- お役立ち記事
- “Revolutionizing Japanese Manufacturing: The Impact of High-Level Synthesis Circuit Design”
月間77,185名の
製造業ご担当者様が閲覧しています*
*2025年2月28日現在のGoogle Analyticsのデータより
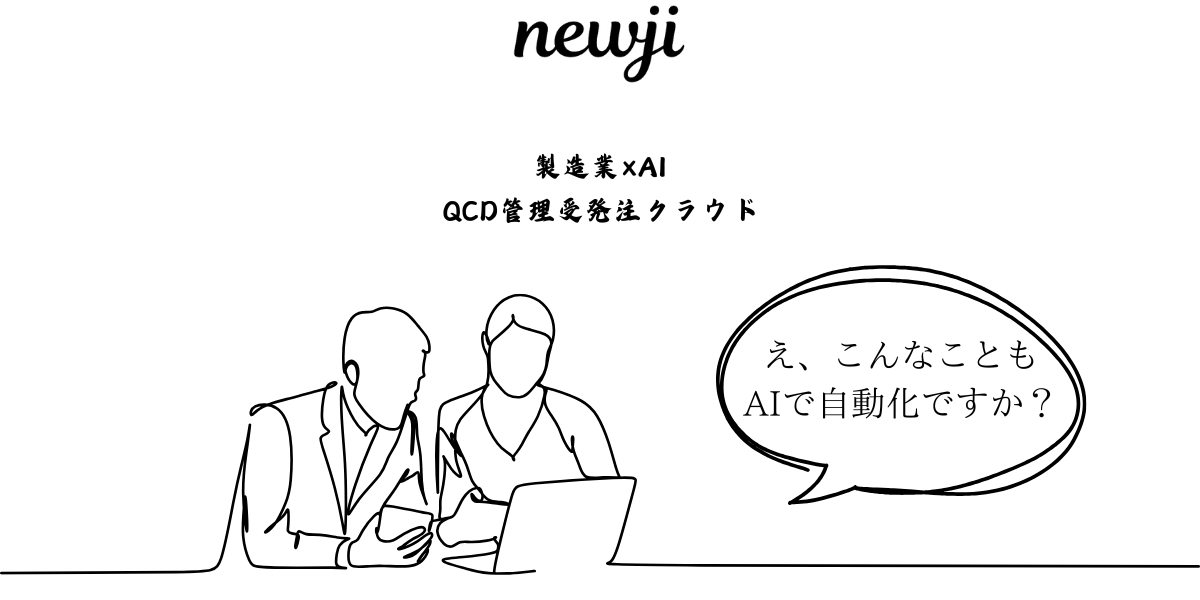
“Revolutionizing Japanese Manufacturing: The Impact of High-Level Synthesis Circuit Design”
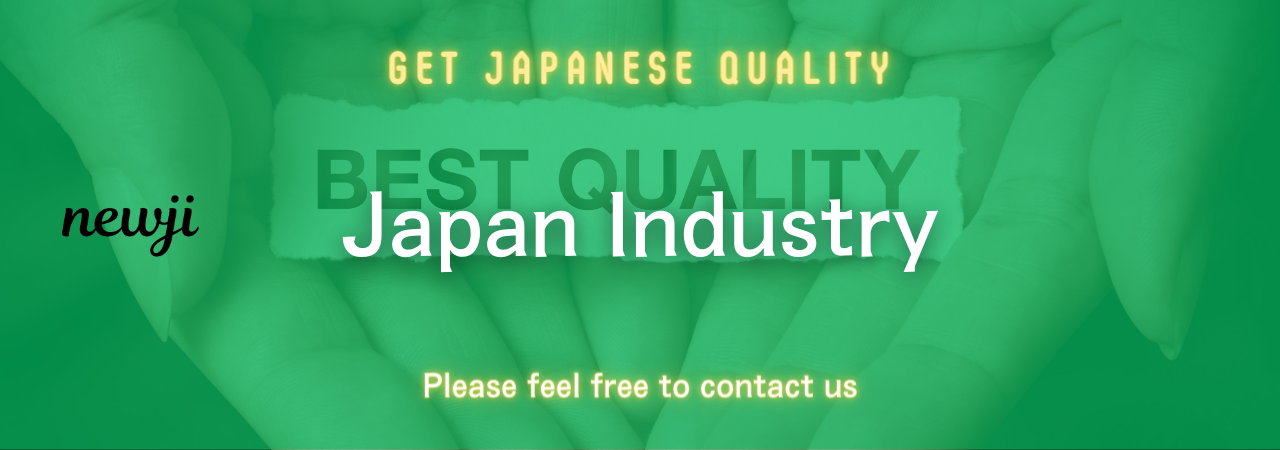
目次
Introduction
Japanese manufacturing has long been synonymous with precision, quality, and innovation. In recent years, the integration of advanced technologies has further cemented Japan’s position as a global leader in the manufacturing sector. One such technological advancement is High-Level Synthesis (HLS) circuit design. This article explores the transformative impact of HLS on Japanese manufacturing, particularly focusing on procurement and purchasing practices, supplier negotiations, market conditions, and best practices. By delving into these areas, we aim to provide a comprehensive understanding of how HLS is revolutionizing the manufacturing landscape in Japan.
Understanding High-Level Synthesis Circuit Design
What is High-Level Synthesis?
High-Level Synthesis is an automated process that converts high-level programming languages, such as C or C++, into hardware description languages (HDLs) like Verilog or VHDL. This process accelerates the design of digital circuits by allowing engineers to work at a higher abstraction level, thereby reducing design time and increasing efficiency.
Importance in Modern Manufacturing
In the realm of manufacturing, HLS plays a crucial role in the development of complex integrated circuits (ICs) used in various applications, from automotive electronics to consumer devices. By enabling rapid design iterations and facilitating easier modifications, HLS helps manufacturers keep pace with the fast-evolving technological landscape.
The Impact of HLS on Procurement and Purchasing
Streamlining the Procurement Process
The adoption of HLS in circuit design significantly streamlines the procurement process. With faster design cycles, the time between product conception and market entry is reduced. This allows procurement teams to plan and execute purchasing strategies more effectively, ensuring that components are sourced in a timely manner to meet production schedules.
Cost Efficiency
High-Level Synthesis contributes to cost efficiency in procurement by minimizing the need for extensive manual design work. The reduction in design time translates to lower labor costs and decreased time-to-market, enabling manufacturers to allocate resources more strategically across the procurement pipeline.
Enhancing Supplier Relationships
HLS fosters stronger relationships with suppliers by enabling more predictable and transparent procurement processes. Suppliers can better anticipate demand for components, facilitating more accurate production planning and inventory management. This mutual transparency builds trust and long-term partnerships between manufacturers and suppliers.
Advantages of High-Level Synthesis in Manufacturing
Increased Design Flexibility
One of the primary advantages of HLS is the increased flexibility it offers in circuit design. Engineers can experiment with different design architectures and quickly iterate on solutions without being bogged down by low-level implementation details. This flexibility leads to more innovative and optimized circuit designs.
Faster Time-to-Market
HLS significantly reduces the time required to develop and validate circuit designs. By automating the translation from high-level code to HDL, the design cycle is compressed, allowing manufacturers to bring products to market faster. This agility is critical in industries where technological advancements occur rapidly.
Improved Quality and Reliability
Automated synthesis processes reduce the likelihood of human error, resulting in higher quality and more reliable circuit designs. This improvement in quality directly impacts the overall reliability of manufactured products, enhancing brand reputation and customer satisfaction.
Resource Optimization
HLS optimizes the use of engineering resources by allowing designers to focus on high-level architecture and functionality rather than low-level implementation. This focus leads to more efficient use of talent and better allocation of resources within the organization.
Disadvantages and Challenges of High-Level Synthesis
Initial Implementation Costs
Adopting HLS technology involves significant initial investment in terms of software tools, training, and integration into existing workflows. For some manufacturers, especially smaller enterprises, the upfront costs can be a barrier to adoption.
Learning Curve
Transitioning to HLS requires engineers to acquire new skills and adapt to different workflows. The learning curve can be steep, potentially leading to temporary productivity dips as teams acclimate to the new technology.
Tool Limitations
While HLS tools have advanced significantly, they still have limitations in terms of supporting complex design requirements. Certain specialized or highly optimized designs may not be fully compatible with automated synthesis, necessitating manual intervention and expertise.
Dependency on Tool Vendors
Manufacturers become reliant on HLS tool vendors for updates, support, and compatibility. This dependency can pose risks if vendors discontinue support or fail to keep pace with evolving industry standards and technological advancements.
Supplier Negotiation Techniques in the Context of HLS
Leveraging Technological Advantage
Manufacturers utilizing HLS can leverage their technological advantage in negotiations by demonstrating their ability to optimize design cycles and production schedules. This capability can lead to favorable terms, such as better pricing, priority in production queues, and exclusive access to advanced components.
Building Collaborative Partnerships
Effective negotiation in the context of HLS emphasizes collaboration. By working closely with suppliers and involving them early in the design process, manufacturers can ensure that component specifications align with design requirements, fostering a more cooperative and mutually beneficial relationship.
Transparency and Data Sharing
Sharing relevant data and insights with suppliers enhances transparency and builds trust. Providing suppliers with access to design timelines, forecasts, and performance metrics enables more accurate demand forecasting and inventory management, leading to more effective negotiations.
Incorporating Long-Term Agreements
Long-term agreements can provide stability and predictability for both manufacturers and suppliers. These agreements often include clauses that benefit both parties, such as price stability, guaranteed supply, and collaborative development initiatives, making negotiations smoother and more productive.
Market Conditions Affecting High-Level Synthesis Adoption
Global Competition
The highly competitive global market demands continuous innovation and efficiency. HLS adoption enables Japanese manufacturers to maintain their competitive edge by accelerating design cycles, reducing costs, and enhancing product quality.
Technological Advancements
Rapid advancements in semiconductor technology and digital integration necessitate the adoption of advanced design methodologies like HLS. Staying ahead in technology trends ensures that manufacturers can meet the evolving demands of the market.
Supply Chain Dynamics
Global supply chain disruptions, as seen during recent geopolitical tensions and pandemics, highlight the need for flexible and efficient design and procurement processes. HLS contributes to more resilient supply chains by enabling quicker adjustments to design and sourcing strategies in response to supply chain challenges.
Regulatory and Compliance Factors
Adherence to international standards and regulatory requirements is crucial in global manufacturing. HLS tools often come with compliance checks and certifications, aiding manufacturers in meeting necessary standards and avoiding potential legal and financial penalties.
Best Practices for Implementing High-Level Synthesis in Manufacturing
Comprehensive Training Programs
Investing in comprehensive training programs ensures that engineering teams are well-versed in HLS methodologies and tools. Well-trained personnel can maximize the benefits of HLS, leading to more efficient and effective circuit designs.
Incremental Implementation
Adopting HLS incrementally allows manufacturers to integrate the technology into existing workflows gradually. Starting with pilot projects or specific product lines can help identify potential challenges and refine processes before a full-scale rollout.
Collaboration with Tool Vendors
Maintaining a close relationship with HLS tool vendors facilitates access to the latest updates, technical support, and best practices. Collaboration ensures that manufacturers can fully leverage the capabilities of their HLS tools and stay ahead of technological advancements.
Continuous Monitoring and Optimization
Implementing HLS is not a one-time effort but requires continuous monitoring and optimization. Regularly assessing the performance of HLS processes and making necessary adjustments ensures sustained efficiency and quality in circuit design.
Case Studies: Successful Adoption in Japanese Companies
Company A: Automotive Electronics
Company A, a leading automotive electronics manufacturer in Japan, integrated HLS into their design process to accelerate the development of advanced driver-assistance systems (ADAS). By leveraging HLS, the company reduced design cycles by 30%, allowing for quicker iterations and more robust system validations. This efficiency contributed to the company’s ability to launch competitive ADAS features ahead of rivals.
Company B: Consumer Electronics
Company B, specializing in consumer electronics, adopted HLS to enhance the design of their cutting-edge smartphones. The use of HLS enabled the engineering team to rapidly prototype and test new features, such as enhanced camera functionalities and improved battery management systems. As a result, Company B achieved a significant reduction in time-to-market, maintaining its reputation for innovation and quality.
Company C: Industrial Automation
In the industrial automation sector, Company C employed HLS to design complex control systems for manufacturing equipment. The integration of HLS streamlined their design process, leading to more efficient and reliable control systems. This improvement not only enhanced product performance but also strengthened supplier relationships through more predictable and optimized procurement strategies.
Future Trends and the Continued Impact of HLS
Integration with Artificial Intelligence
The convergence of HLS with artificial intelligence (AI) is poised to further revolutionize circuit design. AI-driven HLS tools can offer predictive design optimizations, automate more aspects of the synthesis process, and enable the creation of smarter, more adaptive circuits.
Advancements in HLS Tools
Ongoing advancements in HLS tools are expected to address current limitations, such as supporting more complex designs and improving compatibility with a broader range of applications. Enhanced tool capabilities will expand the scope and effectiveness of HLS in manufacturing.
Expansion into New Industries
While HLS has gained substantial traction in sectors like automotive and consumer electronics, its application is expanding into industries such as healthcare, aerospace, and renewable energy. This diversification underscores the versatile nature of HLS and its potential to drive innovation across various manufacturing domains.
Sustainability and Efficiency
As sustainability becomes a critical focus in manufacturing, HLS contributes by enabling the design of more energy-efficient and environmentally friendly circuits. Optimized designs lead to reduced energy consumption and lower material waste, aligning with global sustainability goals.
Conclusion
High-Level Synthesis circuit design is undeniably transforming Japanese manufacturing by enhancing procurement and purchasing processes, fostering innovation, and maintaining the competitive edge of Japanese manufacturers in the global market. Despite initial challenges such as implementation costs and the learning curve, the advantages of HLS—ranging from increased design flexibility to improved quality and faster time-to-market—make it a valuable asset in modern manufacturing. By adopting best practices, building strong supplier relationships, and staying abreast of technological advancements, Japanese manufacturers can continue to leverage HLS to drive efficiency, innovation, and sustained growth in an increasingly dynamic and competitive landscape.
資料ダウンロード
QCD管理受発注クラウド「newji」は、受発注部門で必要なQCD管理全てを備えた、現場特化型兼クラウド型の今世紀最高の受発注管理システムとなります。
ユーザー登録
受発注業務の効率化だけでなく、システムを導入することで、コスト削減や製品・資材のステータス可視化のほか、属人化していた受発注情報の共有化による内部不正防止や統制にも役立ちます。
NEWJI DX
製造業に特化したデジタルトランスフォーメーション(DX)の実現を目指す請負開発型のコンサルティングサービスです。AI、iPaaS、および先端の技術を駆使して、製造プロセスの効率化、業務効率化、チームワーク強化、コスト削減、品質向上を実現します。このサービスは、製造業の課題を深く理解し、それに対する最適なデジタルソリューションを提供することで、企業が持続的な成長とイノベーションを達成できるようサポートします。
製造業ニュース解説
製造業、主に購買・調達部門にお勤めの方々に向けた情報を配信しております。
新任の方やベテランの方、管理職を対象とした幅広いコンテンツをご用意しております。
お問い合わせ
コストダウンが利益に直結する術だと理解していても、なかなか前に進めることができない状況。そんな時は、newjiのコストダウン自動化機能で大きく利益貢献しよう!
(β版非公開)