- お役立ち記事
- Revolutionizing Japanese Manufacturing: The Power of Predictive Maintenance
Revolutionizing Japanese Manufacturing: The Power of Predictive Maintenance
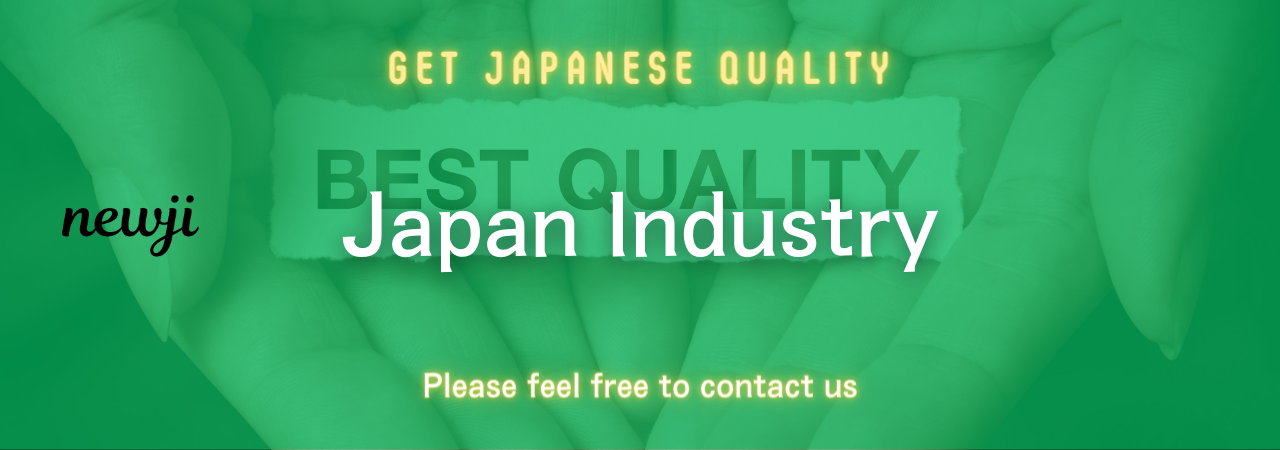
目次
Introduction to Predictive Maintenance in Japanese Manufacturing
Predictive maintenance is transforming the landscape of Japanese manufacturing by leveraging advanced technologies to anticipate equipment failures before they occur. This proactive approach not only enhances operational efficiency but also significantly reduces downtime and maintenance costs. In an industry renowned for its precision and reliability, integrating predictive maintenance systems is a strategic move that aligns with the core principles of Japanese manufacturing excellence.
The Role of Procurement and Purchasing in Predictive Maintenance
Effective procurement and purchasing strategies are pivotal in implementing predictive maintenance. Sourcing the right technology and establishing strong relationships with suppliers ensures that manufacturing processes remain uninterrupted and optimized.
Sourcing Advanced Technologies
Procurement teams must identify and acquire state-of-the-art predictive maintenance tools such as IoT sensors, data analytics platforms, and machine learning software. These technologies are essential for monitoring equipment health in real-time and generating actionable insights.
Building Strategic Supplier Relationships
Developing partnerships with reliable suppliers allows for seamless integration of predictive maintenance solutions. Collaborative relationships enable better negotiation outcomes, ensuring that manufacturers receive high-quality equipment and timely support.
Advantages of Implementing Predictive Maintenance
Adopting predictive maintenance offers numerous benefits that contribute to the overall efficiency and competitiveness of Japanese manufacturing firms.
Enhanced Equipment Reliability
Predictive maintenance ensures that machinery operates at peak performance by preventing unexpected breakdowns. This reliability is crucial for maintaining production schedules and meeting customer demands consistently.
Cost Savings
By addressing issues before they escalate, manufacturers can avoid costly repairs and extend the lifespan of their equipment. Additionally, optimized maintenance schedules reduce labor costs and minimize resource wastage.
Improved Safety and Compliance
Regular monitoring and maintenance help in identifying potential safety hazards, ensuring that manufacturing environments adhere to stringent safety standards and regulatory requirements.
Challenges and Disadvantages
While predictive maintenance offers significant advantages, there are challenges that manufacturers must navigate to realize its full potential.
High Initial Investment
Implementing predictive maintenance systems requires substantial upfront investment in technology and training. This financial barrier can be a deterrent for some organizations, especially smaller manufacturers.
Data Management and Integration
Handling vast amounts of data generated by predictive maintenance tools can be daunting. Integrating this data with existing systems demands robust IT infrastructure and expertise, which may not be readily available in all manufacturing setups.
Skill Gap and Training
The successful adoption of predictive maintenance relies on having skilled personnel who can interpret data and respond appropriately. Bridging the skill gap through training and development is essential but can be time-consuming and resource-intensive.
Supplier Negotiation Techniques
Negotiating effectively with suppliers is crucial for securing the best terms and ensuring the successful implementation of predictive maintenance systems.
Understand Supplier Capabilities
Before entering negotiations, it is vital to thoroughly assess the supplier’s technological expertise, reliability, and track record in delivering predictive maintenance solutions. This understanding forms the basis for informed negotiation strategies.
Leverage Long-Term Partnerships
Emphasizing the potential for long-term collaboration can provide leverage in negotiations. Suppliers are more likely to offer favorable terms if they anticipate an ongoing business relationship.
Focus on Total Cost of Ownership
Rather than solely negotiating on price, consider the total cost of ownership, including installation, maintenance, training, and support services. A holistic view ensures that the chosen solution is cost-effective over its entire lifecycle.
Market Conditions Influencing Predictive Maintenance
The adoption and effectiveness of predictive maintenance are influenced by various market conditions that manufacturers must consider.
Technological Advancements
Rapid advancements in IoT, AI, and machine learning are continually shaping the capabilities of predictive maintenance systems. Staying abreast of these developments is crucial for maintaining a competitive edge.
Global Supply Chain Dynamics
Fluctuations in global supply chains, including delays and material shortages, can impact the implementation of predictive maintenance. Manufacturers must develop flexible strategies to mitigate these risks.
Regulatory Environment
Compliance with international and local regulations regarding data privacy, machinery standards, and safety protocols can influence the deployment of predictive maintenance solutions. Navigating these regulations is essential for successful implementation.
Best Practices for Implementing Predictive Maintenance
Adopting best practices ensures that the integration of predictive maintenance into manufacturing processes is smooth and effective.
Comprehensive Planning and Assessment
Begin with a thorough assessment of current equipment and maintenance practices. Identify critical machinery that would benefit most from predictive maintenance and develop a detailed implementation plan.
Invest in Training and Development
Equip your workforce with the necessary skills to manage and utilize predictive maintenance tools. Continuous training ensures that employees can effectively interpret data and make informed decisions.
Utilize Data Analytics Effectively
Harness the power of data analytics to transform raw data into meaningful insights. Implementing robust data management systems will facilitate better decision-making and enhance the overall maintenance strategy.
Continuous Monitoring and Improvement
Predictive maintenance is not a set-and-forget solution. Regularly monitor system performance, gather feedback, and make adjustments as necessary to optimize maintenance processes and outcomes.
Case Studies: Success Stories in Japanese Manufacturing
Examining real-world examples demonstrates the tangible benefits of predictive maintenance in enhancing manufacturing operations.
Automotive Industry
A leading Japanese automotive manufacturer implemented predictive maintenance across its assembly lines, resulting in a 20% reduction in downtime and a 15% increase in overall equipment effectiveness. By anticipating machinery failures, the company maintained high production standards and met tight delivery schedules.
Electronics Manufacturing
An electronics manufacturer adopted predictive maintenance to monitor sensitive fabrication equipment. The proactive approach minimized defects and ensured consistent product quality, giving the company a competitive advantage in the market.
Future Trends in Predictive Maintenance
The future of predictive maintenance in Japanese manufacturing is poised for further advancements driven by emerging technologies and evolving industry needs.
Integration with Artificial Intelligence
AI will play an increasingly significant role in predictive maintenance by enhancing the accuracy of failure predictions and enabling more sophisticated data analysis techniques.
Edge Computing
Edge computing allows for real-time data processing at the source, reducing latency and enabling quicker responses to potential equipment issues. This technology will enhance the effectiveness of predictive maintenance systems.
Sustainability and Energy Efficiency
Predictive maintenance contributes to sustainability efforts by optimizing energy use and reducing waste. Future implementations will likely focus on environmentally friendly practices alongside operational efficiency.
Conclusion
Predictive maintenance is revolutionizing Japanese manufacturing by fostering a proactive approach to equipment management. Through strategic procurement and purchasing, manufacturers can harness the power of advanced technologies to enhance reliability, reduce costs, and maintain high-quality standards. While challenges such as initial investments and data management persist, the benefits of predictive maintenance far outweigh the drawbacks. By adopting best practices and staying attuned to market trends, Japanese manufacturers can continue to lead the way in innovation and excellence.
資料ダウンロード
QCD調達購買管理クラウド「newji」は、調達購買部門で必要なQCD管理全てを備えた、現場特化型兼クラウド型の今世紀最高の購買管理システムとなります。
ユーザー登録
調達購買業務の効率化だけでなく、システムを導入することで、コスト削減や製品・資材のステータス可視化のほか、属人化していた購買情報の共有化による内部不正防止や統制にも役立ちます。
NEWJI DX
製造業に特化したデジタルトランスフォーメーション(DX)の実現を目指す請負開発型のコンサルティングサービスです。AI、iPaaS、および先端の技術を駆使して、製造プロセスの効率化、業務効率化、チームワーク強化、コスト削減、品質向上を実現します。このサービスは、製造業の課題を深く理解し、それに対する最適なデジタルソリューションを提供することで、企業が持続的な成長とイノベーションを達成できるようサポートします。
オンライン講座
製造業、主に購買・調達部門にお勤めの方々に向けた情報を配信しております。
新任の方やベテランの方、管理職を対象とした幅広いコンテンツをご用意しております。
お問い合わせ
コストダウンが利益に直結する術だと理解していても、なかなか前に進めることができない状況。そんな時は、newjiのコストダウン自動化機能で大きく利益貢献しよう!
(Β版非公開)