- お役立ち記事
- Revolutionizing Japanese Manufacturing: The Power of Equipment Data Collection Tools in Industry 4.0
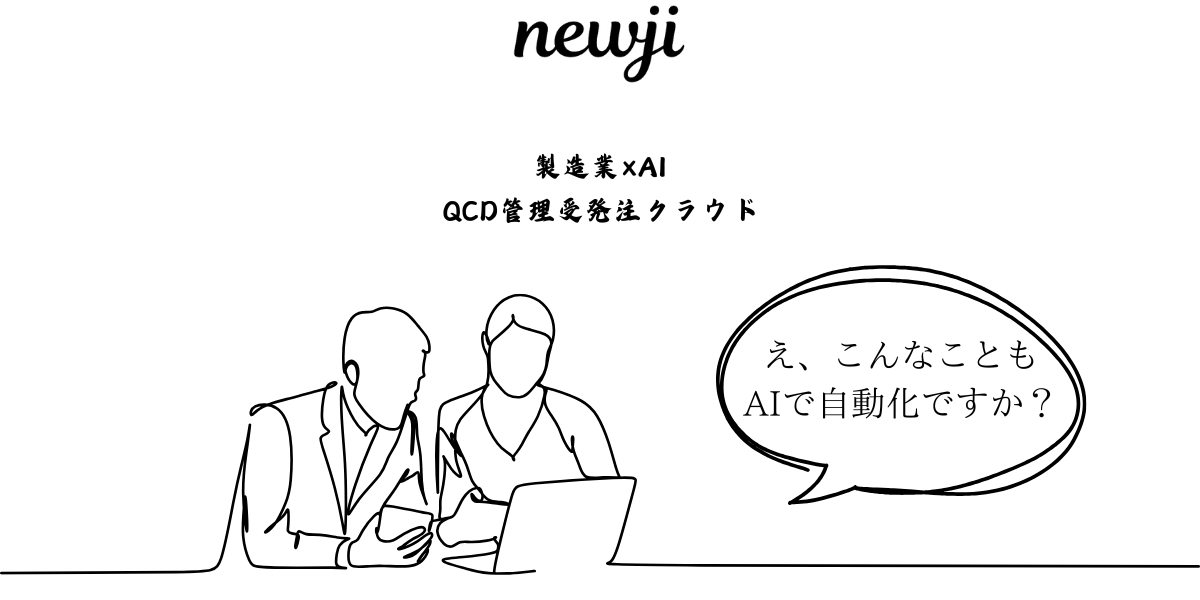
Revolutionizing Japanese Manufacturing: The Power of Equipment Data Collection Tools in Industry 4.0
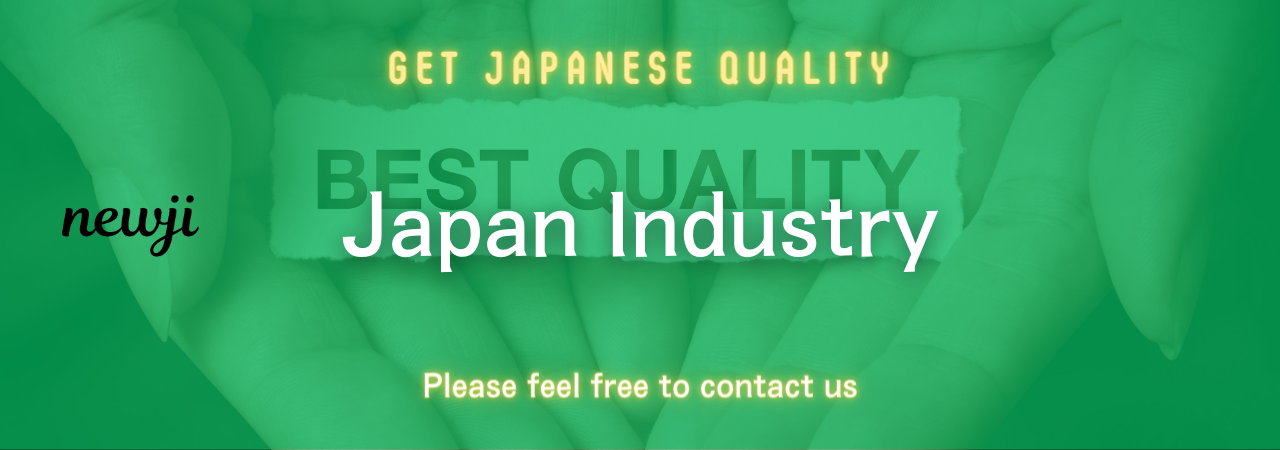
目次
Introduction
The industrial landscape is undergoing a significant transformation with the advent of Industry 4.0, characterized by the fusion of digital technologies with traditional manufacturing processes.
Japan, known for its sophisticated manufacturing prowess, is leading the charge in this revolution.
One of the key components driving this change is equipment data collection tools.
These tools play a crucial role in optimizing production, enhancing quality control, and streamlining supply chain operations.
The Role of Equipment Data Collection Tools
Enhancing Production Efficiency
Equipment data collection tools have become the cornerstone of smart manufacturing.
By capturing real-time data from machinery, these tools provide insights into equipment performance, usage patterns, and potential bottlenecks.
For instance, predictive maintenance can be implemented by analyzing machine data, thereby preventing unexpected downtimes and extending the lifespan of equipment.
Improving Quality Control
In the realm of quality control, data collection tools offer unprecedented advantages.
They enable continuous monitoring of production processes, ensuring that products meet stringent quality standards.
Anomalies and defects can be detected early, reducing the rate of rejected products.
Furthermore, data-driven insights allow for the fine-tuning of production parameters, leading to consistent product quality.
Streamlining Supply Chain Operations
Supply chain efficiency is another area where equipment data collection tools are making a significant impact.
By providing visibility into equipment status and production output, these tools enable better planning and coordination across the supply chain.
This results in reduced lead times, optimizes inventory levels, and ultimately increases customer satisfaction.
Advantages of Equipment Data Collection in Japanese Manufacturing
Precision and Reliability
Japanese manufacturing is renowned for its precision and reliability.
Equipment data collection tools enhance these attributes by offering meticulous monitoring capabilities.
Accurate data collection ensures that every detail of the production process is tracked, maintaining the high standards synonymous with Japanese products.
Incremental Improvement (Kaizen)
Kaizen, or continuous improvement, is a core principle in Japanese manufacturing.
Data collection tools provide the metrics necessary to implement Kaizen effectively.
By analyzing performance data, manufacturers can identify areas for improvement and make incremental changes, leading to significant long-term gains.
Integration with Advanced Technologies
Japanese manufacturers are at the forefront of integrating advanced technologies such as IoT, AI, and machine learning into their operations.
Equipment data collection tools serve as the foundation for these integrations.
For example, IoT sensors can collect real-time data, which is then analyzed using AI algorithms to optimize production processes.
Disadvantages and Challenges
Initial Investment Costs
Implementing equipment data collection tools requires significant initial investment in hardware, software, and training.
While the long-term benefits are substantial, the upfront costs can be a barrier for smaller manufacturers.
Data Security Concerns
The collection and transmission of vast amounts of data introduce security risks.
Manufacturers must invest in robust cybersecurity measures to protect sensitive production data from breaches and cyberattacks.
Data Overload and Management
The sheer volume of data generated by modern manufacturing equipment can be overwhelming.
Effective data management strategies are essential to ensure that the collected data is useful and actionable.
Best Practices for Implementing Equipment Data Collection
Start with a Clear Strategy
Before implementing data collection tools, manufacturers should have a clear strategy outlining objectives, key performance indicators (KPIs), and expected outcomes.
This ensures that the data collected aligns with the organization’s goals.
Pilot Programs
Launching pilot programs allows manufacturers to test the effectiveness of equipment data collection tools on a smaller scale.
This can help identify potential issues and refine the implementation process before a full-scale rollout.
Employee Training
Proper training is essential for the successful implementation of data collection tools.
Employees need to understand how to use the technology, interpret the data, and apply insights to their work processes.
Negotiation Techniques with Japanese Suppliers
Understanding Cultural Nuances
Successful negotiation with Japanese suppliers often hinges on understanding cultural nuances.
Building trust and demonstrating respect are critical components.
Patience and a willingness to engage in detailed discussions can significantly aid in reaching favorable agreements.
Leverage Data-Driven Insights
When negotiating with suppliers, leveraging data-driven insights can be advantageous.
Clear evidence of production efficiency, quality control success, and supply chain reliability can support negotiations for better terms and conditions.
Long-Term Partnerships
Japanese business culture places a high value on long-term relationships.
Fostering a partnership mindset rather than a transactional approach can lead to more fruitful negotiations and collaborations.
Market Conditions and Trends
Adoption of Industry 4.0 Technologies
The global manufacturing sector is increasingly embracing Industry 4.0 technologies.
Japan, in particular, is investing heavily in IoT, AI, and big data analytics to maintain its competitive edge.
This creates a fertile ground for the adoption of equipment data collection tools.
Focus on Sustainability
Sustainability is becoming a significant focus in manufacturing.
Data collection tools contribute to sustainable practices by enabling more efficient resource use, reducing waste, and lowering carbon footprints.
Customization and Flexibility
There is a growing demand for customized and flexible manufacturing solutions.
Equipment data collection tools offer the agility needed to adapt to changing market demands and produce tailored products efficiently.
Case Studies: Success Stories from Japanese Manufacturers
Case Study 1: Toyota
Toyota, a leader in automotive manufacturing, has leveraged equipment data collection tools to enhance its production system.
By implementing IoT sensors and data analytics, Toyota has improved predictive maintenance, leading to a significant reduction in unexpected downtimes and associated costs.
Case Study 2: Panasonic
Panasonic uses data collection tools to optimize its electronics manufacturing process.
Through real-time monitoring and machine learning algorithms, Panasonic has achieved higher product quality and consistency, reducing defects and customer returns.
Case Study 3: Sony
Sony has integrated data collection tools into its varied manufacturing operations.
This integration has resulted in enhanced process efficiencies, better resource management, and a more agile production system that can quickly respond to market changes.
Conclusion
The integration of equipment data collection tools into Japanese manufacturing is revolutionizing the industry.
By enhancing production efficiency, improving quality control, and streamlining supply chain operations, these tools provide a competitive edge.
Despite the challenges, the benefits of adopting this technology are manifold.
With a clear strategy, proper training, and a focus on long-term partnerships, manufacturers can successfully leverage equipment data collection tools to thrive in the era of Industry 4.0.
As the market continues to evolve, the emphasis on precision, reliability, and continuous improvement will drive further advancements.
For companies looking to excel, investing in and mastering equipment data collection tools is no longer optional – it is a necessity.
資料ダウンロード
QCD調達購買管理クラウド「newji」は、調達購買部門で必要なQCD管理全てを備えた、現場特化型兼クラウド型の今世紀最高の購買管理システムとなります。
ユーザー登録
調達購買業務の効率化だけでなく、システムを導入することで、コスト削減や製品・資材のステータス可視化のほか、属人化していた購買情報の共有化による内部不正防止や統制にも役立ちます。
NEWJI DX
製造業に特化したデジタルトランスフォーメーション(DX)の実現を目指す請負開発型のコンサルティングサービスです。AI、iPaaS、および先端の技術を駆使して、製造プロセスの効率化、業務効率化、チームワーク強化、コスト削減、品質向上を実現します。このサービスは、製造業の課題を深く理解し、それに対する最適なデジタルソリューションを提供することで、企業が持続的な成長とイノベーションを達成できるようサポートします。
オンライン講座
製造業、主に購買・調達部門にお勤めの方々に向けた情報を配信しております。
新任の方やベテランの方、管理職を対象とした幅広いコンテンツをご用意しております。
お問い合わせ
コストダウンが利益に直結する術だと理解していても、なかなか前に進めることができない状況。そんな時は、newjiのコストダウン自動化機能で大きく利益貢献しよう!
(Β版非公開)