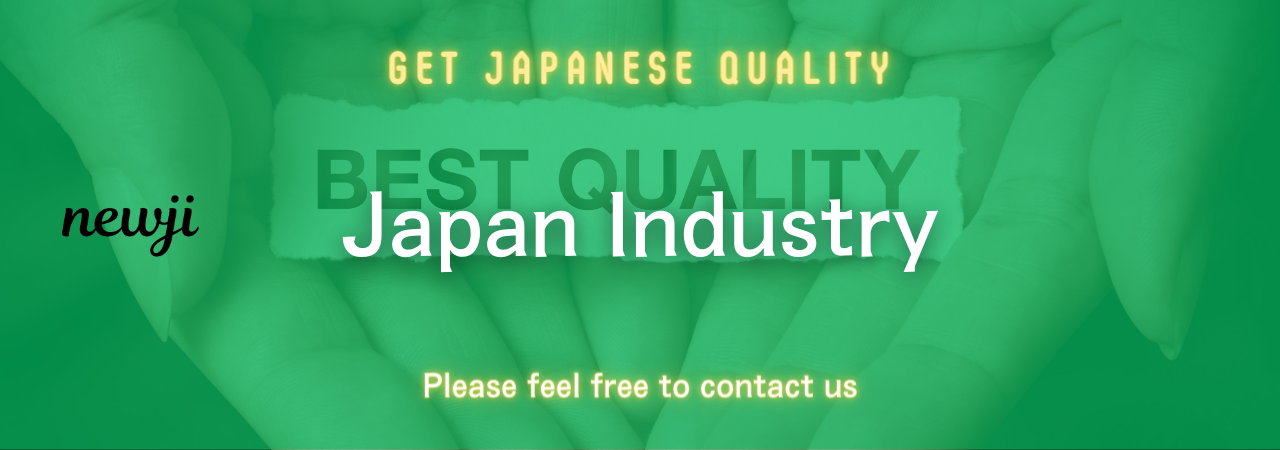
目次
The Evolution of Japanese Manufacturing
Historical Overview
Japanese manufacturing has long been synonymous with quality and precision. From the post-war era, Japan focused on rebuilding its industrial base with a strong emphasis on innovation and efficiency. Industries such as automotive and electronics became global leaders, setting standards for excellence. The adoption of lean manufacturing principles and continuous improvement strategies, known as Kaizen, played a pivotal role in this success. Over the decades, Japanese manufacturers have consistently pushed the boundaries of technology to enhance productivity and maintain competitive advantage in the global market.
The Shift Towards Automation
In recent years, there has been a significant shift towards automation within Japanese manufacturing sectors. This transformation is driven by the need to address labor shortages, increase production efficiency, and maintain high-quality standards. Automation technologies, including robotics and artificial intelligence, have been integrated into various stages of the manufacturing process. This shift not only streamlines operations but also allows for greater flexibility and scalability in production. The integration of advanced automation systems has enabled Japanese manufacturers to sustain their reputation for quality while meeting the demands of a rapidly evolving market.
Understanding Autonomous Mobile Robots (AMR)
What are AMRs?
Autonomous Mobile Robots (AMRs) are advanced robotic systems designed to navigate and perform tasks in dynamic environments without human intervention. Unlike traditional robots that operate in fixed locations, AMRs are equipped with sophisticated sensors, software, and navigation capabilities that allow them to move freely within a facility. These robots can transport materials, assist in assembly processes, and manage inventory, among other functions. AMRs are increasingly being adopted in manufacturing settings to enhance operational efficiency and support human workers by taking on repetitive and physically demanding tasks.
Key Technologies Behind AMRs
The functionality of AMRs is powered by several key technologies. Advanced sensors such as LiDAR, cameras, and ultrasonic devices enable these robots to perceive their surroundings accurately. Machine learning algorithms and artificial intelligence allow AMRs to make real-time decisions and adapt to changing environments. Robust navigation systems, including simultaneous localization and mapping (SLAM), ensure precise movement and obstacle avoidance. Additionally, connectivity technologies like the Internet of Things (IoT) facilitate seamless communication between AMRs and other systems within the manufacturing ecosystem. These technologies collectively empower AMRs to perform complex tasks efficiently and reliably.
Impact of AMRs on Manufacturing Efficiency
Streamlining Production Processes
AMRs play a crucial role in streamlining production processes by automating the movement of materials and components across different stages of manufacturing. This automation reduces the time and effort required for manual material handling, thereby accelerating production cycles. By ensuring timely delivery of materials to assembly lines, AMRs minimize downtime and enhance overall workflow efficiency. Furthermore, the ability of AMRs to operate continuously without breaks increases the throughput of manufacturing operations, contributing to higher productivity levels.
Reducing Operational Costs
The integration of AMRs in manufacturing facilities leads to significant cost savings in various ways. By automating routine tasks, companies can reduce the reliance on manual labor, lowering labor costs. AMRs also minimize errors associated with manual material handling, which can result in cost savings related to waste reduction and quality control. Additionally, the predictable and efficient operation of AMRs contributes to lower maintenance and operational expenses compared to traditional machinery. Over time, the initial investment in AMR technology is offset by the ongoing cost reductions and improved financial performance.
Enhancing Supply Chain Management
AMRs enhance supply chain management by providing real-time tracking and efficient handling of materials. These robots can seamlessly integrate with inventory management systems, ensuring accurate monitoring of stock levels and timely replenishment of supplies. By automating the transport of materials between suppliers, warehouses, and production lines, AMRs reduce delays and improve the overall responsiveness of the supply chain. This enhanced coordination results in better alignment between supply and demand, reducing the risk of shortages or overstock situations and contributing to more efficient supply chain operations.
Driving Innovation in Japanese Manufacturing
Facilitating Research and Development
The adoption of AMRs in Japanese manufacturing fosters innovation by freeing up human resources to focus on research and development (R&D). With robots handling repetitive and time-consuming tasks, engineers and designers can dedicate more time to developing new products and improving existing processes. AMRs also generate valuable data that can be analyzed to identify areas for innovation and process optimization. This data-driven approach enables continuous improvement and the development of cutting-edge manufacturing techniques, maintaining Japan’s position as a leader in technological advancements.
Fostering a Culture of Continuous Improvement
AMRs contribute to a culture of continuous improvement by providing manufacturers with the tools to constantly evaluate and enhance their operations. The data collected by AMRs on production metrics allows companies to identify inefficiencies and implement targeted improvements. This iterative process of assessment and enhancement aligns with the Japanese philosophy of Kaizen, promoting ongoing excellence and adaptability in manufacturing practices. By embracing AMR technology, Japanese manufacturers reinforce their commitment to innovation and operational excellence, ensuring sustained competitiveness in the global marketplace.
Advantages of Integrating AMRs in Manufacturing
Increased Productivity
One of the primary advantages of integrating AMRs is the substantial increase in productivity. AMRs can operate around the clock without the need for breaks, significantly boosting production capacity. Their ability to perform tasks swiftly and accurately minimizes bottlenecks and accelerates the manufacturing process. Additionally, AMRs can be reprogrammed to handle different tasks as production needs evolve, providing manufacturers with the flexibility to adapt quickly to changing demands without compromising on output levels.
Improved Quality Control
AMRs enhance quality control by ensuring consistent and precise execution of tasks. Automated material handling reduces the likelihood of human error, leading to higher accuracy in the production process. AMRs can also be equipped with sensors to monitor environmental conditions and detect anomalies in real-time, allowing for immediate corrective actions. This proactive approach to quality control helps maintain high standards, reduce defect rates, and ensure that products meet stringent quality requirements, thereby reinforcing the reputation of Japanese manufacturing excellence.
Flexibility and Scalability
The versatility of AMRs allows manufacturers to scale their operations efficiently in response to market demands. AMRs can be easily reconfigured or redeployed to new areas of the facility as production requirements change. This flexibility is particularly valuable in industries with fluctuating demand or those involved in the production of diverse product lines. Additionally, the modular nature of AMR systems enables seamless expansion, allowing manufacturers to incrementally increase their automation capabilities without significant disruptions to existing operations.
Challenges and Disadvantages
High Initial Investment
One of the significant challenges associated with integrating AMRs into manufacturing operations is the high initial investment required. The cost of purchasing and implementing advanced robotic systems can be substantial, particularly for small and medium-sized enterprises. Additionally, there may be expenses related to infrastructure upgrades, training, and maintenance. While the long-term benefits often outweigh the initial costs, securing the necessary capital can be a barrier for some manufacturers looking to adopt AMR technology.
Integration with Existing Systems
Integrating AMRs with existing manufacturing systems and processes can present technical challenges. Compatibility issues may arise when attempting to connect new robotic systems with legacy equipment or software platforms. Ensuring seamless communication and data exchange between AMRs and other machinery is crucial for achieving optimal performance. Manufacturers may need to invest in additional resources or seek specialized expertise to facilitate smooth integration, which can add to the complexity and cost of implementing AMR technology.
Workforce Adaptation
The introduction of AMRs into the manufacturing environment necessitates changes in workforce dynamics. Employees may need to acquire new skills to operate and maintain the robotic systems, requiring comprehensive training programs. There may also be concerns about job displacement as robots take over certain tasks. Addressing these workforce adaptation challenges involves fostering a collaborative environment where human workers and robots complement each other’s strengths, and providing opportunities for employees to engage in more value-added roles within the organization.
Procurement and Purchasing Considerations
Selecting the Right AMR Suppliers
Choosing the appropriate AMR suppliers is critical for successful implementation. Manufacturers should evaluate suppliers based on their technological capabilities, experience in the industry, and the quality of their products. It is essential to consider factors such as the supplier’s track record, customer support services, and ability to provide customized solutions tailored to specific manufacturing needs. Engaging with reputable suppliers who offer reliable and state-of-the-art AMR systems can significantly influence the effectiveness and longevity of the automation strategy.
Evaluating Supplier Capabilities
When assessing potential AMR suppliers, it is important to thoroughly evaluate their capabilities. This includes examining the technical specifications of their robots, the flexibility and scalability of their solutions, and their integration capabilities with existing systems. Additionally, manufacturers should consider the supplier’s ability to provide ongoing support, including maintenance, upgrades, and troubleshooting. Visiting supplier facilities, reviewing case studies, and seeking references from other clients can provide valuable insights into the supplier’s performance and reliability.
Negotiation Techniques with Japanese Suppliers
Negotiating with Japanese suppliers requires an understanding of Japanese business culture and practices. Building strong relationships based on trust and mutual respect is fundamental. Manufacturers should approach negotiations with a collaborative mindset, focusing on long-term partnerships rather than short-term gains. Clear communication, patience, and attention to detail are crucial during negotiations. It is also beneficial to understand the supplier’s perspective and constraints, enabling more effective and harmonious negotiations that can lead to favorable terms and successful collaborations.
Market Conditions for AMRs in Japan
Current Market Trends
The Japanese AMR market is experiencing robust growth, driven by the increasing demand for automation in manufacturing and other industries. Key trends include the adoption of collaborative robots that work alongside human workers, the integration of AI and machine learning to enhance AMR capabilities, and the development of specialized robots for specific industrial applications. Additionally, there is a growing emphasis on sustainability and energy efficiency in AMR design, aligning with broader environmental goals within the manufacturing sector.
Future Outlook
The future of the AMR market in Japan looks promising, with continued advancements in robotics technology expected to drive further adoption. Innovations in autonomous navigation, artificial intelligence, and sensor technologies will enhance the functionality and efficiency of AMRs, making them even more integral to manufacturing operations. The expansion of Industry 4.0 initiatives and smart factory concepts will also support the integration of AMRs into more complex and interconnected manufacturing ecosystems. As these trends evolve, Japanese manufacturers are well-positioned to leverage AMR technology to maintain their competitive edge globally.
Best Practices for Implementing AMRs
Strategic Planning
Successful implementation of AMRs starts with strategic planning. Manufacturers should clearly define their automation goals, identify the areas of operation that will benefit most from AMR integration, and develop a comprehensive implementation roadmap. This planning process should include an assessment of current processes, a cost-benefit analysis, and the establishment of key performance indicators (KPIs) to measure the success of the AMR deployment. Engaging stakeholders from different departments ensures that the automation strategy aligns with the overall business objectives and operational needs.
Employee Training and Development
Investing in employee training and development is essential for maximizing the benefits of AMR integration. Providing comprehensive training programs helps employees acquire the necessary skills to operate, maintain, and collaborate with AMRs. This not only enhances workforce competency but also fosters a positive attitude towards automation. Encouraging continuous learning and offering opportunities for professional growth can mitigate resistance to change and promote a culture of innovation within the organization.
Continuous Monitoring and Evaluation
Continuous monitoring and evaluation are critical to ensuring the ongoing effectiveness of AMR systems. Manufacturers should regularly assess the performance of AMRs against established KPIs, identify any operational bottlenecks, and implement necessary adjustments to optimize performance. Utilizing data analytics and real-time monitoring tools can provide valuable insights into system performance and facilitate proactive maintenance. By maintaining a vigilant approach to monitoring, manufacturers can ensure that AMRs continue to deliver maximum value and adapt to evolving manufacturing requirements.
Case Studies: Successful AMR Integration
Example 1
A leading Japanese automotive manufacturer implemented AMRs to streamline its assembly line operations. By automating the material transport between different stages of the assembly process, the company reduced manual labor costs and increased production speed. The AMRs were equipped with advanced navigation systems, allowing them to operate seamlessly alongside human workers without disrupting workflow. As a result, the manufacturer achieved a 20% increase in production efficiency and significantly minimized production downtime, reinforcing its position in the competitive automotive market.
Example 2
A major electronics manufacturer in Japan integrated AMRs into its supply chain management system. The AMRs were used to handle the movement of components from storage to production areas, enhancing inventory management and reducing lead times. The real-time data provided by the AMRs enabled better forecasting and inventory planning, leading to a 15% reduction in inventory holding costs. Additionally, the automation of material handling allowed the company to allocate more resources to research and development, fostering innovation and the development of new electronic products.
Conclusion
The integration of Autonomous Mobile Robots is revolutionizing Japanese manufacturing by significantly enhancing efficiency and driving innovation. AMRs streamline production processes, reduce operational costs, and improve supply chain management, contributing to increased productivity and quality control. While challenges such as high initial investment and workforce adaptation exist, the long-term benefits of AMR adoption far outweigh the drawbacks. By carefully selecting suppliers, understanding market conditions, and following best practices for implementation, Japanese manufacturers can successfully leverage AMR technology to maintain their competitive edge. As the manufacturing landscape continues to evolve, AMRs will play an increasingly vital role in ensuring that Japanese industries remain at the forefront of global manufacturing excellence.
資料ダウンロード
QCD管理受発注クラウド「newji」は、受発注部門で必要なQCD管理全てを備えた、現場特化型兼クラウド型の今世紀最高の受発注管理システムとなります。
ユーザー登録
受発注業務の効率化だけでなく、システムを導入することで、コスト削減や製品・資材のステータス可視化のほか、属人化していた受発注情報の共有化による内部不正防止や統制にも役立ちます。
NEWJI DX
製造業に特化したデジタルトランスフォーメーション(DX)の実現を目指す請負開発型のコンサルティングサービスです。AI、iPaaS、および先端の技術を駆使して、製造プロセスの効率化、業務効率化、チームワーク強化、コスト削減、品質向上を実現します。このサービスは、製造業の課題を深く理解し、それに対する最適なデジタルソリューションを提供することで、企業が持続的な成長とイノベーションを達成できるようサポートします。
製造業ニュース解説
製造業、主に購買・調達部門にお勤めの方々に向けた情報を配信しております。
新任の方やベテランの方、管理職を対象とした幅広いコンテンツをご用意しております。
お問い合わせ
コストダウンが利益に直結する術だと理解していても、なかなか前に進めることができない状況。そんな時は、newjiのコストダウン自動化機能で大きく利益貢献しよう!
(β版非公開)