- お役立ち記事
- Revolutionizing Japanese Manufacturing: The Power of Abrasives in Precision Engineering
Revolutionizing Japanese Manufacturing: The Power of Abrasives in Precision Engineering
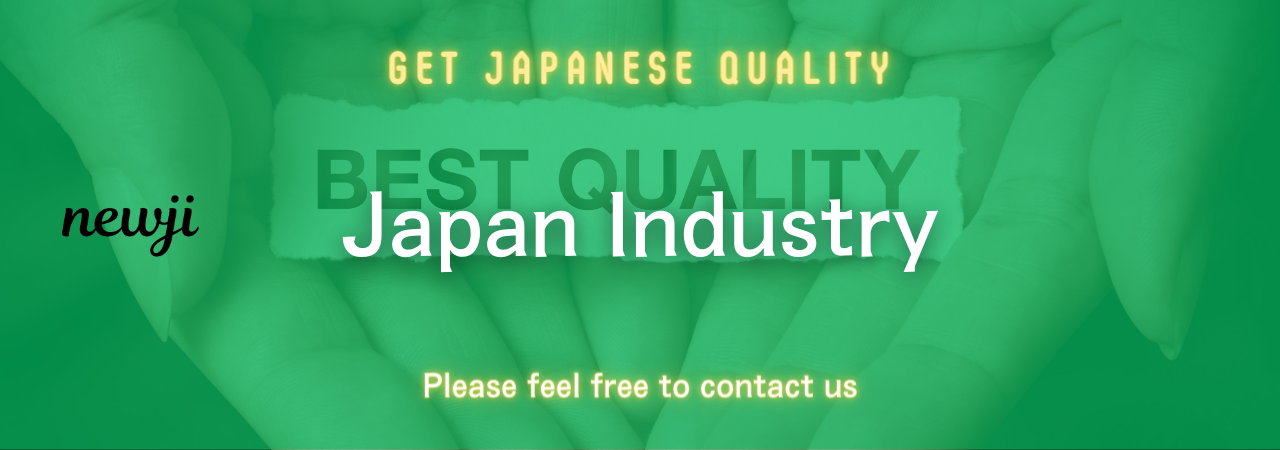
目次
Introduction to Japanese Precision Engineering
Japanese manufacturing has long been synonymous with precision, quality, and innovation. In the realm of precision engineering, abrasives play a pivotal role in maintaining the high standards that Japanese manufacturers are known for. This article delves into how abrasives revolutionize Japanese manufacturing, the advantages and disadvantages of their use, supplier negotiation techniques, market conditions, and best practices in procurement and purchasing.
The Role of Abrasives in Precision Engineering
Abrasives are essential materials used in various manufacturing processes to shape, finish, and improve the surface properties of components. In precision engineering, the quality and performance of abrasives directly impact the final product’s accuracy and durability. Japanese manufacturers leverage advanced abrasive technologies to achieve the tight tolerances and superior finishes required in industries such as automotive, aerospace, and electronics.
Types of Abrasives Used in Japanese Manufacturing
Japanese precision engineering employs a wide range of abrasives, each suited for specific applications:
– **Silicon Carbide:** Known for its hardness and thermal conductivity, it is ideal for grinding non-ferrous metals, ceramics, and glass.
– **Aluminum Oxide:** Versatile and durable, it is commonly used for metalworking and woodworking applications.
– **Diamond Abrasives:** Utilized for ultra-precision grinding and polishing of hard materials like sapphire and ceramics.
– **Ceramic Abrasives:** Offer high thermal stability and are used in applications requiring long tool life and consistent performance.
Applications of Abrasives in Precision Engineering
Abrasives are integral to several precision engineering processes, including:
– **Grinding:** Achieves fine surface finishes and precise dimensions.
– **Polishing:** Enhances surface smoothness and reduces roughness.
– **Cutting:** Facilitates clean and accurate material removal.
– **Deburring:** Removes sharp edges and burrs to ensure safety and functionality.
Advantages of Using Abrasives in Japanese Manufacturing
Incorporating abrasives into manufacturing processes offers numerous benefits that contribute to the overall efficiency and quality of production.
Enhanced Precision and Quality
Abrasives enable Japanese manufacturers to achieve high levels of precision in component fabrication. The ability to control material removal at microscopic levels ensures that products meet stringent quality standards and perform reliably in demanding applications.
Increased Efficiency and Productivity
Advanced abrasive materials and technologies streamline manufacturing processes, reducing cycle times and increasing throughput. This efficiency is crucial in maintaining Japan’s competitive edge in global markets.
Cost-Effectiveness
Despite the initial investment in high-quality abrasives, the long-term benefits include reduced tool wear, lower maintenance costs, and minimized waste. This cost-effectiveness is a significant advantage for manufacturers aiming to optimize their operations.
Improved Surface Finishes
Abrasives contribute to superior surface finishes, which are essential for the functionality and aesthetics of many precision-engineered products. Enhanced surface quality can also lead to better performance and longevity of components.
Disadvantages and Challenges
While abrasives offer substantial benefits, there are challenges and disadvantages associated with their use in manufacturing processes.
High Initial Costs
Premium abrasive materials can be expensive, posing a financial challenge for some manufacturers. The investment may be justified by the long-term gains in efficiency and product quality, but it requires careful financial planning.
Tool Wear and Maintenance
Abrasives themselves can wear down during use, necessitating regular maintenance and replacement. Managing tool wear is critical to maintaining consistent production quality and avoiding unexpected downtime.
Environmental and Safety Concerns
The use of certain abrasive materials can pose environmental and safety risks. Proper handling, storage, and disposal are essential to mitigate these concerns and comply with regulatory standards.
Technical Expertise Required
Effective utilization of abrasives in precision engineering requires specialized knowledge and skills. Manufacturers must invest in training and development to ensure their workforce can maximize the benefits of abrasive technologies.
Supplier Negotiation Techniques
Establishing strong relationships with abrasive suppliers is crucial for securing high-quality materials at competitive prices. Japanese manufacturers employ various negotiation techniques to achieve favorable terms.
Building Long-Term Partnerships
Japanese companies prioritize long-term relationships with suppliers, fostering trust and collaboration. This approach often leads to better pricing, priority access to new products, and customized solutions tailored to the manufacturer’s specific needs.
Leveraging Volume Purchases
By committing to large or consistent orders, manufacturers can negotiate bulk discounts and more favorable payment terms. Suppliers are more likely to offer concessions to clients who provide steady business.
Transparency and Communication
Clear and open communication about requirements, expectations, and feedback helps prevent misunderstandings and ensures that suppliers can meet the manufacturer’s needs effectively. Transparency builds trust and facilitates smoother negotiations.
Exploring Alternative Suppliers
While maintaining strong relationships with existing suppliers, Japanese manufacturers also explore alternative sources to ensure competitive pricing and mitigate supply chain risks. Diversifying suppliers can provide leverage in negotiations and enhance supply chain resilience.
Market Conditions Affecting Abrasive Procurement
Understanding the market dynamics surrounding abrasives is essential for effective procurement and purchasing strategies.
Global Supply Chain Trends
Global supply chain disruptions, such as those caused by geopolitical tensions or pandemics, can impact the availability and cost of abrasives. Manufacturers must stay informed about these trends to anticipate challenges and adjust their procurement strategies accordingly.
Technological Advancements
Innovations in abrasive materials and manufacturing techniques continuously evolve the market. Staying abreast of these advancements allows manufacturers to adopt more efficient and effective abrasives, maintaining their competitive edge.
Price Fluctuations
The cost of raw materials used in abrasives, such as aluminum oxide and diamond, can fluctuate based on market demand and supply conditions. Manufacturers need to implement strategies such as hedging or long-term contracts to manage price volatility.
Regulatory Changes
Environmental and safety regulations governing the use and disposal of abrasives can affect sourcing and production processes. Compliance with these regulations is crucial to avoid legal issues and maintain operational licenses.
Best Practices in Procurement and Purchasing
Implementing best practices in procurement and purchasing can enhance the effectiveness of abrasive utilization in Japanese manufacturing.
Strategic Sourcing
Strategic sourcing involves identifying the most suitable suppliers based on quality, reliability, and cost-effectiveness. This approach ensures that manufacturers secure the best abrasives that meet their technical and financial requirements.
Supplier Evaluation and Selection
Thoroughly evaluating potential suppliers based on their capabilities, quality standards, and past performance is essential. Manufacturers often conduct site visits, audits, and assess certifications to ensure suppliers can consistently deliver high-quality abrasives.
Demand Forecasting
Accurate forecasting of abrasive needs helps in planning purchases, managing inventory levels, and avoiding stockouts or excess inventory. Utilizing data analytics and historical consumption patterns can enhance forecasting accuracy.
Quality Control and Assurance
Implementing stringent quality control measures ensures that abrasives meet the required specifications and performance standards. Regular testing and inspections help maintain product consistency and reliability.
Cost Management
Effective cost management strategies, such as negotiating favorable terms, bulk purchasing, and reducing waste, contribute to overall procurement efficiency. Manufacturers should continuously seek ways to optimize costs without compromising on quality.
Risk Management
Identifying and mitigating risks related to supply chain disruptions, quality issues, and price fluctuations is crucial. Developing contingency plans and diversifying supplier bases can enhance resilience against unforeseen challenges.
Case Studies: Successful Integration of Abrasives in Japanese Manufacturing
Examining real-world examples highlights the effective use of abrasives in enhancing precision engineering within Japanese manufacturing.
Automotive Industry: Enhancing Component Precision
A leading Japanese automotive manufacturer implemented advanced diamond abrasives in their engine component production. This integration resulted in increased precision, reduced wear, and improved overall engine performance. The consistent quality achieved through superior abrasives contributed to the brand’s reputation for reliability and performance.
Aerospace Sector: Achieving Ultra-Precision Standards
In the aerospace industry, a Japanese manufacturer specialized in turbine blades adopted silicon carbide abrasives for grinding and polishing. The enhanced precision and surface finish provided by these abrasives ensured compliance with stringent aerospace standards, leading to successful partnerships with major global aerospace companies.
Electronics Manufacturing: Innovating Surface Finishing
A Japanese electronics manufacturer utilized advanced ceramic abrasives to achieve the necessary surface smoothness for semiconductor components. The improved surface quality contributed to better device performance and longevity, reinforcing the company’s position in the competitive electronics market.
Future Trends in Abrasive Technology
The abrasive industry is continually evolving, with several trends shaping the future of precision engineering in Japanese manufacturing.
Nanotechnology Integration
The incorporation of nanotechnology into abrasives is enabling the creation of ultra-fine abrasive particles. These nanostructured abrasives offer enhanced performance, allowing for even greater precision and superior surface finishes in manufacturing processes.
Eco-Friendly Abrasives
Sustainability is becoming increasingly important, leading to the development of eco-friendly abrasives. These materials are designed to minimize environmental impact through reduced energy consumption, lower emissions, and safer disposal methods, aligning with global sustainability goals.
Smart Abrasives with Embedded Sensors
The advent of smart materials has led to abrasives embedded with sensors that can monitor wear, temperature, and performance in real-time. This innovation allows for predictive maintenance, reducing downtime and ensuring consistent manufacturing quality.
Advanced Coatings and Surface Treatments
Enhancements in coating technologies are improving the durability and performance of abrasives. Advanced surface treatments extend the lifespan of abrasive tools, reduce material consumption, and enhance the efficiency of manufacturing processes.
Implementing Effective Procurement Strategies
To fully capitalize on the benefits of abrasives in precision engineering, Japanese manufacturers must adopt effective procurement strategies.
Collaborative Planning with Suppliers
Engaging in collaborative planning with suppliers fosters a deeper understanding of mutual needs and challenges. This partnership approach can lead to co-development of abrasive solutions tailored to specific manufacturing requirements, enhancing overall efficiency and product quality.
Investing in Supplier Development
Supporting suppliers in improving their processes and capabilities ensures a consistent supply of high-quality abrasives. Investing in supplier development can result in better product innovations, reduced lead times, and enhanced reliability.
Utilizing Technology for Procurement Optimization
Leveraging procurement software and analytics can streamline purchasing processes, improve visibility, and facilitate data-driven decision-making. Technology integration helps in managing supplier relationships, tracking orders, and optimizing inventory levels.
Focusing on Total Cost of Ownership (TCO)
Considering the total cost of ownership, rather than just the initial purchase price, provides a more comprehensive view of procurement decisions. Factors such as tool lifespan, maintenance costs, and operational efficiency should be evaluated to make informed purchasing choices.
Conclusion: The Future of Abrasives in Japanese Precision Engineering
Abrasives are a cornerstone of Japanese precision engineering, driving advancements in manufacturing quality, efficiency, and innovation. By understanding the role of abrasives, leveraging best procurement practices, and staying ahead of market and technological trends, Japanese manufacturers can continue to excel in the global marketplace. The ongoing evolution of abrasive technologies promises even greater enhancements in precision engineering, ensuring that Japanese manufacturing remains at the forefront of excellence and reliability.
資料ダウンロード
QCD調達購買管理クラウド「newji」は、調達購買部門で必要なQCD管理全てを備えた、現場特化型兼クラウド型の今世紀最高の購買管理システムとなります。
ユーザー登録
調達購買業務の効率化だけでなく、システムを導入することで、コスト削減や製品・資材のステータス可視化のほか、属人化していた購買情報の共有化による内部不正防止や統制にも役立ちます。
NEWJI DX
製造業に特化したデジタルトランスフォーメーション(DX)の実現を目指す請負開発型のコンサルティングサービスです。AI、iPaaS、および先端の技術を駆使して、製造プロセスの効率化、業務効率化、チームワーク強化、コスト削減、品質向上を実現します。このサービスは、製造業の課題を深く理解し、それに対する最適なデジタルソリューションを提供することで、企業が持続的な成長とイノベーションを達成できるようサポートします。
オンライン講座
製造業、主に購買・調達部門にお勤めの方々に向けた情報を配信しております。
新任の方やベテランの方、管理職を対象とした幅広いコンテンツをご用意しております。
お問い合わせ
コストダウンが利益に直結する術だと理解していても、なかなか前に進めることができない状況。そんな時は、newjiのコストダウン自動化機能で大きく利益貢献しよう!
(Β版非公開)