- お役立ち記事
- Revolutionizing Japanese Manufacturing: The Power and Precision of Vacuum Chucks
月間77,185名の
製造業ご担当者様が閲覧しています*
*2025年2月28日現在のGoogle Analyticsのデータより
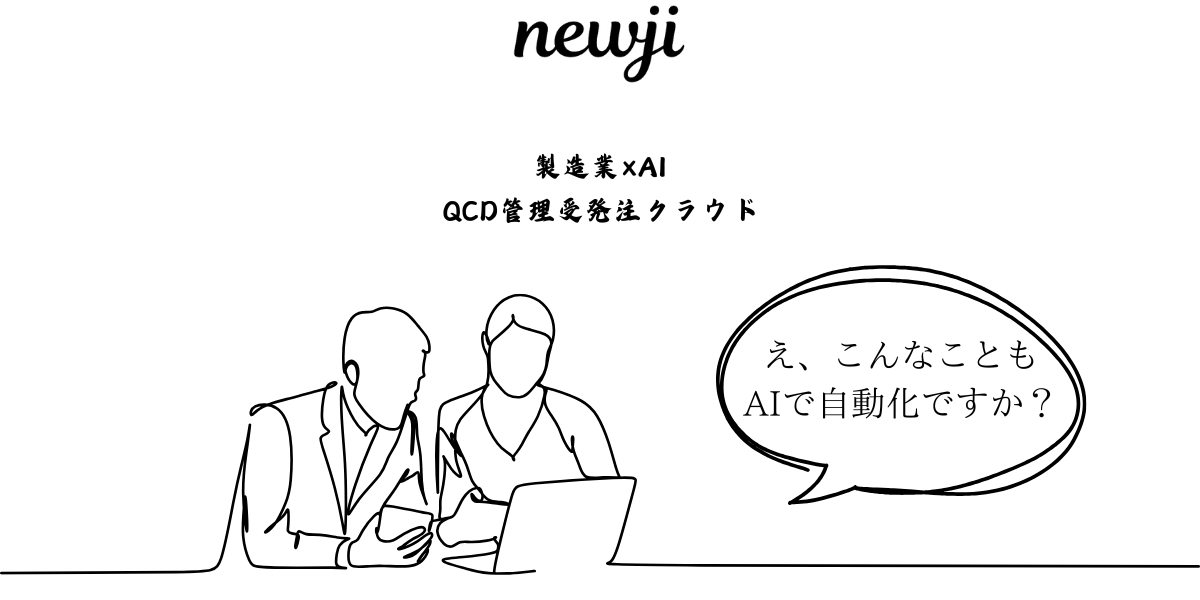
Revolutionizing Japanese Manufacturing: The Power and Precision of Vacuum Chucks
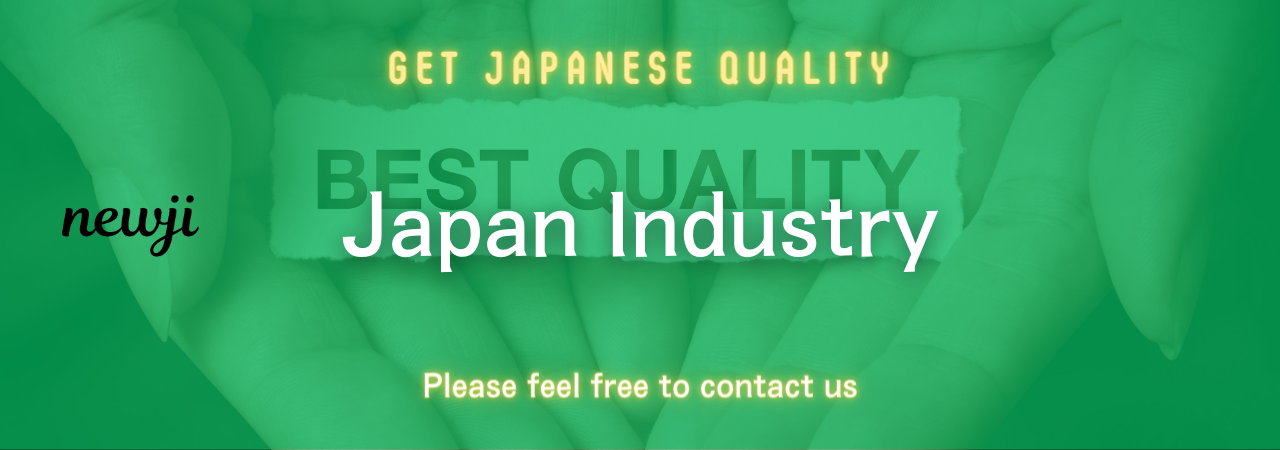
目次
Introduction
Japanese manufacturing has long been synonymous with quality, precision, and innovation.
One of the critical components that underpin this reputation is the use of vacuum chucks.
These devices play a pivotal role in various manufacturing processes, enhancing both efficiency and product quality.
In this article, we delve into the power and precision of vacuum chucks in revolutionizing Japanese manufacturing.
We will explore their advantages and disadvantages, procurement and purchasing strategies, supplier negotiation techniques, market conditions, and best practices.
Our goal is to provide a comprehensive guide for procurement and purchasing professionals looking to leverage Japanese expertise in vacuum chuck technology.
Understanding Vacuum Chucks in Japanese Manufacturing
Vacuum chucks are fundamental tools in manufacturing, used to hold workpieces securely in place during machining, assembly, and other processes.
They utilize vacuum pressure to create a stable, non-invasive grip, ensuring precision and reducing the risk of damage to delicate components.
In Japanese manufacturing, vacuum chucks are employed across various industries, including automotive, electronics, aerospace, and precision engineering.
The integration of advanced vacuum chuck technology has significantly contributed to the high standards of Japanese products, enabling consistent quality and repeatability in production.
Types of Vacuum Chucks
Japanese manufacturers utilize several types of vacuum chucks, each designed to meet specific operational requirements.
These include flat plate vacuum chucks, conformable vacuum chucks, and specialized chucks for handling irregular or fragile components.
Flat plate vacuum chucks are commonly used for uniformly shaped workpieces, while conformable vacuum chucks adapt to the contours of irregularly shaped items.
Specialized chucks incorporate features such as temperature control and vibration damping to cater to unique manufacturing needs.
Technological Innovations
The Japanese manufacturing sector is at the forefront of technological innovations in vacuum chuck design.
Advances include the integration of smart sensors for real-time monitoring of vacuum pressure and grip strength.
These innovations enhance the automation capabilities of manufacturing systems, allowing for precise adjustments and minimizing human intervention.
Moreover, the development of lightweight and compact vacuum chucks has improved the overall efficiency and flexibility of production lines.
Advantages of Vacuum Chucks
Vacuum chucks offer numerous advantages that make them indispensable in modern manufacturing environments.
Their ability to provide a stable and adjustable grip ensures high precision and reduces the likelihood of defects.
Additionally, vacuum chucks minimize mechanical stress on workpieces, preserving the integrity of sensitive components.
Enhanced Precision and Stability
One of the primary benefits of vacuum chucks is their ability to hold workpieces with high precision.
The consistent vacuum pressure ensures that the workpiece remains stationary, allowing for accurate machining and assembly.
This stability is crucial in industries where even minor deviations can lead to significant quality issues.
Reduced Mechanical Stress
Unlike mechanical clamps, vacuum chucks do not exert pressure on specific points of the workpiece.
This uniform distribution of force reduces the risk of deformation or damage, particularly in delicate or complex components.
As a result, vacuum chucks are ideal for handling fragile materials without compromising their structural integrity.
Flexibility and Versatility
Vacuum chucks are highly versatile, accommodating a wide range of workpiece sizes and shapes.
Their design can be customized to suit specific manufacturing requirements, making them adaptable to various production scenarios.
This flexibility enhances the overall efficiency of manufacturing processes, allowing for quick adjustments without the need for extensive retooling.
Disadvantages of Vacuum Chucks
Despite their numerous advantages, vacuum chucks also present certain challenges that manufacturers must address.
Understanding these disadvantages is essential for implementing effective solutions and optimizing manufacturing workflows.
Dependence on Vacuum Pressure
Vacuum chucks rely heavily on consistent vacuum pressure to maintain grip strength.
Fluctuations in vacuum levels due to leaks, duct blockages, or compressor failures can compromise the stability of the workpiece.
Such inconsistencies can lead to production delays and quality issues, necessitating robust maintenance and monitoring systems.
Limitations with Non-Porous Materials
Vacuum chucks are most effective with porous or semi-porous materials that allow air to pass through.
Handling non-porous materials can be challenging, as achieving a sufficient vacuum seal becomes difficult.
In such cases, additional sealing mechanisms or alternative gripping methods may be required, adding complexity to the setup.
Initial Investment and Maintenance Costs
The advanced design and technology incorporated into high-quality vacuum chucks result in higher initial costs.
Moreover, regular maintenance is essential to ensure optimal performance and longevity.
Manufacturers must factor these costs into their procurement budgets and consider the long-term return on investment.
Procurement and Purchasing Strategies
Effective procurement and purchasing strategies are crucial for acquiring high-quality vacuum chucks from Japanese suppliers.
Given Japan’s reputation for precision engineering, establishing strong relationships with reliable suppliers is paramount.
Identifying Reputable Suppliers
The first step in the procurement process is identifying reputable Japanese suppliers with a proven track record in vacuum chuck manufacturing.
This involves conducting thorough market research, evaluating supplier credentials, and assessing their technological capabilities.
Engaging with industry associations and attending trade fairs can also provide valuable insights into potential suppliers.
Assessing Supplier Capabilities
Once potential suppliers are identified, it is essential to assess their manufacturing capabilities, quality control processes, and commitment to innovation.
Requesting samples and conducting site visits can offer a firsthand understanding of their operational standards.
Additionally, evaluating their ability to customize products to meet specific requirements ensures flexibility and adaptability in production.
Building Long-Term Partnerships
Establishing long-term partnerships with Japanese suppliers fosters trust and facilitates smoother procurement processes.
Long-term collaborations enable better communication, more favorable pricing, and priority access to new technologies.
Investing in these relationships can lead to mutual growth and sustained competitive advantage.
Supplier Negotiation Techniques
Negotiating effectively with Japanese suppliers requires a nuanced approach that respects cultural norms and emphasizes mutual benefits.
Cultural Considerations
Understanding Japanese business etiquette is crucial for successful negotiations.
Japanese suppliers value respect, patience, and harmony in business dealings.
Building rapport through formal introductions, exchanging business cards respectfully, and adhering to formal communication protocols lays the foundation for productive negotiations.
Value-Based Negotiation
Rather than focusing solely on price, adopt a value-based negotiation approach that emphasizes the quality and reliability of the products.
Highlighting long-term collaboration benefits and mutual growth opportunities can lead to more favorable terms.
Demonstrating a clear understanding of the supplier’s business and aligning your objectives with theirs fosters a cooperative atmosphere.
Leveraging Volume and Commitment
In negotiations, leveraging your purchasing volume and commitment can yield better pricing and terms.
Japanese suppliers are more inclined to offer discounts and favorable terms to partners who present consistent and substantial orders.
Demonstrating a commitment to long-term procurement increases the supplier’s incentive to prioritize your business.
Market Conditions for Vacuum Chucks
The global market for vacuum chucks is influenced by various factors, including technological advancements, demand fluctuations, and competitive dynamics.
Understanding these market conditions is essential for making informed procurement decisions.
Technological Trends
Advancements in automation, robotics, and Industry 4.0 have heightened the demand for sophisticated vacuum chuck solutions.
Japanese manufacturers are at the forefront of integrating smart technologies into vacuum chucks, enhancing their functionality and adaptability.
Staying abreast of these technological trends enables procurement professionals to source cutting-edge products that align with modern manufacturing needs.
Global Demand and Supply Dynamics
The demand for vacuum chucks is closely tied to the performance of key industries such as automotive, electronics, and aerospace.
Economic fluctuations in these sectors can impact the demand for vacuum chuck technology.
Additionally, supply chain disruptions, such as those caused by geopolitical tensions or pandemics, can affect the availability and pricing of vacuum chucks.
Diversifying supplier bases and maintaining contingency plans are strategies to mitigate such risks.
Competitive Landscape
The vacuum chuck market is highly competitive, with numerous suppliers vying for market share.
Japanese suppliers distinguish themselves through their commitment to quality, innovation, and customer service.
Understanding the competitive landscape helps in benchmarking supplier offerings and identifying those that provide the best value propositions.
Best Practices in Implementing Vacuum Chucks
Implementing vacuum chucks effectively requires adherence to best practices that maximize their benefits and ensure seamless integration into manufacturing processes.
Comprehensive Training and Skill Development
Ensuring that personnel are adequately trained in the operation and maintenance of vacuum chucks is essential.
Comprehensive training programs enhance the workforce’s ability to utilize vacuum chucks effectively, troubleshoot issues, and perform routine maintenance.
Investing in skill development reduces downtime and prolongs the lifespan of the equipment.
Regular Maintenance and Inspections
Preventative maintenance is critical for sustaining the performance and reliability of vacuum chucks.
Regular inspections help identify and address potential issues before they escalate into significant problems.
Establishing a maintenance schedule and adhering to it ensures consistent operation and minimizes unexpected disruptions.
Integration with Automation Systems
Integrating vacuum chucks with automation systems enhances their efficiency and reduces manual intervention.
Automation can optimize vacuum pressure settings, monitor performance in real-time, and facilitate data-driven decision-making.
Seamless integration with existing manufacturing systems maximizes productivity and aligns vacuum chuck operations with overall production goals.
Quality Control and Assurance
Maintaining high quality standards is paramount in the implementation of vacuum chucks in Japanese manufacturing.
Supplier Quality Assurance
Collaborating with suppliers who adhere to stringent quality assurance practices is essential.
Implementing supplier audits and requiring certifications such as ISO 9001 ensures that suppliers maintain consistent quality standards.
Quality assurance agreements can delineate expectations and responsibilities, fostering accountability and excellence.
In-House Quality Control Measures
Complementing supplier quality assurance with robust in-house quality control measures enhances overall product reliability.
Implementing rigorous inspection protocols, utilizing advanced testing equipment, and conducting regular performance evaluations ensure that vacuum chucks meet specified standards.
Continuous quality improvement initiatives drive the refinement of manufacturing processes and product offerings.
Feedback and Continuous Improvement
Establishing feedback mechanisms allows for the identification of quality issues and areas for improvement.
Encouraging open communication between procurement teams, suppliers, and manufacturing personnel facilitates the swift resolution of quality concerns.
Adopting a continuous improvement mindset promotes the ongoing enhancement of vacuum chuck performance and reliability.
Leveraging Industry Relationships in Japan
Building strong relationships within the Japanese manufacturing sector is a strategic advantage in procuring vacuum chucks.
Networking and Relationship Building
Engaging in networking activities, such as industry conferences, trade shows, and business forums, fosters connections with key stakeholders in the Japanese market.
Building personal relationships through regular interactions and collaborative projects enhances trust and mutual understanding.
These relationships can lead to preferential treatment, insider knowledge of market trends, and access to exclusive product offerings.
Collaborative Innovation
Collaborating with Japanese suppliers on innovation projects unlocks opportunities for co-development and technological advancements.
Joint research and development initiatives can result in customized vacuum chuck solutions tailored to specific manufacturing needs.
Such collaborations drive innovation, strengthen partnerships, and position both parties as leaders in the industry.
Cultural Exchange and Mutual Respect
Promoting cultural exchange and demonstrating mutual respect for Japanese business practices fosters a harmonious working relationship.
Understanding and appreciating cultural nuances, such as the importance of consensus-building and indirect communication, enhances collaboration effectiveness.
A respectful and culturally aware approach lays the groundwork for successful long-term partnerships.
Technological Innovations in Vacuum Chuck Design
Japanese manufacturers continually push the boundaries of vacuum chuck technology, integrating cutting-edge features that enhance performance and versatility.
Smart Vacuum Chucks
The integration of smart technologies, such as IoT sensors and automation controls, has transformed vacuum chucks into intelligent devices.
Smart vacuum chucks can monitor and adjust vacuum levels in real-time, detect anomalies, and communicate performance data to centralized systems.
These capabilities enable predictive maintenance, reduce downtime, and optimize manufacturing processes.
Advanced Materials and Manufacturing Techniques
Japanese firms leverage advanced materials and precision manufacturing techniques to enhance the durability and functionality of vacuum chucks.
The use of high-strength, lightweight materials improves the overall efficiency of vacuum chucks, while precision machining ensures exact tolerances and fit.
Innovative manufacturing methods, such as additive manufacturing, allow for the creation of complex geometries and customized designs that meet specific application requirements.
Energy Efficiency and Sustainability
Energy efficiency is a growing focus in vacuum chuck design, aligning with global sustainability initiatives.
Japanese manufacturers are developing vacuum chucks with lower energy consumption without compromising performance.
Sustainable design practices, such as the use of recyclable materials and eco-friendly manufacturing processes, contribute to environmentally responsible production.
Enhancing Factory Efficiency with Vacuum Chucks
The strategic implementation of vacuum chucks can significantly enhance factory efficiency, leading to improved productivity and reduced operational costs.
Streamlining Production Processes
Vacuum chucks facilitate the seamless handling of workpieces, reducing the time and labor required for manual clamping and positioning.
This streamlining of production processes accelerates manufacturing cycles, allowing for higher throughput and increased output.
Efficient handling also minimizes the risk of errors and defects, enhancing overall product quality.
Reducing Setup Times
The ease of adjusting vacuum chucks between different workpieces or production runs reduces setup times.
Quick and efficient changeovers enable manufacturers to respond swiftly to varying production demands, enhancing flexibility and responsiveness.
Reduced downtime during setup translates to higher operational efficiency and better utilization of manufacturing resources.
Minimizing Waste and Defects
Reliable workpiece holding reduces the likelihood of misalignment, vibration-induced defects, and material waste.
By ensuring consistent positioning and stability, vacuum chucks contribute to higher precision in manufacturing operations.
This reduction in defects not only improves product quality but also decreases the costs associated with rework and scrap.
Conclusion
Vacuum chucks have emerged as a cornerstone of Japanese manufacturing excellence, embodying the principles of precision, reliability, and innovation.
Their ability to securely hold workpieces with minimal mechanical stress enables manufacturers to achieve unparalleled levels of accuracy and quality.
While vacuum chucks offer numerous advantages, including enhanced precision, flexibility, and reduced mechanical stress, they also present challenges such as dependence on consistent vacuum pressure and higher initial investment costs.
Effective procurement and purchasing strategies, coupled with successful supplier negotiation techniques, are essential for sourcing high-quality vacuum chucks from Japanese suppliers.
Understanding market conditions and embracing best practices in implementation further amplifies the benefits of vacuum chucks in manufacturing operations.
As Japanese manufacturers continue to lead in technological advancements, leveraging their expertise in vacuum chuck design will be instrumental in driving factory efficiency and sustaining competitive advantage in the global market.
By adopting a strategic and collaborative approach, procurement professionals can harness the power and precision of vacuum chucks to revolutionize their manufacturing processes and achieve long-term success.
資料ダウンロード
QCD管理受発注クラウド「newji」は、受発注部門で必要なQCD管理全てを備えた、現場特化型兼クラウド型の今世紀最高の受発注管理システムとなります。
ユーザー登録
受発注業務の効率化だけでなく、システムを導入することで、コスト削減や製品・資材のステータス可視化のほか、属人化していた受発注情報の共有化による内部不正防止や統制にも役立ちます。
NEWJI DX
製造業に特化したデジタルトランスフォーメーション(DX)の実現を目指す請負開発型のコンサルティングサービスです。AI、iPaaS、および先端の技術を駆使して、製造プロセスの効率化、業務効率化、チームワーク強化、コスト削減、品質向上を実現します。このサービスは、製造業の課題を深く理解し、それに対する最適なデジタルソリューションを提供することで、企業が持続的な成長とイノベーションを達成できるようサポートします。
製造業ニュース解説
製造業、主に購買・調達部門にお勤めの方々に向けた情報を配信しております。
新任の方やベテランの方、管理職を対象とした幅広いコンテンツをご用意しております。
お問い合わせ
コストダウンが利益に直結する術だと理解していても、なかなか前に進めることができない状況。そんな時は、newjiのコストダウン自動化機能で大きく利益貢献しよう!
(β版非公開)