- お役立ち記事
- Revolutionizing Japanese Manufacturing: The Power of Wireless Digital Picking Systems
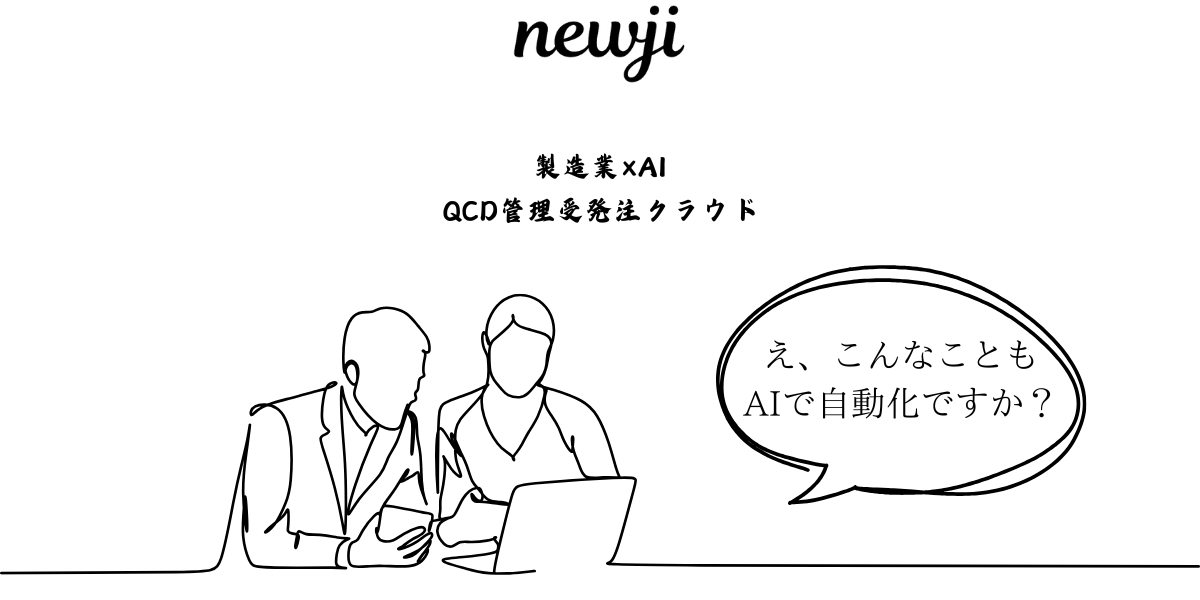
Revolutionizing Japanese Manufacturing: The Power of Wireless Digital Picking Systems
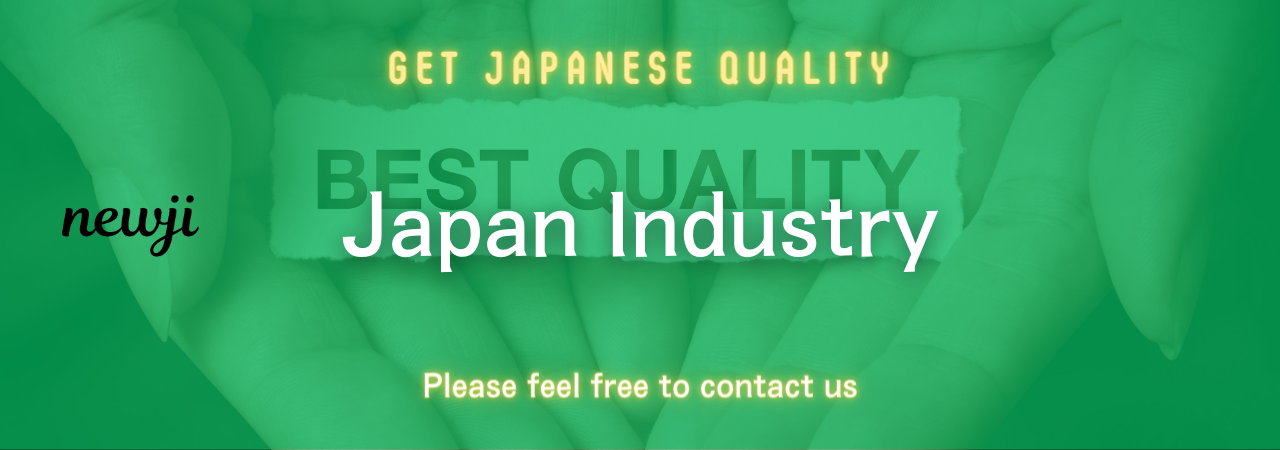
目次
Introduction to Wireless Digital Picking Systems
Manufacturing companies across the globe are continuously seeking ways to enhance their production processes and elevate factory efficiency.
One such groundbreaking innovation, especially prevalent in Japanese manufacturing, is the wireless digital picking system.
These systems are designed to streamline warehousing and production operations by eliminating the need for traditional paper-based picking lists and manual verifications.
The adoption of wireless digital picking systems in Japan has demonstrated significant improvements in picking accuracy, reduction of errors, and efficient utilization of labor.
Understanding Wireless Digital Picking Systems
What is a Wireless Digital Picking System?
A wireless digital picking system is an advanced logistical solution that employs wireless communication, digital screens, and sensor technology to guide pickers to the correct locations in the warehouse.
At its core, this system uses real-time data to provide workers with immediate instructions on which items to pick and where to place them, streamlining the entire picking process.
This technology can be integrated with Warehouse Management Systems (WMS) and Enterprise Resource Planning (ERP) systems, ensuring seamless operation and coordination.
Components of a Wireless Digital Picking System
The primary components of a wireless digital picking system include:
- Wireless Network Infrastructure: A robust and reliable wireless network is essential for ensuring the system operates smoothly.
- Digital Displays: These screens are usually mounted on shelves and racks, displaying real-time picking instructions and item information.
- Sensors and RFID: Sensors and Radio Frequency Identification (RFID) technology help track the exact location of items and detect pick completion.
- Handheld Devices: Workers may use handheld devices, such as tablets or smart scanners, to receive instructions and confirm picks.
- Central Management Software: This software coordinates all components, integrates with existing IT systems, and provides data analytics and reporting capabilities.
The Advantages of Implementing Wireless Digital Picking Systems
Enhanced Picking Accuracy
One of the key advantages is the dramatic improvement in picking accuracy.
By providing precise, real-time instructions, the system minimizes human error and ensures that the correct items are picked every time.
This enhancement reduces the risk of costly errors and returns, consequently boosting customer satisfaction.
Labor Efficiency
Wireless digital picking systems streamline workflows and eliminate the need for time-consuming manual processes.
They reduce the cognitive load on workers, enabling them to pick items more quickly and efficiently.
This efficiency allows companies to optimize labor utilization, reducing operational costs and increasing overall productivity.
Real-time Data and Analytics
These systems generate a wealth of real-time data that can be analyzed to improve warehouse operations.
Managers can track picking performance, identify bottlenecks, and make informed decisions to enhance productivity.
Moreover, this data can be used to forecast demand, manage inventory levels effectively, and improve supply chain visibility.
Flexibility and Scalability
Wireless digital picking systems are highly flexible and scalable.
They can be easily adapted to changing warehouse layouts, product assortments, and seasonal variations in demand.
This scalability makes them suitable for both small and large manufacturing environments, ensuring that companies can continue to benefit from the system as they grow.
Challenges and Considerations
Initial Investment Costs
While the long-term benefits are substantial, the initial implementation of a wireless digital picking system can be costly.
These costs include hardware, software, installation, and training expenses.
Companies must carefully evaluate their budget and return on investment (ROI) projections before committing to this technology.
Integration with Existing Systems
Integrating a wireless digital picking system with existing warehouse management and ERP systems can be complex.
Compatibility issues may arise, requiring sophisticated IT support and potential system upgrades.
It is crucial to conduct thorough testing and provide comprehensive training to ensure a smooth transition and effective system integration.
Maintenance and Upgrades
Ongoing maintenance and periodic upgrades are necessary to keep the system functioning optimally.
This requirement involves regular software updates, hardware maintenance, and troubleshooting.
Companies must allocate resources for continuous support and improvements to maximize the system’s longevity and effectiveness.
Best Practices for Successful Implementation
Conducting a Detailed Needs Assessment
Before implementing a wireless digital picking system, it is essential to conduct a thorough needs assessment.
This assessment should identify the specific challenges and pain points in current operations, outline the desired outcomes, and set measurable goals.
Understanding these factors will help design a customized system that aligns with the company’s unique requirements.
Choosing the Right Technology Partner
Selecting a reputable and experienced technology partner is critical to the success of the implementation.
Companies should seek partners with a proven track record in wireless digital picking systems, deep industry knowledge, and robust support services.
The right partner will provide valuable insights, guide the implementation process, and offer ongoing support and training.
Comprehensive Training Programs
Ensuring that all employees receive comprehensive training on the new system is crucial.
Training programs should cover system operation, troubleshooting, and best practices.
By equipping workers with the necessary skills and knowledge, companies can facilitate a smoother transition and maximize the system’s benefits.
Regular Monitoring and Continuous Improvement
After implementation, continuous monitoring is essential to identify areas for improvement and ensure optimal performance.
Regular data analysis and performance reviews can help identify inefficiencies and guide process improvements.
Companies should foster a culture of continuous improvement, encouraging feedback and innovation from employees at all levels.
The Role of Wireless Digital Picking Systems in Japanese Manufacturing
Japan’s Commitment to Excellence
Japanese manufacturing companies are renowned for their commitment to quality, efficiency, and innovation.
The adoption of wireless digital picking systems aligns with Japan’s emphasis on continuous improvement (kaizen) and meticulous attention to detail.
These systems support the principles of lean manufacturing, minimizing waste and enhancing operational efficiency.
Case Studies of Successful Implementation
Several leading Japanese manufacturing companies have successfully implemented wireless digital picking systems.
For example, a well-known electronics manufacturer reported a 30% increase in picking accuracy and a 25% reduction in labor costs within the first year of implementation.
Another automotive parts supplier saw a significant reduction in order processing times and inventory discrepancies, leading to improved customer satisfaction and market competitiveness.
Embracing Technological Advancements
As technology continues to evolve, Japanese manufacturers are proactively embracing advancements to maintain their competitive edge.
Innovations such as the Internet of Things (IoT), artificial intelligence (AI), and machine learning are being integrated with wireless digital picking systems to further optimize operations and drive efficiency.
By staying ahead of technological trends, Japanese manufacturers can continue to set industry benchmarks for excellence.
Conclusion
Wireless digital picking systems represent a transformative innovation in the realm of manufacturing, especially within the Japanese context.
These systems offer numerous advantages, including enhanced picking accuracy, improved labor efficiency, real-time data insights, and flexibility.
However, companies must carefully consider the challenges and implement best practices to ensure successful adoption.
By leveraging the power of wireless digital picking systems, manufacturers can elevate their operational efficiency, reduce costs, and maintain a competitive edge in an increasingly dynamic and demanding global market.
資料ダウンロード
QCD調達購買管理クラウド「newji」は、調達購買部門で必要なQCD管理全てを備えた、現場特化型兼クラウド型の今世紀最高の購買管理システムとなります。
ユーザー登録
調達購買業務の効率化だけでなく、システムを導入することで、コスト削減や製品・資材のステータス可視化のほか、属人化していた購買情報の共有化による内部不正防止や統制にも役立ちます。
NEWJI DX
製造業に特化したデジタルトランスフォーメーション(DX)の実現を目指す請負開発型のコンサルティングサービスです。AI、iPaaS、および先端の技術を駆使して、製造プロセスの効率化、業務効率化、チームワーク強化、コスト削減、品質向上を実現します。このサービスは、製造業の課題を深く理解し、それに対する最適なデジタルソリューションを提供することで、企業が持続的な成長とイノベーションを達成できるようサポートします。
オンライン講座
製造業、主に購買・調達部門にお勤めの方々に向けた情報を配信しております。
新任の方やベテランの方、管理職を対象とした幅広いコンテンツをご用意しております。
お問い合わせ
コストダウンが利益に直結する術だと理解していても、なかなか前に進めることができない状況。そんな時は、newjiのコストダウン自動化機能で大きく利益貢献しよう!
(Β版非公開)