- お役立ち記事
- Revolutionizing Japanese Manufacturing: The Power of QC Circles in Boosting Quality and Efficiency
月間77,185名の
製造業ご担当者様が閲覧しています*
*2025年2月28日現在のGoogle Analyticsのデータより
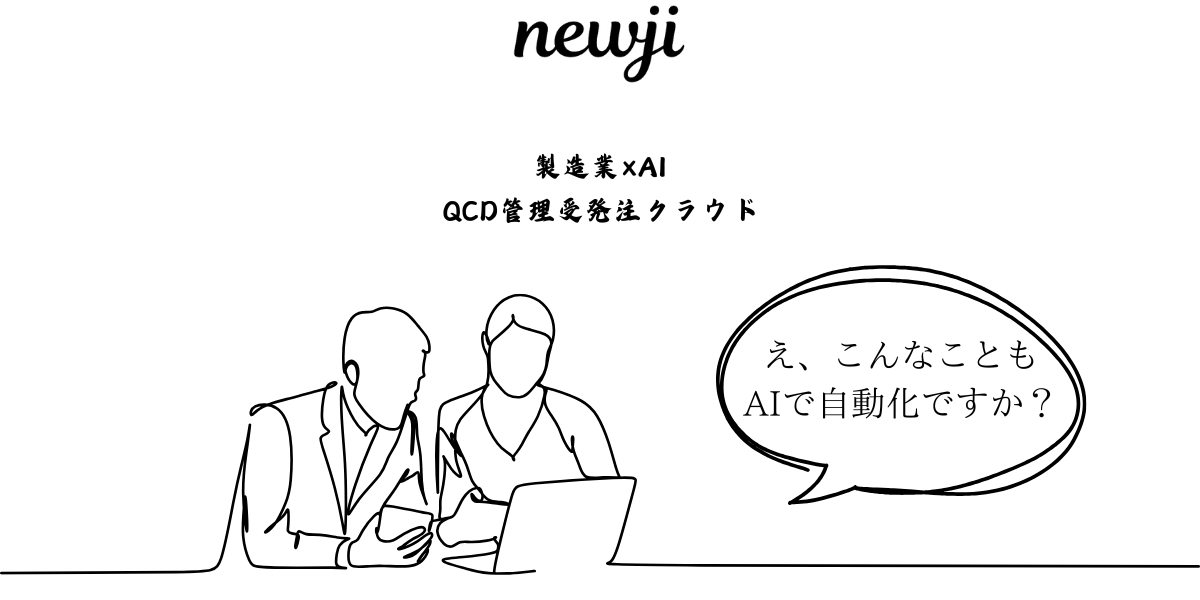
Revolutionizing Japanese Manufacturing: The Power of QC Circles in Boosting Quality and Efficiency
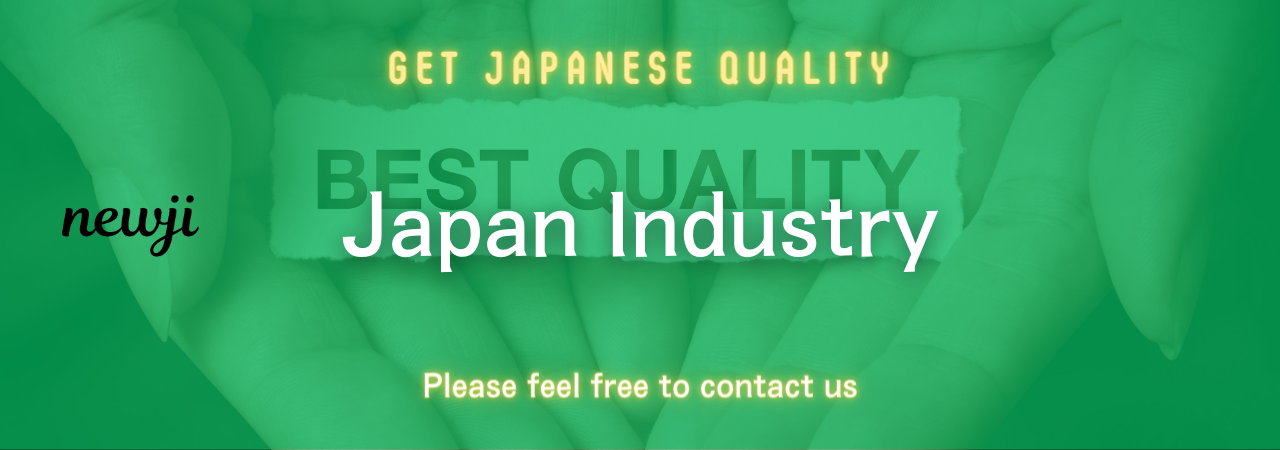
目次
Introduction to QC Circles in Japanese Manufacturing
QC Circles, or Quality Control Circles, are small groups of workers who voluntarily come together to identify, analyze, and solve work-related problems.
Originating in Japan in the 1960s, QC Circles have become a cornerstone of Japanese manufacturing excellence.
These circles focus on continuous improvement, fostering a culture of quality and efficiency within organizations.
By empowering employees at all levels, QC Circles contribute significantly to the overall performance and competitiveness of manufacturing companies.
In this article, we explore the power of QC Circles in revolutionizing Japanese manufacturing, highlighting their impact on quality and efficiency.
The History and Evolution of QC Circles
QC Circles emerged during Japan’s post-war industrial boom, a period marked by rapid economic growth and industrial expansion.
Japanese manufacturers sought innovative methods to enhance productivity and product quality to compete globally.
Inspired by Total Quality Management (TQM) principles, QC Circles were introduced as a way to involve employees directly in quality improvement efforts.
Initially, QC Circles were small, informal groups within factories, but their success quickly led to widespread adoption across various industries.
Over the decades, QC Circles have evolved, incorporating advanced problem-solving techniques and integration with modern quality management systems.
Today, QC Circles remain a vital element of Japanese manufacturing, continuously adapting to new challenges and technological advancements.
Core Principles of QC Circles
QC Circles are built on several core principles that guide their operation and effectiveness.
First, they emphasize employee participation and empowerment, recognizing that those closest to the work processes are best positioned to identify and solve problems.
Second, QC Circles focus on continuous improvement, striving for incremental enhancements that accumulate over time.
Third, they promote teamwork and collaboration, fostering a sense of collective responsibility for quality and efficiency.
Fourth, QC Circles utilize systematic problem-solving methods, such as the Plan-Do-Check-Act (PDCA) cycle, to ensure structured and effective solutions.
Finally, QC Circles encourage open communication and feedback, creating an environment where ideas and innovations can flourish.
Benefits of Implementing QC Circles
Implementing QC Circles offers numerous benefits to manufacturing organizations.
One of the primary advantages is the significant improvement in product and service quality.
By involving employees in quality control processes, organizations can identify and address defects more effectively.
QC Circles also enhance operational efficiency by streamlining processes and reducing waste.
Moreover, they foster a culture of continuous improvement, encouraging employees to seek out and implement innovative solutions.
Another key benefit is increased employee morale and job satisfaction, as workers feel valued and empowered to contribute to the organization’s success.
Additionally, QC Circles can lead to better communication and collaboration across different departments and levels within the organization.
Challenges and Limitations of QC Circles
Despite their many advantages, QC Circles face several challenges and limitations.
One common obstacle is employee resistance, particularly if workers are unfamiliar with the concept or skeptical about their ability to effect change.
Effective implementation of QC Circles requires strong support from management, which can sometimes be lacking.
Another challenge is maintaining consistency and momentum over time, as enthusiasm for QC Circles can wane without ongoing encouragement and resources.
Additionally, the success of QC Circles depends on the availability of training and access to necessary tools and data for effective problem-solving.
In some cases, QC Circles may struggle to address more complex or systemic issues that require broader organizational changes.
Finally, measuring the impact of QC Circles can be difficult, making it challenging to demonstrate their value and secure continued investment.
The Role of QC Circles in Procurement and Purchasing
QC Circles play a crucial role in the procurement and purchasing functions of manufacturing companies.
By involving procurement teams in QC Circle activities, organizations can enhance supplier quality and strengthen supplier relationships.
QC Circles allow procurement professionals to systematically evaluate and monitor supplier performance, identifying areas for improvement.
Through collaborative problem-solving, procurement teams and suppliers can work together to address quality issues, reduce lead times, and optimize costs.
Furthermore, QC Circles facilitate the sharing of best practices and technical expertise between buyers and suppliers, fostering mutual growth and innovation.
This collaborative approach helps ensure that procurement strategies align with overall organizational goals and quality standards.
Supplier Negotiation Techniques Leveraging QC Circles
QC Circles can significantly enhance supplier negotiation techniques by providing a structured framework for collaboration and mutual improvement.
One effective technique is joint problem-solving, where procurement teams and suppliers work together to identify and resolve issues that impact quality and efficiency.
This approach builds trust and fosters a cooperative relationship, making negotiations more productive and less adversarial.
Another technique is the use of data-driven discussions, leveraging the analysis and findings generated by QC Circles to support negotiation points.
By presenting concrete evidence of areas needing improvement, procurement professionals can make a compelling case for better terms or support from suppliers.
Additionally, QC Circles facilitate continuous dialogue, ensuring that negotiations are ongoing and adaptive to changing circumstances and needs.
This transparency and openness help maintain long-term, sustainable relationships with suppliers.
Market Conditions Influencing QC Circle Effectiveness
The effectiveness of QC Circles is influenced by various market conditions that shape the manufacturing landscape.
Economic factors, such as market competition and demand fluctuations, can impact the resources and focus available for QC Circle activities.
In highly competitive markets, there is greater incentive for organizations to leverage QC Circles to gain a quality and efficiency edge.
Technological advancements also play a role, as access to modern tools and data analytics can enhance the problem-solving capabilities of QC Circles.
Globalization introduces additional complexities, including managing diverse supplier networks and adapting QC Circle practices to different cultural contexts.
Regulatory changes and industry standards can drive the need for continuous improvement, making QC Circles even more relevant and necessary.
Understanding these market conditions enables organizations to tailor their QC Circle initiatives to maximize effectiveness and align with broader strategic objectives.
Best Practices for Implementing QC Circles
Implementing QC Circles successfully requires careful planning and adherence to best practices.
First, secure strong commitment and support from top management to provide necessary resources and establish the importance of QC Circles within the organization.
Second, provide comprehensive training to QC Circle members, equipping them with the skills and knowledge needed for effective problem-solving and quality control.
Third, establish clear objectives and measurable goals for QC Circles to ensure alignment with overall business strategies and to track progress.
Fourth, promote a collaborative and open culture that encourages participation, idea sharing, and mutual respect among team members.
Fifth, integrate QC Circle activities with existing quality management systems and processes to create a cohesive approach to continuous improvement.
Sixth, recognize and reward the contributions of QC Circle members to maintain motivation and sustain engagement over time.
Finally, regularly evaluate and refine QC Circle practices based on feedback and performance metrics to ensure continuous enhancement and relevance.
Integrating QC Circles with Modern Quality Management Systems
Integrating QC Circles with modern quality management systems amplifies their impact on organizational performance.
Combining QC Circles with methodologies like Lean Manufacturing and Six Sigma fosters a more comprehensive approach to quality and efficiency.
Lean principles eliminate waste and optimize processes, complementing the problem-solving focus of QC Circles.
Six Sigma’s emphasis on reducing variation and enhancing quality aligns with QC Circle objectives, enabling more precise and data-driven improvements.
Moreover, advanced technologies such as data analytics, automation, and real-time monitoring tools can enhance the effectiveness of QC Circles by providing deeper insights and facilitating faster decision-making.
Integration with enterprise resource planning (ERP) systems ensures that QC Circle initiatives are aligned with broader operational workflows and strategic goals.
This synergy between QC Circles and modern quality management systems drives sustained excellence and adaptability in a dynamic manufacturing environment.
Case Studies: Successful QC Circle Implementation in Japanese Manufacturing
Examining case studies of successful QC Circle implementations provides valuable insights into best practices and tangible benefits.
One notable example is Toyota, where QC Circles are integral to the Toyota Production System (TPS), emphasizing continuous improvement and respect for people.
At Toyota, QC Circles contribute to reducing defects, enhancing process efficiency, and fostering a culture of collaboration and innovation.
Another example is Canon, which utilizes QC Circles to improve product quality and operational efficiency across its manufacturing facilities.
Canon’s approach involves structured problem-solving sessions, cross-functional collaboration, and a focus on customer satisfaction.
These case studies demonstrate how QC Circles can drive significant improvements in quality and efficiency when supported by strong leadership and a commitment to continuous enhancement.
They also highlight the importance of aligning QC Circle activities with organizational goals and integrating them into the broader quality management framework.
Measuring the Impact of QC Circles
Measuring the impact of QC Circles is essential to demonstrate their value and guide future initiatives.
Key performance indicators (KPIs) such as defect rates, production efficiency, and cost savings provide quantitative measures of QC Circle effectiveness.
Employee engagement and satisfaction scores can gauge the cultural impact of QC Circles, reflecting improvements in morale and collaboration.
Additionally, tracking the number and scope of improvement projects undertaken by QC Circles highlights their contribution to continuous enhancement efforts.
Customer satisfaction ratings and feedback are also critical metrics, as they directly relate to the ultimate goal of quality improvement.
Regular reviews and assessments of QC Circle activities against these metrics enable organizations to identify successes, address challenges, and refine their approach for greater impact.
The Future of QC Circles in Japanese Manufacturing
As the manufacturing landscape continues to evolve, QC Circles remain a relevant and powerful tool for driving quality and efficiency.
Emerging trends such as Industry 4.0, digital transformation, and smart manufacturing present new opportunities for QC Circle integration and innovation.
The increasing use of artificial intelligence and machine learning can enhance the analytical capabilities of QC Circles, enabling more sophisticated problem-solving.
Furthermore, the global emphasis on sustainability and lean practices aligns with the continuous improvement philosophy of QC Circles, supporting environmentally friendly and resource-efficient manufacturing.
In an increasingly interconnected world, QC Circles can also facilitate cross-cultural collaboration and knowledge sharing, expanding their impact beyond traditional boundaries.
By adapting to technological advancements and shifting market demands, QC Circles will continue to play a vital role in maintaining the excellence of Japanese manufacturing.
Conclusion: The Enduring Power of QC Circles
QC Circles have revolutionized Japanese manufacturing by fostering a culture of continuous improvement, quality control, and operational efficiency.
Their integration into various aspects of manufacturing, particularly in procurement and purchasing, has enabled organizations to enhance supplier relationships and drive mutual growth.
Despite challenges, the benefits of QC Circles in improving product quality, reducing costs, and increasing employee engagement are undeniable.
By adhering to best practices, leveraging modern technologies, and aligning QC Circle activities with strategic objectives, Japanese manufacturers can sustain their competitive edge in the global market.
As the industry continues to evolve, QC Circles remain a powerful mechanism for driving innovation, excellence, and resilience in manufacturing operations.
Practical Implementation Tips for QC Circles
Implementing QC Circles effectively requires a strategic approach and attention to practical details.
Start by defining the scope and objectives of QC Circle initiatives, ensuring they align with the organization’s overall goals.
Select diverse members who bring various skills and perspectives to the QC Circle, promoting comprehensive problem-solving.
Provide training on quality management principles, problem-solving techniques, and effective communication to empower QC Circle members.
Establish regular meeting schedules and create a structured agenda to maintain focus and productivity during QC Circle sessions.
Facilitate access to necessary resources, such as data, tools, and support from other departments, to enable effective problem-solving.
Encourage open dialogue and a safe environment where members feel comfortable sharing ideas and addressing challenges.
Monitor progress through regular check-ins and track contributions to organizational performance, adjusting strategies as needed for continuous improvement.
By following these practical implementation tips, organizations can maximize the effectiveness of QC Circles and achieve sustained quality and efficiency gains.
Integrating Supplier Feedback into QC Circle Activities
Integrating supplier feedback into QC Circle activities enhances the collaborative efforts between buyers and suppliers.
Establish channels for regular communication with suppliers, enabling them to provide insights and feedback on quality and process improvements.
Incorporate supplier perspectives into QC Circle meetings, allowing for joint analysis and problem-solving on shared challenges.
Use feedback to identify common issues, develop standardized solutions, and implement best practices across the supply chain.
Fostering an open and transparent relationship with suppliers through QC Circles builds trust and mutual commitment to quality and efficiency goals.
Additionally, involving suppliers in QC Circle activities promotes a sense of partnership, encouraging suppliers to invest in their processes and contribute to continuous improvement initiatives.
This collaborative approach ensures that both buyers and suppliers are aligned in their pursuit of excellence, leading to enhanced overall supply chain performance.
Leveraging Technology to Enhance QC Circle Effectiveness
Technology plays a pivotal role in enhancing the effectiveness of QC Circles in modern manufacturing environments.
Digital tools such as data analytics platforms can provide QC Circles with valuable insights into process performance and quality metrics.
Automation technologies streamline data collection and analysis, allowing QC Circles to focus on interpreting results and developing solutions.
Collaboration software facilitates communication and coordination among QC Circle members, especially in geographically dispersed teams.
Virtual meeting platforms enable remote participation, expanding the reach and inclusivity of QC Circle initiatives.
Advanced simulation and modeling tools can aid QC Circles in testing and validating proposed improvements before implementation.
By leveraging these technologies, QC Circles can increase their efficiency, accuracy, and impact, driving more substantial quality and efficiency improvements within manufacturing organizations.
Fostering a Culture of Continuous Improvement through QC Circles
Creating a culture of continuous improvement is essential for the sustained success of QC Circles and overall organizational excellence.
Promote values such as innovation, collaboration, and accountability, aligning them with the objectives of QC Circles.
Encourage leadership to model and reinforce these values, demonstrating a commitment to quality and improvement at all levels.
Provide ongoing training and development opportunities to enhance the skills and capabilities of QC Circle members.
Celebrate successes and recognize contributions, reinforcing the importance of continuous improvement efforts.
Integrate continuous improvement principles into everyday operations, ensuring that QC Circle activities remain a core aspect of the organizational culture.
By fostering such a culture, organizations empower their employees to take ownership of quality and efficiency, making QC Circles an integral part of their strategic framework.
Enhancing Employee Engagement through QC Circles
QC Circles significantly enhance employee engagement by involving workers in decision-making and problem-solving processes.
Participation in QC Circles gives employees a sense of ownership and responsibility for their work and its outcomes.
This involvement fosters a deeper connection to the organization’s goals and a commitment to achieving them.
Moreover, QC Circles provide opportunities for personal and professional growth, as employees develop new skills and gain valuable experience.
The collaborative nature of QC Circles also strengthens team dynamics, promoting mutual support and a shared commitment to excellence.
Enhanced employee engagement through QC Circles leads to higher job satisfaction, reduced turnover, and a more motivated and productive workforce.
Organizations that prioritize employee engagement through QC Circles reap the benefits of a more committed and capable team, driving sustained quality and efficiency improvements.
Training and Development for QC Circle Members
Effective training and development are critical for the success of QC Circle initiatives.
Training programs should cover fundamental quality management concepts, problem-solving techniques, and effective communication strategies.
Equip QC Circle members with tools such as the PDCA cycle, root cause analysis, and statistical process control to enhance their problem-solving capabilities.
Provide opportunities for hands-on learning and practical application of QC Circle methodologies within the manufacturing environment.
Encourage continuous learning and knowledge sharing among QC Circle members, fostering a culture of collective expertise and innovation.
Additionally, offer leadership training to empower QC Circle facilitators and ensure they can guide their teams effectively.
By investing in comprehensive training and development, organizations ensure that QC Circle members are well-prepared to drive quality and efficiency improvements.
Aligning QC Circles with Organizational Goals
Aligning QC Circle activities with the broader organizational goals is essential to maximize their impact and relevance.
Start by clearly defining how QC Circles contribute to the company’s strategic objectives, such as enhancing customer satisfaction, reducing costs, or increasing market share.
Ensure that QC Circle projects are selected based on their potential to advance these goals, prioritizing initiatives that offer significant value.
Communicate the alignment between QC Circle efforts and organizational priorities to maintain focus and motivation among members.
Regularly review and adjust QC Circle activities to stay aligned with any shifts in strategic direction or market conditions.
By ensuring that QC Circle initiatives are directly linked to organizational goals, companies can optimize the effectiveness of their continuous improvement efforts and achieve meaningful, measurable outcomes.
Conclusion: Embracing QC Circles for Sustainable Manufacturing Excellence
QC Circles have proven to be a transformative force in Japanese manufacturing, driving significant improvements in quality and efficiency.
Their emphasis on employee participation, continuous improvement, and collaborative problem-solving aligns perfectly with the demands of modern manufacturing environments.
By leveraging QC Circles, organizations can enhance their procurement and purchasing functions, strengthen supplier relationships, and foster a culture of excellence.
Despite challenges, the benefits of QC Circles in promoting operational efficiency, reducing costs, and increasing employee engagement make them an invaluable tool for manufacturers.
As the industry continues to evolve, embracing and adapting QC Circles will be crucial for achieving sustainable manufacturing excellence and maintaining a competitive edge in the global market.
Final Thoughts on the Power of QC Circles
The power of QC Circles lies in their ability to harness the collective knowledge and skills of employees to drive meaningful improvements.
In the context of Japanese manufacturing, QC Circles embody the principles of quality, efficiency, and continuous innovation that have propelled the industry to global leadership.
Organizations looking to replicate this success can benefit from adopting QC Circle methodologies, tailoring them to their unique needs and challenges.
By fostering an environment of collaboration, empowerment, and relentless pursuit of excellence, QC Circles can transform manufacturing operations and deliver lasting value.
Ultimately, the enduring success of QC Circles underscores the importance of people-centric approaches in achieving operational excellence and sustaining competitive advantage in the manufacturing sector.
資料ダウンロード
QCD管理受発注クラウド「newji」は、受発注部門で必要なQCD管理全てを備えた、現場特化型兼クラウド型の今世紀最高の受発注管理システムとなります。
ユーザー登録
受発注業務の効率化だけでなく、システムを導入することで、コスト削減や製品・資材のステータス可視化のほか、属人化していた受発注情報の共有化による内部不正防止や統制にも役立ちます。
NEWJI DX
製造業に特化したデジタルトランスフォーメーション(DX)の実現を目指す請負開発型のコンサルティングサービスです。AI、iPaaS、および先端の技術を駆使して、製造プロセスの効率化、業務効率化、チームワーク強化、コスト削減、品質向上を実現します。このサービスは、製造業の課題を深く理解し、それに対する最適なデジタルソリューションを提供することで、企業が持続的な成長とイノベーションを達成できるようサポートします。
製造業ニュース解説
製造業、主に購買・調達部門にお勤めの方々に向けた情報を配信しております。
新任の方やベテランの方、管理職を対象とした幅広いコンテンツをご用意しております。
お問い合わせ
コストダウンが利益に直結する術だと理解していても、なかなか前に進めることができない状況。そんな時は、newjiのコストダウン自動化機能で大きく利益貢献しよう!
(β版非公開)