- お役立ち記事
- Revolutionizing Japanese Manufacturing: The Power of Strain Measurement (ひずみ計測) in Industry Innovation
月間76,176名の
製造業ご担当者様が閲覧しています*
*2025年3月31日現在のGoogle Analyticsのデータより
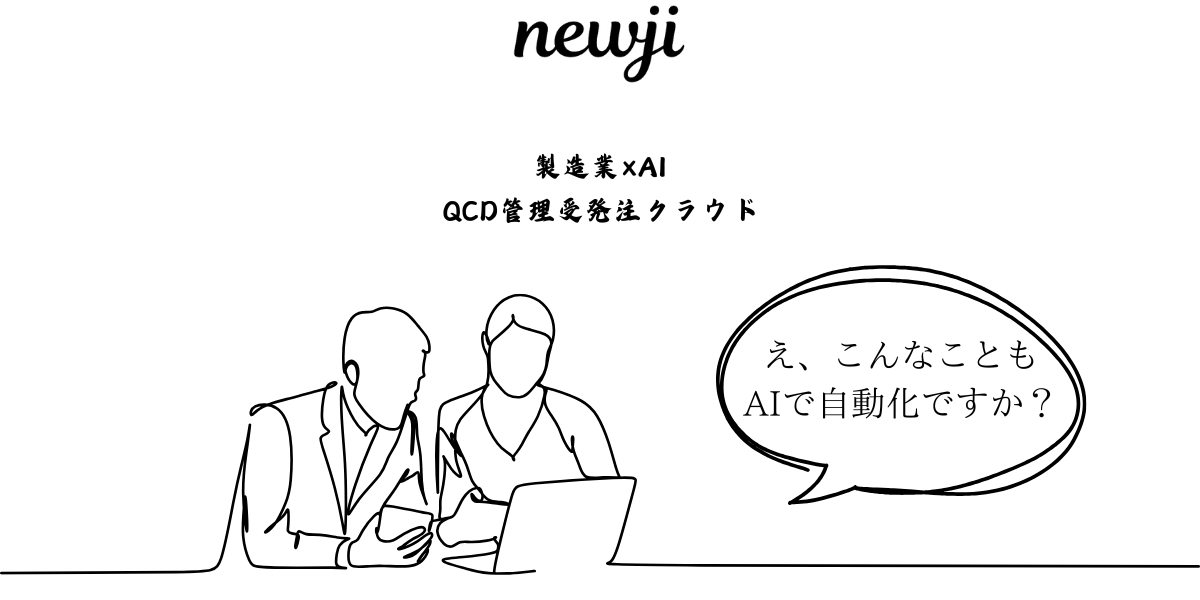
Revolutionizing Japanese Manufacturing: The Power of Strain Measurement (ひずみ計測) in Industry Innovation
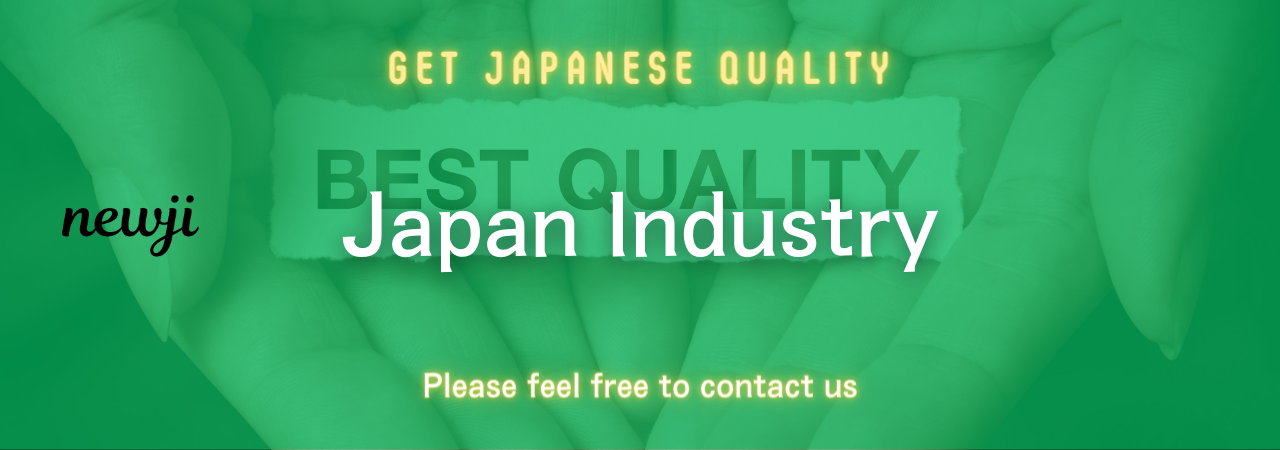
目次
Introduction
Strain measurement (ひずみ計測) is transforming the landscape of Japanese manufacturing, bringing about unprecedented levels of quality and efficiency. As a critical component in various industries, this technology measures the deformation of materials under stress, allowing for precise monitoring and control. The advent of strain measurement has revolutionized traditional practices in procurement, production, and quality management, contributing to the renowned excellence of Japanese manufacturing. This article delves into the practical aspects, advantages, and best practices of strain measurement, offering a comprehensive guide for industry professionals.
The Importance of Strain Measurement in Manufacturing
Enhancing Product Quality
Strain measurement plays a pivotal role in ensuring the high quality of manufactured products. By accurately measuring the strain and stress on materials, manufacturers can identify potential weaknesses or defects early in the production process. This early detection enables corrections to be made before final assembly, significantly reducing the rate of defective products. For example, in the automotive industry, precise strain measurements ensure vehicle components can withstand high levels of stress, enhancing safety and reliability.
Improving Process Efficiency
Integrating strain measurement into manufacturing processes leads to greater efficiency. Continuous monitoring allows for real-time adjustments to be made, optimizing production parameters and reducing downtime. In industries where precision is paramount, such as aerospace and electronics, this translates to significant cost savings and improved output. By understanding the stress distribution within materials, engineers can fine-tune the manufacturing processes to minimize waste and maximize yield.
Practical Application in Procurement and Purchasing
Supplier Evaluation and Selection
Using strain measurement as a criterion during supplier evaluation can ensure higher standards of material quality. When procuring raw materials or components, it’s beneficial to require suppliers to provide strain measurement data. This transparency helps in choosing suppliers who offer materials with the desired strength and durability. For international procurement, this data serves as a universally understood quality benchmark, simplifying the evaluation process.
Contractual Specifications
Incorporating strain measurement parameters into contractual agreements ensures that all supplied materials meet predetermined standards. This practice reduces disputes and returns, fostering a more collaborative relationship with suppliers. By establishing clear expectations and quality metrics, procurement departments can better manage supplier performance and compliance.
Advantages of Strain Measurement in Manufacturing
Precision and Accuracy
One of the leading advantages of strain measurement is its unparalleled precision. Advanced sensors and data logging technologies provide highly accurate readings of material deformation. This precision is essential in industries where even minor deviations can lead to significant failures, such as in medical devices or high-performance sports equipment.
Cost Efficiency
While the initial investment in strain measurement technology can be substantial, the long-term cost savings are considerable. Improved product quality and reduced waste lead to lower production costs. Additionally, real-time monitoring minimizes the need for extensive post-production inspections, further cutting costs.
Enhanced Safety
Safety is a critical concern in manufacturing. Strain measurement contributes significantly to safer products by ensuring that materials can withstand expected loads and stresses. This is particularly crucial in industries such as construction, transportation, and consumer electronics, where product failure can have serious consequences.
Disadvantages and Challenges
High Initial Costs
The implementation of strain measurement systems involves significant upfront costs. Purchasing sophisticated sensors, data loggers, and software, along with the necessary training for staff, requires a substantial financial commitment. Small and medium-sized enterprises may find these initial costs prohibitive.
Complex Data Analysis
Interpreting the data from strain measurement systems can be complex. It requires skilled personnel with specialized training to understand and analyze the results accurately. This complexity might pose a challenge for companies lacking in-house expertise.
Integration with Existing Systems
Integrating strain measurement technology with existing manufacturing systems can be challenging. Compatibility issues and the need for customized solutions might arise. This integration process can disrupt ongoing operations and require substantial effort to achieve seamless functionality.
Supplier Negotiation Techniques
Leveraging Data Transparency
When negotiating with suppliers, emphasize the importance of transparency in strain measurement data. Suppliers who are open about sharing this data often demonstrate a commitment to quality and reliability. Use this transparency as a bargaining tool to negotiate better terms or enhanced warranties.
Collaborative Development
Strive for a collaborative approach when dealing with suppliers. Work together to develop materials and components that meet specific strain measurement criteria. This partnership can lead to innovation and improvements that benefit both parties.
Benchmarking and Auditing
Regularly benchmark supplier performance using strain measurement data to ensure consistent quality. Conducting periodic audits based on these benchmarks fosters accountability and encourages suppliers to maintain high standards. These audits also help identify areas for improvement and best practice sharing.
Current Market Conditions and Trends
Growing Demand for Advanced Materials
There is a growing demand for advanced materials with superior mechanical properties. Strain measurement technology supports this trend by providing the data needed to develop and validate these materials. Industries such as aerospace, automotive, and consumer electronics are particularly focused on materials that offer high strength-to-weight ratios.
IoT and Industry 4.0 Integration
The integration of Internet of Things (IoT) and Industry 4.0 principles is revolutionizing strain measurement. Sensor networks and real-time data analytics allow for more sophisticated monitoring and control. This integration enhances predictive maintenance capabilities, reducing downtime and extending the lifespan of equipment.
Environmental Considerations
Increased awareness of environmental impact drives the market towards sustainable manufacturing practices. Strain measurement helps optimize material usage, reducing waste and promoting sustainability. By ensuring that materials are used efficiently, manufacturers can lower their environmental footprint.
Best Practices in Strain Measurement
Comprehensive Training Programs
Implement comprehensive training programs for staff to ensure they are proficient in using strain measurement technology. Training should cover not only the operation of the equipment but also data analysis and interpretation. This holistic approach ensures that all personnel can effectively utilize the technology.
Regular Calibration and Maintenance
Regular calibration of strain measurement equipment is crucial for maintaining accuracy. Establish a maintenance schedule to ensure that sensors and data loggers are functioning correctly. Regular maintenance reduces the risk of measurement errors and prolongs the lifespan of the equipment.
Data-Driven Decision Making
Foster a culture of data-driven decision-making within the organization. Encourage engineers and production managers to utilize strain measurement data to inform their decisions. This practice enhances the overall efficiency and effectiveness of manufacturing processes.
Continuous Improvement
Adopt a continuous improvement mindset. Regularly review and analyze strain measurement data to identify opportunities for process improvements. Implement changes based on these insights to achieve higher levels of efficiency and quality.
Conclusion
Strain measurement (ひずみ計測) is a powerful tool revolutionizing Japanese manufacturing. Its ability to enhance product quality, improve process efficiency, and support safety standards is unmatched. While the initial costs and complexity pose challenges, the long-term benefits in terms of cost savings and competitive advantage make it a worthwhile investment.
By adopting best practices and fostering strong supplier relationships, manufacturers can unlock the full potential of strain measurement technology. Embracing this innovation sets the stage for continued excellence and leadership in the global manufacturing landscape.
資料ダウンロード
QCD管理受発注クラウド「newji」は、受発注部門で必要なQCD管理全てを備えた、現場特化型兼クラウド型の今世紀最高の受発注管理システムとなります。
ユーザー登録
受発注業務の効率化だけでなく、システムを導入することで、コスト削減や製品・資材のステータス可視化のほか、属人化していた受発注情報の共有化による内部不正防止や統制にも役立ちます。
NEWJI DX
製造業に特化したデジタルトランスフォーメーション(DX)の実現を目指す請負開発型のコンサルティングサービスです。AI、iPaaS、および先端の技術を駆使して、製造プロセスの効率化、業務効率化、チームワーク強化、コスト削減、品質向上を実現します。このサービスは、製造業の課題を深く理解し、それに対する最適なデジタルソリューションを提供することで、企業が持続的な成長とイノベーションを達成できるようサポートします。
製造業ニュース解説
製造業、主に購買・調達部門にお勤めの方々に向けた情報を配信しております。
新任の方やベテランの方、管理職を対象とした幅広いコンテンツをご用意しております。
お問い合わせ
コストダウンが利益に直結する術だと理解していても、なかなか前に進めることができない状況。そんな時は、newjiのコストダウン自動化機能で大きく利益貢献しよう!
(β版非公開)