- お役立ち記事
- Revolutionizing Japanese Manufacturing: The Power of Barcode and QR Code-Based Inventory Management Systems
月間76,176名の
製造業ご担当者様が閲覧しています*
*2025年3月31日現在のGoogle Analyticsのデータより
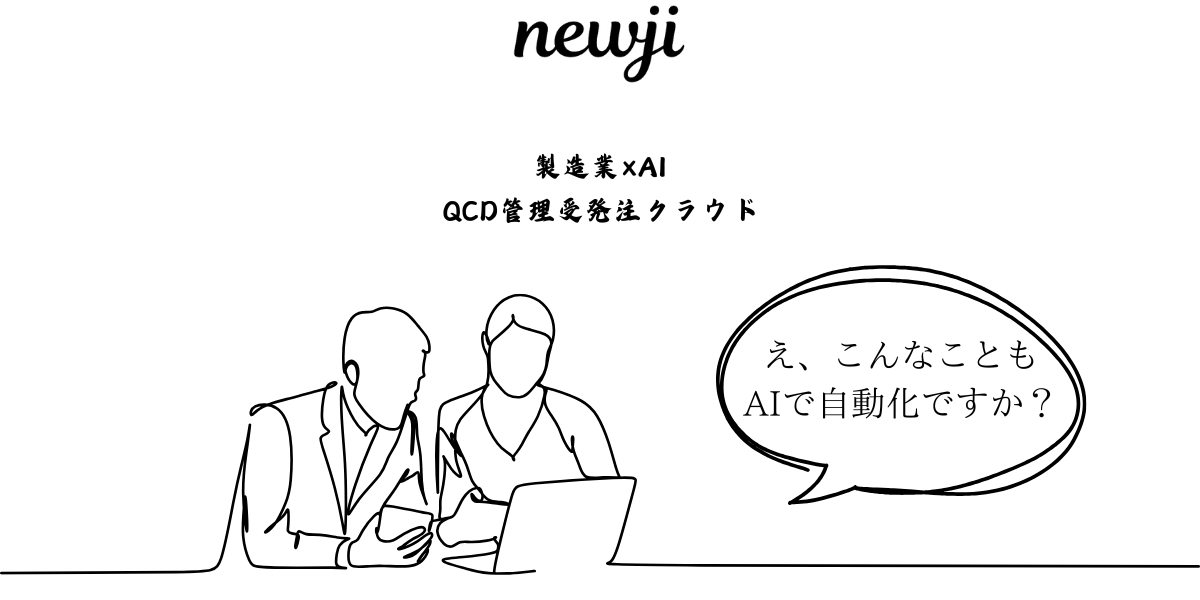
Revolutionizing Japanese Manufacturing: The Power of Barcode and QR Code-Based Inventory Management Systems
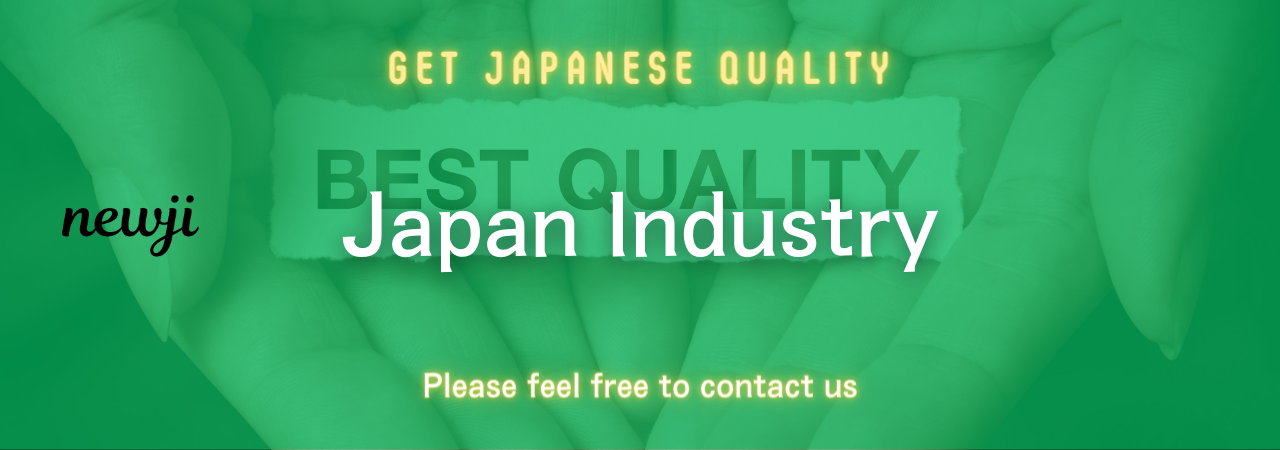
目次
Introduction
In the modern manufacturing landscape, efficient inventory management is a critical factor that can determine the success or failure of operations.
Traditionally, Japanese manufacturing has been lauded for its precision, quality, and efficiency, often setting the benchmark for global standards.
As these industries continue to evolve, incorporating cutting-edge technologies into inventory management systems has become indispensable.
Here, we’ll discuss how barcode and QR code-based inventory management systems are revolutionizing Japanese manufacturing.
The Essence of Inventory Management in Manufacturing
Inventory management involves overseeing and controlling the ordering, storage, and use of components that a company uses in the production of items it sells.
In the context of manufacturing, it directly impacts production schedules, operational efficiency, and ultimately, the bottom line.
In Japan, where Just-In-Time (JIT) production methodologies and Kaizen principles are embedded in the manufacturing ethos, high accuracy in inventory management is vital.
Traditional manual methods are increasingly unsustainable in the face of global competition, frequent product changes, and the demand for mass customization.
The Role of Barcode and QR Code Technologies
Understanding Barcode and QR Code Technologies
Barcodes and QR codes are two types of machine-readable codes that store information about the objects they’re attached to.
Barcodes are one-dimensional and read horizontally while QR codes are two-dimensional and can store more complex data.
In practice, both of these codes are used to track and manage inventory but offer different capacities and applications.
How Barcodes Enhance Inventory Management
Barcodes store alphanumeric information, usually only a few dozen characters, which are primarily read by laser scanners.
They are ideal for tracking large volumes of products quickly and efficiently.
When integrated into an inventory management system, barcodes help to:
1. **Automate Data Entry**: This reduces human errors associated with manual data entry.
2. **Speed Up Processes**: Scanning barcodes for inventory management is much faster than manual entries.
3. **Improve Accuracy**: Barcodes improve the accuracy of stock levels and order fulfillment.
The Advantages of QR Codes in Inventory Management
QR codes, short for Quick Response codes, can hold much more information than traditional barcodes.
They can store URLs, product descriptions, and even complex instructions.
They are typically scanned using camera-based devices like smartphones and tablets.
Advantages include:
1. **Enhanced Data Capacity**: Store more detailed information on inventory.
2. **Versatility**: QR codes can direct users to web pages for real-time updates, user manuals, or instructional videos.
3. **Error Correction**: QR codes can still function even if part of the code is damaged.
Practical Applications in Japanese Manufacturing
Procurement and Inbound Logistics
For procurement, barcode and QR codes can streamline the receipt and verification of materials received from suppliers.
By scanning barcodes provided by suppliers, companies can automatically update their inventory systems, verify the accuracy of shipments, and expedite the validation process.
In the context of Japanese manufacturing, this aligns well with the high standards for quality control and precision.
Production and Assembly Lines
Each component in a production line can be tracked using barcode and QR codes, ensuring that the exact number of parts are available where and when they are needed.
This real-time tracking enables manufacturers to implement JIT production more effectively, reducing stock levels and waste.
For example, Toyota has implemented extensive barcode systems to support their lean manufacturing processes.
Quality Control
In a high-precision environment like Japanese manufacturing, monitoring the quality of goods at every stage is crucial.
QR codes can include detailed product information, enabling quick access to specifications, quality assurance standards, and audit trails.
This helps in swiftly isolating defective batches and tracing issues back to their source, thereby maintaining high-quality standards.
Advantages of Integrating Barcode and QR Code Systems
Efficiency and Accuracy
One of the significant advantages is the boost in efficiency and accuracy.
Automating data entry minimizes human errors and speeds up inventory tracking, saving time that can be better spent on value-adding activities.
The seamless integration of scanning systems into ERP (Enterprise Resource Planning) software means that inventory levels are updated in real-time, providing an accurate picture of stock at any given moment.
Cost Reduction
Efficient inventory management naturally leads to cost savings by reducing carrying costs, minimising stockouts, and smoother operational workflows.
Given the high cost structure of Japanese manufacturing, these systems can contribute significantly by optimizing resource allocation and reducing waste.
Enhanced Customer Satisfaction
With real-time inventory tracking, fulfilment can be more reliable and quicker, leading to higher customer satisfaction.
This is particularly pertinent in exporting goods, where accurate inventory levels help meet international demand and deadlines.
Challenges in Implementing Barcode and QR Code Systems
Initial Setup Costs
The initial investment in barcode and QR code systems, including software, scanners, and training, can be substantial.
This can be a hurdle for small to medium-sized enterprises (SMEs) despite the long-term benefits.
However, considering the ROI and potential for cost savings, this initial outlay is often justified.
Integration with Existing Systems
Another challenge is ensuring that new inventory management systems integrate smoothly with existing ERP or Manufacturing Execution Systems (MES).
This requires thorough planning, customisation, and potentially overcoming compatibility issues.
Manufacturers need to prepare for this by conducting extensive trials and gradually phasing in new systems.
Employee Training
To fully realise the benefits, adequate training for the workforce is crucial.
Employees need to be proficient in using the scanning equipment and software, which necessitates both time and resources.
A well-conceived training program can mitigate this risk, transforming the workforce into a more efficient team.
Best Practices for Implementing Barcode and QR Code Systems
Conducting a Needs Assessment
Before diving into implementation, conduct a thorough needs assessment.
Identify pain points in your current inventory management process and envisage how barcode and QR codes can address these challenges.
This could involve mapping out the supply chain, assessing inventory turnover rates, or identifying bottlenecks in production workflows.
Choosing the Right Technology
Not all barcode or QR code systems are created equal.
Evaluate different solutions based on your operational needs, budget, and compatibility with existing systems.
Consider factors like the durability of the labels, the scanning technology, and the capacity for future expansion.
Pilot Testing
Implement a pilot program to test the new system in a controlled environment before a full-scale roll-out.
This will help identify any issues without disrupting your broader operations.
Collect feedback from employees and make necessary adjustments before deploying the system company-wide.
Employee Involvement and Training
Involve your employees in the transition process from the outset. Their insights can be invaluable in identifying practical issues and ensuring a smooth transition.
A detailed training program should cover both the technical aspects of operating the new systems and the strategic importance of accurate inventory management.
Regular Audits and Updates
Implement regular audits and updates to ensure the system is running efficiently.
Technology and requirements constantly evolve, so keep updating the system and training all concerned to stay abreast of new features and functionalities.
The Future of Inventory Management in Japanese Manufacturing
Artificial Intelligence and Machine Learning
The next wave of improvements in inventory management will likely involve artificial intelligence (AI) and machine learning.
These technologies can forecast demand, optimize stock levels, and even flag potential supply chain disruptions before they occur.
When integrated with barcode and QR code systems, AI can make inventory management smarter and more responsive.
The Internet of Things (IoT)
IoT can further enhance inventory management by providing real-time data from interconnected devices across the supply chain.
Smart sensors can track the condition of goods, monitor inventory levels, and even automate reordering processes, ensuring that supply chains are more responsive and resilient.
Blockchain and Supply Chain Transparency
Blockchain technology could revolutionize supply chain transparency, enabling secure, tamper-proof records of every transaction and movement in the supply chain.
This will make it easier to track inventory, ensure authenticity, and maintain detailed records for compliance and auditing purposes.
Conclusion
The integration of barcode and QR code-based inventory management systems is revolutionizing Japanese manufacturing.
These technologies offer significant advantages in terms of efficiency, accuracy, and cost savings.
While challenges exist in the form of initial setup costs, system integration, and employee training, the long-term benefits far outweigh the investments.
By adhering to best practices and staying abreast of technological advancements, Japanese manufacturers can continue to lead the world in efficiency, quality, and innovation.
Adopting these advanced inventory management systems is not just about improving operational efficiency; it is about setting a future-proof strategy that ensures sustained competitive advantage.
資料ダウンロード
QCD管理受発注クラウド「newji」は、受発注部門で必要なQCD管理全てを備えた、現場特化型兼クラウド型の今世紀最高の受発注管理システムとなります。
ユーザー登録
受発注業務の効率化だけでなく、システムを導入することで、コスト削減や製品・資材のステータス可視化のほか、属人化していた受発注情報の共有化による内部不正防止や統制にも役立ちます。
NEWJI DX
製造業に特化したデジタルトランスフォーメーション(DX)の実現を目指す請負開発型のコンサルティングサービスです。AI、iPaaS、および先端の技術を駆使して、製造プロセスの効率化、業務効率化、チームワーク強化、コスト削減、品質向上を実現します。このサービスは、製造業の課題を深く理解し、それに対する最適なデジタルソリューションを提供することで、企業が持続的な成長とイノベーションを達成できるようサポートします。
製造業ニュース解説
製造業、主に購買・調達部門にお勤めの方々に向けた情報を配信しております。
新任の方やベテランの方、管理職を対象とした幅広いコンテンツをご用意しております。
お問い合わせ
コストダウンが利益に直結する術だと理解していても、なかなか前に進めることができない状況。そんな時は、newjiのコストダウン自動化機能で大きく利益貢献しよう!
(β版非公開)