- お役立ち記事
- Revolutionizing Japanese Manufacturing: The Power of Error Correction in Quality Control
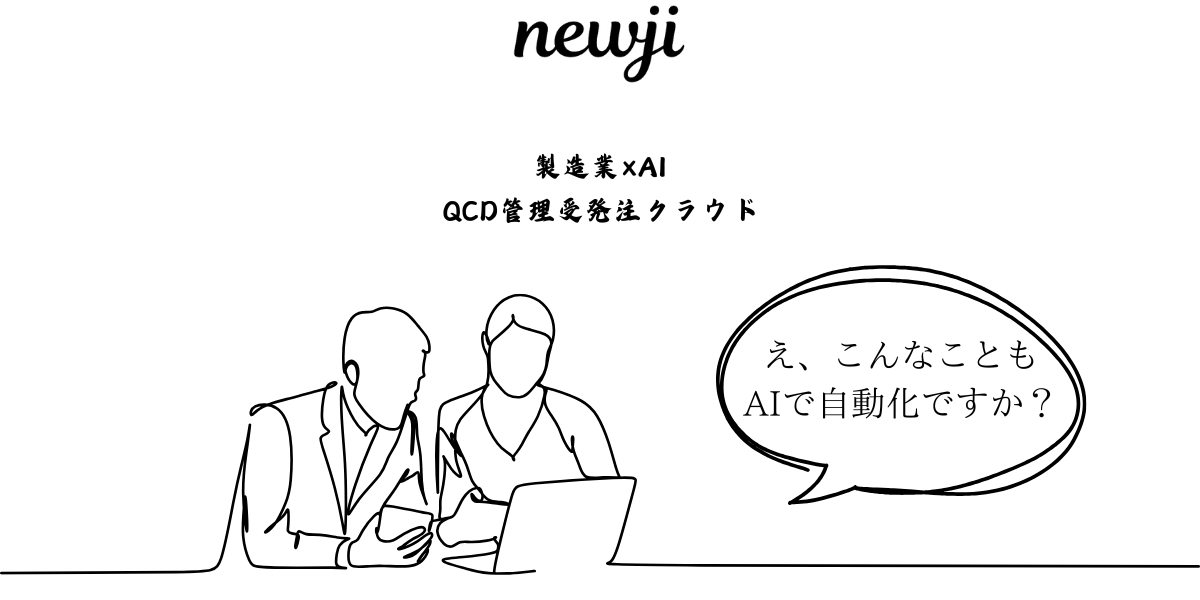
Revolutionizing Japanese Manufacturing: The Power of Error Correction in Quality Control
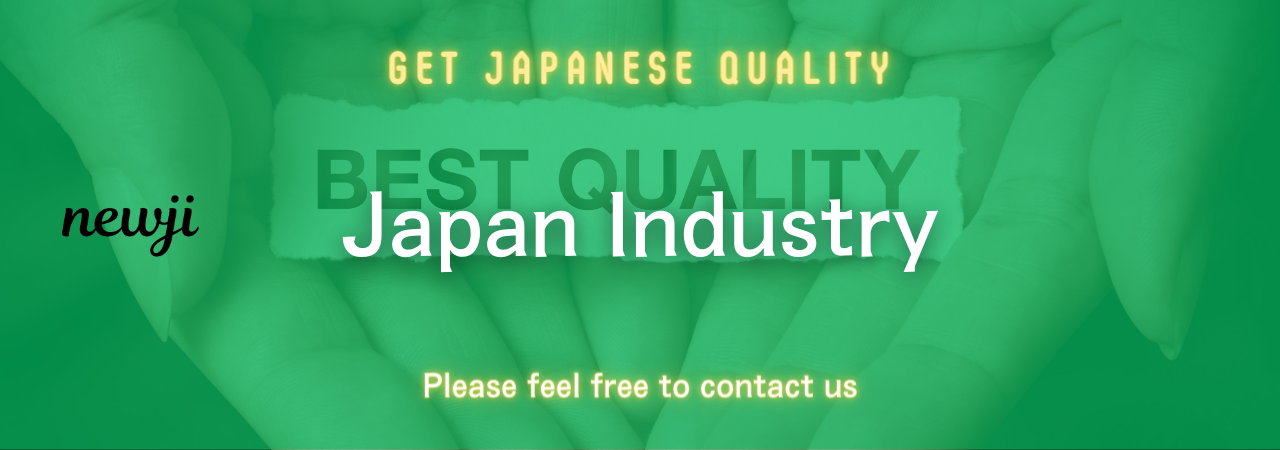
目次
Introduction to Quality Control in Japanese Manufacturing
Japanese manufacturing has long been synonymous with quality and precision. Central to this reputation is the rigorous quality control processes that Japanese companies employ. These processes are not just about maintaining standards but also about continuous improvement and error correction. Understanding these methodologies can provide significant advantages to international companies involved in procurement and purchasing from Japan.
The Philosophy Behind Error Correction
Kaizen: Continuous Improvement
Kaizen, a cornerstone of Japanese manufacturing, emphasizes continuous improvement. This philosophy encourages all employees to look for ways to enhance processes, reduce waste, and improve quality. In procurement and purchasing, this means that suppliers are always striving to provide better products and services, ensuring that the quality you receive only gets better over time.
Poka-Yoke: Mistake-Proofing
Poka-yoke refers to error-proofing mechanisms designed to prevent mistakes before they occur. In the context of quality control, this involves designing processes that inherently reduce the likelihood of errors. For buyers, this translates to more reliable and consistent products, minimizing the risk of defects and associated costs.
Advantages of Japanese Quality Control Practices
High-Quality Standards
Japanese suppliers adhere to stringent quality standards, often exceeding international benchmarks. This commitment ensures that the products you procure are reliable, durable, and perform consistently.
Efficient Supplier Relationships
The emphasis on quality fosters strong relationships between buyers and suppliers. Japanese companies prioritize long-term partnerships, offering better terms, support, and collaboration opportunities to their partners.
Cost-Effectiveness
While the initial cost may sometimes be higher, the overall cost-effectiveness is achieved through reduced defects, lower warranty claims, and decreased downtime. This long-term perspective can lead to significant savings and increased profitability.
Challenges and Considerations
Cultural Differences
Understanding and respecting cultural nuances is essential when dealing with Japanese suppliers. Differences in communication styles, decision-making processes, and business etiquette can pose challenges if not properly navigated.
Language Barriers
While many Japanese companies operate in English, language barriers can still exist. Ensuring clear and precise communication is crucial to avoid misunderstandings and ensure that specifications and requirements are met accurately.
Lead Times
Japanese manufacturing processes may involve longer lead times due to their emphasis on quality and precision. Planning and forecasting are essential to align procurement schedules with supplier capabilities.
Effective Supplier Negotiation Techniques
Building Trust and Rapport
Establishing a strong, trust-based relationship is fundamental in Japanese business culture. Taking the time to build rapport can lead to more favorable negotiations and stronger partnerships.
Understanding Supplier Needs
By comprehending the supplier’s business objectives and constraints, buyers can negotiate terms that are mutually beneficial. This approach fosters collaboration and long-term success.
Leveraging Quality Control Insights
Using the knowledge of Japanese quality control practices, buyers can discuss specific quality metrics, error correction mechanisms, and continuous improvement initiatives. This demonstrates a deep understanding and respect for the supplier’s processes, facilitating more effective negotiations.
Market Conditions and Trends
Technological Advancements
Japanese manufacturers are at the forefront of technological innovation, integrating automation, robotics, and AI into their production processes. Staying abreast of these advancements can provide buyers with access to cutting-edge products and more efficient production capabilities.
Sustainability Practices
There is a growing emphasis on sustainability and environmentally friendly practices in Japanese manufacturing. Suppliers are increasingly adopting green technologies and sustainable processes, which can be a significant advantage for companies aiming to meet their own sustainability goals.
Global Supply Chain Dynamics
Understanding the global supply chain landscape is crucial. Factors such as geopolitical shifts, trade policies, and logistical challenges can impact procurement strategies. Japanese suppliers are adept at navigating these dynamics, ensuring reliability and resilience in supply chains.
Best Practices for Procurement and Purchasing
Thorough Supplier Evaluation
Conduct comprehensive assessments of potential suppliers, focusing on their quality control processes, reliability, financial stability, and ability to meet your specific needs. Site visits and audits can provide valuable insights into their operations.
Clear and Detailed Specifications
Provide precise and comprehensive product specifications to ensure that suppliers fully understand your requirements. Clear communication helps prevent errors and ensures that the final products meet your expectations.
Collaborative Relationship Management
Foster a collaborative relationship with your suppliers. Regular communication, joint problem-solving, and sharing of best practices can lead to continuous improvement and mutual success.
Continuous Monitoring and Feedback
Implement a system for ongoing monitoring of supplier performance. Providing regular feedback helps suppliers understand your expectations and areas for improvement, ensuring sustained quality and performance.
Implementing Japanese Quality Control Techniques
Adopting Kaizen in Procurement
Incorporate the Kaizen philosophy into your procurement processes. Encourage your team to seek continuous improvements in sourcing strategies, supplier management, and cost optimization.
Utilizing Poka-Yoke in Supply Chains
Integrate Poka-yoke principles to minimize errors in the supply chain. This could involve implementing automated checks, standardized procedures, and clear documentation to ensure accuracy and consistency.
Emphasizing Training and Development
Invest in training your procurement and purchasing teams in Japanese quality control methodologies. Understanding these techniques can enhance your ability to collaborate effectively with Japanese suppliers and drive quality improvements.
Case Studies: Success Stories in Japanese Procurement
Automotive Industry Collaborations
Many international automotive companies have successfully partnered with Japanese suppliers to enhance their production quality and efficiency. These collaborations have led to the development of high-performance components and streamlined manufacturing processes.
Electronics Manufacturing Partnerships
Global electronics firms have leveraged Japanese quality control practices to produce reliable and innovative products. By adopting Japanese methodologies, these companies have improved product durability and customer satisfaction.
Industrial Equipment Supply Chains
Japanese suppliers of industrial equipment have enabled global manufacturers to achieve higher levels of precision and reliability in their operations. The integration of advanced quality control techniques has been pivotal in these successes.
Future Outlook: The Evolution of Quality Control
The landscape of manufacturing and quality control is continuously evolving. Japanese manufacturers are likely to lead the way with advancements in automation, AI, and sustainable practices. For international companies, staying informed and adapting to these changes will be crucial in maintaining competitive advantage and ensuring the highest quality in their procurement and purchasing strategies.
Conclusion
Revolutionizing Japanese manufacturing through the power of error correction in quality control offers substantial benefits to international procurement and purchasing departments. By embracing Japanese philosophies like Kaizen and Poka-yoke, understanding the cultural and operational nuances, and implementing best practices in supplier management, companies can achieve unparalleled quality and efficiency in their supply chains. Building strong, collaborative relationships with Japanese suppliers not only ensures high-quality products but also fosters long-term partnerships that drive continuous improvement and mutual success.
資料ダウンロード
QCD調達購買管理クラウド「newji」は、調達購買部門で必要なQCD管理全てを備えた、現場特化型兼クラウド型の今世紀最高の購買管理システムとなります。
ユーザー登録
調達購買業務の効率化だけでなく、システムを導入することで、コスト削減や製品・資材のステータス可視化のほか、属人化していた購買情報の共有化による内部不正防止や統制にも役立ちます。
NEWJI DX
製造業に特化したデジタルトランスフォーメーション(DX)の実現を目指す請負開発型のコンサルティングサービスです。AI、iPaaS、および先端の技術を駆使して、製造プロセスの効率化、業務効率化、チームワーク強化、コスト削減、品質向上を実現します。このサービスは、製造業の課題を深く理解し、それに対する最適なデジタルソリューションを提供することで、企業が持続的な成長とイノベーションを達成できるようサポートします。
オンライン講座
製造業、主に購買・調達部門にお勤めの方々に向けた情報を配信しております。
新任の方やベテランの方、管理職を対象とした幅広いコンテンツをご用意しております。
お問い合わせ
コストダウンが利益に直結する術だと理解していても、なかなか前に進めることができない状況。そんな時は、newjiのコストダウン自動化機能で大きく利益貢献しよう!
(Β版非公開)