- お役立ち記事
- Revolutionizing Japanese Manufacturing: The Key Role of Safety and Health Management in 2023
Revolutionizing Japanese Manufacturing: The Key Role of Safety and Health Management in 2023
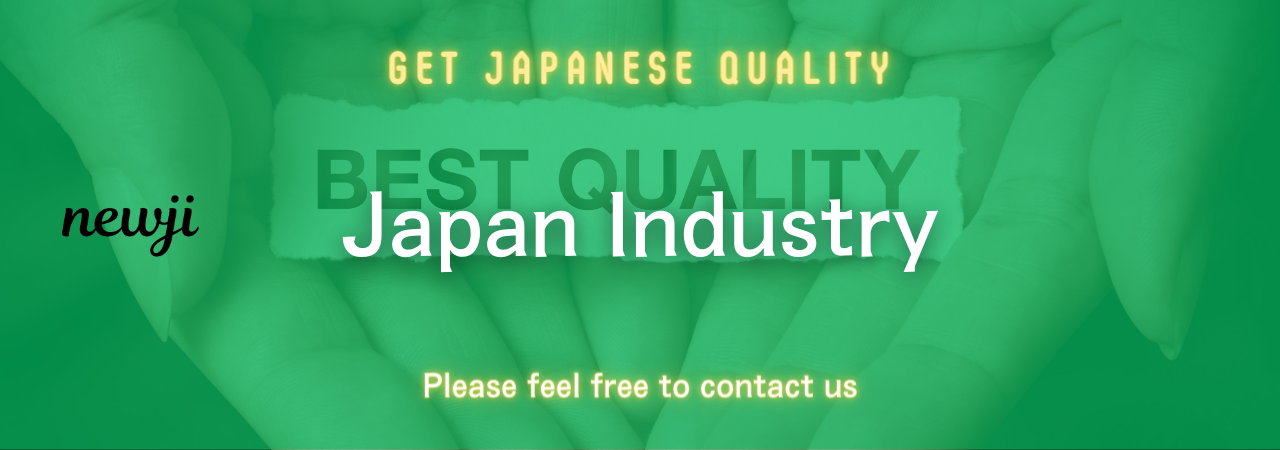
目次
Introduction
Safety and health management have always been pivotal in the manufacturing sector, and their significance has only grown as industries evolve.
Japanese manufacturing has long been regarded as a global leader due to its commitment to quality, efficiency, and innovation.
In 2023, the focus has sharpened even further on ensuring workplaces are safe and employees remain healthy.
With a confluence of regulatory, technological, and social changes, the landscape of safety and health management in Japanese manufacturing is undergoing a revolution.
The Evolution of Safety and Health Management in Japan
Historical Context
Japan’s journey towards industrial excellence began post-World War II, where rapid industrialization emphasized productivity and quality.
Over the decades, safety and health management gradually moved to the forefront as industries recognized the direct impact of workplace conditions on productivity and employee well-being.
The enactment of laws like the Industrial Safety and Health Act in 1972 marked a significant step towards institutionalizing safety and health measures.
Regular amendments to these regulations reflect the changing dynamics and growing importance of this field.
Current Trends
In 2023, several trends define safety and health management in Japanese manufacturing:
– Increased automation and the introduction of AI and IoT in monitoring safety conditions.
– A greater emphasis on mental health alongside physical safety.
– Stricter compliance requirements driven by both national and international regulations.
– The integration of sustainability goals with safety and health practices.
The Advantages of Rigorous Safety and Health Management
Enhanced Productivity
A safe and healthy work environment translates directly into higher productivity.
Employees can focus on their tasks without the distraction of safety concerns.
They also tend to take fewer sick leaves, leading to more consistent production schedules.
Improved Employee Morale and Retention
When employees see that their well-being is a priority for management, their satisfaction and loyalty to the company increase.
High morale reduces turnover rates, which is crucial in times of skill shortages.
Regulatory Compliance and Avoidance of Penalties
Adhering to safety and health regulations protects the company from legal repercussions.
Penalties for non-compliance can be severe, including hefty fines and shutdowns, which can significantly impact business operations.
Brand Image and Market Reputation
Companies known for their stringent safety and health standards often enjoy a better reputation in the market.
This can be a decisive factor for both clients and potential employees when choosing between competitors.
Challenges and Disadvantages
Initial Implementation Costs
One of the primary challenges in enhancing safety and health measures is the initial cost involved.
Purchasing state-of-the-art safety equipment, upgrading existing infrastructure, and training employees can be expensive.
Continuous Monitoring and Upgradation
Due to the dynamic nature of manufacturing environments and evolving regulations, continuous monitoring and upgradation of safety measures are necessary.
This requires ongoing investment of both time and resources.
Resistance to Change
Employees and management might resist changes, especially if they perceive new measures as cumbersome or unnecessary.
Overcoming this resistance requires effective communication and change management strategies.
Balancing Production with Safety
There is sometimes a perceived trade-off between maintaining safety and achieving production goals.
Balancing these can be challenging, especially in high-pressure environments where meeting production deadlines is critical.
Effective Supplier Negotiation Techniques
Understanding Supplier Capabilities and Standards
When negotiating with Japanese suppliers, it’s crucial to understand their capabilities and the standards they adhere to.
This not only ensures that they can meet your quality requirements but also that they comply with safety regulations.
Building Long-Term Relationships
Japanese business culture places a high value on long-term relationships and trust.
Approaching negotiations with a focus on developing a lasting partnership can facilitate smoother discussions and better outcomes.
Emphasizing Mutual Benefits
Highlighting how both parties can benefit from the relationship can create a more collaborative negotiation atmosphere.
This might include discussing how improved safety measures can lead to better product quality and reduced production downtime.
Regular Audits and Assessments
Incorporating clauses for regular safety audits and assessments in supplier contracts ensures continuous compliance with safety standards.
This proactive approach can prevent potential issues and maintain high safety levels.
Market Conditions and Best Practices
Current Market Conditions
The current market conditions for Japanese manufacturing are influenced by global supply chain disruptions, evolving trade policies, and technological advancements.
These factors necessitate a flexible and proactive approach to safety and health management.
Best Practices for Safety and Health Management
– **Comprehensive Training Programs:** Regular training sessions for employees at all levels on safety protocols, emergency responses, and health practices.
– **Technology Integration:** Utilizing advanced technologies like IoT for real-time monitoring, predictive maintenance, and automated safety checks.
– **Employee Engagement:** Encouraging employees to participate in safety committees and to report potential hazards without fear of reprisal.
– **Continuous Improvement:** Regularly reviewing and updating safety and health policies to incorporate the latest industry standards and practices.
Case Studies and Examples
Case Study 1: Toyota’s Safety Culture
Toyota Motor Corporation has long been recognized for its robust safety culture.
By integrating safety into its core values and operational practices, Toyota has achieved remarkable success in minimizing workplace incidents and enhancing employee well-being.
The company employs a comprehensive safety training program, advanced technologies for hazard detection, and a proactive approach to safety management.
Case Study 2: Sony’s Mental Health Initiatives
Sony Corporation has taken significant strides in addressing mental health issues among its employees.
Recognizing the importance of mental health in overall well-being and productivity, Sony has implemented counseling services, stress management programs, and workshops on mental health awareness.
These initiatives have led to a more supportive work environment and have significantly reduced mental health-related absenteeism.
Conclusion
The revolution in safety and health management within Japanese manufacturing is not just a regulatory requirement but a strategic advantage.
From enhancing productivity and employee morale to avoiding legal penalties and improving brand reputation, the benefits are manifold.
However, the journey comes with challenges that require careful navigation and continuous improvement.
By embracing best practices, leveraging technology, and fostering a culture of safety, Japanese manufacturers can not only ensure compliance but also lead the way in creating safer and healthier workplaces.
In 2023 and beyond, those who prioritize safety and health management will be best positioned to thrive in an increasingly complex and competitive global market.
資料ダウンロード
QCD調達購買管理クラウド「newji」は、調達購買部門で必要なQCD管理全てを備えた、現場特化型兼クラウド型の今世紀最高の購買管理システムとなります。
ユーザー登録
調達購買業務の効率化だけでなく、システムを導入することで、コスト削減や製品・資材のステータス可視化のほか、属人化していた購買情報の共有化による内部不正防止や統制にも役立ちます。
NEWJI DX
製造業に特化したデジタルトランスフォーメーション(DX)の実現を目指す請負開発型のコンサルティングサービスです。AI、iPaaS、および先端の技術を駆使して、製造プロセスの効率化、業務効率化、チームワーク強化、コスト削減、品質向上を実現します。このサービスは、製造業の課題を深く理解し、それに対する最適なデジタルソリューションを提供することで、企業が持続的な成長とイノベーションを達成できるようサポートします。
オンライン講座
製造業、主に購買・調達部門にお勤めの方々に向けた情報を配信しております。
新任の方やベテランの方、管理職を対象とした幅広いコンテンツをご用意しております。
お問い合わせ
コストダウンが利益に直結する術だと理解していても、なかなか前に進めることができない状況。そんな時は、newjiのコストダウン自動化機能で大きく利益貢献しよう!
(Β版非公開)