- お役立ち記事
- Revolutionizing Japanese Manufacturing: The Impact of Microfluidic Devices on Industry Innovation
Revolutionizing Japanese Manufacturing: The Impact of Microfluidic Devices on Industry Innovation
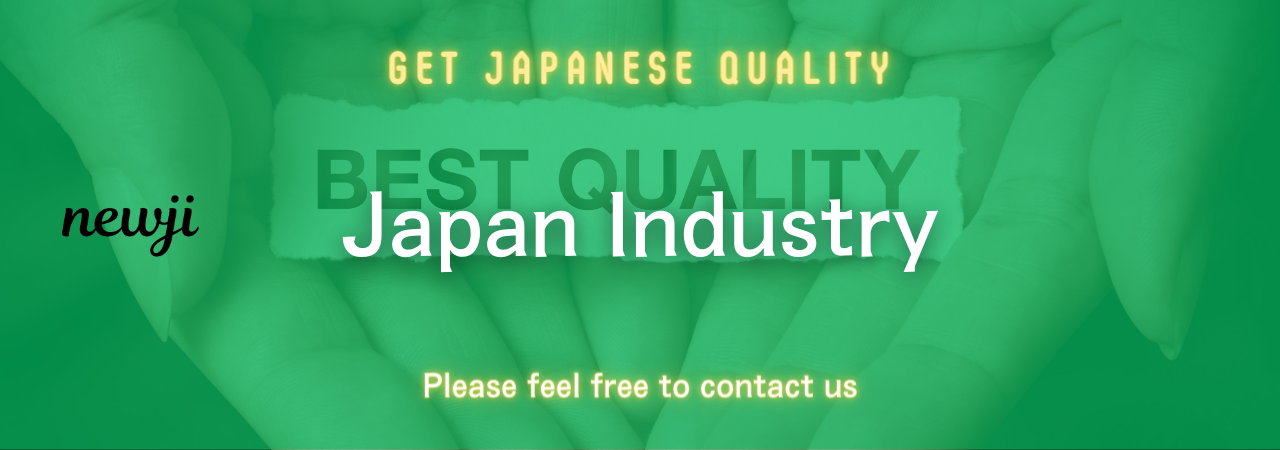
目次
Introduction to Microfluidic Devices in Japanese Manufacturing
Japanese manufacturing has long been synonymous with precision, quality, and innovation. In recent years, one of the most significant advancements driving this reputation forward is the integration of microfluidic devices. These miniature systems are revolutionizing various industries by enabling precise control and manipulation of fluids at the microscale. This article explores the impact of microfluidic devices on Japanese manufacturing, examining their benefits, challenges, procurement strategies, and best practices from a procurement and purchasing perspective.
The Role of Microfluidic Devices in Industry Innovation
Microfluidic devices are engineered systems that process small volumes of fluids through channels with dimensions of tens to hundreds of micrometers. Their applications span across diverse fields such as biotechnology, pharmaceuticals, environmental monitoring, and electronics. In the context of Japanese manufacturing, these devices are pivotal in driving innovation by enhancing product development, improving quality control, and enabling the creation of more efficient manufacturing processes.
Enhancing Product Development
Microfluidic technology allows for the rapid prototyping and testing of new products. By facilitating precise experimentation with small fluid volumes, manufacturers can accelerate the development cycle, reducing time-to-market for new innovations. This capability is particularly beneficial in industries like pharmaceuticals, where the ability to quickly iterate on drug formulations can lead to more effective treatments.
Improving Quality Control
Quality control is a cornerstone of Japanese manufacturing excellence. Microfluidic devices contribute by offering highly accurate and automated testing methods. These devices can monitor fluid properties in real-time, ensuring that products meet stringent quality standards. The integration of microfluidics into quality control processes minimizes human error and enhances the reliability of manufacturing outputs.
Enabling Efficient Manufacturing Processes
The precision offered by microfluidic devices translates into more efficient manufacturing processes. For example, in electronics manufacturing, these devices facilitate the precise deposition of materials, leading to the production of smaller and more complex components. This efficiency not only reduces material waste but also lowers production costs, contributing to the overall competitiveness of Japanese manufacturers.
Advantages of Integrating Microfluidic Devices
The adoption of microfluidic devices in Japanese manufacturing presents several advantages that drive industry innovation and competitiveness.
Precision and Control
Microfluidic devices provide unparalleled precision in fluid manipulation. This level of control is essential for applications requiring exact measurements and minimal variability, such as pharmaceutical formulations and chemical synthesis. The ability to maintain consistent conditions ensures high-quality and reliable products.
Cost-Effectiveness
Despite their advanced capabilities, microfluidic devices are often cost-effective due to their small size and the minimal amounts of reagents required. This reduction in material usage not only cuts costs but also makes these devices sustainable and environmentally friendly, aligning with global trends towards greener manufacturing practices.
Scalability
Microfluidic technology is inherently scalable, allowing manufacturers to start with small-scale production and seamlessly transition to larger volumes as demand grows. This scalability is particularly advantageous for startups and small to medium-sized enterprises looking to innovate without significant upfront investments.
Integration with Automation and AI
The compatibility of microfluidic devices with automation and artificial intelligence (AI) enhances their utility in modern manufacturing environments. Automated systems can leverage data from microfluidic devices to optimize processes, predict maintenance needs, and improve overall operational efficiency.
Challenges and Disadvantages
While microfluidic devices offer numerous benefits, their integration into Japanese manufacturing is not without challenges.
High Initial Investment
The initial cost of acquiring and implementing microfluidic technology can be substantial. Specialized equipment and training are required, which may pose a barrier for some manufacturers, especially smaller firms with limited capital resources.
Complexity in Design and Operation
Designing effective microfluidic systems requires a high level of expertise in both engineering and fluid dynamics. Additionally, operating these devices often necessitates specialized knowledge, which can complicate their adoption and integration into existing manufacturing processes.
Maintenance and Reliability Issues
Maintaining microfluidic systems can be challenging due to their delicate components and the precision required for their operation. Ensuring consistent performance over time demands regular maintenance and the availability of skilled personnel, which can increase operational costs.
Market Acceptance and Regulatory Hurdles
Industries that rely on microfluidic devices, such as healthcare and pharmaceuticals, are subject to rigorous regulatory standards. Navigating these regulations to gain market acceptance can be time-consuming and may delay the deployment of microfluidic technologies in certain sectors.
Procurement Strategies for Microfluidic Devices
Effective procurement strategies are crucial for successfully integrating microfluidic devices into Japanese manufacturing. These strategies encompass supplier selection, negotiation techniques, and risk management to ensure the acquisition of high-quality devices at competitive prices.
Supplier Selection
Choosing the right supplier is a critical first step in the procurement process. Japanese manufacturers should consider the following factors when selecting suppliers of microfluidic devices:
– **Reputation and Track Record:** Evaluate the supplier’s history in the industry, including their experience in manufacturing microfluidic devices and their reputation for quality and reliability.
– **Technical Expertise:** Ensure that the supplier has the necessary technical capabilities to produce advanced microfluidic devices that meet your specific requirements.
– **Customization Options:** Assess the supplier’s ability to provide customized solutions tailored to your unique manufacturing needs.
– **After-Sales Support:** Consider the level of support offered by the supplier, including maintenance services, training, and technical assistance.
Negotiation Techniques
Effective negotiation can lead to favorable terms and cost savings when procuring microfluidic devices. Here are some techniques to employ:
– **Bulk Purchasing Discounts:** Negotiate discounts based on the volume of devices being purchased. Large orders can often secure better pricing and favorable delivery terms.
– **Long-Term Contracts:** Establishing long-term agreements with suppliers can result in price stability and priority access to new technologies.
– **Flexible Payment Terms:** Discuss options for flexible payment schedules, such as deferred payments or installment plans, to manage cash flow more effectively.
– **Value-Added Services:** Negotiate for additional services such as training, customization, or extended warranties without incurring extra costs.
Risk Management
Mitigating risks associated with the procurement of microfluidic devices is essential for maintaining smooth operations. Strategies include:
– **Diversified Supplier Base:** Avoid reliance on a single supplier by establishing relationships with multiple vendors. This approach reduces the impact of supply chain disruptions.
– **Quality Assurance:** Implement stringent quality control measures to ensure that procured devices meet the required standards and specifications.
– **Contingency Planning:** Develop contingency plans to address potential delays or failures in the supply chain, ensuring minimal disruption to manufacturing processes.
Market Conditions and Trends
Understanding the market conditions and trends is vital for informed procurement decisions regarding microfluidic devices in Japanese manufacturing.
Technological Advancements
The microfluidics market is rapidly evolving, with continuous advancements in materials, fabrication techniques, and integration with digital technologies. Staying abreast of these developments enables manufacturers to adopt cutting-edge solutions that enhance their competitive edge.
Global Supply Chain Dynamics
Global supply chain dynamics, including geopolitical factors and trade policies, influence the availability and cost of microfluidic devices. Japanese manufacturers must monitor these factors to anticipate potential disruptions and adjust their procurement strategies accordingly.
Increasing Demand Across Industries
The demand for microfluidic devices is growing across various sectors, driven by the need for precision, efficiency, and innovation. This increased demand can lead to higher competition among suppliers, potentially affecting pricing and availability. Manufacturers should anticipate these market shifts and plan their procurement accordingly.
Regulatory Landscape
Changes in regulations, particularly in industries such as healthcare and pharmaceuticals, can impact the procurement of microfluidic devices. Manufacturers need to stay informed about regulatory updates to ensure compliance and avoid potential delays in product development and deployment.
Best Practices in Procuring Microfluidic Devices
Adopting best practices in procurement can optimize the acquisition process and ensure the successful integration of microfluidic devices into manufacturing operations.
Comprehensive Needs Assessment
Begin by conducting a thorough assessment of your manufacturing needs. Identify the specific applications for microfluidic devices, the required specifications, and the desired outcomes. This clarity will guide supplier selection and ensure that the procured devices align with your operational goals.
Thorough Supplier Evaluation
Evaluate potential suppliers based on their technical capabilities, quality standards, and reliability. Request samples, review case studies, and seek references from other clients to assess the supplier’s performance and suitability for your needs.
Collaborative Partnership Development
Foster collaborative relationships with suppliers to facilitate open communication and mutual growth. Engaging suppliers as partners rather than mere vendors can lead to better alignment of goals, smoother problem-solving, and access to innovative solutions.
Effective Contract Management
Develop clear and detailed contracts that outline all aspects of the procurement, including specifications, pricing, delivery schedules, quality standards, and after-sales support. Regularly review and manage contracts to ensure compliance and address any issues promptly.
Continuous Monitoring and Improvement
Implement a system for continuously monitoring the performance of procured microfluidic devices and the suppliers providing them. Gather feedback, analyze performance metrics, and identify areas for improvement to enhance the overall procurement process and operational efficiency.
Supplier Negotiation Techniques
Negotiating effectively with suppliers is crucial for securing favorable terms and ensuring the successful procurement of microfluidic devices. Here are key techniques to enhance negotiation outcomes:
Preparation and Research
Before entering negotiations, conduct comprehensive research on the supplier, market prices, and alternative options. Understanding the supplier’s position and identifying your own priorities will empower you to negotiate from a position of strength.
Building Rapport
Establishing a positive relationship with the supplier can facilitate smoother negotiations. Building rapport through respectful communication and demonstrating a genuine interest in the supplier’s business can lead to more cooperative and flexible negotiation outcomes.
Leveraging Volume and Long-Term Commitment
Highlight your potential for large or recurring orders as leverage during negotiations. Suppliers are often willing to offer discounts and better terms to secure long-term commitments and bulk purchases.
Highlighting Mutual Benefits
Frame negotiations in a way that emphasizes mutual benefits. Demonstrate how a successful partnership can lead to growth and success for both parties, fostering a collaborative rather than adversarial negotiation environment.
Flexibility and Compromise
Be prepared to make concessions on less critical aspects to achieve your primary objectives. Flexibility in negotiations can lead to compromises that satisfy both parties and establish a foundation for future cooperation.
Case Studies: Successful Integration of Microfluidic Devices in Japanese Manufacturing
Examining real-world examples of successful microfluidic device integration provides valuable insights into effective procurement and implementation strategies.
Pharmaceutical Manufacturing
A leading Japanese pharmaceutical company integrated microfluidic devices into their drug development process. By automating the testing of drug formulations, the company reduced the development cycle by 30%, enabling faster time-to-market for new medications. The procurement strategy focused on partnering with a specialized supplier that offered customized solutions and comprehensive support, ensuring seamless integration into existing workflows.
Electronics Manufacturing
In the electronics sector, a Japanese manufacturer adopted microfluidic technology for the precise deposition of conductive materials in the fabrication of flexible electronics. This integration enhanced product performance and reliability while reducing material waste. The company’s procurement approach emphasized long-term contracts with suppliers capable of scaling production to meet increasing demand, ensuring consistent quality and supply chain stability.
Environmental Monitoring
A Japanese environmental technology firm utilized microfluidic devices for real-time water quality monitoring. These devices provided accurate and timely data, enabling proactive environmental management. The procurement process involved selecting suppliers with robust quality assurance practices and the ability to provide ongoing maintenance and support, ensuring the devices operated effectively in diverse environmental conditions.
Future Outlook and Emerging Trends
The future of microfluidic devices in Japanese manufacturing is promising, with several emerging trends poised to further revolutionize the industry.
Integration with Internet of Things (IoT)
The convergence of microfluidic technology with IoT is set to create smart manufacturing environments. IoT-enabled microfluidic devices can provide real-time data analytics, predictive maintenance, and enhanced process control, driving greater efficiency and innovation.
Advancements in Materials and Fabrication
Ongoing research into new materials and fabrication techniques will lead to more durable, versatile, and cost-effective microfluidic devices. Innovations such as 3D printing and novel polymers will expand the applications and accessibility of microfluidic technology in various manufacturing sectors.
Personalized Manufacturing
Microfluidics facilitates personalized manufacturing by allowing for customization at the microscale. This capability is particularly relevant in sectors like healthcare, where personalized medical devices and treatments are increasingly in demand. Japanese manufacturers can leverage this trend to cater to niche markets and enhance customer satisfaction.
Sustainability and Green Manufacturing
Sustainability is becoming a critical focus in manufacturing. Microfluidic devices contribute to green manufacturing by minimizing waste, reducing energy consumption, and enabling the use of eco-friendly materials. As environmental regulations tighten and consumer demand for sustainable products grows, the role of microfluidics in supporting sustainable manufacturing practices will become increasingly important.
Conclusion
Microfluidic devices are at the forefront of innovation in Japanese manufacturing, offering unparalleled precision, efficiency, and flexibility across various industries. While the integration of this technology presents challenges such as high initial investment and complexity, the advantages in product development, quality control, and process optimization are substantial. Effective procurement strategies, including careful supplier selection, skilled negotiation, and robust risk management, are essential for leveraging the full potential of microfluidic devices. As technological advancements and market trends continue to evolve, Japanese manufacturers that adeptly adopt and integrate microfluidic technology will maintain their competitive edge and drive further industry innovation.
資料ダウンロード
QCD調達購買管理クラウド「newji」は、調達購買部門で必要なQCD管理全てを備えた、現場特化型兼クラウド型の今世紀最高の購買管理システムとなります。
ユーザー登録
調達購買業務の効率化だけでなく、システムを導入することで、コスト削減や製品・資材のステータス可視化のほか、属人化していた購買情報の共有化による内部不正防止や統制にも役立ちます。
NEWJI DX
製造業に特化したデジタルトランスフォーメーション(DX)の実現を目指す請負開発型のコンサルティングサービスです。AI、iPaaS、および先端の技術を駆使して、製造プロセスの効率化、業務効率化、チームワーク強化、コスト削減、品質向上を実現します。このサービスは、製造業の課題を深く理解し、それに対する最適なデジタルソリューションを提供することで、企業が持続的な成長とイノベーションを達成できるようサポートします。
オンライン講座
製造業、主に購買・調達部門にお勤めの方々に向けた情報を配信しております。
新任の方やベテランの方、管理職を対象とした幅広いコンテンツをご用意しております。
お問い合わせ
コストダウンが利益に直結する術だと理解していても、なかなか前に進めることができない状況。そんな時は、newjiのコストダウン自動化機能で大きく利益貢献しよう!
(Β版非公開)