- お役立ち記事
- Revolutionizing Japanese Manufacturing: The Power of Preventive Measures for Unprecedented Success
Revolutionizing Japanese Manufacturing: The Power of Preventive Measures for Unprecedented Success
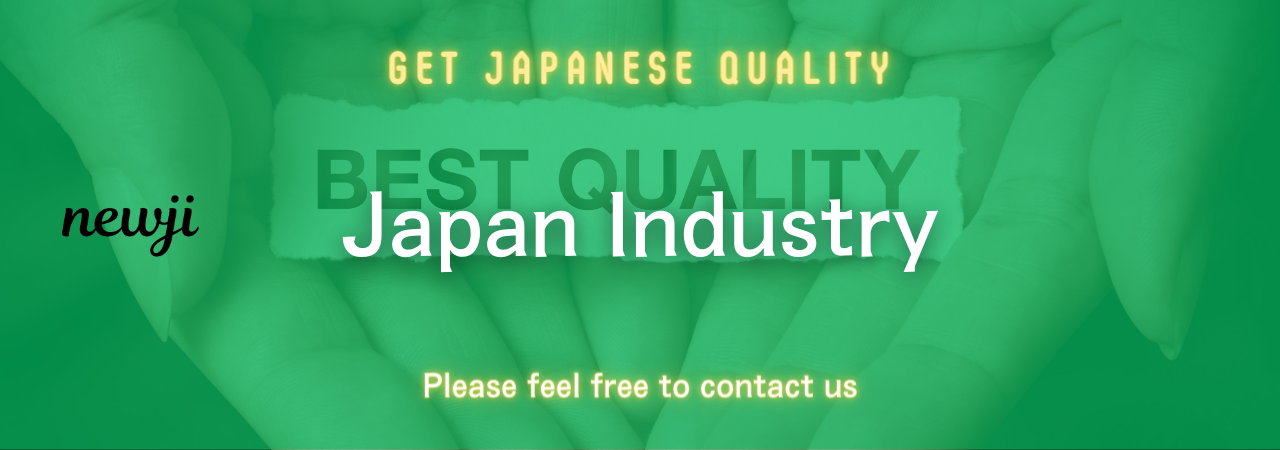
目次
Introduction
Japanese manufacturing has long been lauded for its remarkable efficiency, precision, and quality.
These coveted traits have not materialized by chance but rather through deliberate methodologies and philosophies that guide the industry.
Among these, the practice of implementing preventive measures stands out as a critical factor for success.
Preventive strategies are essential in minimizing risks, curtailing unexpected downtimes, and fostering a culture of continuous improvement.
The Pillars of Japanese Manufacturing Success
Lean Manufacturing and Kaizen
Japan is the birthplace of lean manufacturing, a system developed to maximize value by minimizing waste.
This model places strong emphasis on continual improvement through Kaizen, a systematic approach involving every employee, from the shop floor to the executive suite.
Kaizen promotes the idea that small, ongoing positive changes can lead to significant improvements over time.
Prevention is deeply embedded in this approach, ensuring that issues are addressed before they evolve into larger problems.
Quality Control Circles
Quality control circles are another key element in Japanese manufacturing.
These are small groups of workers who regularly meet to identify, analyze, and solve work-related problems.
The goal is to improve product quality and operational efficiency.
The preventive nature of these circles is evident, as they function to preemptively identify potential issues and develop solutions, averting defects before they occur.
Jidoka – Automation with a Human Touch
Jidoka translates to automation with a human touch, integrating machines with the ability to detect abnormalities and halt production to prevent defective products.
This principle empowers workers and machinery to address problems immediately, minimizing defective processes and enhancing overall production quality.
Advantages of Implementing Preventive Measures
Cost Savings
Preventive measures in manufacturing reduce costs by identifying potential issues early, saving money on repairs, and mitigating risks associated with production downtime.
A proactive approach means fewer defective products, reduced waste, and less expenditure on rework.
Enhanced Product Quality
Incorporating preventive strategies ensures a high standard of product quality.
Through continuous monitoring and improvement processes, manufacturers can adhere to rigorous quality standards, thereby increasing customer satisfaction and loyalty.
Improved Operational Efficiency
By establishing preventive measures, Japanese manufacturers achieve superior operational efficiency.
This efficiency results from reduced downtime, seamless production schedules, and a smooth operational flow, which cumulatively bolster productivity.
Increased Supplier Reliability
A strong network of reliable suppliers is a cornerstone of Japanese manufacturing.
Through preventive measures, suppliers are elevated to higher standards, contributing to stable supply chains that benefit all stakeholders involved.
Challenges and Considerations
Initial Investment
Implementing preventive systems requires an upfront investment in technology, training, and staff engagement.
These initial costs can be a barrier for companies unfamiliar with such processes.
Cultural Shift
For organizations not accustomed to continuous improvement, a cultural shift towards prevention and quality can be challenging.
It takes commitment across all levels to embrace a proactive stance truly.
Complexity in Implementation
Preventive measures can be complex and challenging to implement correctly.
They require detailed planning, systematic execution, and continuous monitoring to be effective.
Best Practices for Successful Implementation
Comprehensive Training Programs
Investing in comprehensive training programs for employees is crucial.
Understanding the rationale behind preventive measures and mastering the skills needed to implement them effectively are vital for success.
Effective Communication
Open lines of communication among all team members ensure alignment of objectives and streamlining of tasks.
Regular meetings and feedback sessions are essential components for clear communication.
Leveraging Technology
Embracing technology is vital to advance preventive strategies.
Automation, real-time monitoring, data analytics, and machine learning can all play crucial roles in evolving manufacturing processes for maximized efficiency and quality.
Negotiating with Japanese Suppliers
Building Long-Term Relationships
Japanese suppliers value long-term partnerships grounded in trust, reliability, and mutual respect.
By investing time and effort into nurturing these relationships, procurement professionals can unlock multiple benefits, including preferred pricing and reliable supply.
Understanding Cultural Nuances
Navigating negotiations requires an understanding of Japanese culture, where honor, respect, and subtlety underpin business interactions.
Listening attentively, showing deference to seniority, and exhibiting patience can facilitate successful negotiations.
Emphasizing Quality and Detail
Japanese suppliers prize precision and quality, attributes reflected in their detailed evaluations and quality inspections.
Engaging them with comprehensive, data-backed presentations and submissions will resonate and elevate credibility.
Market Conditions and Trends
Growing Technological Integration
The integration of advanced technologies in manufacturing is a prevailing trend in Japan.
This trend emphasizes automation, artificial intelligence, and data-driven manufacturing processes.
Sustainability and Green Manufacturing
Sustainability is a growing focus in Japan, with manufacturers adopting eco-friendly processes and materials.
Preventive measures regarding environmental impact are gaining prominence, driving more responsible production practices.
Global Supply Chain Dynamics
Japan’s role in global supply chains is evolving due to geopolitical factors, supply chain digitization, and shifts towards diverse sourcing.
Proactive management of these dynamics can lead to more resilient and adaptable sourcing strategies.
Conclusion
The power of preventive measures in Japanese manufacturing reflects a philosophy that values anticipation over reaction.
Incorporating these practices leads to remarkable cost savings, improved quality, heightened efficiency, and robust supplier collaborations.
While challenges exist, the benefits and enduring success stories demonstrate the transformative impact of such approaches.
By understanding cultural nuances, building strong supplier partnerships, and continuously investing in innovation, global manufacturing enterprises can embrace the benchmarks set by their Japanese counterparts, achieving unprecedented success in the ever-evolving industrial landscape.
資料ダウンロード
QCD調達購買管理クラウド「newji」は、調達購買部門で必要なQCD管理全てを備えた、現場特化型兼クラウド型の今世紀最高の購買管理システムとなります。
ユーザー登録
調達購買業務の効率化だけでなく、システムを導入することで、コスト削減や製品・資材のステータス可視化のほか、属人化していた購買情報の共有化による内部不正防止や統制にも役立ちます。
NEWJI DX
製造業に特化したデジタルトランスフォーメーション(DX)の実現を目指す請負開発型のコンサルティングサービスです。AI、iPaaS、および先端の技術を駆使して、製造プロセスの効率化、業務効率化、チームワーク強化、コスト削減、品質向上を実現します。このサービスは、製造業の課題を深く理解し、それに対する最適なデジタルソリューションを提供することで、企業が持続的な成長とイノベーションを達成できるようサポートします。
オンライン講座
製造業、主に購買・調達部門にお勤めの方々に向けた情報を配信しております。
新任の方やベテランの方、管理職を対象とした幅広いコンテンツをご用意しております。
お問い合わせ
コストダウンが利益に直結する術だと理解していても、なかなか前に進めることができない状況。そんな時は、newjiのコストダウン自動化機能で大きく利益貢献しよう!
(Β版非公開)